Top 30 Bottom Loader Interview Questions and Answers [Updated 2025]
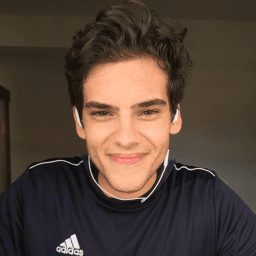
Andre Mendes
•
March 30, 2025
Preparing for a Bottom Loader interview can be daunting, but we've got you covered with this comprehensive guide. Dive into the most common interview questions for the Bottom Loader role and equip yourself with example answers and practical tips to respond effectively. Whether you're a seasoned professional or a newcomer, this post will help you confidently navigate your upcoming interview.
Download Bottom Loader Interview Questions in PDF
To make your preparation even more convenient, we've compiled all these top Bottom Loaderinterview questions and answers into a handy PDF.
Click the button below to download the PDF and have easy access to these essential questions anytime, anywhere:
List of Bottom Loader Interview Questions
Behavioral Interview Questions
Can you describe a time when you identified a safety risk in your work environment and how you addressed it?
How to Answer
- 1
Think of a specific situation where you noticed a safety risk.
- 2
Explain how you assessed the risk and its potential impact.
- 3
Detail the steps you took to address or mitigate the risk.
- 4
Mention any collaboration with others or reporting to supervisors.
- 5
Conclude with the outcome and any improvements made.
Example Answers
In my previous role, I noticed that a section of the warehouse had poor lighting which increased the risk of accidents. I reported this to my supervisor, and we subsequently installed better lighting. This significantly reduced near-miss incidents.
Give an example of how you worked with a team to improve a process in a logistics environment.
How to Answer
- 1
Identify a specific process you improved.
- 2
Highlight your role in the team and your contributions.
- 3
Use metrics or results to demonstrate the impact.
- 4
Explain how you collaborated and communicated with team members.
- 5
Conclude with lessons learned or how it influenced future work.
Example Answers
In my previous role at XYZ Logistics, our team noticed that the loading process was taking too long. I proposed a new layout for the loading area, and together we restructured the workflow. After implementation, we reduced loading time by 20%, improving overall efficiency.
Don't Just Read Bottom Loader Questions - Practice Answering Them!
Reading helps, but actual practice is what gets you hired. Our AI feedback system helps you improve your Bottom Loader interview answers in real-time.
Personalized feedback
Unlimited practice
Used by hundreds of successful candidates
Describe a situation where you managed multiple tasks under a tight schedule. How did you prioritize your work?
How to Answer
- 1
Identify a specific project or time period where you faced tight deadlines.
- 2
Explain how you listed out tasks and their deadlines.
- 3
Discuss the criteria you used for prioritization, such as urgency or importance.
- 4
Share any tools or methods you used to keep track of tasks.
- 5
Conclude with the outcome and what you learned from the experience.
Example Answers
In my previous role, I managed a project with overlapping deadlines for multiple clients. I created a detailed task list and ranked tasks based on their urgency and impact on client satisfaction. I prioritized client A's deliverables since their deadline was the earliest, and used a project management tool to track progress. As a result, I met all deadlines and received positive feedback from clients.
Tell us about a time you had to explain a complex process to a colleague or partner. How did you ensure they understood?
How to Answer
- 1
Choose a specific example that relates to your work experience.
- 2
Describe the complex process clearly and concisely.
- 3
Illustrate the methods you used to explain, like using visuals or step-by-step instructions.
- 4
Mention how you checked for understanding, such as asking questions.
- 5
Conclude with the outcome or how it benefited your colleague.
Example Answers
In my previous job, I had to explain our data entry process to a new team member. I broke it down into simple steps, created a flowchart, and walked them through it. After we went through the process, I asked them to summarize it back to me, which confirmed their understanding. This helped them complete their tasks much faster.
Can you give an example of a problem you faced in your role and how you approached solving it?
How to Answer
- 1
Identify a specific problem that relates to the Bottom Loader role.
- 2
Explain the context briefly so the interviewer understands the situation.
- 3
Describe the steps you took to analyze and solve the problem.
- 4
Mention the outcome and what you learned from the experience.
- 5
Keep your answer structured: Situation, Task, Action, Result (STAR).
Example Answers
In my last role, we had frequent delays in unloading shipments due to equipment malfunctions. I investigated the maintenance records and discovered a lack of regular checks. I proposed a new maintenance schedule that addressed the overlooked areas. As a result, equipment reliability improved, and unloading times decreased by 20%. I learned the importance of proactive maintenance.
Describe a change in procedure that you had to adapt to and how you managed the transition.
How to Answer
- 1
Select a specific change in procedure you've encountered.
- 2
Describe the context and the reason for the change.
- 3
Explain how you adapted your work habits or strategies.
- 4
Mention any support or resources you utilized during the transition.
- 5
Conclude with the positive outcome resulting from your adaptation.
Example Answers
In my last job, our team shifted from a paper-based inventory system to a digital one. This change aimed to improve accuracy. I took the initiative to learn the new software quickly, attended training sessions, and encouraged my team to share tips. As a result, our inventory management became more efficient, reducing errors by 30%.
Tell us about a time when you mediated a conflict between team members during a loading operation.
How to Answer
- 1
Identify the specific conflict and the team members involved.
- 2
Explain the steps you took to address the issue, such as communication or finding common ground.
- 3
Highlight any techniques you used to ensure everyone felt heard.
- 4
Discuss the outcome and how it improved the team dynamics.
- 5
Reflect on what you learned from the experience.
Example Answers
In a recent loading operation, two team members disagreed about the best way to stack crates. I brought them both together and allowed each to express their concerns. We discussed the merits of each approach, and eventually, they agreed on a compromise method that ensured safety and efficiency. The outcome not only resolved the conflict but also strengthened our collaboration during future operations.
Give an example of when you took initiative to enhance efficiency in your job.
How to Answer
- 1
Think about specific tasks you streamlined or improved.
- 2
Choose a situation with measurable outcomes or positive results.
- 3
Use the STAR method: Situation, Task, Action, Result.
- 4
Highlight your role and decision-making process.
- 5
Emphasize teamwork if others were involved.
Example Answers
In my previous role, we had a slow inventory process. I noticed it took too long to restock items and suggested a new labeling system. After implementing it, we reduced restock time by 30%.
Describe a time when you had to work extra hours to complete a critical project. How did you stay motivated?
How to Answer
- 1
Choose a specific project that required extra hours
- 2
Mention the reason it was critical and the implications of not completing it
- 3
Discuss your personal strategies for motivation during long hours
- 4
Highlight teamwork or support from colleagues if applicable
- 5
Conclude with the successful outcome and any lessons learned
Example Answers
In my last job, we had a product launch that required working late hours to fix some bugs. The launch was critical because we had a big client expecting it. I stayed motivated by setting small goals for myself and celebrating each milestone. My team also supported each other by taking short breaks together, which kept our spirits high. We successfully launched on time and received positive feedback.
Give an example where your attention to detail helped prevent a potential issue.
How to Answer
- 1
Choose a specific situation from your past experience.
- 2
Describe what details you noticed and why they were important.
- 3
Explain the actions you took because of your observations.
- 4
Outline the positive outcomes that resulted from your attention to detail.
- 5
Keep the example relevant to tasks a Bottom Loader would face.
Example Answers
In my previous job, I noticed that the loading schedule was not aligned with the truck capacity. I double-checked the weight limits and adjusted the load plans. This adjustment prevented overloading and ensured timely deliveries.
Don't Just Read Bottom Loader Questions - Practice Answering Them!
Reading helps, but actual practice is what gets you hired. Our AI feedback system helps you improve your Bottom Loader interview answers in real-time.
Personalized feedback
Unlimited practice
Used by hundreds of successful candidates
Technical Interview Questions
What types of loading equipment are you familiar with, and how proficient are you with them?
How to Answer
- 1
List specific types of loading equipment you have used
- 2
Mention the environments where you operated them
- 3
Include your level of proficiency with each equipment
- 4
Highlight any certifications or training you have received
- 5
Share examples of how you effectively used the equipment in a work setting
Example Answers
I have operated forklifts and pallet jacks in warehouse settings for over three years. I am certified to operate both types of equipment and have fine-tuned my skills in loading and unloading trucks efficiently.
What are the key safety protocols you follow when performing bottom loading operations?
How to Answer
- 1
Always wear appropriate personal protective equipment (PPE) such as gloves, goggles, and flame-resistant clothing.
- 2
Ensure that the area is well-ventilated and free from ignition sources before starting the loading process.
- 3
Check all equipment and hoses for leaks or damage prior to use.
- 4
Implement proper grounding and bonding procedures to prevent static electricity buildup.
- 5
Conduct a pre-operation safety meeting to review roles and emergency procedures.
Example Answers
I ensure to wear full PPE and inspect all loading equipment for leaks before starting. I also make sure the area is well-ventilated.
Don't Just Read Bottom Loader Questions - Practice Answering Them!
Reading helps, but actual practice is what gets you hired. Our AI feedback system helps you improve your Bottom Loader interview answers in real-time.
Personalized feedback
Unlimited practice
Used by hundreds of successful candidates
Can you walk us through the typical steps involved in a bottom loading operation?
How to Answer
- 1
Start with a brief overview of bottom loading and its purpose.
- 2
List the preparation steps, such as ensuring safety and equipment checks.
- 3
Describe the loading process step-by-step, mentioning key operations.
- 4
Highlight any safety measures or checks during loading.
- 5
Conclude with steps for post-loading procedures such as documentation.
Example Answers
Bottom loading involves loading liquid products from the bottom of the tank. First, I ensure all safety protocols are followed, including checking equipment and wearing protective gear. Next, I connect the loading hoses and start the pump while monitoring flow rates. Throughout the process, I check for leaks and gauge the tank levels. Finally, after loading is complete, I disconnect the hoses and document the operation.
What routine maintenance do you perform on loading equipment to ensure it operates efficiently?
How to Answer
- 1
Identify key maintenance tasks specific to bottom loaders
- 2
Emphasize the importance of safety checks
- 3
Mention scheduled inspections and documentation
- 4
Include regular lubrication and parts replacement
- 5
Discuss the role of operator training in equipment maintenance
Example Answers
I perform daily visual inspections to check for any signs of damage or wear. I also ensure that the hydraulic fluid levels are adequate and that all moving parts are properly lubricated weekly to prevent excessive wear.
What role does technology play in modern bottom loading operations, and how comfortable are you using these technologies?
How to Answer
- 1
Discuss specific technologies used in bottom loading, like automated systems and control software.
- 2
Mention the importance of technology for safety and efficiency in operations.
- 3
Share personal experiences with technology in loading operations to illustrate comfort level.
- 4
Highlight adaptability to new technologies and eagerness to learn.
- 5
Conclude with how you stay updated on industry advancements.
Example Answers
Technology is crucial in bottom loading operations as it enhances safety and increases efficiency. I've worked with automated loading systems and control software which streamline processes. I'm very comfortable using these technologies and always seek to learn about new developments.
How do you ensure compliance with regulations in bottom loading operations?
How to Answer
- 1
Stay updated on relevant local and federal regulations
- 2
Conduct regular training sessions for all personnel involved
- 3
Implement checklists to ensure all safety protocols are followed
- 4
Perform routine audits to identify and mitigate potential compliance issues
- 5
Ensure proper documentation of all operations and compliance measures
Example Answers
I ensure compliance by regularly reviewing regulations and conducting training sessions with my team. We also use checklists before every operation to verify that we meet safety protocols.
How do you calculate the weight and distribution of a load to ensure safety and compliance?
How to Answer
- 1
Identify the maximum load capacity of the equipment being used.
- 2
Use scales to measure the actual weight of the load before transportation.
- 3
Ensure the load is evenly distributed to maintain balance.
- 4
Refer to safety regulations to know legal guidelines for load limits.
- 5
Perform a center of gravity check to avoid tipping during transport.
Example Answers
First, I refer to the equipment's load capacity and check the weight of the load on scales. I ensure the weight is within limits and distribute the load evenly to maintain stability.
What documentation do you need to complete when executing a bottom-loading task?
How to Answer
- 1
Identify the required documents for bottom loading.
- 2
Mention safety checklists and procedures.
- 3
Reference inventory logs and transfer reports.
- 4
Discuss compliance with regulatory documentation.
- 5
Highlight the importance of maintaining accurate records.
Example Answers
When executing a bottom-loading task, I ensure to complete a safety checklist, fill in the inventory logs to track product levels, and prepare a transfer report to document the loading process. I also verify compliance with all regulatory requirements.
How do you ensure the quality and integrity of the products loaded?
How to Answer
- 1
Inspect each product visually for damage before loading.
- 2
Follow the loading procedures and checklists provided.
- 3
Use proper materials and tools to secure loads.
- 4
Perform regular maintenance checks on loading equipment.
- 5
Communicate with team members about any issues or irregularities.
Example Answers
I visually inspect each item for any signs of damage before loading, following the standard checklist to ensure nothing is overlooked. I also communicate with my team if I find any problems.
How do you handle loading hazardous materials differently from other types of cargo?
How to Answer
- 1
Understand specific regulations for hazardous materials.
- 2
Use personal protective equipment when handling these materials.
- 3
Ensure proper labeling and documentation during transportation.
- 4
Follow specific loading procedures to prevent leaks or spills.
- 5
Conduct risk assessments to identify potential hazards.
Example Answers
I handle hazardous materials by strictly adhering to regulations, using PPE, and ensuring all materials are properly labeled and documented.
Don't Just Read Bottom Loader Questions - Practice Answering Them!
Reading helps, but actual practice is what gets you hired. Our AI feedback system helps you improve your Bottom Loader interview answers in real-time.
Personalized feedback
Unlimited practice
Used by hundreds of successful candidates
Situational Interview Questions
While loading a tanker, you notice a leak. What steps do you take to ensure safety and compliance?
How to Answer
- 1
Immediately stop the loading process to prevent further leakage.
- 2
Identify the source of the leak and assess its severity.
- 3
Notify your supervisor and relevant safety personnel right away.
- 4
Activate emergency response procedures if necessary.
- 5
Document the incident according to company policy.
Example Answers
If I notice a leak while loading a tanker, I would first stop the loading process to avoid any hazards. I'd assess the source and severity of the leak, then alert my supervisor and safety personnel. If the leak is significant, I would initiate emergency procedures. Lastly, I would ensure the incident is documented properly.
You've been given the task to improve loading efficiency. How would you approach this task?
How to Answer
- 1
Analyze current loading processes and identify bottlenecks
- 2
Collect data on loading times to understand where delays occur
- 3
Engage with team members to gather insights and suggestions
- 4
Research best practices and innovations in loading technology
- 5
Implement changes in phases and monitor their impact
Example Answers
I would start by observing the current loading operations and identifying any bottlenecks. Then, I would analyze loading time data to pinpoint specific delays. Engaging with team members for their insights would also be key as they often have practical suggestions. Finally, I'd adopt relevant best practices and implement changes gradually, measuring the results after each phase.
Don't Just Read Bottom Loader Questions - Practice Answering Them!
Reading helps, but actual practice is what gets you hired. Our AI feedback system helps you improve your Bottom Loader interview answers in real-time.
Personalized feedback
Unlimited practice
Used by hundreds of successful candidates
A team member disagrees with the way you have organized the loading schedule. How do you handle the disagreement?
How to Answer
- 1
Stay calm and listen to the team member's concerns.
- 2
Acknowledge their point of view to show you value their input.
- 3
Ask questions to understand the reason behind their disagreement.
- 4
Present your rationale for the schedule in a clear and respectful manner.
- 5
Collaborate to find a solution that incorporates both perspectives.
Example Answers
I would first listen to my team member's concerns about the loading schedule. Understanding their perspective is important. Then, I would explain my reasoning and discuss any adjustments we could make together to improve the schedule.
What would you do if the loading equipment failed in the middle of an operation?
How to Answer
- 1
Stay calm and assess the situation quickly.
- 2
Communicate the issue to your team and the supervisor immediately.
- 3
Check for any simple solutions you can perform on the spot.
- 4
Follow safety protocols to ensure no one is at risk.
- 5
Document the failure and report it for maintenance.
Example Answers
If the loading equipment fails, I would first remain calm and assess the situation. Then, I would inform my team and supervisor about the failure. While waiting for assistance, I would check if there's a simple fix that I can implement. It's important to make sure everyone is safe and there are no hazards around.
If you are behind schedule on a loading task, how do you prioritize your actions to catch up while maintaining safety?
How to Answer
- 1
Assess what is causing the delay and if it affects safety.
- 2
Prioritize tasks that can be completed quickly without compromising safety.
- 3
Communicate with your team about the situation and any adjustments.
- 4
Focus on high-impact areas where time can be gained efficiently.
- 5
Take regular short breaks to ensure safety and prevent fatigue.
Example Answers
I would first identify the reasons for the delay, ensuring that none affect safety. Then, I'd prioritize loading the most critical items first while keeping a steady pace and communicating with my team so we can work together efficiently.
You arrive at a job site and discover the equipment needed isn't working. What do you do?
How to Answer
- 1
Assess the problem with the equipment immediately
- 2
Check if there are backup tools or equipment available
- 3
Communicate the issue to your supervisor or team lead
- 4
Determine if the problem can be fixed on-site or needs professional help
- 5
Document the issue for future reference and follow up on repairs
Example Answers
I would first inspect the equipment to understand the specific issue. Then, I would check if there are any alternative tools we could use. After that, I would notify my supervisor about the situation and discuss whether we can fix it ourselves or need to call for technical support.
A customer requests a change in loading specifications. How do you handle this?
How to Answer
- 1
Listen carefully to the customer's request
- 2
Ask clarifying questions to fully understand their needs
- 3
Assess the feasibility of the requested change
- 4
Communicate any implications or changes to the timeline
- 5
Confirm the agreement with the customer before proceeding
Example Answers
I would listen to the customer's request and clarify the details to ensure I understand exactly what they need. Then, I would check if it's feasible to implement the change within our current constraints and communicate any impacts on the timeline. Finally, I would confirm the changes with the customer and proceed.
There is a delay in receiving cargo for loading. How do you manage the logistics to minimize downtime?
How to Answer
- 1
Assess the situation quickly to understand the extent of the delay
- 2
Communicate with the suppliers to get updates on cargo arrival
- 3
Reorganize schedules and tasks for the crew to utilize their time effectively
- 4
Explore alternative loading options if available, such as different cargo or routes
- 5
Document the incident and analyze it for future improvements
Example Answers
First, I would quickly assess how long the delay is expected to be. Then, I would contact the supplier for real-time updates. While waiting, I would reorganize the crew's tasks to focus on other loading operations. If feasible, I would also consider alternative shipments that could be loaded in the meantime.
You've received feedback from a supervisor to improve your loading technique. How would you implement this?,
How to Answer
- 1
Acknowledge the feedback and express gratitude
- 2
Ask specific questions to clarify areas of improvement
- 3
Observe experienced colleagues to learn best practices
- 4
Practice the new techniques during your next loading shift
- 5
Request follow-up feedback to ensure progress
Example Answers
I appreciate the feedback from my supervisor. I would ask for specific examples of where my technique needs improvement. Then, I would observe some experienced loaders to see how they handle similar tasks and practice those techniques myself. Finally, I'd ask for feedback after implementing these changes during my next shift.
How would you handle a loading process if it involved sensitive or perishable materials that require special attention?
How to Answer
- 1
Identify the specific needs of the materials.
- 2
Ensure proper training on handling sensitive items.
- 3
Use appropriate equipment for safe loading.
- 4
Implement strict time management to minimize exposure.
- 5
Communicate clearly with the team about procedures.
Example Answers
I would first assess the specific requirements of the sensitive materials, ensuring we have the right equipment, like temperature-controlled containers. I would also ensure the team is trained to handle these items carefully to avoid damage.
Don't Just Read Bottom Loader Questions - Practice Answering Them!
Reading helps, but actual practice is what gets you hired. Our AI feedback system helps you improve your Bottom Loader interview answers in real-time.
Personalized feedback
Unlimited practice
Used by hundreds of successful candidates
Bottom Loader Position Details
Related Positions
- Top Loader
- Chain Puller
- Log Roller
- Road Cutter
- Log Cutter
- Log Driver
- Carrier Driver
- Picker
- Boom Worker
- Logging Worker
Similar positions you might be interested in.
Ace Your Next Interview!
Practice with AI feedback & get hired faster
Personalized feedback
Used by hundreds of successful candidates
Ace Your Next Interview!
Practice with AI feedback & get hired faster
Personalized feedback
Used by hundreds of successful candidates