Top 29 Top Loader Interview Questions and Answers [Updated 2025]
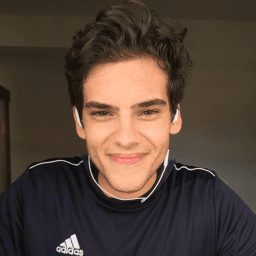
Andre Mendes
•
March 30, 2025
Preparing for a Top Loader interview? This blog post is your ultimate guide to navigating the most common questions you might face in this role. Dive into expertly crafted example answers and insightful tips to help you respond effectively and confidently. Whether you're a seasoned professional or new to the field, this resource is designed to give you the edge you need to succeed.
Download Top Loader Interview Questions in PDF
To make your preparation even more convenient, we've compiled all these top Top Loaderinterview questions and answers into a handy PDF.
Click the button below to download the PDF and have easy access to these essential questions anytime, anywhere:
List of Top Loader Interview Questions
Behavioral Interview Questions
Can you describe a time when you had to work with a team to meet a tight deadline as a Top Loader?
How to Answer
- 1
Identify a specific project with a deadline.
- 2
Explain your role and responsibilities clearly.
- 3
Highlight teamwork and communication strategies employed.
- 4
Discuss any challenges faced and how they were overcome.
- 5
Conclude with the successful outcome and what you learned.
Example Answers
In my previous role at Warehouse X, our team had to load a large shipment by the end of the day. I coordinated with my teammates to prioritize the heaviest items first and communicated with the forklift operator for quick access. Despite a broken conveyor, we adjusted and finished on time, which helped us avoid penalties.
Tell me about a situation where you encountered a conflict with a coworker while operating a Top Loader. How did you handle it?
How to Answer
- 1
Describe the conflict clearly without assigning blame.
- 2
Focus on communication; highlight how you addressed the issue directly.
- 3
Emphasize problem-solving and collaboration to resolve the conflict.
- 4
Share the outcome, focusing on positive results or lessons learned.
- 5
Mention any steps taken to prevent similar conflicts in the future.
Example Answers
While operating a Top Loader, I had a disagreement with a coworker about the best approach to stack containers. I initiated a calm conversation, listened to their perspective, and shared my suggestions. We compromised and found a mutual stacking method that improved efficiency. This experience reinforced the importance of open communication.
Don't Just Read Top Loader Questions - Practice Answering Them!
Reading helps, but actual practice is what gets you hired. Our AI feedback system helps you improve your Top Loader interview answers in real-time.
Personalized feedback
Unlimited practice
Used by hundreds of successful candidates
Describe a challenge you faced while operating a Top Loader and how you overcame it.
How to Answer
- 1
Identify a specific and relevant challenge you encountered
- 2
Explain the context of the challenge clearly and concisely
- 3
Describe the specific action steps you took to address the challenge
- 4
Highlight the outcome of your actions and what you learned
- 5
Keep the focus on your skills and problem-solving abilities
Example Answers
I faced a visibility issue while operating the Top Loader during a foggy morning. I adjusted my route to avoid tight spaces and communicated closely with my team for guidance. As a result, we completed our loading tasks safely and on time.
Can you provide an example of how you promoted safety practices while working with the Top Loader?
How to Answer
- 1
Highlight specific safety protocols you followed while operating the Top Loader
- 2
Mention any training you provided to team members on safety techniques
- 3
Share an incident where your safety measures prevented an accident
- 4
Discuss how you monitored equipment for safety compliance regularly
- 5
Emphasize the importance of communication among team members regarding safety
Example Answers
In my previous role, I ensured all operators followed the safety checklists before using the Top Loader. This practice helped us avoid accidents and maintain a safe work environment.
Give an example of a time when you had to adapt to changes in work processes or equipment as a Top Loader.
How to Answer
- 1
Choose a specific example related to the job.
- 2
Explain the changes you faced clearly.
- 3
Describe the steps you took to adapt.
- 4
Highlight any positive outcomes of your adaptation.
- 5
Keep your answer focused on your role and contributions.
Example Answers
In my previous position, we switched to a new inventory management system. I took the initiative to attend training sessions and helped my team understand the new processes. As a result, we improved our loading efficiency by 15%.
Tell me about a time when you had to lead a team of loaders. What was your approach?
How to Answer
- 1
Start with context about the team and the task at hand.
- 2
Explain the specific leadership style you used, like being hands-on or delegating.
- 3
Describe how you communicated goals and expectations to your team.
- 4
Share a challenge you faced and how you responded to it.
- 5
Conclude with the positive outcome or lesson learned.
Example Answers
In my last role, I led a team of 5 loaders during a peak season. I used a hands-on approach, demonstrating the processes myself and then having team members practice. I set clear daily targets and held brief check-ins. One challenge was managing differing skill levels, so I paired experienced loaders with newer ones. Ultimately, we exceeded our loading targets by 15%.
Give an example of how your attention to detail made a difference in your work as a Top Loader.
How to Answer
- 1
Think of a specific incident where your attention to detail directly impacted safety or efficiency.
- 2
Use numbers or metrics if possible to quantify the impact of your actions.
- 3
Describe the steps you took to ensure details were not overlooked.
- 4
Highlight how this attention to detail benefited the team or operations.
- 5
Keep your example concise but focused on the outcome.
Example Answers
In my last role, I noticed a discrepancy in load weights that could have led to cargo shifts. I double-checked each load against our specifications, which prevented a potential accident and saved the company thousands in damages.
Describe a time you had to focus on customer needs while operating the Top Loader.
How to Answer
- 1
Identify a specific situation where customer needs were a priority
- 2
Explain how you communicated with customers about their needs
- 3
Describe the actions you took to meet those needs while operating the Top Loader
- 4
Highlight the positive outcome for both the customer and your operation
- 5
Keep it concise and focused on the result
Example Answers
While operating the Top Loader during a busy shipment period, a customer requested expedited loading. I communicated with them about their deadlines, adjusted my loading plan, and successfully prioritized their needs, resulting in on-time delivery.
What motivates you to perform well in your role as a Top Loader?
How to Answer
- 1
Identify specific aspects of the job that excite you.
- 2
Connect your motivations to teamwork and efficiency.
- 3
Mention the satisfaction of accomplishing goals.
- 4
Highlight safety and skill development as motivators.
- 5
Relate personal growth and responsibility to your performance.
Example Answers
I am motivated by the thrill of working in a dynamic environment where I can contribute to team efficiency and productivity.
Don't Just Read Top Loader Questions - Practice Answering Them!
Reading helps, but actual practice is what gets you hired. Our AI feedback system helps you improve your Top Loader interview answers in real-time.
Personalized feedback
Unlimited practice
Used by hundreds of successful candidates
Technical Interview Questions
What do you think are the essential maintenance checks for ensuring a Top Loader is functioning properly?
How to Answer
- 1
Check the drum for any foreign objects before each use
- 2
Inspect the hoses for leaks or blockages regularly
- 3
Ensure the electrical connections are secure and in good condition
- 4
Clean the detergent dispenser and filter to prevent buildup
- 5
Perform regular calibrations to ensure accurate water levels
Example Answers
I believe essential maintenance checks include inspecting the drum for foreign objects, checking hoses for leaks, and ensuring electrical connections are secure.
Can you explain the operational procedures you follow when loading materials with a Top Loader?
How to Answer
- 1
Start by describing the pre-loading checklist for the Top Loader.
- 2
Discuss safety measures taken during operation.
- 3
Explain how you assess the loading area and materials to avoid hazards.
- 4
Outline the techniques you employ for efficient loading.
- 5
Mention the importance of communication with the ground crew.
Example Answers
Before loading, I conduct a pre-check of the Top Loader, ensuring all safety features are functional. Then, I survey the loading area for obstacles and hazards. I use proper loading techniques to maintain balance while communicating with the ground crew throughout the process.
Don't Just Read Top Loader Questions - Practice Answering Them!
Reading helps, but actual practice is what gets you hired. Our AI feedback system helps you improve your Top Loader interview answers in real-time.
Personalized feedback
Unlimited practice
Used by hundreds of successful candidates
What safety regulations should operators follow when working with a Top Loader?
How to Answer
- 1
Ensure proper training on Top Loader operations.
- 2
Wear appropriate personal protective equipment (PPE) at all times.
- 3
Conduct pre-operation inspections to identify any hazards.
- 4
Follow load capacity limits to prevent tipping or accidents.
- 5
Maintain clear visibility and communicate with ground personnel.
Example Answers
Operators should always wear PPE, conduct pre-operation checks, and ensure they are properly trained to handle the Top Loader safely.
How do you determine the maximum load a Top Loader can safely handle?
How to Answer
- 1
Check the manufacturer's specifications for load capacity
- 2
Consider the weight distribution across the load
- 3
Adjust for environmental factors like slope or surface type
- 4
Ensure proper maintenance and operational checks are up to date
- 5
Consult with team members for any past incidents or insights
Example Answers
I determine the maximum load by reviewing the manufacturer's specifications to know the official capacity. Then, I ensure the load is evenly distributed to avoid tipping, and I consider the terrain we're operating on.
What steps would you take if the Top Loader was experiencing mechanical issues during operation?
How to Answer
- 1
Immediately stop the operation to ensure safety.
- 2
Perform a visual inspection to identify any obvious issues.
- 3
Refer to the equipment manual for troubleshooting guidelines.
- 4
Communicate the issue to the supervisor and team members.
- 5
Document the problem and any actions taken for future reference.
Example Answers
I would first stop the machine to avoid any safety hazards. Then, I would conduct a quick visual inspection to look for visible problems. If necessary, I’d consult the equipment manual for troubleshooting advice, inform my supervisor, and document everything.
How do you ensure that the load is balanced while using a Top Loader?
How to Answer
- 1
Distribute laundry evenly across the drum to prevent an unbalanced load.
- 2
Avoid overloading with heavy items; mix small and large pieces.
- 3
Place heavier items at the bottom and lighter items on top.
- 4
Monitor the washer during the spin cycle for unusual noises or shaking.
- 5
Adjust the load if the washer indicates an imbalance error.
Example Answers
I ensure a balanced load by distributing clothes evenly around the drum and placing heavier items at the bottom for stability.
Can you explain how hydraulic systems work in a Top Loader?
How to Answer
- 1
Briefly define a hydraulic system and its basic principle of fluid power.
- 2
Discuss key components like the hydraulic pump, cylinder, and valves.
- 3
Explain the process of how these components work together to lift the load.
- 4
Highlight the importance of pressure and fluid dynamics in the system.
- 5
Mention safety features or maintenance practices relevant to hydraulic systems.
Example Answers
A hydraulic system uses pressurized fluid to create motion. In a Top Loader, the hydraulic pump generates pressure, which transfers to the cylinder. This pressure causes the cylinder to extend or retract, lifting or lowering the load efficiently. Proper maintenance ensures reliable operation and safety.
What environmental factors do you consider when operating a Top Loader outdoors?
How to Answer
- 1
Assess wind conditions that may affect stability and control.
- 2
Check the ground surface for stability to prevent tipping.
- 3
Be aware of weather changes that could impact visibility or safety.
- 4
Monitor noise levels to ensure communication is effective.
- 5
Consider the proximity of obstacles, such as overhead lines and nearby vehicles.
Example Answers
I always assess wind conditions before operating a Top Loader outdoors, as strong winds can impact stability and control.
What techniques do you use to safely handle different types of materials with the Top Loader?
How to Answer
- 1
Identify the type of material being handled and adjust lifting techniques accordingly.
- 2
Use appropriate attachments or forks for different materials to ensure a secure grip.
- 3
Inspect the load for stability and weight before lifting to prevent tipping or dropping.
- 4
Maintain clear visibility and communicate with team members during operation.
- 5
Follow safety protocols and wear necessary protective gear at all times.
Example Answers
When handling different materials with the Top Loader, I assess the weight and type first. For heavier loads, I use reinforced forks and double-check their positioning before lifting. I also ensure clear visibility and communicate with coworkers to avoid accidents.
Are you familiar with any software used for inventory management in conjunction with Top Loader operations?
How to Answer
- 1
Research specific inventory management software relevant to your industry
- 2
Mention any software you have used that integrates with Top Loaders
- 3
Explain how that software has improved efficiency or accuracy in your past roles
- 4
Be prepared to discuss features like tracking, reporting, or real-time updates
- 5
Show enthusiasm for learning new software if you're not familiar with specific ones
Example Answers
Yes, I have experience with Warehouse Management Systems like SAP Extended Warehouse Management. I utilized it to streamline inventory tracking alongside Top Loader operations, which greatly improved our accuracy in order fulfillment.
Don't Just Read Top Loader Questions - Practice Answering Them!
Reading helps, but actual practice is what gets you hired. Our AI feedback system helps you improve your Top Loader interview answers in real-time.
Personalized feedback
Unlimited practice
Used by hundreds of successful candidates
Situational Interview Questions
If you were operating a Top Loader and noticed someone in danger nearby, what actions would you take?
How to Answer
- 1
Immediately stop the Top Loader to prevent any further risk.
- 2
Assess the situation quickly to understand the nature of the danger.
- 3
Use your horn or a signal to alert others in the area of the danger.
- 4
Call for assistance or emergency services if needed.
- 5
Stay with the person in danger until help arrives or the situation is resolved.
Example Answers
I would stop operating the Top Loader right away to avoid any accidents. Then, I would assess how to best assist the person in danger and alert nearby workers using my horn.
Imagine you are tasked with improving loading efficiency. What strategies would you consider implementing?
How to Answer
- 1
Analyze the current loading process to identify bottlenecks
- 2
Implement technology solutions like automated loading systems
- 3
Train staff on best practices for loading techniques
- 4
Use data to predict peak loading times and adjust schedules accordingly
- 5
Encourage feedback from loading staff to refine processes
Example Answers
I would start by analyzing the current loading process to pinpoint any bottlenecks. From there, I could invest in automated loading solutions to speed things up.
Don't Just Read Top Loader Questions - Practice Answering Them!
Reading helps, but actual practice is what gets you hired. Our AI feedback system helps you improve your Top Loader interview answers in real-time.
Personalized feedback
Unlimited practice
Used by hundreds of successful candidates
What would you do if you encountered unexpected delays in the loading schedule with the Top Loader?
How to Answer
- 1
Assess the cause of the delay quickly.
- 2
Communicate the delay to your team and supervisors immediately.
- 3
Prioritize safety and efficiency in resolving the issue.
- 4
Adjust loading plans as needed to minimize downtime.
- 5
Document the incident for future reference and process improvement.
Example Answers
If I encounter unexpected delays, I would first determine the root cause of the issue. Then, I would inform my team and supervisors so that everyone is on the same page. I would prioritize safety while coordinating adjustments to the loading schedule to minimize impact on the overall operations.
You are working with a team, and another worker is not following proper loading procedures. How would you address this?
How to Answer
- 1
Approach the worker privately to discuss the issue
- 2
Use clear and respectful language to express your concerns
- 3
Explain the importance of following proper procedures for safety and efficiency
- 4
Invite them to share their perspective on the situation
- 5
Offer assistance or training if they are unsure about the procedures
Example Answers
I would first speak to the worker privately to address my concerns. I would explain why following loading procedures is crucial for everyone’s safety and efficiency. I would listen to their side and offer to help if they are struggling with the process.
If a crucial tool on the Top Loader failed while you were in the middle of a job, how would you proceed?
How to Answer
- 1
Assess the situation calmly to understand the failure's impact
- 2
Check if there is an alternative tool or workaround available
- 3
Communicate with your team or supervisor about the issue
- 4
Prioritize safety and follow any necessary shutdown procedures
- 5
Document the issue for future reference and analysis
Example Answers
If a crucial tool failed, I would first assess how it affects my current task. Then, if there is an alternative tool, I'd utilize that. I would also inform my team and ensure everyone's safety before moving forward.
What would you do if a workflow disruption occurred that impacted your Top Loader operations?
How to Answer
- 1
Identify the cause of the disruption quickly
- 2
Communicate with team members about the issue
- 3
Develop a temporary workaround to minimize impact
- 4
Implement a long-term solution to prevent future disruptions
- 5
Follow up with the team to ensure the plan is working
Example Answers
I would first assess what caused the disruption, then inform my team to ensure everyone is aware. I would create a temporary plan to keep operations running smoothly while we resolve the main issue, and later, implement a preventive measure.
If a new team member needed training on the Top Loader, how would you approach their training?
How to Answer
- 1
Start with an overview of the Top Loader's functions and safety protocols.
- 2
Demonstrate the basic operation through a hands-on walkthrough.
- 3
Encourage questions throughout the training to ensure understanding.
- 4
Provide opportunities for supervised practice with gradual independence.
- 5
Follow up with a review session to assess their confidence and skills.
Example Answers
I would begin by explaining the Top Loader's key functions and safety rules. Then, I'd demonstrate how to operate it, allowing the new team member to ask questions. After that, I would supervise their practice, giving them feedback until they feel comfortable using it independently.
How would you communicate with other departments about loading priorities and issues?
How to Answer
- 1
Establish regular updates through meetings or bulletins to discuss priorities and issues.
- 2
Utilize collaborative tools for real-time sharing of loading schedules and potential problems.
- 3
Keep communication clear and concise to avoid misunderstandings.
- 4
Encourage feedback from other departments to improve the loading process.
- 5
Maintain a positive relationship with colleagues to foster teamwork and support.
Example Answers
I would set up weekly meetings with representatives from other departments to discuss loading priorities and any issues. This way, we can stay aligned and address concerns promptly.
You’re tasked with assessing the weight of loads before they’re lifted. How would you approach this?
How to Answer
- 1
Identify the tools available for weight measurement.
- 2
Consider the safety of personnel and equipment during the process.
- 3
Establish a standardized method for weighing loads.
- 4
Train staff on proper techniques and equipment use.
- 5
Regularly calibrate weighing equipment to ensure accuracy.
Example Answers
I would start by using a calibrated scale, ensuring it's placed on a stable surface. This allows for accurate weight measurement while keeping safety in mind. I'd create a checklist for staff to follow, ensuring everyone uses the same method for consistency.
Top Loader Position Details
Recommended Job Boards
ZipRecruiter
www.ziprecruiter.com/Jobs/Top-LoaderThese job boards are ranked by relevance for this position.
Related Positions
- Bottom Loader
- Topper
- Chain Puller
- Carrier Driver
- Log Roller
- Log Driver
- Log Cutter
- Road Cutter
- Skidder Operator
- Cable Puller
Similar positions you might be interested in.
Ace Your Next Interview!
Practice with AI feedback & get hired faster
Personalized feedback
Used by hundreds of successful candidates
Ace Your Next Interview!
Practice with AI feedback & get hired faster
Personalized feedback
Used by hundreds of successful candidates