Top 30 Can Maker Interview Questions and Answers [Updated 2025]
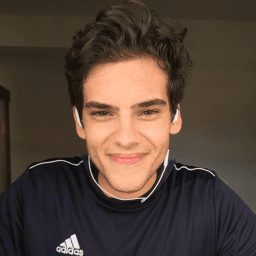
Andre Mendes
•
March 30, 2025
Preparing for a Can Maker interview can be daunting, but we're here to help you stand out. This blog post covers the most common interview questions for the Can Maker role, equipped with example answers and insightful tips to help you respond effectively. Whether you're a seasoned professional or a newcomer, dive in to boost your confidence and ace your interview with ease.
Download Can Maker Interview Questions in PDF
To make your preparation even more convenient, we've compiled all these top Can Makerinterview questions and answers into a handy PDF.
Click the button below to download the PDF and have easy access to these essential questions anytime, anywhere:
List of Can Maker Interview Questions
Behavioral Interview Questions
Describe a project where your focus was on increasing operational efficiency.
How to Answer
- 1
Identify a specific project to discuss
- 2
Highlight the goal of improving efficiency
- 3
Explain the methods or strategies you implemented
- 4
Share quantifiable results or improvements
- 5
Reflect on what you learned and how it applies to the role
Example Answers
In my previous role at a manufacturing plant, I led a project to streamline the assembly line. We analyzed our workflow and identified bottlenecks, then implemented a new scheduling system that reduced downtime by 15%. This resulted in a 10% increase in overall production efficiency in just three months.
Can you describe a time when you had to collaborate with others to complete a project on time?
How to Answer
- 1
Choose a specific project that had a clear deadline.
- 2
Detail your role and the roles of others involved.
- 3
Explain the challenges faced and how collaboration helped overcome them.
- 4
Highlight the outcome of the project and the importance of teamwork.
- 5
Keep it concise and focus on your contributions.
Example Answers
In my previous job at a packaging company, we had a rush order for a new product launch. I coordinated with the design team and production staff, holding daily meetings to ensure everyone was aligned. We faced delays due to material shortages, but by collaborating and brainstorming solutions, we were able to adjust our workflow and meet the deadline successfully, resulting in a successful product launch.
Don't Just Read Can Maker Questions - Practice Answering Them!
Reading helps, but actual practice is what gets you hired. Our AI feedback system helps you improve your Can Maker interview answers in real-time.
Personalized feedback
Unlimited practice
Used by hundreds of successful candidates
Tell me about a challenging situation you faced in a previous job and how you resolved it.
How to Answer
- 1
Select a specific challenge relevant to your past experience.
- 2
Describe the context and impact of the challenge clearly.
- 3
Focus on the actions you took to resolve the situation.
- 4
Highlight the outcome and any lessons learned.
- 5
Keep your answer structured and concise.
Example Answers
In my last job, our production line faced a sudden equipment failure that delayed output. I assessed the issue, coordinated with maintenance for a quick repair, and implemented a temporary workaround. This minimized downtime by 30% and taught me the importance of having contingency plans.
Describe a time when you had to adapt to a significant change at work. How did you handle it?
How to Answer
- 1
Identify a specific change you faced at work
- 2
Explain how the change impacted your role
- 3
Describe the actions you took to adapt
- 4
Highlight any positive outcomes from your adaptation
- 5
Keep your answer concise and focused on your role
Example Answers
At my previous job, the production process changed to a new technology. It required me to learn new machinery quickly. I took extra hours to train with the new equipment and collaborated with my team to share insights. As a result, we improved our output by 20%.
Give an example of a project where attention to detail was critical. How did you ensure high quality?
How to Answer
- 1
Select a specific project that required precision.
- 2
Describe the steps you took to ensure quality.
- 3
Mention tools or methods used for verification.
- 4
Highlight any challenges and how you overcame them.
- 5
Conclude with the positive outcome or results of your efforts.
Example Answers
In my previous role, I worked on a project to design a new can for a beverage. We used CAD software for precise dimensions and performed regular quality checks. I initiated a peer review process and regularly consulted with the production team to address any discrepancies. This attention to detail reduced errors by 30% and improved production efficiency.
Describe a situation where you took initiative to improve a process or system.
How to Answer
- 1
Identify a specific process you improved.
- 2
Describe the problem with the existing process.
- 3
Explain your initiative and the steps you took.
- 4
Highlight the positive outcome or results.
- 5
Reflect on what you learned from the experience.
Example Answers
In my previous job, I noticed our inventory tracking was manual and prone to errors. I proposed and implemented an automated system using software that reduced errors by 30% and saved us two hours of work weekly.
Tell me about a time when effective communication with your team made a difference in a project's outcome.
How to Answer
- 1
Choose a specific project or situation.
- 2
Highlight the communication methods used, like meetings or updates.
- 3
Mention the team's challenges before the communication.
- 4
Explain how the communication resolved issues or improved outcomes.
- 5
Conclude with the positive results for the project.
Example Answers
In a recent project to improve production efficiency, we faced delays due to misunderstandings. I organized daily stand-up meetings where each team member shared their progress and challenges. This open communication helped us identify bottlenecks quickly. As a result, we finished the project two weeks ahead of schedule.
How have you handled conflicts with colleagues in the past? Can you give a specific example?
How to Answer
- 1
Choose a specific conflict that had a positive outcome.
- 2
Explain your role in resolving it.
- 3
Focus on communication and understanding.
- 4
Highlight any compromises or solutions reached.
- 5
Mention the lessons learned from the experience.
Example Answers
In my previous job, I had a conflict with a colleague about the design of a can. We both had strong opinions, so I suggested we sit down and discuss our ideas. During our conversation, I listened to his perspective and shared my thoughts. We found common ground and decided to integrate both of our ideas into the final design, which improved the product. This taught me the importance of collaboration.
Don't Just Read Can Maker Questions - Practice Answering Them!
Reading helps, but actual practice is what gets you hired. Our AI feedback system helps you improve your Can Maker interview answers in real-time.
Personalized feedback
Unlimited practice
Used by hundreds of successful candidates
Technical Interview Questions
How would you set up a production line for a new can design?
How to Answer
- 1
Identify the specifications of the new can design and its material requirements.
- 2
Select appropriate machinery that can handle the new design and material.
- 3
Plan the layout of the production line for efficiency and safety.
- 4
Train staff on new processes and quality control measures for the can design.
- 5
Test the production line with initial runs to refine processes before full-scale production.
Example Answers
To set up a production line for a new can design, I would start by reviewing the design specifications to understand the materials and dimensions needed. Then, I would choose machinery capable of processing those materials effectively. I would layout the production line to minimize bottlenecks, ensuring safety protocols are integrated. Staff would receive training on the new design's requirements and quality checks. Finally, I'd conduct trial runs to ensure everything functions smoothly before starting full production.
What steps do you take to troubleshoot a problem during the can-making process?
How to Answer
- 1
Identify the symptoms of the issue immediately
- 2
Consult production records to find unexpected changes
- 3
Inspect equipment and machinery for visible issues
- 4
Engage with team members to gather insights and observations
- 5
Implement corrective actions and monitor results
Example Answers
First, I observe the issue to identify symptoms, like inconsistent can sizes. Then, I check the production logs for any changes. I perform a quick equipment inspection and involve my team to discuss their observations. Finally, I make adjustments and closely monitor the output to ensure the problem is resolved.
Don't Just Read Can Maker Questions - Practice Answering Them!
Reading helps, but actual practice is what gets you hired. Our AI feedback system helps you improve your Can Maker interview answers in real-time.
Personalized feedback
Unlimited practice
Used by hundreds of successful candidates
How do you interpret technical drawings and blueprints related to can manufacturing?
How to Answer
- 1
Familiarize yourself with common symbols and notations used in technical drawings.
- 2
Understand the dimensions and tolerances indicated to ensure accuracy in manufacturing.
- 3
Practice reading blueprints to identify key features like weld lines or seams in cans.
- 4
Discuss any specific software tools you might use for interpreting these drawings.
- 5
Share experiences where your interpretation of a drawing led to successful production outcomes.
Example Answers
I always start by reviewing the symbols and common notations in the technical drawings. For example, I know how to identify the seam details in can designs that are crucial for their structural integrity.
What routine maintenance do you perform on can-making machines to prevent issues?
How to Answer
- 1
Check and lubricate moving parts weekly
- 2
Calibrate machines regularly to maintain precision
- 3
Inspect electrical connections for wear or damage
- 4
Clean the machine to remove debris that could affect performance
- 5
Document all maintenance activities for future reference
Example Answers
I perform weekly checks on all moving parts, ensuring they are properly lubricated to reduce friction and prevent wear.
How familiar are you with using CAD software to design or modify can blueprints?
How to Answer
- 1
Mention specific CAD software you have experience with.
- 2
Describe how you have used CAD in previous jobs or projects.
- 3
Highlight any relevant projects involving can design.
- 4
Emphasize your ability to learn new software quickly.
- 5
Connect your skills to the requirements of the Can Maker position.
Example Answers
I have extensive experience using AutoCAD and SolidWorks for designing and modifying can blueprints, including a project where I redesigned a beverage can for lighter packaging.
What are the key steps involved in manufacturing a high-quality can?
How to Answer
- 1
Start with material selection for durability and safety.
- 2
Ensure precise metal forming to eliminate defects.
- 3
Implement rigorous quality control checks during production.
- 4
Focus on proper coating and lining for corrosion resistance.
- 5
Verify sealing techniques to ensure the can is airtight.
Example Answers
Manufacturing a high-quality can begins with selecting the right materials, like aluminum or steel, to ensure they can withstand pressure and are safe for food. Next, metal forming must be precise to avoid any dents or imperfections. Quality control checks should be conducted regularly to catch any issues early. Coating the inside of the can is crucial to prevent corrosion and ensure product safety. Finally, strong sealing techniques are vital so the can remains airtight, preserving the contents inside.
What materials are commonly used in can making, and why are they chosen?
How to Answer
- 1
Mention the primary materials: aluminum and steel.
- 2
Explain the benefits of each material, such as durability and recyclability.
- 3
Discuss the significance of coatings or linings used in cans.
- 4
Highlight environmental considerations, like sustainability of materials.
- 5
Be prepared to discuss specific applications or types of cans.
Example Answers
Can making primarily uses aluminum and steel. Aluminum is lightweight and recyclable, making it energy-efficient. Steel is strong and ideal for many food types. Both materials ensure the cans are durable and safe for storage.
How do you ensure that can-making machines are operating optimally and efficiently?
How to Answer
- 1
Conduct regular maintenance checks on the machines to prevent breakdowns.
- 2
Monitor production metrics such as speed and scrap rates closely.
- 3
Train the operators on efficient machine handling techniques.
- 4
Utilize sensors and automation for real-time performance data.
- 5
Implement a feedback loop with the production team for continuous improvement.
Example Answers
I ensure optimal operation by conducting regular maintenance checks and monitoring the production metrics closely. This helps in minimizing downtime and improving efficiency.
What techniques do you use to ensure that each can meets quality standards?
How to Answer
- 1
Describe specific quality control measures you implement.
- 2
Mention monitoring processes during production.
- 3
Explain how you train staff on quality standards.
- 4
Talk about using equipment to test can integrity.
- 5
Share examples of how you analyze defects and make improvements.
Example Answers
I implement strict quality control measures by conducting regular inspections during production. Each batch of cans is tested for leaks and defects using pressure tests.
What safety protocols are essential in the can-making process?
How to Answer
- 1
Emphasize the importance of personal protective equipment like gloves and goggles.
- 2
Discuss machine safety protocols such as lockout/tagout procedures.
- 3
Mention the need for regular safety training for employees.
- 4
Highlight the importance of maintaining clean and organized workspaces.
- 5
Talk about emergency procedures for equipment failures or accidents.
Example Answers
In the can-making process, it's essential to use personal protective equipment like gloves and safety goggles to protect workers from hazards. We also follow strict lockout/tagout procedures to ensure machines are shut down safely during maintenance.
Don't Just Read Can Maker Questions - Practice Answering Them!
Reading helps, but actual practice is what gets you hired. Our AI feedback system helps you improve your Can Maker interview answers in real-time.
Personalized feedback
Unlimited practice
Used by hundreds of successful candidates
Situational Interview Questions
How would you approach a sudden increase in production targets from management?
How to Answer
- 1
Assess current production capacity and resources
- 2
Communicate with the team to understand challenges
- 3
Identify bottlenecks and areas for improvement
- 4
Propose practical solutions or adjustments
- 5
Maintain open communication with management for feedback
Example Answers
First, I would evaluate our current production capacity to see how we can meet the new targets. Then, I would gather input from my team to identify challenges. After that, I'd pinpoint any bottlenecks and suggest ways to streamline our processes, like overtime or optimizing workflows. Finally, I would keep management informed and seek their input on my proposed changes.
How would you prioritize tasks if faced with a significant deadline to meet?
How to Answer
- 1
Identify the most critical tasks that directly impact the deadline
- 2
Break down large tasks into manageable steps
- 3
Assess which tasks have the highest urgency or importance
- 4
Use a simple prioritization method like the Eisenhower Matrix
- 5
Communicate with your team to delegate or share workload effectively
Example Answers
I would first identify the critical tasks that will impact our deadline, then break them down into smaller steps to tackle efficiently. I would prioritize based on urgency and importance, using a simple list to keep track of progress. Communication with the team would be key to ensure we are aligned and can share the workload as needed.
Don't Just Read Can Maker Questions - Practice Answering Them!
Reading helps, but actual practice is what gets you hired. Our AI feedback system helps you improve your Can Maker interview answers in real-time.
Personalized feedback
Unlimited practice
Used by hundreds of successful candidates
Imagine a key piece of equipment breaks down during production. How would you handle this?
How to Answer
- 1
Stay calm and assess the situation quickly.
- 2
Communicate the issue to your supervisor and team immediately.
- 3
Implement emergency procedures if available.
- 4
Identify the cause and determine if it can be fixed in-house or requires outside help.
- 5
Minimize downtime by finding an alternative solution or equipment.
Example Answers
First, I would stay calm and quickly assess the breakdown to understand its impact. Then, I would inform my supervisor and team about the issue. If we have emergency procedures, I would follow those. Next, I would look into the cause of the breakdown and determine if it can be fixed internally. Otherwise, I would seek external assistance while looking for alternative production methods to reduce downtime.
What would you do if a batch of cans was found to be below quality standards?
How to Answer
- 1
Immediately isolate the affected batch to prevent further use.
- 2
Conduct a thorough inspection to determine the extent of the quality issue.
- 3
Communicate with the team about the findings and involve key personnel.
- 4
Implement corrective actions based on the root cause analysis.
- 5
Document the incident and the steps taken for future reference and training.
Example Answers
I would first isolate the affected batch to ensure no substandard cans are used. Then, I'd inspect them to identify the specific issues. After that, I would gather the team to discuss our findings and brainstorm corrective actions. Finally, I would document everything for future reference.
A disagreement arises within your team about the best production method. How would you resolve it?
How to Answer
- 1
Encourage open discussion to understand all perspectives
- 2
Gather data on each method to support decision-making
- 3
Facilitate a pros and cons analysis with the team
- 4
Aim for a consensus or compromise that satisfies key concerns
- 5
If necessary, propose a trial period to test the best methods
Example Answers
I would start by encouraging my team to express their views on the different production methods we are considering. Then, I would gather data to compare the effectiveness of each method, and guide the team to analyze the pros and cons together. If we still struggle to choose, I would suggest a compromise or even a trial run to see which method works best in practice.
If faced with a shortage of raw materials, what steps would you take to ensure continued production?
How to Answer
- 1
Assess the current inventory to understand available materials.
- 2
Communicate with suppliers to explore alternative sourcing options.
- 3
Prioritize production schedules based on available materials.
- 4
Investigate substitutes or alternative materials that meet quality standards.
- 5
Implement a short-term plan to reduce waste and optimize production.
Example Answers
I would first assess our current inventory to determine how much raw material we have on hand. Then, I would reach out to our suppliers to see if we can source materials from different vendors or negotiate faster delivery times.
You are tasked with developing a new can type. How would you approach this project?
How to Answer
- 1
Research current market trends and consumer needs for can designs.
- 2
Identify potential materials and their benefits for the new can type.
- 3
Evaluate environmental impact and sustainability options.
- 4
Engage with stakeholders for feedback and requirements.
- 5
Prototype the design and test for functionality and appeal.
Example Answers
I would start by analyzing market trends to understand what consumers are looking for in a can design. Then, I would explore materials like aluminum or bioplastics to find the best option for our needs. Considering the environmental impact is crucial, so I'd aim for sustainable choices. Feedback from stakeholders would guide our design requirements, and finally, I'd create prototypes to test usability and aesthetics before launching.
You need to reduce production costs without compromising quality. What strategies would you consider?
How to Answer
- 1
Analyze the current production process to identify waste points
- 2
Negotiate better rates with suppliers for raw materials
- 3
Invest in training workers to improve efficiency
- 4
Implement preventive maintenance to reduce equipment downtime
- 5
Explore alternative materials that maintain quality but lower costs
Example Answers
I would analyze our production workflow to pinpoint areas where we can minimize waste, such as reducing excess raw material usage. Additionally, I would negotiate with suppliers to secure better pricing for our materials while evaluating alternative suppliers who might offer us cost savings without sacrificing quality.
How would you handle a situation where your can components supplier fails to deliver on time?
How to Answer
- 1
Assess the impact of the delay on production and inventory.
- 2
Communicate promptly with the supplier to understand the issue.
- 3
Explore alternative suppliers or temporary solutions.
- 4
Keep stakeholders informed about the situation and potential impacts.
- 5
Implement a plan to mitigate future supply chain risks.
Example Answers
I would first evaluate how the delay affects our production schedule. Then, I would contact the supplier to find out the cause and expected time frame for delivery. If the delay is significant, I would look for alternative suppliers. Communication with my team would be key to adjust our plans accordingly.
A major client provides negative feedback on your product. How do you address their concerns?
How to Answer
- 1
Acknowledge the client's feedback sincerely.
- 2
Ask clarifying questions to fully understand their concerns.
- 3
Provide a plan of action to address the issues raised.
- 4
Follow up with the client after implementing changes.
- 5
Document the feedback and responses for future reference.
Example Answers
I appreciate the feedback from the client and acknowledge their concerns. I would ask them for more details to ensure I understand completely. Then, I would outline a specific plan to address the issues, such as adjusting the product specifications or improving communication. After making the changes, I would follow up with the client to ensure they are satisfied.
Don't Just Read Can Maker Questions - Practice Answering Them!
Reading helps, but actual practice is what gets you hired. Our AI feedback system helps you improve your Can Maker interview answers in real-time.
Personalized feedback
Unlimited practice
Used by hundreds of successful candidates
Can Maker Position Details
Related Positions
- End Maker
- Body Maker
- Pencil Maker
- Camera Maker
- Sign Maker
- Hair Weaver
- Lens Matcher
- Mat Maker
- Window Maker
- Rubber Stamp Maker
Similar positions you might be interested in.
Ace Your Next Interview!
Practice with AI feedback & get hired faster
Personalized feedback
Used by hundreds of successful candidates
Ace Your Next Interview!
Practice with AI feedback & get hired faster
Personalized feedback
Used by hundreds of successful candidates