Top 29 Rubber Stamp Maker Interview Questions and Answers [Updated 2025]
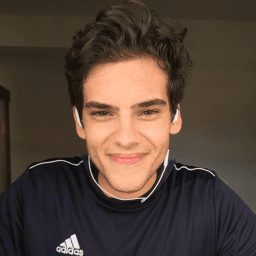
Andre Mendes
•
March 30, 2025
Are you preparing for a Rubber Stamp Maker job interview and want to make a remarkable impression? This comprehensive guide presents the most common interview questions tailored for this unique role, complete with example answers and insightful tips on how to respond effectively. Dive in to boost your confidence and ensure you're well-equipped to showcase your skills and expertise to potential employers.
Download Rubber Stamp Maker Interview Questions in PDF
To make your preparation even more convenient, we've compiled all these top Rubber Stamp Makerinterview questions and answers into a handy PDF.
Click the button below to download the PDF and have easy access to these essential questions anytime, anywhere:
List of Rubber Stamp Maker Interview Questions
Behavioral Interview Questions
Can you give an example of a time when your attention to detail caught a potential mistake in your work?
How to Answer
- 1
Think of a specific project where details were crucial.
- 2
Describe the mistake you caught and how you noticed it.
- 3
Explain the impact of catching the mistake on the project outcome.
- 4
Focus on the importance of detail in your role as a rubber stamp maker.
- 5
Conclude with how this experience reinforced your attention to detail.
Example Answers
In one project, I was preparing a custom stamp for a client's branding. While reviewing the design, I noticed the text was slightly misaligned. I corrected it before printing, ensuring the final product met the client's expectations and avoided rework.
Describe a challenging project you worked on as a rubber stamp maker and how you overcame the difficulties.
How to Answer
- 1
Choose a specific project that had significant challenges.
- 2
Clearly outline the difficulties you faced during the project.
- 3
Explain the steps you took to resolve the issues.
- 4
Highlight the results and what you learned from the experience.
- 5
Keep your answer focused and concise.
Example Answers
One challenging project involved creating a complex multi-color rubber stamp for a local business. The difficulty was aligning the colors perfectly. I created a template to ensure proper alignment and did several test runs before finalizing. The result was a beautiful stamp that delighted the client, and I learned the importance of precision planning.
Don't Just Read Rubber Stamp Maker Questions - Practice Answering Them!
Reading helps, but actual practice is what gets you hired. Our AI feedback system helps you improve your Rubber Stamp Maker interview answers in real-time.
Personalized feedback
Unlimited practice
Used by hundreds of successful candidates
Tell me about a time when you had to collaborate with others to complete an order of rubber stamps. What was your role?
How to Answer
- 1
Choose a specific project where collaboration was key.
- 2
Describe your individual contribution clearly.
- 3
Mention communication methods used with the team.
- 4
Highlight the outcome of the collaboration.
- 5
Reflect on what you learned from the experience.
Example Answers
In a recent rubber stamp project, our team needed to complete an order for a local business quickly. I organized a meeting to outline tasks, assigned roles based on each person's strengths, and I focused on the design aspect. By maintaining clear communication via chat and regular check-ins, we completed the order ahead of schedule, resulting in positive feedback from the client.
Describe a situation where you had to manage multiple orders at once. How did you prioritize your tasks?
How to Answer
- 1
Identify the main orders you had to manage.
- 2
Explain how you assessed the urgency and importance of each order.
- 3
Describe any tools or methods you used to stay organized.
- 4
Provide an example of how you communicated with clients about their orders.
- 5
Conclude with the results or outcomes of your prioritization.
Example Answers
In my previous job, I had to manage 5 different orders all due by the end of the week. I listed them out and prioritized based on delivery deadlines. I used a project management tool to track progress and communicated with clients about expected timelines. As a result, I completed all orders on time and received positive feedback.
Tell us about a time you introduced a new technique or tool in the rubber stamp making process. What impact did it have?
How to Answer
- 1
Select a specific technique or tool you introduced.
- 2
Explain why you felt it was necessary to make this change.
- 3
Describe the steps you took to implement it.
- 4
Share the results or impact it had on the process.
- 5
Keep your answer focused on your actions and the outcomes.
Example Answers
In my previous role, I introduced laser engraving for detailed stamp designs. I noticed that traditional methods couldn't replicate fine details. I researched laser tools, conducted trials, and trained the team on their use. This improved design accuracy and reduced production time by 30%.
Can you describe an instance when you handled a customer complaint about a rubber stamp? What resolution did you provide?
How to Answer
- 1
Listen carefully to the customer's issue and show empathy.
- 2
Clarify the specifics of the complaint about the rubber stamp.
- 3
Offer immediate solutions such as replacements or refunds.
- 4
Explain any corrective measures to prevent future issues.
- 5
Follow up with the customer to ensure satisfaction.
Example Answers
A customer complained that their custom rubber stamp wasn't clear. I listened to their concerns, clarified the specifics, and offered to remake the stamp at no extra cost. I ensured they received the new stamp within a week and followed up to confirm their satisfaction.
Describe a time when you had to adapt your usual process to meet a unique client requirement.
How to Answer
- 1
Identify a specific client requirement that was unusual.
- 2
Explain how you recognized the need to adapt your process.
- 3
Describe the steps you took to make the adjustment.
- 4
Highlight the positive outcome or client satisfaction from the change.
- 5
Keep your answer focused and relevant to the role of Rubber Stamp Maker.
Example Answers
A client requested a rubber stamp design with a very intricate logo that was outside of our usual specifications. I quickly assessed the design's detail and adapted my technique by using a finer engraving method that we typically reserve for special projects. The result was a highly detailed stamp that exceeded the client's expectations and reinforced our reputation for quality.
Give an example of a task in rubber stamp making where your manual dexterity was crucial for success.
How to Answer
- 1
Think of a specific task that requires precision.
- 2
Explain why manual dexterity is important in that task.
- 3
Describe a successful outcome due to your skills.
- 4
Use metrics or results to highlight your success when possible.
- 5
Keep your answer focused and concise.
Example Answers
When carving intricate designs for rubber stamps, my manual dexterity was crucial. I had to ensure that every detail was precise to avoid any errors. This resulted in high-quality stamps that consistently met client specifications without requiring rework.
Technical Interview Questions
What types of materials are commonly used in rubber stamp production, and how do they impact the final product?
How to Answer
- 1
Identify key materials like rubber, photopolymer, and wood.
- 2
Explain their roles in durability, detail, and usage.
- 3
Highlight how material choice affects the stamp's quality and print clarity.
- 4
Mention the environmental aspects of material selection if relevant.
- 5
Be prepared to discuss personal experience with these materials.
Example Answers
Common materials for rubber stamps include natural rubber, photopolymer, and wood. Rubber offers good durability and is ideal for detailed designs, while photopolymer allows for intricate designs and clearer impressions. The choice of material directly impacts the quality and lifespan of the stamp.
Can you explain the process of creating a custom rubber stamp from design to completion?
How to Answer
- 1
Start with understanding the client's design requirements
- 2
Create a digital design or prototype of the stamp
- 3
Choose the appropriate materials and stamp size
- 4
Use a laser engraver or carving tool to create the stamp
- 5
Assemble the stamp with the chosen handle and mount
Example Answers
First, I gather the client's design specifications and preferences. Then, I create a digital prototype using graphic design software. After confirming the design, I select the right materials, typically rubber and a suitable mounting base. I then laser engrave the design onto the rubber and finally assemble it with a handle for easy use.
Don't Just Read Rubber Stamp Maker Questions - Practice Answering Them!
Reading helps, but actual practice is what gets you hired. Our AI feedback system helps you improve your Rubber Stamp Maker interview answers in real-time.
Personalized feedback
Unlimited practice
Used by hundreds of successful candidates
What tools do you regularly use in rubber stamp making, and how does each tool contribute to the process?
How to Answer
- 1
List the key tools you use, such as carving tools, inks, and stamp bases.
- 2
Explain the purpose of each tool in the rubber stamp making process.
- 3
Provide specific examples of how you use each tool effectively.
- 4
Mention any techniques or best practices with each tool.
- 5
Keep your answer structured to show your knowledge and experience.
Example Answers
I regularly use carving tools to shape the design into the rubber. The X-Acto knife allows for precision cuts, while the gouges help in creating deeper lines for clearer impressions. I also use a stamp base that holds the rubber securely, and my ink pads ensure vibrant color application.
How do you create or modify digital designs for rubber stamps?
How to Answer
- 1
Use vector design software like Adobe Illustrator or CorelDRAW to create scalable designs.
- 2
Ensure the design is clear and simple, focusing on bold outlines for visibility when stamped.
- 3
Modify existing designs by adjusting shapes and colors, keeping the end use in mind to maintain clarity.
- 4
Test the design by printing a sample to see how it transfers to the rubber stamp.
- 5
Iterate based on feedback, making changes to ensure the final stamp meets quality and durability expectations.
Example Answers
I use Adobe Illustrator to create designs, focusing on bold lines that will print well on rubber. I often print a sample to check clarity before finalizing the design.
What techniques do you use to ensure precision when cutting the rubber for stamps?
How to Answer
- 1
Use a sharp, reliable carving tool to ensure clean cuts.
- 2
Follow guidelines or templates carefully to maintain accuracy.
- 3
Practice steady hand movements to control cutting lines.
- 4
Regularly check alignment and fit of the rubber to the stamp base.
- 5
Utilize measuring tools to gauge rubber thickness and dimensions.
Example Answers
I always use a sharp carving tool, as it creates clean cuts. I carefully follow the template lines and make sure to keep my hand steady while carving.
Describe the different types of inks used with rubber stamps and their applications.
How to Answer
- 1
Identify the main types of inks: dye-based, pigment-based, and solvent-based.
- 2
Explain the drying time and permanence of each ink type.
- 3
Mention specific applications for each ink type.
- 4
Consider the material of the surface being stamped on.
- 5
Conclude with a recommendation based on common use cases.
Example Answers
There are three main types of inks for rubber stamps: dye-based inks are quick-drying and great for paper, pigment-based inks are more permanent and suitable for porous surfaces, and solvent-based inks are used for non-porous surfaces like plastic.
What routine maintenance is necessary for the machines used in rubber stamp production?
How to Answer
- 1
Check and clean machine components regularly to prevent buildup of rubber and ink.
- 2
Lubricate moving parts to reduce wear and tear and ensure smooth operation.
- 3
Inspect blades and cutting tools for dullness and replace them as needed.
- 4
Calibrate machines periodically to maintain accuracy in stamp production.
- 5
Keep the machine environment clean to avoid contamination and damage.
Example Answers
Regular maintenance for rubber stamp machines includes cleaning components to avoid rubber buildup and lubricating moving parts to ensure they function smoothly.
What safety procedures do you follow when using cutting and engraving machines for stamp production?
How to Answer
- 1
Always wear appropriate personal protective equipment like safety goggles and gloves.
- 2
Keep the workstation clean and organized to prevent accidents.
- 3
Ensure all safety guards on machines are in place and functional before use.
- 4
Conduct a pre-operation inspection of the equipment to identify any issues.
- 5
Follow the manufacturer's instructions for the specific machine settings and operations.
Example Answers
When using cutting and engraving machines, I always wear safety goggles and gloves. I also make sure to keep my work area tidy and check that all safety guards are in place before I start.
How do you troubleshoot machinery problems in the stamp production process?
How to Answer
- 1
Identify the specific machine and its function in the process
- 2
Check for common issues such as jams or misalignments
- 3
Use the machine's manual to understand error codes and troubleshoot
- 4
Conduct systematic tests on components to isolate the problem
- 5
Document the issue and the steps taken to resolve it for future reference
Example Answers
In stamp production, I first identify the machine and its role. If there are jams, I check for misalignments. I refer to the manual for error codes, perform tests on parts, and document my findings.
Situational Interview Questions
A customer requests a last-minute order of custom stamps that would normally take more time to produce. How do you handle it?
How to Answer
- 1
Assess the urgency and customer needs clearly
- 2
Check production capacity for rush orders
- 3
Communicate openly about possible timelines
- 4
Offer alternatives if the request cannot be fulfilled
- 5
Follow up after delivery for customer satisfaction
Example Answers
I would first clarify the details and urgency of the request with the customer. Then, I would check if I have the capacity to complete the order in a rush. If possible, I would confirm a timeline and keep the customer informed throughout the process.
What would you do if a critical piece of equipment breaks down during a production run?
How to Answer
- 1
Assess the situation quickly to understand the impact on production.
- 2
Communicate immediately with your team and management about the issue.
- 3
Implement temporary workarounds if possible to minimize downtime.
- 4
Contact maintenance or technical support to repair the equipment.
- 5
Document the incident and review it later to improve processes.
Example Answers
I would first assess the situation to see how it affects our production targets. Then, I'd inform my team and management about the breakdown. If possible, I would implement a temporary workaround to keep some production going while we arrange for repairs.
Don't Just Read Rubber Stamp Maker Questions - Practice Answering Them!
Reading helps, but actual practice is what gets you hired. Our AI feedback system helps you improve your Rubber Stamp Maker interview answers in real-time.
Personalized feedback
Unlimited practice
Used by hundreds of successful candidates
A client changes their stamp design specifications at the last moment. How do you address this situation?
How to Answer
- 1
Listen carefully to the new specifications to understand the client's needs.
- 2
Communicate the implications of the changes on time and costs transparently.
- 3
Offer solutions that address the changes while managing expectations.
- 4
Reassure the client of your commitment to meeting their new requirements.
- 5
Document the changes to avoid misunderstandings later.
Example Answers
I would start by listening carefully to the client's new specifications to fully understand what they want. Then, I would explain how these changes might affect our timeline and costs. I would suggest ways to adapt the design while ensuring we stay on track.
You notice a batch of stamps has a quality defect after production. What steps do you take to resolve the issue?
How to Answer
- 1
Identify the specific defects in the stamps.
- 2
Communicate the issue to the production team immediately.
- 3
Stop the production line if necessary to prevent further defective products.
- 4
Analyze the cause of the defects by reviewing production processes and materials used.
- 5
Implement corrective measures and conduct a quality check on the next batch.
Example Answers
First, I would inspect the defective stamps to identify the specific issues. Then, I would notify the production team and halt the current production if the defects are widespread. Next, I would analyze our production process to find the cause and implement changes before we resume production. Finally, I would ensure that we carry out quality checks on future batches to prevent a recurrence.
How would you handle a situation where you unexpectedly run out of a critical material for rubber stamp production?
How to Answer
- 1
Stay calm and assess the situation quickly
- 2
Check inventory for alternative materials or substitutes
- 3
Communicate with your supervisor or team about the issue
- 4
Explore emergency suppliers or vendors for immediate restocking
- 5
Document the incident to improve future inventory management
Example Answers
If I run out of a critical material, I would first assess what we have in stock to see if there are any suitable alternatives. Then, I would inform my supervisor about the situation and work together to find a solution such as ordering from an emergency supplier.
A client is dissatisfied with the final stamp product. How do you rectify the situation?
How to Answer
- 1
Listen closely to the client's concerns and understand their dissatisfaction
- 2
Apologize for the inconvenience caused by the product
- 3
Offer to fix the issue by either redoing the stamp or providing a replacement
- 4
Ensure clear communication about the steps you will take to resolve the issue
- 5
Follow up with the client after the resolution to ensure they are satisfied
Example Answers
I would start by listening carefully to the client's concerns and apologizing for any mistakes. After understanding the problem, I would offer to remake the stamp to meet their expectations, and keep them informed throughout the process.
You identify an inefficiency in the stamp production process. How would you propose and implement a solution?
How to Answer
- 1
Define the specific inefficiency you observed.
- 2
Suggest a measurable solution to address the inefficiency.
- 3
Explain how you would gather input from the team for buy-in.
- 4
Outline a simple implementation plan with clear steps.
- 5
Discuss how you would measure the success of the solution.
Example Answers
I noticed that our ink drying time is too long, causing delays. I propose we switch to a faster-drying ink. I would present this idea to the team and gather their feedback. Then, we could do a small test on the production line and assess the drying time compared to our current process.
How would you manage a large bulk order of stamps with varying designs and tight deadlines?
How to Answer
- 1
Break down the order into smaller tasks to manage efficiently
- 2
Prioritize designs based on complexity and deadline requirements
- 3
Use a production schedule to allocate resources and time effectively
- 4
Establish clear communication with team members and clients about progress
- 5
Ensure quality control checks are in place to maintain standards throughout the process
Example Answers
I would start by breaking down the bulk order into smaller production tasks, prioritizing the more complex designs first to ensure they are completed ahead of the deadline. I would then create a detailed production schedule to allocate our resources effectively and communicate regularly with my team to track our progress.
How do you handle a disagreement with a colleague about the best approach to fulfilling a complex order?
How to Answer
- 1
Listen actively to your colleague's perspective
- 2
Acknowledge their points and show understanding
- 3
Suggest a compromise or a combined approach
- 4
Focus on the project's goals rather than personal opinions
- 5
Follow up with a discussion on the results after implementation
Example Answers
I first listen carefully to my colleague's approach, acknowledging their expertise. Then, I suggest we combine our ideas to create a solution that meets the client's expectations while also considering any limitations we have.
How would you approach the task of developing a new type of stamp for a specific client need?
How to Answer
- 1
Understand the client's specific requirements and expectations
- 2
Research similar stamp designs for inspiration
- 3
Sketch initial ideas and concepts based on client needs
- 4
Select suitable materials and techniques for the stamp production
- 5
Test prototypes and gather feedback from the client
Example Answers
I would start by discussing the client's requirements in detail to ensure I understand their vision. Then, I would look at existing designs to generate ideas, sketch a few concepts, and choose materials that suit the purpose, before creating a prototype and refining it based on the client's feedback.
Don't Just Read Rubber Stamp Maker Questions - Practice Answering Them!
Reading helps, but actual practice is what gets you hired. Our AI feedback system helps you improve your Rubber Stamp Maker interview answers in real-time.
Personalized feedback
Unlimited practice
Used by hundreds of successful candidates
You observe a coworker not following safety protocols. How do you handle this situation to ensure a safe working environment?
How to Answer
- 1
Address the situation immediately and privately with the coworker.
- 2
Express your concern for their safety and potential risks to others.
- 3
Encourage them to adhere to safety protocols and explain the importance.
- 4
If the behavior continues, inform a supervisor of the situation.
- 5
Always promote a culture of safety and support among team members.
Example Answers
I would approach my coworker privately and say, 'I noticed you weren't following the safety protocols. I’m concerned about your safety, and it's important we all adhere to these guidelines.' Then I would encourage them to follow the protocols and remind them why they're important.
Rubber Stamp Maker Position Details
Related Positions
- Stamp Maker
- Pencil Maker
- Pen Maker
- Reed Maker
- Plastic Maker
- Sign Maker
- Cushion Maker
- Mat Maker
- Stem Maker
- Camera Maker
Similar positions you might be interested in.
Ace Your Next Interview!
Practice with AI feedback & get hired faster
Personalized feedback
Used by hundreds of successful candidates
Ace Your Next Interview!
Practice with AI feedback & get hired faster
Personalized feedback
Used by hundreds of successful candidates