Top 30 Pen Maker Interview Questions and Answers [Updated 2025]
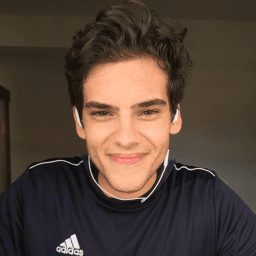
Andre Mendes
•
March 30, 2025
Are you preparing for a Pen Maker role and want to shine in your interview? This blog post is your go-to guide, featuring the most common interview questions for aspiring pen makers. Discover example answers and insightful tips on how to respond effectively, ensuring you make a memorable impression. Dive in and equip yourself with the confidence to ace your interview!
Download Pen Maker Interview Questions in PDF
To make your preparation even more convenient, we've compiled all these top Pen Makerinterview questions and answers into a handy PDF.
Click the button below to download the PDF and have easy access to these essential questions anytime, anywhere:
List of Pen Maker Interview Questions
Technical Interview Questions
What materials would you consider ideal for making pen bodies and tips, and why?
How to Answer
- 1
Identify common materials used in pen manufacturing.
- 2
Explain the properties that make each material suitable.
- 3
Consider aesthetics and functionality in your choices.
- 4
Mention durability and user comfort as key factors.
- 5
Relate your choices to the target market for the pen.
Example Answers
For pen bodies, I would recommend aluminum for its lightweight nature and durability, and for tips, stainless steel due to its resistance to wear and corrosion. These materials combine elegance with practicality, appealing to both professionals and everyday users.
Can you explain the steps involved in the injection molding process?
How to Answer
- 1
Start with the introduction of the material into the injection molding machine.
- 2
Explain how the material is heated and melted before injection.
- 3
Describe the injection phase where the melted material is injected into the mold.
- 4
Mention the cooling stage where the material solidifies in the mold.
- 5
Conclude with the ejection process where the final product is removed from the mold.
Example Answers
The injection molding process begins with loading plastic pellets into the injector. The pellets are then heated until they melt. Once melted, the material is injected into a mold where it cools and solidifies. Finally, the mold opens, and the finished product is ejected.
Don't Just Read Pen Maker Questions - Practice Answering Them!
Reading helps, but actual practice is what gets you hired. Our AI feedback system helps you improve your Pen Maker interview answers in real-time.
Personalized feedback
Unlimited practice
Used by hundreds of successful candidates
What design software are you proficient in, and how have you used it in your past projects?
How to Answer
- 1
Identify the key design software relevant to pen making.
- 2
Briefly describe your proficiency level with each software.
- 3
Give specific examples of projects where you utilized the software.
- 4
Highlight any unique features you leveraged in the software.
- 5
Discuss the outcome and impact of your design work.
Example Answers
I am proficient in Adobe Illustrator and have used it extensively in designing pen graphics for product mockups. In a recent project, I designed a new pen series that increased customer engagement by 20%.
How do you approach creating a production plan for a new pen model?
How to Answer
- 1
Identify the key features and materials required for the new pen model
- 2
Determine production methods and machinery needed
- 3
Establish a timeline for each stage of production
- 4
Consider quality control processes throughout production
- 5
Plan for logistics, including storage and distribution
Example Answers
I start by defining the key features and materials for the new pen, like the type of ink and casing. Next, I assess the production methods required, whether we'll need special machines or tooling. Then, I set a timeline for every production phase, making sure to incorporate quality control checks. Finally, I plan how we will store and distribute the pens once they're produced.
What methods do you use to ensure product quality throughout the manufacturing process?
How to Answer
- 1
Implement regular quality control checks at each stage of production
- 2
Use standardized processes to maintain consistency
- 3
Provide ongoing training for workers on quality standards
- 4
Collect feedback and data to identify areas for improvement
- 5
Incorporate advanced testing methods for final products
Example Answers
I ensure product quality by conducting regular quality control checks at each stage of the manufacturing process. This helps catch any defects early.
How would you design a reliability test for a new pen model?
How to Answer
- 1
Identify key performance metrics like ink flow and write consistency
- 2
Determine environmental conditions the pen will be exposed to
- 3
Create a testing protocol that simulates everyday usage
- 4
Define sample size and duration for comprehensive testing
- 5
Analyze results for failure modes and improve design accordingly
Example Answers
I would first identify key metrics such as ink flow and smoothness. Then, I would simulate different environmental conditions, like varying temperatures and humidity, to test the pen's durability. I’d use a sample size of 100 pens over a two-week period for extensive reliability data.
Describe your approach to optimizing manufacturing processes for higher efficiency.
How to Answer
- 1
Analyze current processes to identify bottlenecks and inefficiencies
- 2
Implement lean manufacturing techniques to reduce waste
- 3
Utilize data analytics to monitor performance and inform decisions
- 4
Encourage team feedback to identify practical improvements
- 5
Regularly review and adjust processes based on results
Example Answers
My approach starts with analyzing existing processes to spot bottlenecks. I focus on implementing lean techniques to cut waste. By using data to track our performance, I can make informed adjustments that enhance efficiency over time.
What factors do you consider when selecting tooling for manufacturing pens?
How to Answer
- 1
Evaluate the materials used for the pen and their compatibility with tooling.
- 2
Consider the production volume to determine necessary tooling durability and efficiency.
- 3
Assess the precision required for the pen's components and select tooling accordingly.
- 4
Think about the cost-effectiveness of tooling options in relation to the budget.
- 5
Factor in the ease of maintenance and availability of support for the tooling.
Example Answers
When selecting tooling for manufacturing pens, I first evaluate the materials used, such as plastic or metal, to ensure the tooling is compatible. I also consider the production volume to choose the right durability and efficiency level needed. Lastly, I focus on the precision required for the pen's tip to ensure a smooth writing experience.
What considerations do you take into account when formulating ink for pens?
How to Answer
- 1
Consider the viscosity for smooth flow and consistency.
- 2
Think about color intensity and how it affects visibility.
- 3
Evaluate drying time to prevent smudging and enhance usability.
- 4
Factor in ingredients for longevity and resistance to fading.
- 5
Ensure safety and non-toxicity of all ink components.
Example Answers
When formulating ink, I prioritize viscosity to ensure it flows well while writing. I also focus on creating rich colors that stand out and evaluate drying times to minimize smudging during writing.
What assembly methods do you find most efficient for pen production?
How to Answer
- 1
Discuss specific assembly techniques used in pen production, such as automated vs. manual assembly.
- 2
Mention any technology or machinery that enhances efficiency.
- 3
Relate your answer to quality control and consistency in pen performance.
- 4
Provide examples of methods you have used or observed in previous roles.
- 5
Be prepared to explain why you consider certain methods more effective.
Example Answers
In my experience, automated assembly methods using precision machinery significantly improve efficiency. These methods reduce human error and increase output, especially in mass production.
Don't Just Read Pen Maker Questions - Practice Answering Them!
Reading helps, but actual practice is what gets you hired. Our AI feedback system helps you improve your Pen Maker interview answers in real-time.
Personalized feedback
Unlimited practice
Used by hundreds of successful candidates
Behavioral Interview Questions
Describe a time when you had to solve a challenging design problem in your previous projects.
How to Answer
- 1
Choose a specific project where you faced a significant challenge.
- 2
Explain the problem clearly and its impact on the project.
- 3
Describe the steps you took to solve the problem.
- 4
Highlight any innovative or creative solutions you implemented.
- 5
Conclude with the successful outcome and what you learned.
Example Answers
In my last project, I was tasked with designing a new pen that could maintain a consistent ink flow. The challenge was that initial prototypes kept clogging. I researched different ink formulations and tested several nib designs. Ultimately, I combined a broader nib with a specific ink type, resulting in a pen that was both reliable and popular. The project not only met deadlines but also exceeded sales projections by 30%.
Give an example of how you introduced a creative solution to improve a product's design or functionality.
How to Answer
- 1
Think of a specific instance where you identified a problem in a product.
- 2
Describe the creative solution you proposed clearly and succinctly.
- 3
Explain how your solution improved the product's design or functionality.
- 4
Mention any feedback or results that came from implementing your solution.
- 5
Keep your response focused on your role and contributions.
Example Answers
In my previous role, I noticed that our pen's grip was uncomfortable for users during long writing sessions. I proposed using a gel material for the grip, which allowed for better comfort and control. After implementing the new design, we received positive feedback from customers, leading to a 20% increase in sales for that product line.
Don't Just Read Pen Maker Questions - Practice Answering Them!
Reading helps, but actual practice is what gets you hired. Our AI feedback system helps you improve your Pen Maker interview answers in real-time.
Personalized feedback
Unlimited practice
Used by hundreds of successful candidates
Tell us about a time when you worked closely with a team to achieve a manufacturing goal.
How to Answer
- 1
Choose a specific project that demonstrates teamwork in manufacturing.
- 2
Highlight your role and contributions to the team effort.
- 3
Mention the goal and how the team collaborated to achieve it.
- 4
Discuss any challenges faced and how you overcame them together.
- 5
Emphasize the results and what you learned from the experience.
Example Answers
In my last role, our team worked on launching a new pen model. I coordinated with design and production to ensure specifications were met. We faced supply chain delays, but by working closely and reallocating resources, we launched on time, resulting in a successful product rollout.
Describe a situation where you had to manage multiple projects with tight deadlines. How did you handle it?
How to Answer
- 1
Identify specific projects and deadlines you managed.
- 2
Explain your prioritization process and tools used.
- 3
Discuss communication with team members or stakeholders.
- 4
Share any challenges faced and how you overcame them.
- 5
Conclude with the results or outcomes of your efforts.
Example Answers
In my previous position, I managed three design projects simultaneously with overlapping deadlines. I prioritized tasks by deadlines and used a project management tool to keep track. Regular check-ins with my team ensured everyone was aligned. One challenge was a delay in supplies, but I proactively sourced alternatives. In the end, all projects were delivered on time and received positive feedback.
Can you provide an example of when you identified a quality issue and how you resolved it?
How to Answer
- 1
Choose a specific instance from your experience.
- 2
Describe the quality issue clearly and its impact.
- 3
Explain the steps you took to identify the root cause.
- 4
Discuss the actions you implemented to resolve the issue.
- 5
Conclude with the outcome and what you learned from the experience.
Example Answers
In my previous role as a pen manufacturer, I noticed that some pens were leaking ink. I analyzed production reports and discovered that the issue was due to a faulty batch of nibs. I contacted the supplier, returned the defective parts, and implemented a quality check for new batches. As a result, we saw a 30% reduction in leaks over the next month.
Tell me about a time when you led a team through a complex project. What was your strategy and outcome?
How to Answer
- 1
Choose a specific project with clear challenges.
- 2
Explain your leadership role and decision-making process.
- 3
Highlight teamwork and collaboration among team members.
- 4
Discuss strategies you used to overcome obstacles.
- 5
Conclude with measurable outcomes or successes achieved.
Example Answers
In my previous role, I led a team of five in developing a new pen design. We faced tight deadlines and design challenges. I organized brainstorming sessions to encourage all team members to share ideas. We prioritized tasks and used a project management tool to track progress. As a result, we completed the project two weeks early, and the new design increased sales by 15%.
Describe a time when you implemented a continuous improvement initiative in manufacturing.
How to Answer
- 1
Choose a specific example from your experience.
- 2
Highlight the problem you identified and the data you analyzed.
- 3
Explain the steps you took to implement the improvement.
- 4
Mention the results and impact on the production process.
- 5
Use clear metrics to demonstrate success.
Example Answers
In my previous job, I noticed that our pen assembly line had frequent downtimes due to machine jams. I collected data on the jams and discovered they were mostly due to incorrect loading of materials. I implemented a training session for operators that focused on proper material handling. This reduced machine jams by 30%, increasing our overall productivity.
Give an example of how you spearheaded an innovation that significantly improved a product's performance.
How to Answer
- 1
Identify a specific innovation you led.
- 2
Explain the problem that existed with the product.
- 3
Detail the steps you took to implement the innovation.
- 4
Quantify the improvements in performance with data if possible.
- 5
Reflect on the impact of this innovation on the team or company.
Example Answers
I led an initiative to redesign the ink cartridge for our premier line of pens. We noticed frequent complaints about ink consistency. By collaborating with the R&D team, we tested new materials for the cartridge which improved ink flow. As a result, we saw a 30% reduction in customer complaints and a 15% increase in sales for that product line.
Tell us how you handled a situation where meeting a customer's requirements involved significant changes to your processes.
How to Answer
- 1
Identify the specific customer requirement that triggered the need for process changes.
- 2
Explain the steps you took to assess the impact of these changes on your team and operations.
- 3
Discuss the collaboration with stakeholders to implement the necessary adjustments.
- 4
Share the outcome of the changes and how it benefited the customer.
- 5
Mention any lessons learned or improvements made for future situations.
Example Answers
In a recent project, a client requested a custom pen design that required a new production method. I organized a meeting with our production team to evaluate the feasibility and outlined the necessary changes. We collaborated on a new workflow and successfully delivered the pens ahead of schedule, enhancing customer satisfaction.
Situational Interview Questions
You need to reduce production costs without sacrificing quality. What steps would you take?
How to Answer
- 1
Analyze current production processes for inefficiencies
- 2
Negotiate bulk purchase agreements with suppliers
- 3
Implement new technologies or automation to enhance efficiency
- 4
Train staff to improve skills and reduce errors
- 5
Regularly review and optimize inventory management
Example Answers
I would start by examining our current production methods to identify any inefficiencies. Then, I would look to negotiate better deals with suppliers to reduce material costs. Implementing a small scale of automation could also help streamline processes and improve output without compromising quality.
A client requests a new pen design with specific features. How would you approach this project?
How to Answer
- 1
Clarify the client's requirements to ensure understanding
- 2
Research existing designs and trends for inspiration
- 3
Sketch initial concepts based on features requested
- 4
Gather feedback from the client early in the design process
- 5
Iterate on the design based on feedback and functionality
Example Answers
I would start by asking the client specific questions to clarify their requirements and expectations. Then, I would look into current pen designs for inspiration and sketch some initial concepts. Afterward, I would present these sketches to the client for feedback and refine the design accordingly.
Don't Just Read Pen Maker Questions - Practice Answering Them!
Reading helps, but actual practice is what gets you hired. Our AI feedback system helps you improve your Pen Maker interview answers in real-time.
Personalized feedback
Unlimited practice
Used by hundreds of successful candidates
Suppose a key supplier fails to deliver on time. What is your plan of action?
How to Answer
- 1
Assess the situation immediately to understand the impact on production.
- 2
Communicate with the supplier to find out the cause of the delay and when they expect to resolve it.
- 3
Develop a temporary solution, such as alternative suppliers or adjusting production schedules.
- 4
Keep all stakeholders informed of the situation and any changes to plans.
- 5
Document the incident for future reference and build a contingency plan.
Example Answers
First, I would assess how the delay affects our production schedule. Then, I would contact the supplier for details on the delay and their expected resolution time. Meanwhile, I would look for alternative suppliers who can provide the materials we need urgently. I would keep the team updated with any changes and document the incident for future planning.
Your primary manufacturing equipment fails unexpectedly. How do you handle the situation?
How to Answer
- 1
Assess the failure and identify the cause immediately.
- 2
Communicate with the team and inform them of the situation.
- 3
Implement emergency protocols if available.
- 4
Coordinate with maintenance or technical support for repairs.
- 5
Plan for alternative methods to minimize production disruption.
Example Answers
First, I would quickly assess the equipment to determine the nature of the failure and communicate with my team to keep everyone informed. If we have emergency protocols, I'd follow those. I would contact maintenance right away for repairs while considering any backup equipment to keep production moving.
How would you handle a request to innovate and create a pen with sustainable materials?
How to Answer
- 1
Research current sustainable materials suitable for pen manufacturing
- 2
Discuss potential partnerships with suppliers of eco-friendly materials
- 3
Consider the cost implications and how to keep the price competitive
- 4
Emphasize user experience and design aesthetics alongside sustainability
- 5
Prepare to iterate on designs based on feedback and sustainability metrics
Example Answers
I would start by researching biodegradable plastics or recycled materials that can be used for the pen. Then, I would engage with suppliers who specialize in sustainable materials to discuss options. Ensuring the pen remains cost-effective is essential, so I’d work on designs that balance sustainability with usability, iterating based on user feedback.
You discover a disagreement between team members affecting productivity. How would you resolve it?
How to Answer
- 1
Identify the core issue by listening to both parties.
- 2
Facilitate a meeting in a neutral space to discuss the disagreement.
- 3
Encourage open communication and respect for differing opinions.
- 4
Help the team members to compromise or find common ground.
- 5
Follow up after the discussion to ensure the resolution is effective.
Example Answers
I would first sit down with each team member separately to understand their perspectives on the issue. Then, I would bring them together in a neutral setting to talk it out, ensuring we focus on finding a compromise that works for both sides. Finally, I would check in later to see how things are going.
A customer reports a recurring issue with one of your pen models. How would you address the feedback?
How to Answer
- 1
Listen carefully to the customer's feedback without interrupting.
- 2
Ask clarifying questions to fully understand the issue.
- 3
Apologize for the inconvenience caused and assure the customer it will be addressed.
- 4
Investigate the reported issue with the production or quality team.
- 5
Follow up with the customer after implementing changes to ensure satisfaction.
Example Answers
I would first listen to the customer’s feedback attentively and ask them to elaborate on the recurring issue. Then, I would apologize for the inconvenience and assure them I will look into it. Afterward, I would coordinate with our production team to investigate and resolve the issue, and I would make sure to follow up with the customer once we have made changes.
If demand for a pen suddenly increases, what steps would you take to scale production effectively?
How to Answer
- 1
Assess current production capacity and identify bottlenecks.
- 2
Increase workforce by hiring temporary staff or reallocating existing employees.
- 3
Expand production hours with overtime shifts or additional shifts.
- 4
Source raw materials quickly to maintain supply chain continuity.
- 5
Implement lean manufacturing techniques to improve efficiency.
Example Answers
I would first assess our current production capacity and pinpoint any bottlenecks. Then, I’d hire additional temporary staff to help meet demand and consider extending production hours to accommodate more shifts.
How will you adapt your manufacturing process to comply with new environmental regulations?
How to Answer
- 1
Research the specific regulations and their requirements.
- 2
Identify areas in the current process that need improvement.
- 3
Consider sustainable materials and eco-friendly practices.
- 4
Implement training for staff on new practices.
- 5
Monitor compliance and adjust the process as necessary.
Example Answers
I will begin by thoroughly researching the new regulations to understand what changes are needed. Then, I will assess our current manufacturing process to identify areas where we can reduce waste and incorporate sustainable materials, such as recyclable plastics for pen bodies.
The market demands a revolutionary pen feature. How would you go about developing it?
How to Answer
- 1
Identify current market trends and customer pain points related to writing instruments.
- 2
Brainstorm innovative features that could enhance the user experience and meet market needs.
- 3
Conduct surveys or focus groups to validate ideas and gather user feedback.
- 4
Prototype the most promising features for testing and refinement.
- 5
Develop a marketing strategy to effectively launch the new pen feature.
Example Answers
I would start by researching market trends and user feedback to pinpoint what features are currently lacking. After identifying a need for a multifunctional pen, I would brainstorm ideas that combine writing with digital tools. Once I have a prototype, I would gather feedback to refine the design before launching it with a targeted marketing campaign.
Don't Just Read Pen Maker Questions - Practice Answering Them!
Reading helps, but actual practice is what gets you hired. Our AI feedback system helps you improve your Pen Maker interview answers in real-time.
Personalized feedback
Unlimited practice
Used by hundreds of successful candidates
Given limited resources, how would you prioritize tasks in a high-demand production period?
How to Answer
- 1
Assess the urgency and importance of tasks.
- 2
Communicate with team members to understand their capabilities.
- 3
Identify bottlenecks in the production process.
- 4
Focus on high-impact tasks that align with business goals.
- 5
Adapt your plan as new information or challenges arise.
Example Answers
I would start by evaluating all tasks based on their urgency and impact on production. I would communicate with my team to see who can handle priority tasks and address any bottlenecks together. This way, we ensure that we focus on the tasks that will fulfill the most critical orders first.
Pen Maker Position Details
Salary Information
Related Positions
- Pencil Maker
- Pad Maker
- Sign Maker
- Camera Maker
- Desk Maker
- Pad Hand
- Fly Maker
- Body Maker
- Stamp Maker
- Frame Maker
Similar positions you might be interested in.
Ace Your Next Interview!
Practice with AI feedback & get hired faster
Personalized feedback
Used by hundreds of successful candidates
Ace Your Next Interview!
Practice with AI feedback & get hired faster
Personalized feedback
Used by hundreds of successful candidates