Top 29 Desk Maker Interview Questions and Answers [Updated 2025]
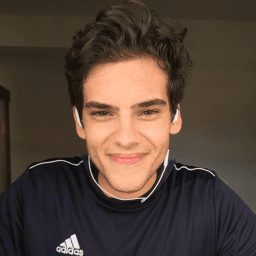
Andre Mendes
•
March 30, 2025
Preparing for a Desk Maker interview can be daunting, but we're here to help. In this post, you'll find a comprehensive list of the most common interview questions for aspiring Desk Makers, complete with example answers and insightful tips on how to respond effectively. Whether you're a seasoned professional or a newcomer, these insights will help you confidently showcase your skills and land the job.
Download Desk Maker Interview Questions in PDF
To make your preparation even more convenient, we've compiled all these top Desk Makerinterview questions and answers into a handy PDF.
Click the button below to download the PDF and have easy access to these essential questions anytime, anywhere:
List of Desk Maker Interview Questions
Behavioral Interview Questions
Can you describe a time when you successfully completed a complex woodworking project? What challenges did you face and how did you overcome them?
How to Answer
- 1
Choose a specific project that highlights your skills
- 2
Mention the complexity and unique aspects of the project
- 3
Identify the key challenges you faced during the project
- 4
Explain the strategies or techniques you used to overcome those challenges
- 5
Conclude with the successful outcome and what you learned from it
Example Answers
In my last project, I built a custom dining table that required precise joinery and large wood pieces. The complexity was in ensuring stability and alignment due to the size. I faced initial challenges with the wood warp, but I overcame it by acclimating the wood and using a jig for consistent cuts. The project was a success and I learned the importance of preparation.
Tell me about a time when you worked as part of a team to meet a production deadline. What was your role and how did you ensure quality was maintained?
How to Answer
- 1
Identify a specific project where teamwork was key.
- 2
Highlight your role and responsibilities within the team.
- 3
Explain the strategies used to meet the deadline.
- 4
Discuss how you ensured quality during the process.
- 5
Consider incorporating team communication and collaboration methods.
Example Answers
In my previous role, we had a project to produce 100 desks in a month. I was the team leader and coordinated between the designers and production staff. We held daily check-ins to track progress and addressed any issues immediately. To ensure quality, we implemented a quality control check at every stage of production, resulting in zero defects at delivery.
Don't Just Read Desk Maker Questions - Practice Answering Them!
Reading helps, but actual practice is what gets you hired. Our AI feedback system helps you improve your Desk Maker interview answers in real-time.
Personalized feedback
Unlimited practice
Used by hundreds of successful candidates
Describe a situation where you had to troubleshoot an issue in the desk-making process. What steps did you take?
How to Answer
- 1
Identify a specific issue you encountered during desk-making.
- 2
Explain the steps you took to analyze and diagnose the problem.
- 3
Describe the solution you implemented to resolve the issue.
- 4
Highlight any lessons learned or improvements made to the process.
- 5
Keep your answer focused on your direct actions and their impact.
Example Answers
During a production run, I noticed that the drawer slides were misaligned, causing the drawers to stick. I reviewed the assembly process and found that the slides were being installed too quickly, which led to errors. I proposed a training session for the team to ensure proper installation techniques and later implemented a quality check to catch issues early. This improved our workflow and reduced customer complaints.
Have you ever had to salvage a project that was not meeting quality standards? What actions did you take to resolve the issue?
How to Answer
- 1
Identify the specific quality issues encountered.
- 2
Describe the steps taken to address those issues.
- 3
Explain how you collaborated with your team or stakeholders.
- 4
Emphasize the results and improvements achieved.
- 5
Reflect on lessons learned from the experience.
Example Answers
In a recent project, we faced issues with inaccurate measurements in our designs. I organized a meeting with the team to address the problems and we re-evaluated our processes. We implemented a new double-check system for measurements and after reworking the designs, we managed to complete the project on time and within quality standards.
Give an example of how you handled a customer complaint about a product. What was the outcome?
How to Answer
- 1
Describe the customer complaint clearly and briefly.
- 2
Explain the steps you took to resolve the complaint.
- 3
Focus on your communication with the customer.
- 4
Highlight the outcome and what you learned.
- 5
Emphasize the importance of customer satisfaction.
Example Answers
A customer complained about a desk with a scratched surface. I immediately apologized and offered a replacement. I arranged for the old desk to be picked up and delivered a new one within two days. The customer appreciated the quick resolution and expressed satisfaction with our service.
Technical Interview Questions
What types of wood do you prefer for making durable desks, and why?
How to Answer
- 1
Mention specific types of wood known for durability.
- 2
Explain the characteristics that make these woods suitable.
- 3
Consider factors like cost, availability, and aesthetics.
- 4
Share personal preferences and experiences with these woods.
- 5
Highlight any sustainable practices if applicable.
Example Answers
I prefer using hardwoods like oak and maple for making durable desks because they are strong and resistant to wear. Oak has a great grain pattern, and it holds up well under heavy use.
What are the essential tools you use in desk making and how do you maintain them?
How to Answer
- 1
Identify key tools: list your main tools like saws, drills, and sanders
- 2
Explain how you use each tool for desk making
- 3
Discuss maintenance practices like cleaning and regular sharpening
- 4
Mention safety checks and using protective gear
- 5
Highlight any unique tools that improve your process
Example Answers
I rely on a table saw for cutting wood, a drill for assembling, and an orbital sander for finishing. I keep my tools clean and check their sharpness regularly to ensure precision and safety.
Don't Just Read Desk Maker Questions - Practice Answering Them!
Reading helps, but actual practice is what gets you hired. Our AI feedback system helps you improve your Desk Maker interview answers in real-time.
Personalized feedback
Unlimited practice
Used by hundreds of successful candidates
Explain the different types of joints you might use in constructing a desk and why you would choose one over another.
How to Answer
- 1
Identify key types of joints such as butt joints, dowel joints, and mortise and tenon.
- 2
Briefly explain the strengths and weaknesses of each joint type.
- 3
Discuss the factors influencing your choice, like aesthetics and strength.
- 4
Relate choices to specific desk design aspects, such as durability and ease of assembly.
- 5
Be concise and to the point, using technical terms appropriately.
Example Answers
For constructing a desk, I might use butt joints for simple assembly, which are easy but less strong. For sturdiness, I would opt for dowel joints that provide better alignment and strength. If aesthetic appeal and maximum strength are needed, I would choose mortise and tenon joints, as they create a very strong connection.
What finishing techniques do you employ to ensure the desk is aesthetically appealing and protected?
How to Answer
- 1
Discuss your choice of finishes like stains, paints, or oils that enhance the wood grain.
- 2
Mention protective coatings such as varnishes or lacquers that add durability.
- 3
Explain the importance of sanding and preparation for a smooth finish.
- 4
Talk about how you ensure color consistency and application techniques.
- 5
Include any environmentally friendly finishes you may use.
Example Answers
I typically use high-quality stains to enhance the natural grain of the wood, followed by a durable polyurethane varnish to protect the surface from scratches and moisture.
How do you ensure precision in your measurements and cuts when constructing a desk?
How to Answer
- 1
Always use a high-quality measuring tape or ruler for accurate measurements
- 2
Double-check measurements before making cuts to avoid mistakes
- 3
Utilize clamps and jigs to stabilize materials during cutting
- 4
Make test cuts on scrap material to verify settings and accuracy
- 5
Keep tools well-maintained to ensure clean and precise cuts
Example Answers
I always use a reliable measuring tape and double-check my measurements before cutting. I also make sure to use clamps to secure the wood, which helps maintain precision.
What safety precautions do you take when operating power tools in woodwork?
How to Answer
- 1
Always wear appropriate personal protective equipment such as safety goggles, gloves, and ear protection.
- 2
Inspect power tools before use to ensure they are in good working condition and free from defects.
- 3
Keep your workspace clean and organized to prevent accidents and falls.
- 4
Ensure that you are familiar with the tool's operation and follow the manufacturer’s instructions.
- 5
Be mindful of your surroundings and keep bystanders at a safe distance while operating power tools.
Example Answers
I always wear safety goggles and gloves when using power tools to protect my eyes and hands. I also check the equipment before starting to ensure everything is functioning properly.
Have you used any design software for planning desk layouts or designs? Which ones?
How to Answer
- 1
Identify specific design software you have used.
- 2
Mention your level of proficiency with each software.
- 3
Share examples of projects where you used the software.
- 4
Highlight any relevant skills developed through your experience.
- 5
Connect your software skills to the desk maker role.
Example Answers
I have used AutoCAD for planning desk layouts. I am proficient in creating detailed designs, having worked on a project for a modern office layout where I designed multiple desk arrangements to optimize space.
How do you estimate the cost of materials and labor before starting a desk-making project?
How to Answer
- 1
List all the materials required for the project along with their costs.
- 2
Research current prices from suppliers for accuracy.
- 3
Calculate labor costs by estimating hours required and hourly wage.
- 4
Include waste and overage in your material cost estimation.
- 5
Document your calculations to justify the total estimated cost.
Example Answers
I start by listing all necessary materials like wood, screws, and varnish, then check current supplier prices. I also estimate the labor time needed and multiply it by my hourly wage to get total labor costs. To ensure I’m covered, I add about 10% more for waste in materials.
What are the key steps in assembling a desk to ensure stability and durability?
How to Answer
- 1
Start by laying out all parts and hardware to confirm nothing is missing.
- 2
Follow the manufacturer's instructions closely for proper assembly order.
- 3
Use appropriate tools to tighten screws and bolts securely.
- 4
Check for levelness by placing the desk on a flat surface before finalizing assembly.
- 5
Test the stability by gently shaking the assembled desk to ensure it does not wobble.
Example Answers
First, I would gather all parts and check that everything is accounted for. Then, I would follow the assembly instructions step by step, ensuring to secure all screws tightly using the right tools. After assembling, I would place the desk on a flat surface to check that it's level and finally, I would give it a gentle shake to confirm it's stable.
How do you perform quality checks during and after the desk-making process?
How to Answer
- 1
Inspect materials for defects before starting the build
- 2
Measure components to ensure accurate dimensions
- 3
Test the assembly for stability and functionality during each stage
- 4
Perform a final inspection for finish quality and overall appearance
- 5
Document any issues and corrective actions taken
Example Answers
I begin by inspecting all the materials for any visible defects before I start building. During the assembly, I measure each part to ensure everything is within specifications. Once the desk is assembled, I test its stability and functionality and check for any scratches or finish imperfections before handing it over.
Don't Just Read Desk Maker Questions - Practice Answering Them!
Reading helps, but actual practice is what gets you hired. Our AI feedback system helps you improve your Desk Maker interview answers in real-time.
Personalized feedback
Unlimited practice
Used by hundreds of successful candidates
Situational Interview Questions
Imagine a client orders a customized desk with a tight deadline. How would you prioritize tasks to ensure timely delivery?
How to Answer
- 1
Assess the client requirements early to understand key features and materials needed.
- 2
Create a timeline that breaks down tasks into manageable steps.
- 3
Prioritize based on task duration and dependencies; tackle high-impact tasks first.
- 4
Communicate with the team regularly to ensure everyone is aligned and on schedule.
- 5
Have contingency plans for potential delays or issues to keep delivery on track.
Example Answers
I would start by understanding the client's requirements in detail. Then, I'd create a timeline prioritizing tasks that are crucial for the desk's features. I would also keep the team updated to ensure we stick to our deadlines.
Suppose there is a shortage of your preferred wood for a project. What alternative steps would you take?
How to Answer
- 1
Identify substitute materials that can achieve a similar aesthetic or strength.
- 2
Consider adjusting the design to accommodate available wood types.
- 3
Consult with suppliers for alternative options or similar woods.
- 4
Evaluate the project timeline to see if waiting for preferred wood is feasible.
- 5
Communicate with stakeholders about the change in materials.
Example Answers
If my preferred wood is unavailable, I would first look for similar materials that can meet the project's standards. I would also discuss with suppliers to explore other wood types that might work for the design.
Don't Just Read Desk Maker Questions - Practice Answering Them!
Reading helps, but actual practice is what gets you hired. Our AI feedback system helps you improve your Desk Maker interview answers in real-time.
Personalized feedback
Unlimited practice
Used by hundreds of successful candidates
What would you do if you discovered a defect in a batch of desks ready to be shipped?
How to Answer
- 1
Immediately report the defect to your supervisor or quality control team
- 2
Assess the extent of the defect to understand how many desks are affected
- 3
Put a temporary hold on the shipment until the issue is resolved
- 4
Collaborate with the production team to determine the cause and fix it
- 5
Communicate transparently with any stakeholders affected by the delay
Example Answers
I would report the defect to my supervisor, assess how many desks are affected, and put a hold on the shipment until we resolve the issue. It's important to fix the problem before proceeding.
If a critical piece of machinery broke down, how would you minimize disruption to your production schedule?
How to Answer
- 1
Assess the situation quickly to understand the extent of the breakdown.
- 2
Notify the maintenance team immediately for a rapid response.
- 3
Implement a temporary workaround to keep production going if possible.
- 4
Communicate with your team about the issue and potential delays.
- 5
Evaluate backup resources or alternative machinery that could reduce downtime.
Example Answers
First, I would assess the breakdown to understand how it affects our production. Then, I'd notify the maintenance team to start repairs right away. If feasible, I would set up a temporary workaround to maintain production flow. Communication with my team would be key to manage expectations and adapt our schedule. Finally, I'd explore any backup machinery that could help minimize the disruption.
How would you negotiate with a client for additional time or resources on a project that has grown in scope?
How to Answer
- 1
Acknowledge the client's needs and concerns first
- 2
Clearly explain the reasons for the increased scope
- 3
Use data or examples to support your request
- 4
Propose specific additional time or resources needed
- 5
Offer solutions to mitigate impact on the project's timeline
Example Answers
I would first express my understanding of the project's importance to the client. Then I'd explain how the new requirements impact our initial timeline, providing specific examples. I would ask for an additional two weeks to complete the project to the best standard, emphasizing that this would enhance the final outcome.
What actions would you take if there was a safety incident in the workshop?
How to Answer
- 1
Assess the situation to determine the severity of the incident.
- 2
Ensure immediate safety for yourself and others in the area.
- 3
Notify a supervisor or follow the established reporting protocol.
- 4
Provide first aid if qualified and necessary.
- 5
Document the incident for future safety improvements.
Example Answers
I would first assess the incident to understand its severity. My priority would be to ensure that everyone is safe, then I would notify my supervisor and follow the proper reporting procedures. If any injuries occurred, I would provide first aid if I was trained to do so, and I would document the incident afterward.
If two team members had a disagreement impacting their work on the desk production line, how would you intervene?
How to Answer
- 1
Acknowledge the disagreement calmly without taking sides
- 2
Encourage both team members to express their views in a private setting
- 3
Identify the root cause of the disagreement through active listening
- 4
Facilitate a constructive discussion aimed at finding a mutual solution
- 5
Follow up to ensure the agreement is implemented and relations remain positive
Example Answers
I would approach the two team members separately to understand their perspectives and then bring them together to discuss their concerns in a constructive manner.
How would you approach designing a desk for a client who wants an innovative, non-traditional design?
How to Answer
- 1
Start by understanding the client's lifestyle and work habits.
- 2
Explore materials and shapes that are unconventional yet functional.
- 3
Incorporate elements of versatility, such as adjustable features.
- 4
Consider integrating technology seamlessly into the design.
- 5
Sketch multiple concepts to visualize different creative directions.
Example Answers
I would first hold a discussion with the client to learn about their daily activities and preferences. Then, I would explore unique materials like recycled wood or metal and consider shapes that break away from standard rectangular forms. For example, a curved desk could promote a collaborative atmosphere. Finally, I would incorporate tech features, such as built-in wireless charging pads.
What strategies would you use to stay within a tight budget while ensuring the quality of the desks?
How to Answer
- 1
Conduct thorough research on materials to find cost-effective options without compromising quality.
- 2
Optimize designs to reduce waste and improve efficiency in manufacturing.
- 3
Build strong relationships with suppliers to negotiate better pricing or bulk discounts.
- 4
Implement strict quality control measures to avoid costly rework or returns.
- 5
Regularly review project budgets and costs to identify potential savings opportunities.
Example Answers
I would start by researching alternative materials that maintain quality but are less expensive. Additionally, I would redesign our desks to minimize waste and maximize material usage.
A customer requests a feature you haven't implemented before in a desk. How would you approach this request?
How to Answer
- 1
Listen carefully to the customer's request and clarify any specifics.
- 2
Evaluate if the feature aligns with product goals and customer needs.
- 3
Engage with your team or stakeholders to discuss feasibility.
- 4
Offer the customer a timeline for evaluation or a follow-up meeting.
- 5
Keep the customer informed about progress and any decisions made.
Example Answers
I would first listen to the customer's request thoroughly and ask for any additional details. After that, I'd evaluate if the feature fits our current product strategy and consult with my team to explore its feasibility. If it's feasible, I'd keep the customer updated on our progress and set expectations for when they can expect a decision.
Don't Just Read Desk Maker Questions - Practice Answering Them!
Reading helps, but actual practice is what gets you hired. Our AI feedback system helps you improve your Desk Maker interview answers in real-time.
Personalized feedback
Unlimited practice
Used by hundreds of successful candidates
Describe how you would handle unforeseen complications like warping or splits discovered during construction.
How to Answer
- 1
Assess the issue calmly and identify the specific problem.
- 2
Communicate with the team about the issue and potential solutions.
- 3
Determine if repair is feasible or if replacement is necessary.
- 4
Document the issue and changes made for future reference.
- 5
Adjust timelines and budgets as needed based on the complication.
Example Answers
If I find warping during construction, I first evaluate the extent of the damage. I then discuss possible repairs or replacement with my team to make sure we make the best decision. I keep records of the issue and any adjustments we had to make to the timeline.
How would you manage an emergency order if it coincided with another major project deadline?
How to Answer
- 1
Assess the urgency and impact of the emergency order.
- 2
Communicate with stakeholders about potential delays or changes.
- 3
Prioritize tasks based on project timelines and resources.
- 4
Delegate responsibilities where possible to ensure timely completion.
- 5
Consider bringing in additional resources if necessary to meet both demands.
Example Answers
In a situation with an emergency order and another deadline, I would first assess the urgency of the emergency order compared to the existing project. Then, I would communicate with my team and stakeholders to inform them of the situation and discuss potential impacts. Prioritizing tasks, I would delegate less critical items to team members and focus on the most pressing needs to ensure both projects stay on track.
Suppose your main supplier raises prices unexpectedly. How would you adjust your operations?
How to Answer
- 1
Assess the impact of the price increase on your overall budget.
- 2
Explore alternative suppliers or materials to mitigate costs.
- 3
Evaluate the possibility of adjusting prices for your customers.
- 4
Consider optimizing your inventory management to reduce waste.
- 5
Communicate transparently with stakeholders about the changes.
Example Answers
If my main supplier raised prices, I would first analyze how this affects our budget and projected margins. After that, I would look for alternative suppliers to see if I could source materials at a lower cost. Additionally, I would communicate with our sales team to discuss if a price adjustment to our products is necessary to maintain profitability.
A client changes the design specifications midway through a project. How would you handle this situation?
How to Answer
- 1
Acknowledge the request and express willingness to adapt.
- 2
Assess the impact of the changes on the project timeline and budget.
- 3
Communicate openly with the client about the changes.
- 4
Propose solutions or adjustments that accommodate the new specifications.
- 5
Document any agreed-upon changes for clarity.
Example Answers
I would first acknowledge the client's request and discuss how it affects the timeline. I would explain any implications on the budget and propose a plan to implement the changes while keeping the client informed throughout.
Desk Maker Position Details
Recommended Job Boards
ZipRecruiter
www.ziprecruiter.com/Jobs/Desk-MakerThese job boards are ranked by relevance for this position.
Related Positions
- Table Maker
- Frame Maker
- Pad Maker
- Panel Maker
- Mat Maker
- Door Builder
- Button Maker
- Seat Maker
- Body Maker
- Bed Maker
Similar positions you might be interested in.
Ace Your Next Interview!
Practice with AI feedback & get hired faster
Personalized feedback
Used by hundreds of successful candidates
Ace Your Next Interview!
Practice with AI feedback & get hired faster
Personalized feedback
Used by hundreds of successful candidates