Top 29 Seat Maker Interview Questions and Answers [Updated 2025]
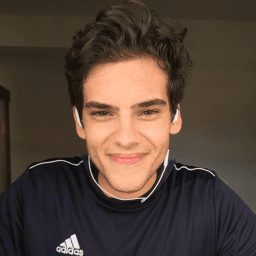
Andre Mendes
•
March 30, 2025
Are you gearing up for a Seat Maker interview and want to feel confident and prepared? Our latest post dives into the most common interview questions for the Seat Maker role, offering example answers and insightful tips on how to tackle them effectively. Whether you're a seasoned professional or new to the field, this guide will help you showcase your skills and make a lasting impression.
Download Seat Maker Interview Questions in PDF
To make your preparation even more convenient, we've compiled all these top Seat Makerinterview questions and answers into a handy PDF.
Click the button below to download the PDF and have easy access to these essential questions anytime, anywhere:
List of Seat Maker Interview Questions
Behavioral Interview Questions
Describe a time when your attention to detail prevented a significant mistake in your work.
How to Answer
- 1
Think of a specific situation where you caught an error before it became a problem
- 2
Be clear about the context and your role in the situation
- 3
Describe the mistake that could have happened and how you identified it
- 4
Explain what steps you took to correct or prevent the error
- 5
Highlight the positive outcome that resulted from your attention to detail
Example Answers
In my previous job as a quality control assistant, I noticed that a batch of materials did not meet the required specifications. I double-checked the measurements and found discrepancies. I reported this to my supervisor, which allowed us to halt production and adjust the process before any defective products were shipped, saving the company from potential returns.
Can you tell us about a challenging project where you had to solve an unexpected problem?
How to Answer
- 1
Choose a specific project where the problem was significant.
- 2
Describe the problem clearly and why it was unexpected.
- 3
Explain the steps you took to address the problem.
- 4
Highlight the outcome and what you learned from the experience.
- 5
Keep your answer focused and use the STAR method: Situation, Task, Action, Result.
Example Answers
In my last project, we were tasked with creating custom seats for a new model car. Midway through, we discovered that the materials ordered didn't meet safety standards. I immediately sourced alternative materials, collaborated with the supplier for expedited shipping, and worked overtime with my team to redesign the seats. In the end, we delivered on time, and my quick action saved the project from delays.
Don't Just Read Seat Maker Questions - Practice Answering Them!
Reading helps, but actual practice is what gets you hired. Our AI feedback system helps you improve your Seat Maker interview answers in real-time.
Personalized feedback
Unlimited practice
Used by hundreds of successful candidates
Give an example of a time when you had to work closely with a team to deliver a quality product.
How to Answer
- 1
Choose a specific project where teamwork was essential.
- 2
Highlight your role and contributions to the team effort.
- 3
Explain how collaboration improved the final product.
- 4
Include any challenges faced and how the team overcame them.
- 5
Conclude with the outcome and what you learned about teamwork.
Example Answers
In my last job, we worked on a custom seat design for a client. I led the design team, collaborating closely with engineers and fabricators. We faced challenges with material durability, but together we researched alternatives and tested options. The final product exceeded client expectations, leading to a 20% increase in sales for that line.
Describe a situation where you had to manage multiple projects at once. How did you prioritize your tasks?
How to Answer
- 1
Identify the projects and their requirements clearly
- 2
Use a method like Eisenhower Matrix to prioritize tasks
- 3
Communicate with stakeholders about deadlines and expectations
- 4
Adjust priorities based on project progress and urgency
- 5
Reflect on the outcome and what you learned from managing multiple projects
Example Answers
In my last role, I managed three projects simultaneously. I listed out all tasks and used an Eisenhower Matrix to prioritize them based on urgency and importance. I communicated regularly with my team to reassign tasks as needed and met all deadlines successfully.
Tell us about a time when you identified a quality issue in a product. How did you handle it?
How to Answer
- 1
Start with a specific example from your experience
- 2
Explain how you discovered the quality issue
- 3
Describe the steps you took to address it
- 4
Mention any collaboration with team members if applicable
- 5
Conclude with the outcome and what you learned
Example Answers
In my last position as a seat maker, I noticed that a batch of seats had inconsistent stitching patterns. I flagged the issue during our quality check and gathered my team to discuss potential causes. We traced it back to a malfunction in one of our sewing machines. I coordinated with maintenance to get the machine repaired and we re-evaluated our quality monitoring process. As a result, we reduced stitching errors by 30%.
How have you adapted to changes in technology or processes in past jobs?
How to Answer
- 1
Focus on a specific technology or process change you faced.
- 2
Describe your initial reaction and how you educated yourself.
- 3
Highlight any training or resources you utilized to adapt.
- 4
Share a positive outcome as a result of this adaptation.
- 5
Conclude with how this experience prepares you for future changes.
Example Answers
In my previous job, we switched to a new software for inventory management. I took the initiative to learn the new system by attending training sessions and practicing on a demo environment. As a result, I not only became proficient quickly but also helped train my colleagues, improving overall team efficiency.
Can you describe a time when you had to take a leadership role within your team?
How to Answer
- 1
Choose a specific situation that highlights your leadership skills.
- 2
Explain the challenge your team faced and why leadership was needed.
- 3
Describe your actions in detail and focus on your decision-making.
- 4
Highlight the positive outcome and what you learned from the experience.
- 5
Keep your answer structured: situation, task, action, result.
Example Answers
In my previous job, our team faced a tight deadline for a large order. I stepped up to organize daily check-in meetings and delegate tasks based on each member's strengths. Due to my leadership, we finished the project two days early, which impressed our client and strengthened team collaboration.
Technical Interview Questions
What are the most common materials used in seat manufacturing and what are their properties?
How to Answer
- 1
Identify key materials commonly used in seat construction.
- 2
Discuss the properties of each material that make it suitable for seating.
- 3
Consider comfort, durability, and maintenance aspects.
- 4
Mention any environmental considerations or trends in material choice.
- 5
Be prepared to relate your answer to manufacturing processes.
Example Answers
Common materials in seat manufacturing include foam, leather, and plastic. Foam provides comfort and cushioning, leather offers durability and an upscale feel, while plastic is lightweight and easy to clean. Each material serves specific purposes in comfort and maintenance.
What tools and equipment are essential for seat making, and how proficient are you in using them?
How to Answer
- 1
List specific tools like sewing machines, cutting tools, and upholstery materials.
- 2
Mention your experience level with each tool.
- 3
Provide examples of projects where you used these tools.
- 4
Highlight any training or certifications related to seat making tools.
- 5
Be prepared to discuss any limitations and how you plan to improve.
Example Answers
For seat making, essential tools include industrial sewing machines, staple guns, and cutting tools. I have 5 years of experience using sewing machines and have completed several upholstery projects. I also hold a certification in upholstery techniques.
Don't Just Read Seat Maker Questions - Practice Answering Them!
Reading helps, but actual practice is what gets you hired. Our AI feedback system helps you improve your Seat Maker interview answers in real-time.
Personalized feedback
Unlimited practice
Used by hundreds of successful candidates
How do you ensure that a seat design meets all required specifications and standards?
How to Answer
- 1
Review all design specifications and standards before starting.
- 2
Use CAD software to create detailed design models.
- 3
Conduct simulations to test the design under different conditions.
- 4
Collaborate with engineers to validate material choices and safety standards.
- 5
Perform prototype testing and gather feedback for improvements.
Example Answers
I ensure compliance by starting with a thorough review of design specifications, creating detailed CAD models, and conducting simulations to test performance. I also work closely with engineers to validate materials and safety standards before moving to prototype testing.
What safety standards must be considered during the seat manufacturing process?
How to Answer
- 1
Identify relevant safety regulations like ANSI and ISO standards in seating.
- 2
Discuss material safety, ensuring all materials are non-toxic and flame-retardant.
- 3
Mention the importance of structural integrity tests for seat durability.
- 4
Highlight ergonomic considerations to prevent user injury and improve safety.
- 5
Include the necessity of quality assurance processes to meet safety compliance.
Example Answers
During the seat manufacturing process, we must comply with ANSI standards, ensuring all materials used are non-toxic and meet flame-retardant requirements. We also conduct structural integrity tests to ensure durability and safety for end users.
Can you explain the different seat assembly techniques you are familiar with?
How to Answer
- 1
Identify the main types of assembly techniques you know.
- 2
Explain each technique clearly and concisely.
- 3
Provide examples of when you have used these techniques.
- 4
Highlight any specific tools or materials related to the techniques.
- 5
Mention any safety or quality standards observed during assembly.
Example Answers
I am familiar with three main assembly techniques: staple assembly, screw assembly, and welding. For example, in staple assembly, I have used pneumatic staple guns for quick and secure fastening of fabric to frames. I have used screw assembly for wooden and metal seat frames, ensuring they are sturdy. In welding, I focused on metal seats where strength is critical, always following safety standards.
Describe the process of fabricating a seat frame.
How to Answer
- 1
Start with material selection based on durability and comfort.
- 2
Outline the design specifications and dimensions required.
- 3
Explain the cutting and shaping of the materials to form the basic structure.
- 4
Describe the joining techniques such as welding or using brackets.
- 5
Mention any finishing processes such as sanding or applying protective coating.
Example Answers
First, I select the appropriate materials like steel or aluminum for strength. Then, I outline the necessary dimensions and create a design blueprint. I cut the materials to size and shape them into the frame structure. I join the pieces using welding to ensure durability and lastly, I finish the frame with a protective coating for rust resistance.
What are the steps involved in cushioning and upholstering a seat?
How to Answer
- 1
Identify the seat frame and remove any old upholstery carefully.
- 2
Cut and shape the foam padding to fit the seat dimensions.
- 3
Attach the foam to the seat frame using adhesive or staples.
- 4
Lay the fabric over the foam, ensuring it's taut and even.
- 5
Secure the fabric with staples or tacks, ensuring clean edges and corners.
Example Answers
First, I would remove any existing upholstery from the seat frame to assess the condition of the structure. Next, I would cut and attach foam padding to the seat, making sure it fits snugly. After that, I would lay the upholstery fabric over the padding and secure it tightly using staples to ensure a clean finish.
How do you incorporate ergonomic principles into seat design?
How to Answer
- 1
Understand the human anatomy and how it interacts with seating.
- 2
Collect data on user preferences and discomfort areas using surveys.
- 3
Incorporate adjustable features for different body types.
- 4
Use materials that support correct posture and reduce pressure points.
- 5
Conduct testing with real users to get feedback on comfort and usability.
Example Answers
I incorporate ergonomic principles by studying human anatomy, ensuring the seat supports the lumbar region while allowing for adjustability to fit various body types. User feedback is also crucial, so I often conduct surveys to gather insights on discomfort areas.
What experience do you have with CAD software in designing seat components?
How to Answer
- 1
Highlight specific CAD software you are proficient in.
- 2
Mention relevant projects where you designed seat components.
- 3
Discuss your design process briefly, focusing on key techniques.
- 4
Include any collaborations with other engineers or stakeholders.
- 5
Emphasize any problem-solving instances during your design work.
Example Answers
I have extensive experience using AutoCAD and SolidWorks to design seat components. In my previous role at ABC Corp, I designed automotive seat frames, collaborating with a team to ensure ergonomic standards were met. I focused on optimizing material usage, resulting in a 15% weight reduction.
Situational Interview Questions
If a batch of seats fails a quality inspection, what steps would you take to address the issue?
How to Answer
- 1
Identify the specific failures that caused the inspection to fail
- 2
Engage the quality control team to gather detailed reports
- 3
Communicate with production to trace the source of the issue
- 4
Implement corrective actions to rectify the problems identified
- 5
Monitor the next batch closely to ensure quality standards are met
Example Answers
First, I would review the inspection report to understand the specific defects. Then, I would meet with the quality control team to discuss the findings and pinpoint potential causes. After that, I would work with the production staff to trace where in the process the issues may have originated. Based on these insights, I would suggest corrective actions, such as adjusting the manufacturing process or retraining staff. Finally, I would oversee the inspection of the next batch to ensure improvements are in place.
How would you handle a situation where a project deadline is moved up unexpectedly?
How to Answer
- 1
Assess the current progress and identify key tasks that are critical for deadline adherence.
- 2
Communicate with the team to gather input and encourage collaboration on task prioritization.
- 3
Be transparent with stakeholders about the new timeline and any potential impacts on quality or scope.
- 4
Adjust the plan by reallocating resources and possibly delegating tasks to ensure focus on critical areas.
- 5
Stay flexible and be prepared to make quick decisions based on the team's capabilities and workload.
Example Answers
I would first assess our current progress to identify the critical tasks that must be completed. Then, I'd hold a quick meeting with the team to discuss how we can prioritize these tasks. I'll communicate with stakeholders about the new deadline and set clear expectations about what can be achieved realistically.
Don't Just Read Seat Maker Questions - Practice Answering Them!
Reading helps, but actual practice is what gets you hired. Our AI feedback system helps you improve your Seat Maker interview answers in real-time.
Personalized feedback
Unlimited practice
Used by hundreds of successful candidates
Imagine a customer complained about the comfort of a seat. How would you address their concerns?
How to Answer
- 1
Acknowledge the customer's feelings and show empathy.
- 2
Ask specific questions to understand their comfort issues.
- 3
Share any relevant product features that address comfort.
- 4
Offer a solution, such as a replacement or adjustment.
- 5
Follow up to ensure their satisfaction with the resolution.
Example Answers
I would start by thanking the customer for their feedback and ask them to describe what specific issues they experienced with the seat's comfort. Then, I would explain features like adjustable lumbar support and offer to arrange a replacement or a different model if needed.
How would you approach the task of designing a new seat that incorporates innovative materials?
How to Answer
- 1
Research current trends in materials technology for seating.
- 2
Identify user needs and ergonomics to guide material selection.
- 3
Consider sustainability and the environmental impact of materials.
- 4
Prototype with a mix of traditional and innovative materials to assess performance.
- 5
Gather user feedback on comfort and usability after initial designs.
Example Answers
I would start by researching advanced materials like bio-based composites and 3D printed polymers that can enhance durability and comfort. Then, I would analyze ergonomic data to ensure the design meets user needs.
What would you do if you had to complete a project but were short on necessary materials?
How to Answer
- 1
Assess the specific materials that are lacking and their importance to the project.
- 2
Determine if alternatives or substitutes for the missing materials are available.
- 3
Communicate with your team or supervisor about the shortage and seek input.
- 4
Prioritize tasks that can be completed with available resources.
- 5
Consider adjusting the project timeline if materials cannot be procured in time.
Example Answers
If I found myself short on materials, I'd first identify which materials are missing and evaluate how critical they are. Then, I'd look for any feasible substitutes that could work in their place. I'd keep my team informed and seek advice, focusing on tasks that can proceed with what we have.
Describe how you would handle a disagreement between team members about the production process.
How to Answer
- 1
Listen to both team members' perspectives carefully.
- 2
Encourage open communication to identify the root cause of the disagreement.
- 3
Facilitate a meeting for discussion, ensuring everyone feels heard.
- 4
Propose a compromise if possible, or suggest an alternative solution.
- 5
Follow up after the discussion to ensure agreement and cooperation.
Example Answers
I would first listen to both team members and understand their viewpoints. I would then facilitate a discussion where both can express their concerns. If we find common ground, we can agree on a process that incorporates both ideas.
If you noticed a safety risk in the seat manufacturing process, how would you handle it?
How to Answer
- 1
Immediately report the safety risk to your supervisor or safety officer
- 2
Document the risk with details and observations to support your report
- 3
Suggest a temporary halt in production if the risk is imminent
- 4
Follow up to ensure the risk is addressed and corrective actions are taken
- 5
Promote a culture of safety by encouraging colleagues to report risks
Example Answers
If I noticed a safety risk in the manufacturing process, I would first report it to my supervisor immediately. I would document what I observed and any relevant details that highlight the danger. If the situation was critical, I'd suggest stopping production temporarily until we could ensure everyone’s safety.
How would you approach the task of reducing production costs without compromising quality?
How to Answer
- 1
Analyze current production processes for inefficiencies
- 2
Investigate alternative, cost-effective materials
- 3
Engage team members for insights and suggestions
- 4
Implement technology for automation where feasible
- 5
Monitor quality metrics closely during any changes
Example Answers
I would start by analyzing our current production processes to identify any inefficiencies. Then, I would explore alternative materials that maintain quality but are less expensive. I believe involving the team can also bring forward valuable suggestions.
If tasked with training a new employee on the production line, how would you ensure they are adequately prepared?
How to Answer
- 1
Start with an overview of the production process to give context.
- 2
Demonstrate each step hands-on before having them try it.
- 3
Provide clear, simple instructions and visual aids if possible.
- 4
Encourage questions throughout the training to clarify doubts.
- 5
Conduct follow-up assessments to gauge their understanding and skills.
Example Answers
I would first explain the entire production process to give them context. Then, I’d demonstrate each step while they observe, followed by having them practice under supervision.
Given the task to improve efficiency in the production line, what steps would you take?
How to Answer
- 1
Analyze current production processes to identify bottlenecks
- 2
Implement lean manufacturing principles to reduce waste
- 3
Incorporate automation where appropriate to speed up tasks
- 4
Train staff on best practices for efficiency
- 5
Regularly review and adjust processes based on feedback and performance data
Example Answers
I would first analyze the production line to pinpoint any bottlenecks causing delays. Then, I'd apply lean principles to streamline processes and minimize waste. By integrating automation in key areas, we could speed up the workflow, and I would ensure my team is trained on efficiency tips to optimize their performance.
Don't Just Read Seat Maker Questions - Practice Answering Them!
Reading helps, but actual practice is what gets you hired. Our AI feedback system helps you improve your Seat Maker interview answers in real-time.
Personalized feedback
Unlimited practice
Used by hundreds of successful candidates
How would you manage the transition to a new piece of machinery in the production process?
How to Answer
- 1
Evaluate the training needs of the team for the new machinery
- 2
Create a detailed transition plan with timelines and responsibilities
- 3
Conduct trials with the new machinery to identify any issues early
- 4
Implement a feedback loop for operators during the transition
- 5
Monitor production closely to measure impacts on efficiency
Example Answers
I would start by assessing the team's training needs and ensure everyone gets proper instruction on the new machinery. Then, I would draft a transition plan that includes a timeline and assign responsibilities to team members. I would run a few trial runs to pinpoint any potential issues before full implementation. Throughout the process, I would encourage feedback from operators to make necessary adjustments. Finally, I would closely monitor the production metrics to evaluate how the new machinery affects overall efficiency.
How would you implement more sustainable practices in the seat manufacturing process?
How to Answer
- 1
Conduct a materials audit to identify eco-friendly alternatives
- 2
Implement recycling programs for waste materials
- 3
Encourage energy-efficient machinery and processes
- 4
Train staff on sustainability practices
- 5
Establish partnerships with sustainable suppliers
Example Answers
I would start by conducting a materials audit to find eco-friendly alternatives and implement a recycling program for any waste materials generated in the process.
Seat Maker Position Details
Recommended Job Boards
CareerBuilder
www.careerbuilder.com/jobs/automotive-seat-makerZipRecruiter
www.ziprecruiter.com/Jobs/Automotive-Seat-MakerThese job boards are ranked by relevance for this position.
Related Positions
- Chair Maker
- Desk Maker
- Bed Maker
- Body Maker
- Car Builder
- Sign Maker
- Camera Maker
- Table Maker
- Cushion Maker
- Fly Maker
Similar positions you might be interested in.
Ace Your Next Interview!
Practice with AI feedback & get hired faster
Personalized feedback
Used by hundreds of successful candidates
Ace Your Next Interview!
Practice with AI feedback & get hired faster
Personalized feedback
Used by hundreds of successful candidates