Top 32 Panel Maker Interview Questions and Answers [Updated 2025]
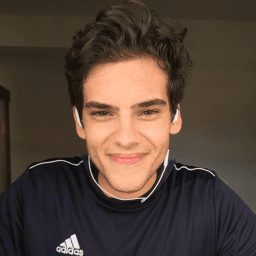
Andre Mendes
•
March 30, 2025
Embarking on a career as a Panel Maker? Our latest blog post is your ultimate guide to acing the interview. Dive into the most common interview questions for the Panel Maker role, complete with example answers and insightful tips to help you respond with confidence and finesse. Whether you're a seasoned professional or a newcomer, this comprehensive resource will equip you to impress your future employers.
Download Panel Maker Interview Questions in PDF
To make your preparation even more convenient, we've compiled all these top Panel Makerinterview questions and answers into a handy PDF.
Click the button below to download the PDF and have easy access to these essential questions anytime, anywhere:
List of Panel Maker Interview Questions
Behavioral Interview Questions
Can you describe a time when you had to collaborate with a team to complete a panel-making project?
How to Answer
- 1
Use the STAR method: Situation, Task, Action, Result.
- 2
Briefly describe the project context and team members involved.
- 3
Highlight your specific role and contributions.
- 4
Emphasize teamwork, communication, and problem-solving skills.
- 5
Conclude with the successful outcome and what you learned.
Example Answers
In a recent project, our team had to create a custom panel for a client. I was responsible for coordinating with the design and fabrication teams. We held weekly meetings to discuss progress and challenges. Together, we met our deadline, and the client praised the final product, enhancing our portfolio.
Tell me about a challenging panel design issue you faced and how you resolved it.
How to Answer
- 1
Clearly define the panel design issue without jargon
- 2
Explain the impact of the issue on the project or team
- 3
Describe the specific steps you took to resolve it
- 4
Highlight the outcome and what you learned from the experience
- 5
Relate it back to how it improves your design approach now
Example Answers
I faced a challenge with a panel that had inconsistent dimensions affecting assembly. I analyzed the design specs, identified the root cause, and recalibrated our tooling. The result was a 20% reduction in assembly time and improved accuracy. I learned the importance of rigorous testing in the early design phase.
Don't Just Read Panel Maker Questions - Practice Answering Them!
Reading helps, but actual practice is what gets you hired. Our AI feedback system helps you improve your Panel Maker interview answers in real-time.
Personalized feedback
Unlimited practice
Used by hundreds of successful candidates
Give an example of how you prioritized tasks during a busy production period.
How to Answer
- 1
Identify key tasks that impact production goals.
- 2
Assess urgency and importance of each task.
- 3
Communicate with the team to understand their workloads.
- 4
Use a task management tool or list to visualize priorities.
- 5
Remain flexible and adjust priorities as needed.
Example Answers
During a busy period last quarter, I focused on the high-priority task of quality checks first because defects could cause delays. I communicated with my team to delegate less critical tasks effectively and ensured we stayed on schedule.
Describe a situation where you had to learn a new technique or tool quickly. How did you handle it?
How to Answer
- 1
Choose a specific technique or tool you learned.
- 2
Explain the context and why it was necessary to learn quickly.
- 3
Describe the steps you took to learn it, highlighting any resources used.
- 4
Mention the outcome and how it benefited your work or team.
- 5
Reflect on what you learned from the experience.
Example Answers
At my previous job, we adopted a new project management software with tight deadlines. I dedicated my evenings to tutorials and sought help from colleagues who were experienced. Within a week, I was able to train my team on its functionalities, improving our project tracking by 30%. This experience taught me the importance of proactive learning.
Have you ever disagreed with a colleague about a design choice? How did you handle it?
How to Answer
- 1
Focus on a specific example that shows your conflict resolution skills
- 2
Describe the design choice and why you disagreed
- 3
Explain your approach to discussing the disagreement respectfully
- 4
Highlight how you reached a compromise or solution
- 5
Mention what you learned from the experience
Example Answers
In a recent project, I disagreed with a colleague about the layout of a panel. I felt it would be more user-friendly with a different arrangement. I scheduled a meeting to discuss our perspectives calmly, and we reviewed user feedback together. Ultimately, we combined our ideas, which improved the design significantly, and I learned the value of collaboration.
Describe a time when you identified a flaw in a panel. What steps did you take to address it?
How to Answer
- 1
Start with a brief description of the panel and the flaw you noticed.
- 2
Explain the immediate impact of the flaw on production or safety.
- 3
Detail the steps you took to investigate and confirm the flaw.
- 4
Describe how you communicated the issue to your team or supervisors.
- 5
Share the outcome after the flaw was addressed, including any improvements made.
Example Answers
In my previous role, I noticed a misalignment in the circuit connections of a panel. This could cause short circuits. I double-checked the wiring against the schematics and confirmed the issue. I immediately reported it to my supervisor and we halted production to prevent any further issues. After rectifying the connections, we also revamped our quality check process to catch similar issues earlier.
Describe an experience where you had to communicate technical information to a non-technical customer.
How to Answer
- 1
Identify the technical concept clearly before the conversation.
- 2
Use simple language and avoid jargon to explain the concept.
- 3
Utilize analogies or examples the customer can relate to.
- 4
Check for understanding by asking questions or seeking feedback.
- 5
Be patient and encourage questions to ensure clarity.
Example Answers
In my previous role, a customer needed help understanding how our software integrated with their existing systems. I simplified the explanation, focusing on how it would improve their workflow, and compared it to a familiar process they already used. After explaining, I asked if they had any questions and clarified key points until they felt comfortable.
Have you ever mentored a junior colleague? What was your approach to sharing knowledge in panel making?
How to Answer
- 1
Share specific instances of mentoring a junior colleague.
- 2
Highlight the techniques used to explain complex concepts in panel making.
- 3
Discuss the importance of hands-on practice and feedback.
- 4
Emphasize building a supportive learning environment.
- 5
Mention any tools or resources that were helpful during mentoring.
Example Answers
Yes, I mentored a junior colleague last year. I focused on hands-on training with panel assembly techniques and provided regular feedback on their progress. I encouraged them to ask questions and used visual aids to explain complex concepts.
Don't Just Read Panel Maker Questions - Practice Answering Them!
Reading helps, but actual practice is what gets you hired. Our AI feedback system helps you improve your Panel Maker interview answers in real-time.
Personalized feedback
Unlimited practice
Used by hundreds of successful candidates
Describe a time when you took initiative to improve a panel-making process in your workplace.
How to Answer
- 1
Identify a specific problem in the panel-making process.
- 2
Explain the solution you proposed or implemented.
- 3
Highlight the benefits that resulted from your initiative.
- 4
Use metrics or qualitative outcomes to showcase success.
- 5
Keep your answer structured: Situation, Task, Action, Result.
Example Answers
In my previous role, we noticed that the curing time for panels was causing delays. I analyzed the process and recommended using a new heating method that reduced curing time by 30%. This change improved our production speed and increased output without compromising quality.
Technical Interview Questions
What types of materials do you have experience with in panel making, and how do you choose the right ones for a project?
How to Answer
- 1
Identify common materials used in panel making like MDF, plywood, or metal.
- 2
Discuss the properties of each material and their suitability for different applications.
- 3
Mention any specific projects where you selected materials based on project requirements.
- 4
Consider factors such as durability, cost, aesthetic appeal, and client preferences.
- 5
Explain how you stay updated on new materials or techniques in panel making.
Example Answers
I have experience with MDF, plywood, and metal. For a recent project, I chose MDF for its smooth finish and ease of use, ensuring it met the client's design requirements while remaining cost-effective.
What machinery and tools are you proficient in using for panel fabrication?
How to Answer
- 1
List specific machinery relevant to panel fabrication like CNC machines or laser cutters
- 2
Mention any hand tools you are skilled in such as saws, drills, or sanding tools
- 3
Include any software used for design and layout of panels
- 4
Highlight your experience level with each piece of equipment
- 5
Be prepared to discuss safety measures and quality control practices
Example Answers
I am proficient in using CNC routers and laser cutters for precision panel fabrication. Additionally, I frequently use hand tools like circular saws and drills. I've also worked with CAD software for panel design, ensuring accuracy and efficiency.
Don't Just Read Panel Maker Questions - Practice Answering Them!
Reading helps, but actual practice is what gets you hired. Our AI feedback system helps you improve your Panel Maker interview answers in real-time.
Personalized feedback
Unlimited practice
Used by hundreds of successful candidates
How do you interpret technical drawings and specifications for panel assembly?
How to Answer
- 1
Familiarize yourself with standard symbols and terminology used in technical drawings.
- 2
Break down the drawing into key components, like dimensions and material specifications.
- 3
Cross-reference the specifications with the drawings to ensure accuracy.
- 4
Look for assembly instructions or notes that indicate special considerations.
- 5
Practice interpreting different types of technical drawings relevant to panel assembly.
Example Answers
I start by identifying the standard symbols and terms in the drawings, then I break down the components, checking dimensions and materials as I go. I always cross-reference with specifications to avoid mistakes.
What industry standards do you follow when manufacturing panels?
How to Answer
- 1
Identify relevant industry standards like ISO, ASTM, or EN.
- 2
Explain how these standards ensure quality and safety.
- 3
Mention specific standards applicable to the type of panels you manufacture.
- 4
Discuss any compliance certifications your facility holds.
- 5
Highlight the importance of staying updated with changing standards.
Example Answers
I follow ISO 9001 standards to ensure consistent quality in my panel manufacturing. This involves regular audits and adherence to quality management principles.
What safety protocols do you implement while working in a panel-making environment?
How to Answer
- 1
Always wear appropriate personal protective equipment such as gloves and goggles.
- 2
Conduct a risk assessment before starting any task to identify potential hazards.
- 3
Ensure all tools and machinery are well-maintained and checked before use.
- 4
Keep the workspace organized to prevent accidents and enable quick access to emergency equipment.
- 5
Follow lockout/tagout procedures when servicing equipment to avoid accidental energization.
Example Answers
I prioritize safety by always wearing gloves and goggles while working. I conduct risk assessments before each task and ensure that all tools are in good condition.
Describe your process for testing the integrity and durability of completed panels.
How to Answer
- 1
Start with visual inspection for defects and ensure quality standards are met
- 2
Conduct stress tests simulating real-world conditions to evaluate performance
- 3
Use tools for measuring dimensional accuracy and material strength
- 4
Document results and compare against benchmarks for accountability
- 5
Implement feedback loops to improve future panel designs based on test outcomes
Example Answers
I begin with a thorough visual inspection to identify any surface defects. Then, I carry out stress tests that mimic the conditions the panels will face in use. I also use measuring tools to check for precision and strength, ensuring they meet industry standards. Finally, I log all results for future reference and continuous improvement.
What CAD software or other computer programs do you use for panel design and manufacturing?
How to Answer
- 1
List specific software you are familiar with, like AutoCAD or SolidWorks.
- 2
Include any industry-specific tools relevant to panel making.
- 3
Mention any experience with simulations or analyses you used in design.
- 4
Be prepared to discuss any collaborative software for team projects.
- 5
Express willingness to learn new software if required.
Example Answers
I primarily use SolidWorks for panel design, complemented by AutoCAD for 2D drafting. I also have experience with manufacturing software like Mastercam for CNC machining.
What fabrication techniques are you most experienced with, and how do they apply to panel making?
How to Answer
- 1
Identify specific techniques you've used, like laser cutting or CNC machining.
- 2
Explain how each technique improves the panel making process, such as precision or efficiency.
- 3
Mention any relevant materials you've worked with, like metal, wood, or composites.
- 4
Share examples of past projects where these techniques were applied successfully.
- 5
Highlight how your expertise can benefit the company's production goals.
Example Answers
I have extensive experience with CNC machining and laser cutting, which enhance the precision of panel design. For instance, I used CNC machining to create custom panels for a furniture project, resulting in a 20% reduction in material waste due to accurate cutting. I also work with various materials including plywood and acrylic, ensuring that I choose the best for each application.
How do you estimate the costs involved in producing panels? What factors do you consider?
How to Answer
- 1
Identify the materials needed for panel production and their costs.
- 2
Consider labor costs including skilled and unskilled workers involved in the process.
- 3
Account for overhead expenses like utilities, rent, and equipment maintenance.
- 4
Factor in waste and potential errors during production to anticipate additional costs.
- 5
Review market trends and competitor pricing to set a competitive cost structure.
Example Answers
I estimate the costs by first calculating the material costs, such as wood and adhesives, and then adding labor costs for both assembly and finishing. I also include overhead costs like electricity and rent, while considering waste percentages.
What assembly techniques do you find most effective in ensuring panel durability?
How to Answer
- 1
Prioritize using high-quality materials that can withstand environmental stresses.
- 2
Implement proper joint design to distribute loads evenly across the panel.
- 3
Incorporate adhesive bonding along with mechanical fasteners for added strength.
- 4
Adopt a thorough quality control process to identify flaws early.
- 5
Continuously test and evaluate panel performance under various conditions.
Example Answers
I find using high-quality materials paired with well-designed joints crucial for durability. This prevents points of failure during stress.
Don't Just Read Panel Maker Questions - Practice Answering Them!
Reading helps, but actual practice is what gets you hired. Our AI feedback system helps you improve your Panel Maker interview answers in real-time.
Personalized feedback
Unlimited practice
Used by hundreds of successful candidates
Situational Interview Questions
If you were given a last-minute design change on a panel you were already working on, how would you approach it?
How to Answer
- 1
Stay calm and assess the impact of the change on the current design.
- 2
Communicate with your team or stakeholders to understand the reasons behind the change.
- 3
Prioritize tasks based on the new requirements and deadlines.
- 4
Re-evaluate your design and make necessary adjustments efficiently.
- 5
Document any changes made for future reference and clarity.
Example Answers
I would first take a moment to understand how the change will affect my current design. After that, I would discuss it with my team to clarify any questions. Then, I would prioritize the affected tasks and adjust my design accordingly, ensuring all changes are documented.
Imagine you're behind schedule on a panel production order. What steps would you take to meet the deadline?
How to Answer
- 1
Assess the current status of the production order and identify bottlenecks
- 2
Communicate with the team to understand challenges and gather input
- 3
Prioritize tasks and reallocate resources as needed to expedite processes
- 4
Consider overtime or additional shifts to increase output if necessary
- 5
Keep stakeholders informed about the situation and progress
Example Answers
I would first evaluate the production timeline to pinpoint where delays are happening. Once I know the bottlenecks, I would discuss with the team to see how we can adjust tasks and reallocate resources effectively. If needed, I’d explore options for overtime to ensure we meet the deadline.
Don't Just Read Panel Maker Questions - Practice Answering Them!
Reading helps, but actual practice is what gets you hired. Our AI feedback system helps you improve your Panel Maker interview answers in real-time.
Personalized feedback
Unlimited practice
Used by hundreds of successful candidates
How would you respond if a client expressed dissatisfaction with a delivered panel?
How to Answer
- 1
Listen carefully to the client's concerns without interrupting.
- 2
Acknowledge their feelings and show empathy for their situation.
- 3
Ask clarifying questions to understand the specifics of their dissatisfaction.
- 4
Offer solutions or alternatives to address their concerns.
- 5
Follow up after the resolution to ensure their satisfaction.
Example Answers
I would start by listening to the client's concerns without interrupting, then acknowledge their feelings. I would ask questions to clarify what specifically they are dissatisfied with and propose a solution, such as revisions or replacements if needed.
If you had the opportunity to suggest an innovative technique in panel making, what would it be and why?
How to Answer
- 1
Research current trends in panel making to identify gaps or opportunities.
- 2
Focus on sustainability and efficiency in your suggestion.
- 3
Consider technology integration, like automation or smart materials.
- 4
Highlight how your technique enhances quality or reduces costs.
- 5
Be prepared to explain the practical implementation of your idea.
Example Answers
I would suggest integrating 3D printing technology into panel making. This method allows for complex designs that conventional methods can't achieve, reduces waste, and can speed up production times significantly.
How would you handle a situation where resources were limited for a project that needed immediate attention?
How to Answer
- 1
Identify essential tasks and prioritize them based on impact.
- 2
Communicate openly with your team and stakeholders about resource constraints.
- 3
Look for ways to optimize current resources instead of requesting more.
- 4
Consider reallocating resources from less critical projects temporarily.
- 5
Be flexible and adapt your plan based on the resources available.
Example Answers
I would prioritize the critical tasks that directly impact the project's success and communicate with my team about what's feasible with our limited resources. This way, we can focus on high-impact activities.
If two team members are not working well together, what would you do to improve their collaboration?
How to Answer
- 1
Observe the interactions between team members to identify specific issues.
- 2
Facilitate a private conversation between them to express their concerns openly.
- 3
Encourage them to find common goals that align with the team's objectives.
- 4
Suggest team-building activities to improve trust and understanding.
- 5
Follow up regularly to monitor progress and adjust strategies as needed.
Example Answers
I would start by observing their interactions to pinpoint the problem areas. Then, I'd arrange a meeting for them to discuss their concerns directly. By encouraging a shared focus on team goals, we can enhance their collaboration.
How would you measure the success of a panel-making project? What metrics would you use?
How to Answer
- 1
Identify key objectives of the project such as quality, cost, and timeliness
- 2
Select quantitative metrics like production time, defect rates, and customer satisfaction scores
- 3
Incorporate qualitative feedback from team members and stakeholders
- 4
Set benchmarks for comparison against previous projects or industry standards
- 5
Regularly review metrics during and after project completion to assess success
Example Answers
I would measure success by tracking production time and ensuring it meets our timeline targets. Additionally, I would monitor defect rates to keep quality high, aiming for less than a 2% error rate.
What would you do if a batch of panels failed quality inspection just before shipping?
How to Answer
- 1
Identify the specific reasons for the failure immediately
- 2
Communicate with the quality control team and relevant stakeholders
- 3
Assess the possibility of reworking the panels if feasible
- 4
Implement corrective measures to prevent future failures
- 5
Prepare a plan to manage customer expectations regarding shipping delays
Example Answers
I would first investigate the failure reasons with the quality control team. Then, I'd communicate with management and customer service to explain the situation. If possible, I would try to rework the panels to meet the standards. Finally, I would put measures in place to ensure this doesn't happen again and inform customers about any shipping delays.
In a team panel fabrication project, how would you assign tasks to ensure efficiency and quality?
How to Answer
- 1
Assess team members' strengths and weaknesses for task allocation
- 2
Break down the project into clear, manageable tasks
- 3
Set specific deadlines and quality standards for each task
- 4
Encourage communication among team members for updates and feedback
- 5
Review progress regularly and adjust assignments as needed
Example Answers
I would first analyze each team member's skills to assign tasks that match their strengths, ensuring efficiency. Then, I would divide the project into specific tasks with clear deadlines and quality expectations. This allows team members to focus and deliver their best work while promoting regular communication to address any issues promptly.
If assigned multiple panel projects at once, how would you manage your time and resources?
How to Answer
- 1
Prioritize projects based on deadlines and complexity
- 2
Allocate specific time blocks for each project in your schedule
- 3
Communicate with stakeholders to set realistic expectations
- 4
Use project management tools to track progress and share updates
- 5
Regularly assess and adjust your workload as needed
Example Answers
I would start by prioritizing the projects based on their deadlines and the resources required. Then, I'd allocate specific time blocks in my calendar for each project, ensuring I stay focused and accountable. Regular check-ins with the team would help manage expectations and keep everyone aligned.
Don't Just Read Panel Maker Questions - Practice Answering Them!
Reading helps, but actual practice is what gets you hired. Our AI feedback system helps you improve your Panel Maker interview answers in real-time.
Personalized feedback
Unlimited practice
Used by hundreds of successful candidates
How would you handle a scenario where the project scope for panel production changes significantly midway through?
How to Answer
- 1
Assess the impact of the scope change on current resources and timelines
- 2
Communicate promptly with project stakeholders about the changes
- 3
Develop a revised plan that accommodates the new scope
- 4
Ensure alignment with team members on new goals and expectations
- 5
Implement a feedback loop to monitor progress and adapt as needed
Example Answers
If the scope changes, I would first evaluate how it affects our current schedule and resources. Then, I would discuss the changes with my team and stakeholders to ensure everyone is aligned. Together, we would create a new plan and set clear expectations moving forward.
Panel Maker Position Details
Recommended Job Boards
CareerBuilder
www.careerbuilder.com/jobs/panel-makerZipRecruiter
www.ziprecruiter.com/Jobs/Panel-Maker/These job boards are ranked by relevance for this position.
Related Positions
- Pad Maker
- Button Maker
- Frame Maker
- Desk Maker
- Table Maker
- Window Maker
- Plug Maker
- Frame Builder
- Pot Builder
- Mat Maker
Similar positions you might be interested in.
Ace Your Next Interview!
Practice with AI feedback & get hired faster
Personalized feedback
Used by hundreds of successful candidates
Ace Your Next Interview!
Practice with AI feedback & get hired faster
Personalized feedback
Used by hundreds of successful candidates