Top 29 Plug Maker Interview Questions and Answers [Updated 2025]
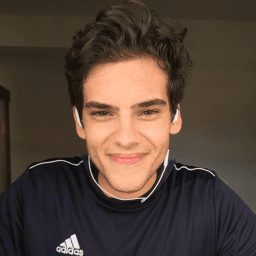
Andre Mendes
•
March 30, 2025
Are you preparing for a Plug Maker job interview and unsure of what to expect? Our latest blog post has you covered with a curated list of the most common interview questions for this role. Dive into example answers and practical tips on crafting effective responses to stand out as a top candidate. Equip yourself with the insights needed to navigate your interview with confidence and success.
Download Plug Maker Interview Questions in PDF
To make your preparation even more convenient, we've compiled all these top Plug Makerinterview questions and answers into a handy PDF.
Click the button below to download the PDF and have easy access to these essential questions anytime, anywhere:
List of Plug Maker Interview Questions
Behavioral Interview Questions
Can you give an example of a time when you collaborated with a team to solve a production issue? How did you contribute?
How to Answer
- 1
Select a specific incident that highlights teamwork and problem-solving.
- 2
Explain the production issue clearly and its impact.
- 3
Describe your role in the collaboration and specific actions you took.
- 4
Mention any tools or methods used to facilitate communication.
- 5
Conclude with the outcome or resolution of the issue.
Example Answers
In my previous role, we faced a bottleneck in the production line that was delaying output. I organized a meeting with team members from production and quality assurance. I led the brainstorming session, where we identified that a specific machine was malfunctioning. I coordinated with maintenance to prioritize its repair, which resolved the issue within a few hours and improved our output by 20%.
Describe a situation where you identified a potential defect in a plug component and what steps you took to address it.
How to Answer
- 1
Start with a brief overview of the situation and the defect you noticed.
- 2
Explain how you verified that this was indeed a defect.
- 3
Describe the actions you took to alert your team or supervisor.
- 4
Mention any steps you took to remedy the defect or prevent future occurrences.
- 5
Conclude with the positive outcome or what you learned from the experience.
Example Answers
In my previous role, I noticed that a batch of plug components had inconsistencies in their insulation thickness. I measured several samples to confirm the issue and reported it to my supervisor immediately. We isolated the affected batch and implemented additional quality checks on the production line. This led to better monitoring and significantly reduced defects in subsequent batches.
Don't Just Read Plug Maker Questions - Practice Answering Them!
Reading helps, but actual practice is what gets you hired. Our AI feedback system helps you improve your Plug Maker interview answers in real-time.
Personalized feedback
Unlimited practice
Used by hundreds of successful candidates
Tell us about a time you had to ensure the high quality of a batch of plugs. What process did you follow?
How to Answer
- 1
Start with a specific instance that highlights your quality assurance skills
- 2
Describe the steps you took to monitor quality during production
- 3
Mention any tools or techniques you employed for quality control
- 4
Explain the outcome and the impact of your actions on the final product
- 5
Conclude with what you learned from the experience and how it improved your process
Example Answers
In a previous role, we had a batch of plugs that were failing quality tests. I immediately implemented a stricter inspection process by adding a quality checkpoint after every 100 plugs. I used precision gauges to measure dimensions accurately. As a result, the batch was completed with zero defects, and we met our delivery deadline. This taught me the importance of proactive quality checks.
Have you ever had a disagreement with a coworker over a production method? How did you resolve it?
How to Answer
- 1
Stay calm and focus on facts instead of emotions.
- 2
Listen to the coworker's perspective before responding.
- 3
Suggest a collaborative approach to find common ground.
- 4
Provide a specific example to illustrate your point.
- 5
Follow up to ensure the solution was effective.
Example Answers
I had a disagreement with a coworker about using different materials for our plugs. I listened to their reasoning and understood their point about cost-efficiency. We decided to run a few tests on both materials and compare the results, which helped us choose the best option based on performance.
Describe an instance where you had to take the lead on a project or initiative in plug making.
How to Answer
- 1
Choose a specific project you led in plug making.
- 2
Explain your role and responsibilities clearly.
- 3
Highlight challenges you faced and how you overcame them.
- 4
Discuss the outcome and any metrics or results.
- 5
Reflect on what you learned from the experience.
Example Answers
In my last role, I led a project to innovate a new plug design for waterproof applications. I coordinated a team of four, set deadlines, and conducted testing. We faced issues with material durability but resolved them by experimenting with alternatives. The final design improved customer satisfaction by 30%. I learned the importance of collaboration in solving project challenges.
Technical Interview Questions
What are the common materials used in plug manufacturing, and how do their properties affect the final product?
How to Answer
- 1
Identify key materials such as rubber, silicone, and plastic.
- 2
Explain how each material's elasticity, durability, and temperature resistance impacts the plug's performance.
- 3
Mention specific applications of each material in plug types.
- 4
Highlight the trade-offs between materials for different plug uses.
- 5
Keep your explanation focused and technical, demonstrating industry knowledge.
Example Answers
Common materials in plug manufacturing include rubber, silicone, and plastic. Rubber offers excellent elasticity and durability, making it ideal for plugs that must withstand significant wear. Silicone is temperature resistant and flexible, suitable for applications where heat is a concern. Plastic, often less expensive, is lightweight but may not withstand high temperatures as well.
Explain the key steps involved in the plug making process.
How to Answer
- 1
Begin by outlining the materials needed for plug making
- 2
Describe the mold preparation steps
- 3
Explain the mixing and pouring of materials into the mold
- 4
Mention the curing process and time required
- 5
Conclude with finishing touches and quality check.
Example Answers
The plug making process starts with selecting materials like resin and a suitable mold. Next, the mold is prepared by cleaning and applying a release agent. After that, the resin is mixed according to specifications and poured into the mold. Once the mixture cures for the designated time, the mold is removed and any rough edges are smoothed out to finish the plug.
Don't Just Read Plug Maker Questions - Practice Answering Them!
Reading helps, but actual practice is what gets you hired. Our AI feedback system helps you improve your Plug Maker interview answers in real-time.
Personalized feedback
Unlimited practice
Used by hundreds of successful candidates
What types of machinery have you used in the past for plug making, and what safety measures do you follow while operating them?
How to Answer
- 1
List specific machinery relevant to plug making, like CNC machines or molding equipment.
- 2
Mention your hands-on experience with each type of machinery.
- 3
Describe key safety measures you implement, such as wearing proper gear and ensuring machine guards are in place.
- 4
Highlight any training you have received regarding safety protocols.
- 5
Show your commitment to maintaining a safe work environment.
Example Answers
I have operated CNC machines and injection molding machines for plug production. For safety, I always wear safety goggles and ear protection, and I ensure that all safety guards are in place before starting the machines.
How would you troubleshoot an issue where a machine is not producing plugs to the correct specifications?
How to Answer
- 1
Check the machine settings to ensure they are correct.
- 2
Inspect the raw materials for any inconsistencies or defects.
- 3
Examine the machine for wear and tear or mechanical failures.
- 4
Review the production process for any deviations from standard operating procedures.
- 5
Conduct test runs to identify at which point the issue occurs.
Example Answers
First, I would verify that the machine settings are aligned with the specifications. Then, I would inspect the raw materials to make sure they meet quality standards. If everything appears correct, I'd check for machine wear and run a test sample to pinpoint where the issue arises.
How do you read and interpret technical blueprints or schematics related to plug design?
How to Answer
- 1
Familiarize yourself with common symbols used in technical schematics.
- 2
Practice reading various blueprints to improve pattern recognition.
- 3
Break down complex designs into simpler sections to understand each part.
- 4
Always refer to the accompanying documentation for specifications.
- 5
Ask clarifying questions if something in the blueprint is not clear.
Example Answers
I carefully study the common symbols and conventions used in wiring diagrams and plug designs. By breaking down the blueprint into sections, I can understand how each component interacts.
What tools do you use to measure the accuracy and dimensions of plugs you create?
How to Answer
- 1
Mention specific measuring tools like calipers and micrometers
- 2
Include precision measurement techniques you employ
- 3
Discuss how you ensure consistency between different plugs
- 4
Explain the importance of accuracy in your work
- 5
Share any examples of adjustments you've made based on measurements
Example Answers
I primarily use digital calipers and micrometers to measure the dimensions of plugs I create, ensuring accuracy within 0.01 mm. I also check samples against a master plug to maintain consistency.
Describe your experience with repair and maintenance of plug making equipment.
How to Answer
- 1
Start by outlining any relevant formal training or certifications.
- 2
Mention specific types of plug making equipment you have worked with.
- 3
Discuss routine maintenance tasks you performed regularly.
- 4
Provide an example of a repair you successfully completed.
- 5
Highlight any improvements you made to enhance equipment performance.
Example Answers
I completed a certification in equipment maintenance and have experience with various plug press machines. I regularly performed routine checks and lubrications. Once, I repaired a malfunctioning air compressor that was affecting production, which improved our output efficiency.
What safety protocols are most critical in the process of plug manufacturing?
How to Answer
- 1
Identify key safety measures like personal protective equipment (PPE)
- 2
Discuss environmental controls to manage dust and chemicals
- 3
Mention machine safety protocols such as lockout/tagout procedures
- 4
Emphasize the importance of regular safety training for all staff
- 5
Highlight emergency response strategies for accidents or spills
Example Answers
In plug manufacturing, using PPE like gloves and masks is essential to protect against dust and chemicals. Regular safety training ensures that everyone knows how to handle equipment safely and respond to emergencies.
How do you manage production requirements for different batch sizes of plugs?
How to Answer
- 1
Assess the specific demands of each batch size before production.
- 2
Communicate with stakeholders about lead times for varying batch sizes.
- 3
Utilize flexible manufacturing techniques to adapt to different sizes.
- 4
Implement robust inventory management to ensure adequate materials.
- 5
Monitor production metrics and adjust processes based on performance.
Example Answers
I assess the production needs for each batch size by analyzing demand and consult with the team to align on timelines. I use flexible manufacturing techniques to ensure we can easily shift between small and large batches.
What quality assurance techniques do you use to ensure plugs meet industry standards?
How to Answer
- 1
Identify specific quality assurance methods you employ in plug manufacturing.
- 2
Mention any relevant standards or regulations that guide your QA process.
- 3
Discuss the importance of testing and validation in your quality assurance practices.
- 4
Include how you handle feedback and continuous improvement.
- 5
Provide examples of tools or metrics you use to measure quality.
Example Answers
I implement a combination of visual inspections and batch testing to ensure plugs meet industry standards, and I regularly refer to ASTM standards as part of my quality assurance process.
Don't Just Read Plug Maker Questions - Practice Answering Them!
Reading helps, but actual practice is what gets you hired. Our AI feedback system helps you improve your Plug Maker interview answers in real-time.
Personalized feedback
Unlimited practice
Used by hundreds of successful candidates
Situational Interview Questions
You're notified of a machine malfunction during a critical production run. What steps would you take immediately?
How to Answer
- 1
Assess the situation to understand the severity of the malfunction.
- 2
Immediately halt the production line to prevent further issues.
- 3
Notify the maintenance team and provide details of the malfunction.
- 4
Check for any safety hazards to ensure the safety of all personnel.
- 5
Communicate with the production manager about the status and estimated downtime.
Example Answers
First, I would assess the malfunction to gauge its severity. Then, I'd stop the production line to prevent any further complications. After that, I would notify maintenance with the specific details and check for safety hazards in the area. Finally, I would update the production manager on the situation.
Your company is considering launching a new plug design. How would you participate in the research and development phase?
How to Answer
- 1
Assess user needs by conducting surveys and interviews with existing customers.
- 2
Collaborate with engineers to understand technical constraints and possibilities.
- 3
Review current market trends for innovative plug designs and features.
- 4
Participate in brainstorming sessions to generate creative design ideas.
- 5
Prototype and test designs to gather feedback before finalizing the product.
Example Answers
I would start by gathering feedback from users to identify their needs, then work closely with the engineering team to explore what is technically feasible.
Don't Just Read Plug Maker Questions - Practice Answering Them!
Reading helps, but actual practice is what gets you hired. Our AI feedback system helps you improve your Plug Maker interview answers in real-time.
Personalized feedback
Unlimited practice
Used by hundreds of successful candidates
If you were given a tight deadline to produce a new type of plug, how would you ensure it is met without compromising quality?
How to Answer
- 1
Prioritize tasks and identify key features for the plug.
- 2
Use rapid prototyping techniques to develop initial designs quickly.
- 3
Engage team members and delegate responsibilities effectively.
- 4
Establish feedback loops to catch quality issues early.
- 5
Plan for testing and quality assurance in parallel with production.
Example Answers
I would start by identifying the most critical features for the new plug and focus on those. Then, I would use rapid prototyping to create initial designs quickly. By delegating tasks to my team, we can parallelize our efforts. I would also set up a quick feedback system to ensure we catch any quality issues early, and make sure to incorporate testing as we go.
Suppose management wants to reduce production costs. How would you suggest identifying and implementing cost-saving measures?
How to Answer
- 1
Analyze current production processes for inefficiencies
- 2
Consider automating repetitive tasks to save labor costs
- 3
Engage with team members for insights on potential cost savings
- 4
Evaluate supplier contracts for better pricing or alternative materials
- 5
Implement regular cost review meetings to track progress and adjust strategies
Example Answers
I would start by analyzing the production processes to identify any inefficiencies, then explore automation options for tasks that are currently manual. Engaging the team for their insights can also reveal cost-saving opportunities from their experiences.
Imagine you notice an inefficiency in the plug manufacturing process. How would you address this with your team and management?
How to Answer
- 1
Identify the specific inefficiency with data to support your claim.
- 2
Discuss your observations with your team and gather their input.
- 3
Propose a meeting with management to present the issue and potential solutions.
- 4
Offer actionable steps for improvement, detailing how they can be implemented.
- 5
Follow up on the discussion to assess progress and make adjustments as needed.
Example Answers
I've noticed that our plug assembly line has delays due to manual handling. I gathered data on the process times and shared this with my team. We brainstormed ideas and I suggested a meeting with management to propose automating some stages. This could cut down production time by 20%.
How would you approach learning to use a new piece of equipment in the plug making process that your company has just acquired?
How to Answer
- 1
Research the equipment specifications and its operational principles
- 2
Ask for training resources from the company or manufacturer
- 3
Seek advice from experienced colleagues who have used similar equipment
- 4
Start with a hands-on trial to familiarize yourself with the controls
- 5
Document your learning process and any issues encountered for future reference
Example Answers
I would begin by researching the equipment to understand its specifications and functions. Then, I would request any training documents or videos from the company or manufacturer. After that, I would reach out to colleagues who might have experience with similar machines for tips. I would set up time for a practical trial to gain hands-on experience, all while taking notes on my learning process for future improvement.
If a batch of plugs was returned due to quality concerns, how would you handle this and ensure future batches meet standards?
How to Answer
- 1
Acknowledge the issue promptly and take responsibility.
- 2
Investigate the root cause of the quality concerns thoroughly.
- 3
Implement corrective actions based on findings from the investigation.
- 4
Communicate with the team about quality standards and expectations.
- 5
Monitor future batches closely and conduct regular quality checks.
Example Answers
I would first acknowledge the return and take responsibility. Then, I would analyze the batch to identify the quality issues, implement corrective actions, and communicate the findings to the team. Moving forward, I would ensure that we have tighter quality checks in place for future batches.
How would you handle receiving negative feedback about your role in a recent plug production project?
How to Answer
- 1
Acknowledge the feedback without becoming defensive
- 2
Ask for specifics to understand the concerns better
- 3
Reflect on the feedback to identify areas for improvement
- 4
Communicate how you will address the issues raised
- 5
Express appreciation for the feedback, it shows growth opportunities
Example Answers
I appreciate the feedback and I take it seriously. I would ask for specific examples to fully understand the issue and I would reflect on how I can improve in those areas for future projects.
You're tasked with ensuring all plugs comply with a new industry regulation. What would be your first steps?
How to Answer
- 1
Review the details of the new regulation thoroughly
- 2
Identify the specific aspects of the plugs that need compliance adjustments
- 3
Collaborate with engineering and production teams for insights
- 4
Develop a checklist for compliance to streamline the process
- 5
Set up a training session for staff on the new regulations
Example Answers
First, I would review the new regulations to understand what changes are required. Then, I would work with the engineering team to identify which components of our plugs need to be updated to meet these standards. Creating a compliance checklist would help track progress, and I would schedule a training session for the staff to ensure everyone understands the new requirements.
How would you handle coordination with other departments for a new plug production project that affects multiple areas?
How to Answer
- 1
Identify key stakeholders in each department
- 2
Schedule regular meetings to discuss progress and issues
- 3
Use collaborative tools for updates and feedback
- 4
Clarify responsibilities and timelines for each team
- 5
Document decisions and share updates with all parties involved
Example Answers
To handle coordination, I would start by identifying key stakeholders from engineering, marketing, and production. Regular meetings would be scheduled to discuss progress and address any issues. I would use collaborative tools to ensure everyone is up to date, clarify responsibilities for each team, and document all decisions for transparency.
Don't Just Read Plug Maker Questions - Practice Answering Them!
Reading helps, but actual practice is what gets you hired. Our AI feedback system helps you improve your Plug Maker interview answers in real-time.
Personalized feedback
Unlimited practice
Used by hundreds of successful candidates
If a vendor delayed shipment of a crucial plug component, how would you manage the situation to minimize production delays?
How to Answer
- 1
Assess the impact of the delay on production schedules.
- 2
Communicate immediately with the vendor to get an updated timeline.
- 3
Explore alternative vendors or substitute materials if applicable.
- 4
Notify affected team members about the issue and any adjustments.
- 5
Prioritize tasks that can proceed without the delayed component.
Example Answers
First, I would assess how the delay affects our production timeline. Then, I would contact the vendor to understand the reasons for the delay and get a new estimated delivery date. If the new timeline is unacceptable, I would look for alternative suppliers who can provide the component quickly. I would also inform my production team about the issue and make sure we focus on other tasks that can be completed in the meantime.
Imagine noticing a discrepancy in plug inventory levels. How would you address and resolve the issue?
How to Answer
- 1
Verify the accuracy of inventory data through physical counts
- 2
Investigate potential causes of discrepancy, such as errors in recording or data entry
- 3
Communicate findings with the team and involve relevant stakeholders
- 4
Implement corrective actions to rectify the inventory levels
- 5
Establish preventive measures to minimize future discrepancies
Example Answers
First, I would conduct a physical count to confirm the inventory levels against our records. Then, I would investigate whether there were any recent data entry errors or miscommunications. After identifying the cause, I would discuss the findings with my team and take steps to correct the inventory and implement guidelines to prevent similar issues in the future.
If you wanted to improve a technical skill to better perform your duties as a plug maker, how would you approach this?
How to Answer
- 1
Identify a specific technical skill relevant to plug making.
- 2
Research training resources like workshops or online courses.
- 3
Set a timeline for your skill improvement.
- 4
Practice the new skill regularly in real-world scenarios.
- 5
Seek feedback from experienced colleagues.
Example Answers
I would focus on mastering CAD software to improve my design precision. I'd take an online course, practice daily, and apply it to my plug designs while asking colleagues for their input.
During a routine quality inspection, you discover a critical flaw in plugs. How would you address this?
How to Answer
- 1
Immediately report the issue to your supervisor or quality assurance team
- 2
Document the flaw with specifics such as type, location, and potential impact
- 3
Isolate the affected batch to prevent further use or distribution
- 4
Work with the team to analyze the root cause of the flaw
- 5
Propose corrective actions and follow up on implementation
Example Answers
I would report the critical flaw to my supervisor right away. Then, I would document all details about the flaw and isolate the affected plugs to ensure safety. After that, I would collaborate with the team to find out what caused the issue and discuss possible corrective actions.
Plug Maker Position Details
Related Positions
- Pad Maker
- Panel Maker
- Fly Maker
- Pot Builder
- Sign Maker
- Frame Maker
- Button Maker
- Camera Maker
- Table Maker
- Mat Maker
Similar positions you might be interested in.
Ace Your Next Interview!
Practice with AI feedback & get hired faster
Personalized feedback
Used by hundreds of successful candidates
Ace Your Next Interview!
Practice with AI feedback & get hired faster
Personalized feedback
Used by hundreds of successful candidates