Top 30 Plastic Maker Interview Questions and Answers [Updated 2025]
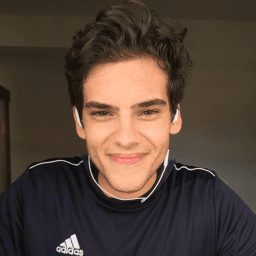
Andre Mendes
•
March 30, 2025
Navigating the competitive landscape of the manufacturing industry requires thorough preparation, especially for specialized roles like a Plastic Maker. In this updated guide, we delve into the most common interview questions aspiring Plastic Makers face, offering insightful example answers and practical tips to help you respond with confidence and clarity. Equip yourself with the knowledge to stand out and secure your desired position in this dynamic field.
Download Plastic Maker Interview Questions in PDF
To make your preparation even more convenient, we've compiled all these top Plastic Makerinterview questions and answers into a handy PDF.
Click the button below to download the PDF and have easy access to these essential questions anytime, anywhere:
List of Plastic Maker Interview Questions
Behavioral Interview Questions
Tell me about a time you successfully worked with a team to complete a plastic manufacturing project. What was your role and how did you contribute to the team?
How to Answer
- 1
Choose a specific project example that highlights teamwork.
- 2
Clearly define your role and responsibilities in the project.
- 3
Explain how you communicated and collaborated with team members.
- 4
Discuss the outcome of the project and any measurable successes.
- 5
Reflect on what you learned from the experience.
Example Answers
In my last job at a plastic manufacturing company, I worked on a project to develop a new plastic part for automotive applications. As the project coordinator, I organized weekly meetings and facilitated communication between the design and production teams. We completed the project on time and reduced costs by 15%, which taught me the importance of clear communication within a team.
Describe a challenging problem you faced when working with plastic production equipment and how you resolved it.
How to Answer
- 1
Identify a specific problem you encountered with the equipment
- 2
Describe the impact of the problem on production or quality
- 3
Explain the steps you took to troubleshoot and resolve the issue
- 4
Highlight any collaboration with team members or experts during the process
- 5
Finish with the positive outcome and what you learned from the experience
Example Answers
In my previous role, our injection molding machine kept jamming, which halted production. I analyzed the process and discovered that a worn-out feed screw was the cause. I coordinated with the maintenance team to replace the screw, which improved our output and reduced downtime significantly. I learned the importance of regular equipment maintenance.
Don't Just Read Plastic Maker Questions - Practice Answering Them!
Reading helps, but actual practice is what gets you hired. Our AI feedback system helps you improve your Plastic Maker interview answers in real-time.
Personalized feedback
Unlimited practice
Used by hundreds of successful candidates
Can you give an example of how you ensured workplace safety while working with hazardous materials or machinery in plastic production?
How to Answer
- 1
Identify specific safety protocols you followed.
- 2
Describe a situation where you noticed potential hazards.
- 3
Explain the actions you took to mitigate risks.
- 4
Mention any training you received related to safety.
- 5
Emphasize the importance of a safe work environment.
Example Answers
In my previous role, we were required to wear personal protective equipment at all times while handling hot plastic materials. One time, I noticed that a colleague was not wearing their gloves. I stopped the operation and reminded them about the safety protocols, ensuring everyone understood the risks involved.
Give an example of a process improvement you proposed in a previous plastic manufacturing job. What was the outcome?
How to Answer
- 1
Identify a specific improvement you suggested
- 2
Explain the problem the improvement addressed
- 3
Describe the steps you took to implement the change
- 4
Quantify the results or benefits achieved if possible
- 5
Use clear and concise examples to illustrate your point
Example Answers
In my previous role, I noticed that our injection molding cycle times were longer than industry standards. I proposed a change in the cooling time and suggested implementing a more efficient cooling system. After implementing this, we reduced our cycle times by 15%, which significantly increased our production output and reduced delays.
Describe a time when you learned a new skill or technology related to plastic manufacturing. How did it benefit your work?
How to Answer
- 1
Select a specific skill or technology you learned that is relevant to plastic manufacturing
- 2
Explain the context in which you learned this skill, such as a project or a challenge
- 3
Describe the steps you took to learn and implement the new skill
- 4
Highlight the positive impact it had on your work, such as efficiency or quality improvements
- 5
Conclude by mentioning any further applications of this skill or how it helped your team
Example Answers
In my previous role, I learned how to operate a new injection molding machine after our old one broke down. I spent a week training with a technician and reading the manual. This allowed us to reduce our production time by 20%, significantly increasing our output and meeting tight deadlines.
Have you led a team in a plastic manufacturing environment before? How did you manage your team to ensure productivity?
How to Answer
- 1
Explain your role and responsibilities in leading the team.
- 2
Discuss specific strategies you used to boost productivity.
- 3
Mention how you ensured team communication and morale.
- 4
Provide examples of challenges faced and how you overcame them.
- 5
Highlight any metrics or results to demonstrate success.
Example Answers
Yes, I led a team of 10 in a plastic manufacturing facility where we focused on injection molding. I implemented daily stand-up meetings to address issues and set goals, which improved our productivity by 20% within 3 months.
How have you resolved conflicts in a work setting where team members disagreed on the best process for plastic production?
How to Answer
- 1
Identify the specific conflict and the parties involved
- 2
Listen actively to each team member's perspective
- 3
Propose a compromise or alternative solution that addresses concerns
- 4
Utilize data or evidence to support your suggestions
- 5
Follow up after the resolution to ensure the solution is effective
Example Answers
In a recent project, two team members disagreed on the best method for molding plastic parts. I facilitated a meeting where everyone shared their viewpoints. After discussing the pros and cons, we agreed to run a small test batch using both methods to gather data that would guide our final decision.
Tell me about a time when you had to adapt to a significant change in technology or processes in the plastic industry. How did you handle it?
How to Answer
- 1
Identify a specific change in technology or processes you faced.
- 2
Describe your initial reaction and any challenges you encountered.
- 3
Explain the steps you took to adapt, such as training or seeking help.
- 4
Highlight the positive results that came from your adaptation.
- 5
Conclude with what you learned from the experience.
Example Answers
At my previous job, we shifted to a new injection molding machine. I was concerned at first because I had limited experience with it. I took the initiative to enroll in a training program and worked closely with the technician who oversaw the new equipment. After a few weeks, I became proficient, which improved our production efficiency by 20%. This experience taught me the value of continuous learning and seeking expertise when facing new technology.
Technical Interview Questions
What are the key differences between thermoplastic and thermosetting plastics, and how do these differences impact their processing?
How to Answer
- 1
Define thermoplastics and thermosetting plastics clearly.
- 2
Highlight the key differences in their molecular structure.
- 3
Explain how these differences affect processing methods.
- 4
Mention common examples of each type of plastic.
- 5
Conclude with an impact statement on applications.
Example Answers
Thermoplastics are polymers that can be melted and reshaped multiple times, while thermosetting plastics solidify permanently. The key difference is that thermoplastics have linear or branched structures, allowing them to be reprocessed, whereas thermosetting plastics have a crosslinked structure, which makes them heat-resistant but unreversible. This affects processing; thermoplastics can be molded using methods like injection molding, while thermosets require curing processes. Common examples include polyethylene as a thermoplastic and epoxy resin as a thermoset. These differences impact their applications, as thermoplastics are used in items needing flexibility and thermosets are used in durable applications like adhesives.
Explain how you would set up an injection molding machine for a new production run. What key parameters must be considered?
How to Answer
- 1
Identify the type of plastic and its specifications.
- 2
Set the temperature settings for the barrel and nozzle based on the material.
- 3
Adjust pressure settings for injection and holding based on part design.
- 4
Configure cycle time, including injection, cooling, and ejection phases.
- 5
Run a test cycle to verify settings and adjust based on initial results.
Example Answers
First, I would select the appropriate plastic material and review its processing parameters. Then, I would set the barrel and nozzle temperatures according to the material's data sheet. Next, I would configure the injection pressure and holding pressure suited for the mold design. After that, I would define the cycle time to ensure efficient production. Finally, I'd conduct a test run and monitor for any adjustments needed.
Don't Just Read Plastic Maker Questions - Practice Answering Them!
Reading helps, but actual practice is what gets you hired. Our AI feedback system helps you improve your Plastic Maker interview answers in real-time.
Personalized feedback
Unlimited practice
Used by hundreds of successful candidates
What techniques do you use to ensure the quality and consistency of plastic products during manufacturing?
How to Answer
- 1
Describe specific quality control methods you use.
- 2
Mention the importance of material selection in achieving quality.
- 3
Explain the role of regular maintenance and calibration in machinery.
- 4
Highlight the use of standardized processes and procedures.
- 5
Discuss the importance of staff training in quality assurance.
Example Answers
I implement strict quality control techniques such as regular sampling and testing, ensuring that every batch meets our specified standards.
Can you explain the polymerization process and how it affects the properties of the plastic produced?
How to Answer
- 1
Define polymerization clearly, mentioning types like addition and condensation.
- 2
Discuss how the molecular weight and structure influence plastic properties.
- 3
Connect polymerization to practical examples like strength and flexibility.
- 4
Use simple terms and avoid jargon to ensure clarity.
- 5
Summarize the relationship between polymerization and final product applications.
Example Answers
Polymerization is the process of linking monomers to form polymers. There are two main types: addition polymerization, where monomers add to form long chains, and condensation polymerization, which releases small molecules like water. This process affects properties like strength and flexibility because longer polymer chains often lead to stronger plastics, like those used in containers.
How would you troubleshoot an extruder that is producing inconsistent results in the plastic characteristics?
How to Answer
- 1
Check the material feed consistency and ensure there are no blockages.
- 2
Monitor the temperature settings along the extruder and adjust as needed.
- 3
Inspect and clean the die to remove any build-up that might affect flow.
- 4
Evaluate the screw speed and design to ensure proper mixing and melting.
- 5
Review the production parameters for any recent changes that could impact results.
Example Answers
I would start by checking the feed material for any inconsistencies or blockages. Next, I’d monitor the temperature zones to ensure they are optimal for the material being used. Lastly, I would inspect the die for cleanliness and ensure the screw settings are appropriate for the desired output.
What types of regulatory or compliance issues must be considered in plastic manufacturing?
How to Answer
- 1
Familiarize with FDA regulations for food-grade plastics if applicable.
- 2
Understand REACH and RoHS compliance for chemicals and materials used.
- 3
Stay aware of environmental regulations related to plastic waste and recycling.
- 4
Consider workplace safety regulations relevant to handling materials and equipment.
- 5
Be prepared to discuss certifications like ISO 9001 that pertain to quality management.
Example Answers
In plastic manufacturing, it's crucial to comply with FDA regulations for any materials used in food packaging. Additionally, understanding REACH for chemical safety and RoHS for restricted substances helps ensure product safety.
Describe a method you would use to optimize the efficiency of a plastic extrusion process.
How to Answer
- 1
Evaluate the current process data to identify bottlenecks.
- 2
Implement temperature controls to ensure consistent melting of material.
- 3
Adjust screw speed and feeding rate for optimal material flow.
- 4
Regularly maintain and clean equipment to prevent downtime.
- 5
Train operators on best practices for monitoring and adjustments.
Example Answers
To optimize plastic extrusion efficiency, I would first analyze the production data to pinpoint where delays occur. Then, I would ensure that the temperature settings of the extruder are calibrated precisely to improve the melting process. Additionally, I would adjust the screw speed based on real-time material flow measurements to enhance throughput.
How would you go about designing a mold for a new plastic part? What factors must be considered?
How to Answer
- 1
Identify the part's geometry and dimensions to determine mold design.
- 2
Consider the type of plastic being used and its properties.
- 3
Account for draft angles to ensure easy part release from the mold.
- 4
Evaluate cooling requirements to minimize cycle time and prevent defects.
- 5
Plan for any necessary inserts or features in the mold for functionality.
Example Answers
To design a mold for a new plastic part, I would start by examining the part's geometry and dimensions to create an accurate mold shape. I would also select appropriate materials based on the type of plastic, ensuring to include draft angles for easy removal and optimize cooling channels to reduce cycle time and maintain part integrity.
What are your steps for performing regular maintenance on plastic production equipment to ensure its longevity and optimal performance?
How to Answer
- 1
Inspect machinery regularly for wear and tear.
- 2
Clean equipment thoroughly to prevent contamination.
- 3
Lubricate moving parts as per the manufacturer's schedule.
- 4
Replace worn-out components proactively to avoid breakdowns.
- 5
Document maintenance activities and any issues for future reference.
Example Answers
I perform monthly inspections on the production line, checking for any signs of wear. After each shift, I clean the equipment to remove any plastic residue. I also lubricate the moving parts according to the manual and keep a log of maintenance activities.
How do you manage and control the costs associated with plastic production without sacrificing quality?
How to Answer
- 1
Analyze the production process for inefficiencies and areas of waste.
- 2
Negotiate with suppliers for better material prices without compromising quality.
- 3
Implement a quality management system to catch defects early, reducing rework costs.
- 4
Train staff on cost-effective practices and quality standards.
- 5
Utilize data monitoring for inventory and production to optimize resource use.
Example Answers
I regularly review the production process to identify any inefficiencies, such as excessive scrap material, and work to minimize those areas. By negotiating better rates with our suppliers while maintaining the quality of materials, I also ensure we have cost-effective components. Additionally, I have implemented a quality management system that reduces defects and minimizes rework costs.
Don't Just Read Plastic Maker Questions - Practice Answering Them!
Reading helps, but actual practice is what gets you hired. Our AI feedback system helps you improve your Plastic Maker interview answers in real-time.
Personalized feedback
Unlimited practice
Used by hundreds of successful candidates
Situational Interview Questions
If a key piece of machinery broke down during a critical time in the production schedule, what steps would you take to address the situation?
How to Answer
- 1
Assess the situation quickly to understand the impact on production.
- 2
Notify your supervisor or team leader about the breakdown immediately.
- 3
Initiate troubleshooting steps or consult the manual for quick fixes.
- 4
Coordinate with maintenance for repairs and communicate estimated downtime.
- 5
Explore alternative solutions like reallocating resources or using backup equipment.
Example Answers
I would first assess the impact of the breakdown on our production schedule and notify my supervisor right away. Then, I would check the equipment manual to troubleshoot any quick fixes. If needed, I’d reach out to maintenance for urgent repairs while considering if we could use backup machinery for the time being.
You have been asked to increase production output by 25% to meet an urgent deadline. How would you go about achieving this goal?
How to Answer
- 1
Assess current production processes and identify bottlenecks
- 2
Implement overtime or additional shifts as needed
- 3
Optimize workflow by reallocating resources and personnel
- 4
Introduce time-saving techniques or tools
- 5
Communicate with the team to motivate and align efforts
Example Answers
To achieve a 25% increase in output, I would first analyze our current workflow to identify any bottlenecks that slow production down. Then, I would consider implementing overtime for key workers to boost productivity. I would also ensure resources are allocated effectively and explore any tools that could enhance our efficiency. Lastly, I'll keep the team informed and motivated throughout this period.
Don't Just Read Plastic Maker Questions - Practice Answering Them!
Reading helps, but actual practice is what gets you hired. Our AI feedback system helps you improve your Plastic Maker interview answers in real-time.
Personalized feedback
Unlimited practice
Used by hundreds of successful candidates
A batch of plastic parts has been returned due to quality issues. How would you investigate and remedy such a situation?
How to Answer
- 1
Gather detailed information about the quality issues reported.
- 2
Inspect the returned parts to identify specific defects.
- 3
Review the production process and materials used for that batch.
- 4
Engage with team members involved in production for their insights.
- 5
Implement corrective actions based on findings and monitor results.
Example Answers
First, I would gather specific details about the quality issues reported with the plastic parts. Next, I'd inspect the returned parts to identify any defects and patterns. Then, I would review the production process and check the materials used. I would also consult with the production team to understand any potential oversights. Based on this investigation, I would implement the necessary corrective actions and closely monitor the next batch for improvements.
How would you approach the task of developing a new plastic product that meets environmental sustainability standards?
How to Answer
- 1
Research current sustainable materials and technologies in plastic production
- 2
Involve stakeholders, including environmental experts, in the design process
- 3
Utilize life cycle assessment to evaluate the environmental impact of the product
- 4
Focus on recyclability and biodegradability in material selection
- 5
Create prototypes and iterate based on sustainability performance feedback
Example Answers
I would start by researching sustainable materials such as bioplastics or recycled plastics. Then, I would collaborate with environmental experts to integrate their insights into the design. Using life cycle assessment would help me ensure the product minimizes environmental impact throughout its life. Finally, I would ensure that the final design is easily recyclable.
You need to train a new employee on the operation of a complex plastic molding machine. How would you ensure they fully understand the process and safety measures?
How to Answer
- 1
Start with a thorough overview of the machine's components and functions
- 2
Conduct a live demonstration of the molding process
- 3
Emphasize the importance of safety protocols and demonstrate them
- 4
Provide written materials that outline procedures and safety measures
- 5
Encourage questions and interactive practice sessions for hands-on learning
Example Answers
I would begin by giving the new employee a detailed overview of the molding machine, explaining each component's role. Then, I'd perform a live demonstration so they can see the process in action. Safety measures would be emphasized throughout, making sure they understand the protocols through both demonstration and written materials. Finally, I'd encourage them to ask questions and participate in practice sessions to reinforce their learning.
You receive a complaint from a client about the consistency of the plastic color in their order. What is your course of action?
How to Answer
- 1
Acknowledge the complaint and thank the client for their feedback.
- 2
Investigate the issue by reviewing the production process and color specifications.
- 3
Communicate transparently with the client about your findings.
- 4
Offer a solution, such as a rework or replacement of the affected order.
- 5
Document the incident and adjust procedures to prevent future issues.
Example Answers
I would first thank the client for bringing the issue to my attention. Then I would review the production records to identify any discrepancies in the color mixing. Once I have gathered the information, I would communicate my findings to the client and propose a solution, whether that be a replacement or adjustment of their order.
Given a limited budget, how would you decide where to allocate resources in a plastic production process to maximize efficiency?
How to Answer
- 1
Analyze current production data to identify bottlenecks.
- 2
Evaluate the cost-benefit ratio of different production areas.
- 3
Consider investing in maintenance of high-use machinery first.
- 4
Prioritize training for workers on critical processes.
- 5
Explore opportunities for material savings without compromising quality.
Example Answers
I would start by reviewing production metrics to pinpoint the stages that slow down output. Then, I'd focus resources on addressing those bottlenecks, perhaps by maintaining key equipment. Investing in worker training could also boost efficiency at those critical points.
If you were tasked with integrating a new manufacturing technology into the plastic production line, how would you approach this implementation?
How to Answer
- 1
Assess the current production line capabilities and limitations
- 2
Engage with stakeholders to understand their needs and concerns
- 3
Research the new technology's requirements and benefits
- 4
Create a detailed implementation plan with timelines and milestones
- 5
Provide training for staff and ensure support during the transition
Example Answers
I would start by evaluating our current production line to identify where the new technology can add value. Then, I would consult with the team to gather their input and address any concerns. After researching the technology, I would draft a thorough implementation plan and schedule training for staff ahead of the switch.
What steps would you take to reduce the environmental impact of plastic production in a manufacturing facility?
How to Answer
- 1
Implement energy-efficient machinery to reduce energy consumption.
- 2
Recycle and reuse plastic scrap within the production process.
- 3
Source raw materials from sustainable suppliers to minimize environmental impact.
- 4
Invest in biodegradable or environmentally friendly alternatives when possible.
- 5
Regularly assess and optimize the production process to reduce waste.
Example Answers
I would focus on energy efficiency by upgrading to machines that consume less power, and I would ensure that we recycle any plastic waste generated during production.
How would you respond if a client called with an urgent request for a large order that exceeds current production capacity?
How to Answer
- 1
Acknowledge the urgency and importance of the request.
- 2
Communicate openly about current production limitations.
- 3
Explore options such as prioritizing existing orders or overtime.
- 4
Discuss potential timelines and negotiate realistic deadlines.
- 5
Maintain a positive attitude and express willingness to find a solution.
Example Answers
I would first thank the client for their urgent request, then explain our current production capacity. I would suggest ways we can accommodate their order, such as scheduling overtime or staggering their request over a few weeks while ensuring they receive updates regularly.
Don't Just Read Plastic Maker Questions - Practice Answering Them!
Reading helps, but actual practice is what gets you hired. Our AI feedback system helps you improve your Plastic Maker interview answers in real-time.
Personalized feedback
Unlimited practice
Used by hundreds of successful candidates
How would you handle a situation where you need to work closely with the design team to ensure the feasibility of a new plastic product?
How to Answer
- 1
Establish clear communication channels with the design team
- 2
Participate in initial design meetings to understand goals and constraints
- 3
Provide input on material properties and manufacturing processes early
- 4
Encourage collaboration through regular check-ins and feedback loops
- 5
Document key decisions and changes to track progress and maintain alignment
Example Answers
I would start by setting up regular meetings with the design team to discuss their ideas and any limitations we might face. By offering suggestions on material properties from the outset, we can ensure that the designs are feasible.
Plastic Maker Position Details
Recommended Job Boards
CareerBuilder
www.careerbuilder.com/jobs/plastic-makerZipRecruiter
www.ziprecruiter.com/Jobs/Plastics-ManufacturingThese job boards are ranked by relevance for this position.
Related Positions
- Plastic Fabricator
- Mat Maker
- Filament Maker
- Mold Filler
- Pencil Maker
- Stem Maker
- Rubber Stamp Maker
- Cable Maker
- Doll Maker
- Crate Maker
Similar positions you might be interested in.
Ace Your Next Interview!
Practice with AI feedback & get hired faster
Personalized feedback
Used by hundreds of successful candidates
Ace Your Next Interview!
Practice with AI feedback & get hired faster
Personalized feedback
Used by hundreds of successful candidates