Top 30 Cable Maker Interview Questions and Answers [Updated 2025]
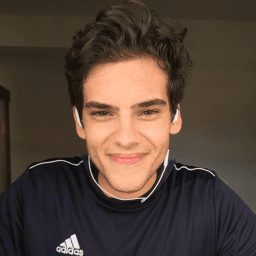
Andre Mendes
•
March 30, 2025
Are you gearing up for a Cable Maker job interview and unsure what to expect? Our latest blog post is your go-to guide for navigating the most common interview questions for this role. We offer example answers and valuable tips to help you respond confidently and effectively. Whether you’re a seasoned professional or a newcomer, prepare to impress and elevate your interview game!
Download Cable Maker Interview Questions in PDF
To make your preparation even more convenient, we've compiled all these top Cable Makerinterview questions and answers into a handy PDF.
Click the button below to download the PDF and have easy access to these essential questions anytime, anywhere:
List of Cable Maker Interview Questions
Behavioral Interview Questions
Can you describe a time when your attention to detail helped prevent a potential issue in manufacturing?
How to Answer
- 1
Identify a specific example from your past experience
- 2
Explain your role in the situation clearly
- 3
Describe the potential issue you prevented
- 4
Highlight the actions you took that demonstrated your attention to detail
- 5
Conclude with the positive outcome of your actions
Example Answers
In my previous role as a cable assembler, I noticed that some wires were not aligned properly before the insulation was applied. I double-checked the setup and discovered a minor error in the machine settings that could have led to misalignment in production. By correcting this before it became an issue, we avoided wastage and ensured all cables met the quality standards.
Tell me about a challenging cable assembly problem you faced and how you resolved it.
How to Answer
- 1
Identify a specific problem you encountered in cable assembly.
- 2
Explain the steps you took to diagnose the issue.
- 3
Detail the solution you implemented and why it was effective.
- 4
Highlight any collaboration with team members if applicable.
- 5
Share what you learned from the experience and how it improved your skills.
Example Answers
In my previous job, we had recurring issues with cable insulation breaking during assembly. I investigated and found the tools we were using were damaging the cables. I switched to a new tool that applied less pressure. This solved the problem completely and we reduced waste by 15%.
Don't Just Read Cable Maker Questions - Practice Answering Them!
Reading helps, but actual practice is what gets you hired. Our AI feedback system helps you improve your Cable Maker interview answers in real-time.
Personalized feedback
Unlimited practice
Used by hundreds of successful candidates
Describe a situation where you had to work closely with a team to complete a project on time. What was your role, and what was the outcome?
How to Answer
- 1
Choose a specific project example where teamwork was essential.
- 2
Clearly define your role and responsibilities in the team.
- 3
Highlight the importance of communication and collaboration.
- 4
Describe any challenges faced and how the team overcame them.
- 5
Conclude with the project's success or learning outcomes.
Example Answers
In my previous job at a manufacturing plant, we had a tight deadline to produce a new batch of cables for a client. I was the team leader responsible for coordinating tasks among the production staff. We held daily meetings to ensure everyone was aligned, and we faced a last-minute issue with raw materials. By communicating effectively and reallocating resources, we completed the project on time, and the client was very satisfied.
Give an example of a time you identified a defect or quality issue in a component. How did you handle it?
How to Answer
- 1
Be specific about the defect you found
- 2
Explain the steps you took to address it
- 3
Discuss the outcome and what was learned
- 4
Highlight collaboration or communication if applicable
- 5
Emphasize your attention to detail and problem-solving skills
Example Answers
In my previous job, I found a frayed wire in a batch of cables during a quality check. I immediately reported it to my supervisor and isolated the affected batch. We conducted a thorough review and identified the source of the defect in our supplier's materials. This led to improved quality checks from the vendor and a 25% reduction in similar defects in future batches.
How do you prioritize your tasks when you have multiple deadlines to meet in a day?
How to Answer
- 1
List all tasks and their deadlines to visualize the workload.
- 2
Identify urgent versus important tasks using the Eisenhower Matrix.
- 3
Break larger tasks into smaller, manageable steps.
- 4
Set specific time slots for focused work on high-priority items.
- 5
Communicate with team members if reassessment of priorities is needed.
Example Answers
I start by listing all my tasks and their deadlines. Then, I categorize them into urgent and important tasks. I focus on the urgent ones first while ensuring I break larger tasks into smaller steps so I can make progress efficiently.
How have you updated your skills and knowledge in cable manufacturing over the years?
How to Answer
- 1
Highlight specific training or certifications you've completed.
- 2
Mention any industry conferences or seminars you've attended.
- 3
Discuss how you stay updated with technological advancements in the field.
- 4
Include any relevant online courses or resources you've engaged with.
- 5
Share experiences of applying new skills in your previous jobs.
Example Answers
Over the past few years, I have completed a certification in advanced cable manufacturing processes, and I regularly attend industry conferences like the Cable Tech Expo to stay informed on the latest technologies.
Describe a time when you proactively improved a process or tool in your workspace.
How to Answer
- 1
Think of a specific situation where you identified a problem.
- 2
Explain the steps you took to analyze the issue.
- 3
Detail the changes you implemented and their impact.
- 4
Use quantifiable results if possible to demonstrate success.
- 5
Conclude with what you learned from the experience.
Example Answers
In my previous job, I noticed that our cable cutting process was slow. I studied the workflow, identified that our measurement tool was outdated, and proposed a new digital measuring tool. After implementing it, we decreased cutting time by 30%, which increased overall productivity.
How have you handled a disagreement with a coworker regarding the approach to a cable assembly?
How to Answer
- 1
Listen actively to your coworker's perspective to understand their reasoning
- 2
Share your thoughts clearly and explain why you prefer your approach
- 3
Seek common ground by looking for a solution that incorporates both ideas
- 4
Suggest a trial period for both methods to evaluate effectiveness
- 5
Maintain professionalism and focus on the project's best outcome
Example Answers
In a previous project, a coworker and I disagreed on the cable routing method. I made sure to listen to their approach and shared my thoughts on why I preferred mine, explaining the benefits. We decided to test both methods side by side and chose the most efficient approach based on the results.
Provide an example of how you met a particularly challenging production target.
How to Answer
- 1
Choose a specific instance where you faced a challenging goal.
- 2
Explain the steps you took to achieve this target.
- 3
Include any teamwork or collaboration involved.
- 4
Discuss the outcome and how it benefited the company.
- 5
Highlight any skills or techniques that helped you succeed.
Example Answers
At my previous job, we had to increase our production output by 20% in just three months due to a new client. I organized weekly meetings to keep everyone aligned, and we implemented a new workflow strategy that increased efficiency. As a result, we not only met but exceeded the target by 5%, strengthening our relationship with the client.
Don't Just Read Cable Maker Questions - Practice Answering Them!
Reading helps, but actual practice is what gets you hired. Our AI feedback system helps you improve your Cable Maker interview answers in real-time.
Personalized feedback
Unlimited practice
Used by hundreds of successful candidates
Technical Interview Questions
What types of materials have you worked with in cable making, and what are their specific applications?
How to Answer
- 1
Identify key materials you have used in cable making.
- 2
Explain specific applications for each material mentioned.
- 3
Relate experiences or projects where you utilized these materials.
- 4
Highlight any relevant standards or certifications followed when using materials.
- 5
Be concise but detailed enough to show knowledge and experience.
Example Answers
I have worked primarily with copper and aluminum for conductors. Copper is used for most power cables due to its excellent conductivity, while aluminum is often chosen for overhead power lines because it is lighter.
What are the steps involved in building a complex wire harness?
How to Answer
- 1
Start with a schematic or design plan of the wire harness layout.
- 2
Select the appropriate materials and components, like wires, connectors, and insulation.
- 3
Cut wires to the required lengths and strip the ends for connections.
- 4
Assemble the wires according to the plan, ensuring proper routing and organization.
- 5
Test the completed harness for continuity and functionality before installation.
Example Answers
To build a complex wire harness, I first review the schematic to understand the layout. Then, I gather all necessary materials such as wires and connectors. After cutting and stripping the wires, I assemble them according to the design, ensuring everything is well organized, and finally, I test the harness for continuity.
Don't Just Read Cable Maker Questions - Practice Answering Them!
Reading helps, but actual practice is what gets you hired. Our AI feedback system helps you improve your Cable Maker interview answers in real-time.
Personalized feedback
Unlimited practice
Used by hundreds of successful candidates
What tools and equipment are essential for a cable maker, and how do you ensure they are properly maintained?
How to Answer
- 1
List key tools such as wire cutters, strippers, and crimping tools.
- 2
Explain the importance of safety equipment like gloves and goggles.
- 3
Discuss maintenance practices like regular cleaning and inspections.
- 4
Mention any testing equipment used to ensure cable quality.
- 5
Highlight the importance of following manufacturer guidelines for equipment care.
Example Answers
As a cable maker, essential tools include wire cutters, strippers, and crimpers. I ensure these tools are maintained by regularly cleaning them after use and checking for any damage. I also perform routine inspections to confirm they work properly.
Can you explain the process of soldering connections in cable manufacturing?
How to Answer
- 1
Start by describing the preparation of the wires, including stripping insulation.
- 2
Explain the soldering tools used, such as soldering iron and solder.
- 3
Detail the soldering process, indicating heating and applying solder to the joint.
- 4
Mention safety precautions, like using protective gear.
- 5
Conclude with the importance of verifying the connection quality.
Example Answers
First, I prepare the wires by stripping the insulation to expose the metal. I then heat my soldering iron and apply it to the joint where the wires meet. I introduce solder to the heated area to create a strong bond. It's crucial to wear safety goggles to protect my eyes. After soldering, I always check the connection to ensure it's solid.
How do you interpret technical diagrams and schematics for cable assembly?
How to Answer
- 1
Identify key components in the diagram such as connectors and wires.
- 2
Use color codes and symbols to understand wiring specifications.
- 3
Trace the connections from point to point to ensure accuracy.
- 4
Cross-reference with the assembly instructions if available.
- 5
Practice reading different types of diagrams to improve speed and comprehension.
Example Answers
I start by identifying the main components such as connectors and wires. Then, I pay attention to the color codes and symbols to interpret their functions correctly. Tracing the connections helps me to visualize how the assembly should be done.
What methods do you use to test the quality and functionality of a cable after assembly?
How to Answer
- 1
Describe visual inspection techniques for identifying physical defects.
- 2
Mention electrical testing methods like continuity tests and insulation resistance tests.
- 3
Include the use of specialized equipment such as cable testers or multimeters.
- 4
Explain the importance of performance testing under various conditions.
- 5
Emphasize the need for documenting and tracking test results.
Example Answers
I start with a visual inspection to check for any visible defects like insulation damage. Then, I perform a continuity test using a multimeter to ensure there are no breaks in the wire. I also check insulation resistance to verify safety standards and sometimes put the cable under load to see how it performs in real conditions.
What safety procedures do you follow when working with electrical cables and equipment?
How to Answer
- 1
Always wear appropriate PPE such as gloves and safety goggles.
- 2
Ensure the power source is turned off before starting any work on cables.
- 3
Use insulated tools to prevent electrical shock.
- 4
Follow lockout/tagout procedures to ensure equipment cannot be accidentally energized.
- 5
Regularly inspect cables for damage or wear before use.
Example Answers
I always wear gloves and goggles, ensure power is off, and use insulated tools. Additionally, I follow the lockout/tagout procedures to keep the workspace safe.
How do you troubleshoot faults in a cable that is not functioning as expected?
How to Answer
- 1
Start by visually inspecting the cable for any obvious damage or wear.
- 2
Use a multimeter to check for continuity and identify breaks in the wire.
- 3
Test the cable with a known good device to confirm if the fault lies within the cable or the device.
- 4
Check the connectors and terminals for proper fit and ensure there is no corrosion.
- 5
Isolate sections of the cable to locate the fault more effectively.
Example Answers
I begin by inspecting the cable visually to look for any physical damage. Next, I use a multimeter to check continuity. If the multimeter shows a break, I isolate sections of the cable to locate the fault.
Describe how you ensure precision when measuring and cutting cable lengths.
How to Answer
- 1
Always use a reliable measuring tool like a tape measure or digital caliper.
- 2
Double-check measurements before cutting to minimize errors.
- 3
Use a cutting tool that is appropriate for the material to ensure a clean cut.
- 4
Mark the cutting point clearly with a pencil or marker for accuracy.
- 5
Practice measuring and cutting techniques to build muscle memory.
Example Answers
I always start by using a precise tape measure, double-checking my measurements before cutting. I mark the cut line clearly and use a sharp pair of cable cutters to get a clean edge.
What are the differences between various insulation types used in cables, and how do you decide which to use?
How to Answer
- 1
Identify common insulation types like PVC, XLPE, and rubber.
- 2
Explain the properties of each insulation type, such as temperature resistance and flexibility.
- 3
Discuss applications where each type is ideally suited.
- 4
Mention factors influencing the choice, like environmental conditions and electrical requirements.
- 5
Conclude with an example of deciding on insulation for a specific project.
Example Answers
There are several insulation types like PVC, XLPE, and rubber. PVC is cost-effective and good for general use, while XLPE can handle higher temperatures and is more durable. Rubber is flexible and ideal for movable applications. I choose based on the project's temperature range and environmental factors, for instance, using XLPE in underground installations for its durability.
Don't Just Read Cable Maker Questions - Practice Answering Them!
Reading helps, but actual practice is what gets you hired. Our AI feedback system helps you improve your Cable Maker interview answers in real-time.
Personalized feedback
Unlimited practice
Used by hundreds of successful candidates
What considerations do you keep in mind when selecting connectors for a specific cable application?
How to Answer
- 1
Consider the electrical specifications such as voltage and current ratings.
- 2
Evaluate the environmental conditions like temperature, moisture, and exposure to chemicals.
- 3
Look at the mechanical requirements including stress, strain, and flexibility needed for the application.
- 4
Assess the compatibility with existing equipment and standards.
- 5
Think about the ease of installation and maintenance for the connectors.
Example Answers
When selecting connectors, I first check the voltage and current ratings to ensure safety and performance. I also assess the environmental conditions, like if they'll be used outdoors or in wet environments, to choose connectors that withstand those factors.
Explain the importance of bonding and grounding in cable assembly.
How to Answer
- 1
Define bonding and grounding clearly to establish a foundation for your answer.
- 2
Explain how bonding enhances safety by preventing electrical shock and reducing noise interference.
- 3
Discuss grounding as a method for protecting equipment from lightning and power surges.
- 4
Mention compliance with industry standards and regulations related to bonding and grounding.
- 5
Provide a practical example of bonding and grounding in a real-world cable assembly application.
Example Answers
Bonding connects different conductive parts together to ensure they have the same electrical potential, which prevents shock hazards, while grounding directs excess electricity safely into the earth, protecting both the system and people.
Situational Interview Questions
If you have five urgent cable orders and not enough resources to complete all on time, how would you handle the situation?
How to Answer
- 1
Prioritize orders based on delivery deadlines and customer importance
- 2
Communicate with customers about possible delays transparently
- 3
Seek assistance from team members or consider reallocating resources
- 4
Focus on completing the most critical tasks first
- 5
Document and learn from the situation to improve future planning
Example Answers
I would first assess the urgency of each order and prioritize them. I'd communicate with the customers about anticipated delays if necessary and see if any team members could help out with the workload, focusing on getting the highest priority orders completed first.
Suppose you discover a batch of cables you've made has a latent defect after it has been shipped. What steps would you take to address the issue?
How to Answer
- 1
Immediately notify your supervisor and the quality assurance team.
- 2
Gather detailed information about the defect and affected batches.
- 3
Communicate with the affected customers and provide a solution.
- 4
Implement corrective actions to prevent future defects.
- 5
Document the incident thoroughly for future reference and improvement.
Example Answers
First, I would inform my supervisor and quality assurance immediately. Then, I’d collect all relevant data about the defect and which batches it affects. I’d reach out to customers to inform them and discuss options for returns or replacements. After that, I would work with the team to implement measures to prevent this kind of defect in the future. Lastly, I would document everything for accountability.
Don't Just Read Cable Maker Questions - Practice Answering Them!
Reading helps, but actual practice is what gets you hired. Our AI feedback system helps you improve your Cable Maker interview answers in real-time.
Personalized feedback
Unlimited practice
Used by hundreds of successful candidates
You're midway through a project and realize you've run out of a critical component. How would you manage the situation to continue production?
How to Answer
- 1
Assess the impact of the missing component on the project timeline.
- 2
Look for alternative sources or suppliers for the critical component.
- 3
Consider using a substitute material if feasible without compromising quality.
- 4
Communicate with the team and stakeholders about the situation and potential solutions.
- 5
Adjust the project plan to accommodate the delay if necessary.
Example Answers
I would first evaluate how critical the component is to the immediate production stage. Then, I would reach out to local suppliers to see if they have the part available or explore any alternative components that could serve the same function. Keeping my team updated on the situation is crucial, and I would adjust our timeline based on the best solution we identify.
Your main soldering equipment breaks down unexpectedly during a critical batch. How would you resolve this issue?
How to Answer
- 1
Assess the situation quickly to understand the breakdown
- 2
Check if there is a backup soldering tool available for immediate use
- 3
Inform your supervisor about the issue and suggest a solution
- 4
If no backup is available, identify the nearest location to get the equipment repaired or replaced
- 5
Document the incident for future reference and maintenance schedules
Example Answers
I would quickly assess the soldering equipment to identify the problem and see if there is a backup tool I can use immediately. If not, I would inform my supervisor and look for the nearest repair shop to get it fixed or find a rental option.
A client has returned a batch of cables citing inconsistent lengths. How would you investigate and resolve the issue?
How to Answer
- 1
Review the order specifications and requirements.
- 2
Check production records for the batch to identify any anomalies.
- 3
Measure a sample of cables from the batch to verify length consistency.
- 4
Engage with the production team to understand the manufacturing process.
- 5
Communicate findings to the client and propose a solution or compensation.
Example Answers
First, I would review the client's specifications to confirm the required lengths. Then, I'd check the production records to see if there were any discrepancies during manufacturing. After that, I'd take a random sample from the returned batch and measure their lengths to assess the inconsistency. I would also consult with the production team to understand any potential issues that may have occurred. Lastly, I'd communicate the results to the client and discuss a suitable resolution.
If a colleague continually overlooks a key step in the quality control process, what would you do to ensure standards are met?
How to Answer
- 1
Identify the specific key step being overlooked
- 2
Communicate with the colleague privately to discuss the issue
- 3
Offer to help them understand the importance of the step
- 4
Suggest additional training or resources if necessary
- 5
Collaborate to develop a checklist or reminder system
Example Answers
I would first identify which specific step they are overlooking and then approach them privately to discuss my concerns. I'd emphasize the importance of that step in maintaining our quality standards and offer to assist them in understanding it better. If needed, I could suggest additional training or develop a checklist we could both use to ensure we don't miss anything.
If you identify a bottleneck in the production line, how would you propose a solution for improving the workflow?
How to Answer
- 1
Observe and analyze the current workflow to identify specific causes of the bottleneck.
- 2
Engage with team members for insights and feedback on the bottleneck.
- 3
Research potential solutions or improvements based on industry best practices.
- 4
Present a clear plan that includes steps to implement the solution and metrics to measure success.
- 5
Suggest conducting a trial of the proposed solution to evaluate its effectiveness before full implementation.
Example Answers
First, I would observe the production line to pinpoint exactly where the bottleneck is occurring and gather data to understand its impact on overall throughput. Then, I would discuss it with my colleagues to hear their perspectives and gather additional insights. After that, I would propose implementing a more efficient machine at that stage or redistributing tasks among team members to alleviate the overload. I would suggest running a 2-week trial and measure the output to see if the solution effectively reduces the bottleneck.
During a routine check, you notice a severe safety hazard. What immediate actions do you take to manage the risk?
How to Answer
- 1
Identify and assess the severity of the hazard immediately.
- 2
Notify your supervisor and relevant personnel about the hazard.
- 3
Implement immediate containment measures to prevent any accidents.
- 4
Document the hazard and your response actions for reporting.
- 5
Follow up to ensure that corrective actions are taken.”],
Example Answers
I would first assess the situation to understand the risk. Then, I would notify my supervisor about the severe safety hazard and take any immediate actions needed to secure the area. I would block access to the hazard until trained personnel can address it. Finally, I would document the incident to ensure it is handled properly.
Cable Maker Position Details
Recommended Job Boards
CareerBuilder
www.careerbuilder.com/jobs/cable-makerZipRecruiter
www.ziprecruiter.com/Jobs/Cable-MakerThese job boards are ranked by relevance for this position.
Related Positions
- Filament Maker
- Mat Maker
- Hose Maker
- Pencil Maker
- Plastic Maker
- End Maker
- Cushion Maker
- Plug Maker
- Camera Maker
- Stem Maker
Similar positions you might be interested in.
Ace Your Next Interview!
Practice with AI feedback & get hired faster
Personalized feedback
Used by hundreds of successful candidates
Ace Your Next Interview!
Practice with AI feedback & get hired faster
Personalized feedback
Used by hundreds of successful candidates