Top 30 Hose Maker Interview Questions and Answers [Updated 2025]
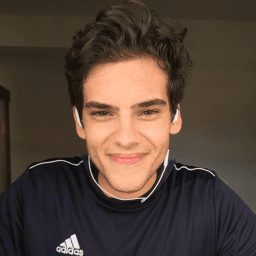
Andre Mendes
•
March 30, 2025
Preparing for a Hose Maker interview? This blog post is your go-to guide for the most common questions interviewers ask in this specialized field. Dive into example answers and practical tips on how to respond effectively, helping you stand out and showcase your expertise. Whether you're a seasoned professional or new to the industry, these insights will boost your confidence and readiness.
Download Hose Maker Interview Questions in PDF
To make your preparation even more convenient, we've compiled all these top Hose Makerinterview questions and answers into a handy PDF.
Click the button below to download the PDF and have easy access to these essential questions anytime, anywhere:
List of Hose Maker Interview Questions
Behavioral Interview Questions
Can you describe a time when you worked as part of a team to complete a hose-making project? What was your role?
How to Answer
- 1
Choose a specific project with clear goals and outcomes
- 2
Highlight your role and contributions to the team
- 3
Discuss any challenges faced and how you overcame them
- 4
Mention the skills you utilized or developed during the project
- 5
Conclude with the results or achievements of the project
Example Answers
During a project to create a custom hose for an agricultural client, I was responsible for coordinating with the design team to ensure specifications were met. We faced a challenge with material availability, so I sourced alternative options that fit the client's needs. The project was completed on time and resulted in a 15% reduction in costs.
Tell me about a challenging issue you faced while manufacturing hoses and how you resolved it.
How to Answer
- 1
Identify a specific issue you encountered during the manufacturing process.
- 2
Explain the impact of the issue on production or quality.
- 3
Describe the steps you took to analyze and resolve the issue.
- 4
Highlight the result of your actions and any lessons learned.
- 5
Keep your answer structured and focused.
Example Answers
During a production run, I noticed a consistent leak in the hoses being manufactured. I analyzed the assembly process and found an issue with the sealing method. I proposed a new technique, tested it, and successfully reduced leak rates by 30%. This experience taught me the importance of thorough quality checks.
Don't Just Read Hose Maker Questions - Practice Answering Them!
Reading helps, but actual practice is what gets you hired. Our AI feedback system helps you improve your Hose Maker interview answers in real-time.
Personalized feedback
Unlimited practice
Used by hundreds of successful candidates
Can you give an example of how your attention to detail improved the quality of the hoses you produced?
How to Answer
- 1
Choose a specific project where your attention to detail made a difference
- 2
Explain the process you followed and the checks you implemented
- 3
Quantify the results if possible, such as reduced defects or improved performance
- 4
Highlight any positive feedback received from supervisors or clients
- 5
Connect the example back to the importance of quality in hose making
Example Answers
In my previous role, I noticed that there were inconsistencies in hose fittings. I implemented a double-check system during assembly, which reduced our defect rate by 30%. This improvement led to positive feedback from our quality assurance team, emphasizing the importance of precision in hose manufacturing.
Describe a conflict you had with a coworker regarding a hose production method. How did you handle it?
How to Answer
- 1
Use the STAR method: Situation, Task, Action, Result.
- 2
Be specific about the conflict and the production method involved.
- 3
Emphasize communication and problem-solving skills.
- 4
Highlight any positive outcomes from the resolution.
- 5
Avoid negative language and focus on lessons learned.
Example Answers
In a previous role, we disagreed on the best method for curing hoses. I took the initiative to discuss our approaches openly. We tested both methods, and ultimately, my coworker's method proved more efficient, leading to a 15% reduction in production time.
Tell me about a time you had to manage multiple hose orders with tight deadlines. How did you prioritize your tasks?
How to Answer
- 1
Identify a specific situation with clear deadlines
- 2
Explain the method you used to prioritize tasks
- 3
Highlight key decisions made based on urgency and importance
- 4
Mention any tools or strategies that aided your organization
- 5
Include the outcome and what you learned from the experience
Example Answers
In my previous role, I had three hose orders due on the same day. I first assessed the order sizes and delivery timelines. I prioritized the largest order, as it was for a key customer. I used a checklist to track progress, ensuring I met the deadlines. All orders were completed on time, and I learned the importance of effective prioritization.
Can you discuss a time when you learned a new technique or skill that significantly enhanced your hose-making ability?
How to Answer
- 1
Choose a specific technique or skill that is relevant to hose making.
- 2
Describe the context or challenge that prompted you to learn it.
- 3
Explain how you went about learning the technique, including any resources used.
- 4
Discuss the impact this new skill had on your work quality or efficiency.
- 5
Conclude with what you learned from the experience and how it shaped your approach.
Example Answers
I learned a new method for layering materials to improve hose flexibility. Faced with a project requiring more durable hoses, I researched techniques online and consulted with experienced colleagues. Implementing this skill increased the hose lifespan by 20% and enhanced customer satisfaction. This taught me the importance of continuous improvement.
Describe a time when you received constructive criticism about your work in hose production. How did you respond?
How to Answer
- 1
Select a specific instance of feedback related to hose production.
- 2
Focus on the criticism received and your immediate reaction.
- 3
Explain the steps taken to improve based on the feedback.
- 4
Highlight any positive outcomes or lessons learned.
- 5
Keep your answer concise and relevant to hose production.
Example Answers
During a quality check, my supervisor noted that my hose connections were not as tight as they should be. I listened carefully, acknowledged the feedback, and immediately reviewed the process. I practiced the connection technique and soon saw a decrease in rework needed. This feedback made my work more efficient.
Can you provide an example of a leadership experience in a hose production environment?
How to Answer
- 1
Think of a specific project or situation where you led a team.
- 2
Highlight your role in improving processes or product quality.
- 3
Include measurable outcomes or results from your leadership.
- 4
Mention how you motivated or supported your team.
- 5
Reflect on any challenges you faced and how you addressed them.
Example Answers
In my previous role, I led a team of five during a production ramp-up. We improved our output by 20% by streamlining the assembly line layout. I encouraged daily briefings to boost team morale and address issues quickly.
Technical Interview Questions
What types of materials are commonly used in hose manufacturing, and how do their properties affect performance?
How to Answer
- 1
Identify key materials like rubber, PVC, and polyurethane.
- 2
Explain how each material's flexibility, durability, and resistance to chemicals affects use.
- 3
Mention specific applications for different materials to demonstrate knowledge.
- 4
Be concise and focus on how material properties impact performance in real-world scenarios.
- 5
Use clear examples to showcase your understanding of material performance.
Example Answers
Common materials include rubber for its flexibility and durability, PVC for its lightweight and affordability, and polyurethane for its abrasion resistance. For example, rubber hoses are great for high-pressure applications, while PVC is often used for standard water delivery.
Can you explain the steps involved in the hose-making process from start to finish?
How to Answer
- 1
Start by outlining the material selection process.
- 2
Describe the manufacturing techniques used for the hose.
- 3
Explain the assembly of components and quality checks.
- 4
Mention testing procedures for durability and performance.
- 5
Conclude with any finishing touches before packaging.
Example Answers
The hose-making process begins with selecting the right materials like rubber or thermoplastic. Next, the hoses are manufactured using extrusion or weaving techniques. After that, components such as fittings are assembled, followed by quality checks to ensure they meet standards. Then, the hoses undergo rigorous testing for durability. Finally, they receive finishing touches and are packaged for distribution.
Don't Just Read Hose Maker Questions - Practice Answering Them!
Reading helps, but actual practice is what gets you hired. Our AI feedback system helps you improve your Hose Maker interview answers in real-time.
Personalized feedback
Unlimited practice
Used by hundreds of successful candidates
What machinery and equipment have you operated in the hose-making process, and what are their maintenance requirements?
How to Answer
- 1
List specific machines you have used, like extruders, crimpers, and testing equipment.
- 2
Explain your direct experience with these machines, including any unique tasks you've performed.
- 3
Mention routine maintenance tasks you handled, such as lubrication and inspections.
- 4
Discuss any troubleshooting or repairs you have experience with.
- 5
Include any relevant certifications or training related to machinery operation and maintenance.
Example Answers
I have operated extruders and crimpers in the hose-making process. I regularly performed maintenance tasks like lubrication and cleaning of the extruder, as well as calibrating the crimper every month to ensure precision.
What safety protocols do you follow while working with high-pressure hoses during production?
How to Answer
- 1
Always wear appropriate personal protective equipment (PPE) such as gloves and goggles.
- 2
Perform regular visual inspections on hoses for signs of wear or damage.
- 3
Ensure proper pressure ratings for hoses match the application requirements.
- 4
Follow lockout/tagout procedures when working on or near pressurized systems.
- 5
Maintain clear communication with team members about pressure levels and potential hazards.
Example Answers
I always wear my PPE, including gloves and goggles. I regularly inspect hoses for damage and ensure they're rated for the right pressures. I also follow lockout/tagout procedures when handling these hoses.
How do you troubleshoot defects in hoses during the manufacturing process?
How to Answer
- 1
Identify the specific defect and its characteristics
- 2
Analyze the manufacturing process for each stage of hose production
- 3
Use data from quality control checks to pinpoint when defects occur
- 4
Collaborate with the production team for insights and potential issues
- 5
Implement corrective actions and monitor results to prevent recurrence
Example Answers
To troubleshoot defects in hoses, I first identify the specific defect, like leaks or kinks. Then, I analyze each stage of production to find where it might have occurred. Using quality control data helps me narrow down the timeline of the defect. I work with the production team to understand potential causes and suggest corrective actions to fix the issue.
What quality control measures do you implement to ensure the hoses meet industry standards?
How to Answer
- 1
Identify the specific industry standards relevant to hose production
- 2
Implement regular testing for material durability and flexibility
- 3
Conduct visual inspections for defects during the production process
- 4
Maintain detailed records of quality tests and their results
- 5
Train staff on quality control practices to ensure compliance
Example Answers
I ensure hoses meet industry standards by conducting regular material tests for durability and flexibility, performing visual inspections for defects, and keeping detailed records of our quality assessments.
How do you ensure compliance with industry standards and regulations in hose manufacturing?
How to Answer
- 1
Stay updated on relevant industry standards and regulations.
- 2
Implement regular training sessions for employees on compliance practices.
- 3
Conduct internal audits to assess adherence to standards.
- 4
Utilize quality management systems to track compliance metrics.
- 5
Collaborate with regulatory bodies to ensure alignment with current regulations.
Example Answers
I regularly review industry standards and hold training sessions for the team to keep everyone informed about compliance requirements.
What considerations do you take into account when designing hoses for specific applications?
How to Answer
- 1
Identify the fluid type and temperature requirements for the application
- 2
Consider the pressure rating needed to ensure safety and performance
- 3
Evaluate the hose's flexibility and bend radius for its intended use
- 4
Choose the right materials for durability and compatibility with the environment
- 5
Assess the ease of installation and maintenance in the application context
Example Answers
When designing hoses, I first determine the type of fluid and its temperature range to select suitable materials. Then, I ensure the hose can handle the required pressure rating, while also considering its flexibility for ease of use in tight spaces.
What hose design software are you familiar with, and how have you used it in previous projects?
How to Answer
- 1
Identify specific hose design software you have experience with.
- 2
Explain how you used the software in practical situations.
- 3
Mention any successful outcomes from your projects using the software.
- 4
Be prepared to discuss any challenges faced and how you overcame them.
- 5
Link your software skills to the requirements of the Hose Maker position.
Example Answers
I am familiar with AutoCAD and SolidWorks for hose design. In my last project, I used AutoCAD to create precise 3D models of custom hoses, which improved production efficiency by 20%.
What methods do you utilize to conduct performance testing on hoses before they reach clients?
How to Answer
- 1
Describe specific testing techniques used, such as burst testing and kink testing.
- 2
Mention equipment and technology that helps in performance evaluation.
- 3
Include safety standards or regulations that guide your testing procedures.
- 4
Discuss how you document and analyze test results.
- 5
Emphasize collaboration with other teams for feedback and improvements.
Example Answers
I utilize burst testing to assess the maximum pressure the hose can handle, using digital pressure gauges for accuracy, and ensure all results meet industry safety standards.
Don't Just Read Hose Maker Questions - Practice Answering Them!
Reading helps, but actual practice is what gets you hired. Our AI feedback system helps you improve your Hose Maker interview answers in real-time.
Personalized feedback
Unlimited practice
Used by hundreds of successful candidates
What types of adhesives or sealants are commonly used in hose assembly, and how do you select the appropriate one?
How to Answer
- 1
Identify common adhesives such as silicone, polyurethane, and epoxy.
- 2
Consider the hose material and operating environment when selecting adhesives.
- 3
Evaluate performance metrics such as temperature resistance and flexibility.
- 4
Ensure compatibility with fluid types that the hose will encounter.
- 5
Refer to manufacturer specifications for recommended adhesives and guidelines.
Example Answers
In hose assembly, I commonly use silicone adhesives for high-temperature applications and polyurethane for flexibility. I always check the hose material and the fluids it will contact to choose the best adhesive.
Situational Interview Questions
If you discovered that a batch of hoses was produced with a defect, what steps would you take to address the issue?
How to Answer
- 1
Immediately halt production to prevent further defective hoses.
- 2
Notify your supervisor and quality control team about the defect.
- 3
Investigate the root cause of the defect through inspection and analysis.
- 4
Document the findings and the steps taken to resolve the issue.
- 5
Implement corrective actions and train staff to prevent future defects.
Example Answers
First, I would stop production to stop any more defective hoses from being made. Then, I would inform the supervisor and quality control immediately. We would analyze the defect to find out what caused it and document everything. After that, I would make sure to implement changes to prevent a repeat issue.
How would you handle a situation where two clients urgently needed hose orders completed at the same time?
How to Answer
- 1
Assess urgency and importance of each client's request
- 2
Communicate transparently with both clients about the situation
- 3
Prioritize tasks based on deadlines and client relationships
- 4
Consider involving team members to expedite the process
- 5
Provide updates to clients regularly until the situation is resolved
Example Answers
I would first evaluate which order is more urgent based on the deadline and impact on the client. Then, I’d communicate with both clients to explain the situation and set realistic expectations. If possible, I’d collaborate with my team to expedite one of the orders.
Don't Just Read Hose Maker Questions - Practice Answering Them!
Reading helps, but actual practice is what gets you hired. Our AI feedback system helps you improve your Hose Maker interview answers in real-time.
Personalized feedback
Unlimited practice
Used by hundreds of successful candidates
Imagine you are faced with a decrease in production efficiency. What strategies would you propose to improve it?
How to Answer
- 1
Analyze current production data to identify root causes.
- 2
Engage the team to gather input on inefficiencies.
- 3
Implement targeted training sessions for employees.
- 4
Optimize the layout and flow of the production line.
- 5
Monitor changes and adjust strategies as needed.
Example Answers
I would first analyze production data to pinpoint specific areas where efficiency has dropped. Next, I'd engage the team for their insights and suggestions, as they often identify issues directly. Based on our findings, I'd implement targeted training sessions to address skill gaps. Furthermore, I would look at the overall production line layout to optimize workflow and reduce bottlenecks. Lastly, I would continuously monitor the outcomes and make necessary adjustments.
A customer reports that the hoses they received do not meet specifications. How would you handle their complaint?
How to Answer
- 1
Listen carefully to the customer's complaint without interrupting
- 2
Apologize for the inconvenience and express understanding of their frustration
- 3
Ask specific questions to determine the details and nature of the problem
- 4
Review the specifications and the order details to verify discrepancies
- 5
Offer a solution, such as a replacement or refund, and follow up to ensure satisfaction
Example Answers
I would start by listening patiently to the customer's concerns. Then, I'd apologize for the hassle and ask specifics about how the hoses differ from their expectations. After confirming the details, I'd check our records and propose a replacement if needed, ensuring they feel supported throughout the process.
If you were tasked with improving the efficiency of the hose-making process, what changes would you consider?
How to Answer
- 1
Analyze the current workflow and identify bottlenecks
- 2
Implement lean manufacturing principles to reduce waste
- 3
Invest in automation for repetitive tasks to speed up production
- 4
Enhance training programs for workers to improve skill levels
- 5
Gather feedback from staff for practical improvement ideas
Example Answers
I would start by mapping out the current workflow to find bottlenecks. Then, I’d apply lean principles to minimize waste and consider automating repetitive tasks for faster production.
You are leading a team that is struggling to meet production targets. How would you motivate your team to boost performance?
How to Answer
- 1
Assess team members' strengths and weaknesses to delegate tasks effectively
- 2
Set clear, achievable goals and celebrate small wins to build momentum
- 3
Provide regular feedback and recognition to boost morale
- 4
Encourage open communication to identify issues and gather team input
- 5
Introduce incentives or rewards for improved productivity
Example Answers
I would first evaluate each team member's strengths to assign roles that play to their skills. Then, I'd set clear goals and celebrate even small achievements to enhance motivation.
How would you conduct a risk assessment for a new hose design before entering production?
How to Answer
- 1
Identify potential failure modes related to material, design, and usage.
- 2
Assess the likelihood and impact of each failure mode using a risk matrix.
- 3
Engage with stakeholders for input on risks, including manufacturing, quality, and safety teams.
- 4
Perform prototype testing to uncover unforeseen issues or design flaws.
- 5
Document all findings and develop a mitigation plan for high-risk areas.
Example Answers
I would start by identifying potential failure modes based on the materials and design. Then, I would use a risk matrix to evaluate their likelihood and impact, involving stakeholders for diverse insights. Finally, I would run prototypes and document everything to clarify our mitigation plans.
If there was a shortage of an essential raw material for hose production, how would you approach the situation?
How to Answer
- 1
Assess the extent of the shortage and its impact on production timelines
- 2
Identify alternative materials or suppliers to mitigate the shortage
- 3
Communicate transparently with stakeholders about potential delays
- 4
Prioritize urgent orders while strategizing long-term solutions
- 5
Collaborate with the procurement team to secure needed resources
Example Answers
I would first evaluate how the shortage affects our production schedule. Then, I would research alternative materials that could temporarily suffice and reach out to new suppliers. Keeping my team updated would be essential to manage expectations.
If you had to collaborate with an external supplier to improve hose materials, how would you approach the partnership?
How to Answer
- 1
Research the supplier’s capabilities and specialties in hose materials.
- 2
Establish clear goals and expectations for the partnership upfront.
- 3
Communicate openly and regularly to build trust and ensure alignment.
- 4
Involve both technical teams to share knowledge and insights.
- 5
Evaluate and iterate on prototypes collaboratively to optimize results.
Example Answers
I would start by researching the supplier to understand their strengths in materials. Then, I would set up a kickoff meeting to define our goals together. Regular check-ins would help maintain alignment, and I would ensure both teams contribute their expertise. Finally, we would test prototypes and refine designs based on feedback.
How would you create a culture of continuous improvement within a hose manufacturing team?
How to Answer
- 1
Encourage open communication for ideas and feedback.
- 2
Implement regular team meetings to discuss improvement suggestions.
- 3
Provide training sessions on best practices and new technologies.
- 4
Recognize and reward employees for innovative solutions.
- 5
Incorporate a suggestion box for anonymous feedback.
Example Answers
I would start by fostering an environment where team members feel comfortable sharing their ideas during regular meetings, ensuring everyone’s voice is heard.
Don't Just Read Hose Maker Questions - Practice Answering Them!
Reading helps, but actual practice is what gets you hired. Our AI feedback system helps you improve your Hose Maker interview answers in real-time.
Personalized feedback
Unlimited practice
Used by hundreds of successful candidates
Hose Maker Position Details
Salary Information
Average Salary
$37,184
Source: SalaryExpert
Related Positions
- Harnessmaker
- Cable Maker
- Sash Maker
- Plastic Maker
- Purse Maker
- Belt Buckle Maker
- Mat Maker
- Reed Maker
- Cushion Maker
- Filament Maker
Similar positions you might be interested in.
Ace Your Next Interview!
Practice with AI feedback & get hired faster
Personalized feedback
Used by hundreds of successful candidates
Ace Your Next Interview!
Practice with AI feedback & get hired faster
Personalized feedback
Used by hundreds of successful candidates