Top 33 Candle Cutter Interview Questions and Answers [Updated 2025]
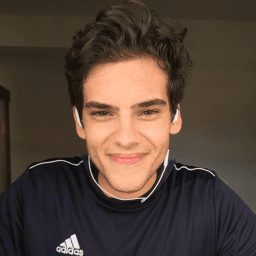
Andre Mendes
•
March 30, 2025
Are you preparing for a Candle Cutter job interview and want to stand out from the competition? Our latest blog post is here to help, featuring the most common and up-to-date interview questions for this specialized role. Dive in to discover insightful example answers and expert tips on responding effectively, ensuring you're well-prepared to impress your potential employers and secure that coveted position.
Download Candle Cutter Interview Questions in PDF
To make your preparation even more convenient, we've compiled all these top Candle Cutterinterview questions and answers into a handy PDF.
Click the button below to download the PDF and have easy access to these essential questions anytime, anywhere:
List of Candle Cutter Interview Questions
Technical Interview Questions
How do you manage different batches of candles to ensure consistent cutting results?
How to Answer
- 1
Identify the specific temperature and consistency of each wax batch before cutting
- 2
Use calibrated cutting tools to maintain uniformity across all batches
- 3
Document each batch's characteristics and results to track variations
- 4
Regularly clean and maintain equipment to prevent contamination of batches
- 5
Implement a standardized cutting process and train all team members effectively
Example Answers
To ensure consistent cutting results, I always check the temperature and consistency of the wax before cutting. I use calibrated tools to keep everything uniform and document each batch's details so I can refer back if issues arise.
What cutting techniques are you familiar with that are applicable to candle production?
How to Answer
- 1
Identify specific cutting techniques you have used in candle making
- 2
Mention tools or equipment you are skilled with, like wick cutters or knives
- 3
Explain the importance of precision in cutting for candle quality
- 4
Share any experience with unique designs or types of cuts
- 5
Be ready to discuss safety measures while cutting
Example Answers
I am well-versed in using wick cutters to ensure the wick is trimmed to the proper length, which is crucial for optimal burn quality.
Don't Just Read Candle Cutter Questions - Practice Answering Them!
Reading helps, but actual practice is what gets you hired. Our AI feedback system helps you improve your Candle Cutter interview answers in real-time.
Personalized feedback
Unlimited practice
Used by hundreds of successful candidates
What types of cutting tools and equipment have you previously used in candle cutting?
How to Answer
- 1
List specific tools you've used, such as knives or saws.
- 2
Mention any specialized equipment for candle cutting.
- 3
Describe how you used these tools in your work process.
- 4
Highlight your ability to maintain and handle tools safely.
- 5
Provide examples of situations where you effectively used these tools.
Example Answers
I have used utility knives and specialized candle saws to cut wax. I ensure that my tools are sharp and in good condition to achieve clean cuts.
How do you ensure safety while using cutting equipment in candle manufacturing?
How to Answer
- 1
Always wear appropriate safety gear such as gloves and goggles.
- 2
Regularly inspect cutting equipment for any damages or wear.
- 3
Follow proper procedures for setting up and using the equipment.
- 4
Keep the workspace clean and free of hazards like spilled wax.
- 5
Stay focused and avoid distractions when operating cutting tools.
Example Answers
I ensure safety by wearing gloves and goggles while using cutting tools. I also inspect the equipment before each use to ensure it is in good condition.
What do you know about different wax types and their implications for candle cutting?
How to Answer
- 1
Identify common wax types used in candle making: paraffin, soy, beeswax, palm.
- 2
Discuss the melting points of each wax type and how it affects cutting.
- 3
Explain how different waxes can affect the fragrance and burning characteristics.
- 4
Mention how the texture of wax impacts the cutting process and results.
- 5
Consider the sustainability implications of using various wax types.
Example Answers
I know that paraffin wax is the most common and has a low melting point, making it easier to cut but can have a shorter burn time. Soy wax is a great eco-friendly option that also trims nicely and holds scent well.
How do you perform quality checks on the cut candles to ensure they meet standards?
How to Answer
- 1
Inspect candle dimensions to ensure they match specifications
- 2
Check for uniformity in cut sizes to maintain consistency
- 3
Assess the cut edges for smoothness and clarity
- 4
Conduct burn tests to verify performance and safety standards
- 5
Document any defects and follow up with corrective actions
Example Answers
I start by measuring each candle's dimensions against our specifications to make sure they are accurate. Then, I visually inspect the cut edges for any roughness and ensure they are smooth. I also run burn tests on a sample of candles to ensure they burn evenly without issues. Any deviations are logged for further investigation.
What methods do you use to ensure precision in your candle cuts?
How to Answer
- 1
Use a quality cutting tool like a sharp knife or specialized cutter for clean edges
- 2
Measure candles accurately using a ruler or marked cutting guide for consistent lengths
- 3
Work slowly and steadily to avoid mistakes or uneven cuts
- 4
Regularly check your measurements as you cut to ensure accuracy
- 5
Practice on scrap pieces to develop your cutting skills before using the actual candles
Example Answers
I always use a sharp, high-quality knife and a ruler to measure the exact length I want for the candle cuts. By taking my time and double-checking the measurements before cutting, I ensure precision.
How does candle design impact the cutting process? Can you give examples?
How to Answer
- 1
Discuss how different shapes affect cutting techniques.
- 2
Mention how the type of wax influences cutting temperature.
- 3
Explain the importance of scent placement in cutting design.
- 4
Highlight how color layering can require precision in cutting.
- 5
Provide real examples of designs and their cutting challenges.
Example Answers
The design of a candle, such as a geometric shape, can require specific cutting tools to ensure clean edges. For instance, a hexagonal candle may need angled cuts that different from a simple cylindrical design.
What routine maintenance tasks do you consider important for cutting equipment?
How to Answer
- 1
Identify key maintenance tasks such as blade sharpening and cleaning.
- 2
Mention regular inspections for wear and tear.
- 3
Discuss the importance of lubricating moving parts.
- 4
Explain the need to keep equipment free from debris.
- 5
Highlight the schedule for routine maintenance checks.
Example Answers
I believe regular blade sharpening and cleaning are crucial to maintain cutting precision. Additionally, I check for wear signs and lubricate moving parts as needed.
How do you adjust your cutting techniques under varying temperature and humidity conditions?
How to Answer
- 1
Monitor environmental conditions regularly to assess temperature and humidity levels
- 2
Modify blade sharpness based on material response to heat and moisture
- 3
Adapt cutting speed; slower speeds can help in high humidity
- 4
Use proper storage for cutting materials to mitigate temperature effects
- 5
Stay informed about ideal conditions for different candle oils and waxes
Example Answers
In high humidity, I slow down my cutting speed to allow better control and avoid sticky situations. I also adjust blade sharpness as needed to maintain precision.
Don't Just Read Candle Cutter Questions - Practice Answering Them!
Reading helps, but actual practice is what gets you hired. Our AI feedback system helps you improve your Candle Cutter interview answers in real-time.
Personalized feedback
Unlimited practice
Used by hundreds of successful candidates
Describe your process for troubleshooting cutting errors in candle production.
How to Answer
- 1
Identify the type of cutting error and its cause.
- 2
Check the quality of the wax and ensure it is at the right temperature.
- 3
Inspect the cutting tools for dullness or misalignment.
- 4
Adjust the cutting machine settings if needed.
- 5
Document the errors and your corrective actions for future reference.
Example Answers
First, I assess the specific cutting error, whether it's uneven cuts or incomplete candles. Then, I examine the wax quality and temperature to ensure optimal cutting conditions. I also check the cutting tool for sharpness and proper alignment. If adjustments are needed, I modify the machine settings accordingly. Finally, I keep records of the issues and how I resolved them to improve future processes.
Behavioral Interview Questions
Describe a time when you worked as part of a team to improve the candle cutting process. What was your role?
How to Answer
- 1
Identify a specific project or situation where you collaborated with others.
- 2
Explain your role clearly and how it contributed to the team's success.
- 3
Highlight any challenges faced and how the team overcame them.
- 4
Discuss the impact of the improvements made on the process or product.
- 5
Use metrics or specific outcomes if possible to illustrate success.
Example Answers
In my last position, our team noticed that the candle cutting process was slow. I led a brainstorming session to identify bottlenecks. We implemented a new cutting tool and streamlined our workflow, which resulted in a 30% increase in production efficiency.
Tell me about a time when you faced a difficult challenge while cutting candles. How did you handle it?
How to Answer
- 1
Choose a specific challenge related to candle cutting.
- 2
Explain the context and what made it difficult.
- 3
Describe the steps you took to overcome the challenge.
- 4
Highlight any skills or techniques you applied.
- 5
Conclude with the outcome and what you learned.
Example Answers
One time, I had a batch of candles that were unevenly poured, making them hard to cut. I assessed the situation and decided to let them cool completely before attempting to cut. I then used a heated knife to make cleaner cuts, which worked effectively, and the candles turned out well. This experience taught me the importance of patience and proper tools.
Don't Just Read Candle Cutter Questions - Practice Answering Them!
Reading helps, but actual practice is what gets you hired. Our AI feedback system helps you improve your Candle Cutter interview answers in real-time.
Personalized feedback
Unlimited practice
Used by hundreds of successful candidates
Can you provide an example of a situation where your attention to detail helped prevent a quality issue with the candles?
How to Answer
- 1
Think of a specific incident related to candle making.
- 2
Describe the process where attention to detail was crucial.
- 3
Focus on how your careful review or checks made a difference.
- 4
Mention any tools or methods you used to ensure quality.
- 5
Highlight the outcome that demonstrated the importance of your actions.
Example Answers
In my last position, I noticed that a batch of wax was slightly off in temperature. I took the time to verify the thermometer calibration and discovered it was faulty. By adjusting the temperature correctly, we avoided poor burn quality in the finished candles.
Discuss an experience where you had to adapt to changes in production requirements or procedures.
How to Answer
- 1
Identify a specific situation in your past experience.
- 2
Explain the initial procedure or requirement and the change that occurred.
- 3
Describe how you adapted your approach to meet the new requirements.
- 4
Mention any positive outcomes that resulted from your adaptation.
- 5
Keep it concise and focus on your problem-solving skills.
Example Answers
In my last role, we faced a sudden increase in demand for a particular candle line. The production team had to adjust our workflow on short notice. I quickly assessed our resources, suggested re-prioritizing tasks, and coordinated with team members to ensure everyone was focused on the high-demand products. As a result, we met the demand without compromising quality.
Give an example of how you communicated effectively with your team to enhance candle cutting efficiency.
How to Answer
- 1
Identify a specific situation where communication was key.
- 2
Explain the method of communication used, such as meetings or group chats.
- 3
Describe the feedback loop established for continuous improvement.
- 4
Include measurable outcomes to demonstrate efficiency gains.
- 5
Highlight teamwork and collaboration in your approach.
Example Answers
In a team meeting, I proposed a new cutting schedule based on our peak hours. We used a shared calendar to coordinate shifts and communicated via group chat for real-time updates. This led to a 20% increase in our monthly output.
Describe a situation where your work ethic positively impacted the candle production process.
How to Answer
- 1
Think of a specific time when you went above and beyond in your duties.
- 2
Describe how your actions improved efficiency or quality in production.
- 3
Use quantifiable results to demonstrate the impact of your work ethic.
- 4
Mention teamwork if applicable, showing how you inspired others.
- 5
Stay positive and focus on solutions you provided.
Example Answers
In my last role, I stayed late to ensure every candle batch was tested before shipping. This dedication led to a 20% reduction in customer complaints over two months, improving our reputation.
Can you describe a time you received constructive criticism about your cutting technique? How did you respond?
How to Answer
- 1
Choose a specific situation that highlights a challenge in your cutting technique.
- 2
Explain the feedback you received and who it came from.
- 3
Describe the steps you took to address the feedback and improve your technique.
- 4
Emphasize the positive outcome and what you learned from the experience.
- 5
Reflect on how this experience influenced your approach to receiving feedback.
Example Answers
In a recent project, my supervisor noted that my cutting angles were inconsistent, which affected the final product. I listened carefully and asked for specific examples. I then practiced those techniques and sought feedback on my improvements. As a result, my cutting precision improved significantly, and I received praise for my attention to detail.
Provide an example when you took the initiative to improve candle production.
How to Answer
- 1
Choose a specific project or change you implemented.
- 2
Explain the problem you identified in candle production.
- 3
Describe the solution you proposed or executed.
- 4
Highlight the results and improvements after your actions.
- 5
Keep your answer focused on your role and impact.
Example Answers
At my last job, I noticed that the wick placement was inconsistent, causing uneven burning. I researched different wick placement techniques and proposed a standardized template. After implementing it, we saw a 20% decrease in customer complaints about burn quality.
How do you handle the stress of working in a fast-paced production environment?
How to Answer
- 1
Prioritize tasks and focus on one task at a time
- 2
Practice deep breathing techniques to stay calm
- 3
Communicate effectively with your team to avoid confusion
- 4
Take short breaks to recharge and regain focus
- 5
Stay organized with checklists or notes to track progress
Example Answers
I handle stress by prioritizing my tasks and focusing on one job at a time. I also take deep breaths during busy moments to stay calm and centered.
Don't Just Read Candle Cutter Questions - Practice Answering Them!
Reading helps, but actual practice is what gets you hired. Our AI feedback system helps you improve your Candle Cutter interview answers in real-time.
Personalized feedback
Unlimited practice
Used by hundreds of successful candidates
What are your long-term goals as a candle cutter, and how do they align with the company’s mission?
How to Answer
- 1
Reflect on personal growth in candle making skills over the next few years.
- 2
Consider how your professional goals can contribute to the company’s vision.
- 3
Mention specific techniques or innovations you wish to explore.
- 4
Express a desire to educate others about candle making within the company.
- 5
Align your goals with sustainability practices if the company values them.
Example Answers
My long-term goal as a candle cutter is to master advanced techniques in fragrance blending, which aligns with the company’s mission to provide unique and high-quality products. I aim to develop new candle lines that reflect sustainability and craftsmanship.
Situational Interview Questions
If you notice that the candles are being cut unevenly, what steps would you take to resolve the problem?
How to Answer
- 1
Inspect the cutting equipment for any malfunctions or misalignments
- 2
Check if the candle placement is consistent before cutting
- 3
Adjust the cutting thickness settings if needed
- 4
Run a test batch after making adjustments to ensure uniformity
- 5
Document the issue and resolution process for future reference
Example Answers
First, I would inspect the cutting equipment for any misalignments. Then, I would ensure that the candles are placed consistently before cutting. After making necessary adjustments, I would run a test batch to confirm they are cut evenly.
What would you do if the cutting machine breaks down during a production run?
How to Answer
- 1
Stay calm and assess the situation quickly.
- 2
Notify your supervisor or team leader immediately.
- 3
Follow the established troubleshooting steps for the machine.
- 4
Check for any easy fixes, like power issues or jams.
- 5
Prepare to switch to a backup plan or machine if needed.
Example Answers
If the cutting machine breaks down, I would first remain calm and assess the problem. I would then notify my supervisor and follow the troubleshooting steps to identify the issue, checking for any blockages or power issues. If it's minor, I would fix it; if not, I would prepare to switch to a spare cutter until repairs are done.
Don't Just Read Candle Cutter Questions - Practice Answering Them!
Reading helps, but actual practice is what gets you hired. Our AI feedback system helps you improve your Candle Cutter interview answers in real-time.
Personalized feedback
Unlimited practice
Used by hundreds of successful candidates
How would you handle a situation where a team member disagrees with your cutting technique?
How to Answer
- 1
Listen carefully to their perspective to understand their concerns
- 2
Ask questions to clarify their thoughts and rationale
- 3
Discuss the benefits and drawbacks of both techniques
- 4
Be open to constructive criticism and willing to adjust if necessary
- 5
Aim for a collaborative solution that benefits the team and the quality of work
Example Answers
I would first listen to my team member's concerns about my cutting technique. I would ask them to explain their reasoning and suggest their approach. After discussing both techniques, if their method shows clear benefits, I would be open to adapting it to improve our workflow.
If you are faced with a rush order for candles, how would you prioritize your cutting tasks?
How to Answer
- 1
Assess the total quantity and types of candles needed.
- 2
Identify the deadline for the rush order.
- 3
Prioritize tasks based on the size and complexity of the cuts.
- 4
Communicate with the team to delegate tasks efficiently.
- 5
Focus first on the highest priority cuts that affect order completion.
Example Answers
I would first check the specifications of the rush order to understand the types and quantities needed. Then, I'd prioritize cutting the larger, more complex candles first, as they take more time. I'd also communicate with my team to possibly assign simpler tasks to them, ensuring we meet the deadline efficiently.
Imagine a new cutting procedure has been implemented. How would you go about learning and applying it?
How to Answer
- 1
Ask for the procedure's documentation and any training materials available.
- 2
Observe a demonstration of the new procedure from an experienced cutter.
- 3
Practice the new cutting technique under supervision to gain hands-on experience.
- 4
Take notes during practice sessions to capture important steps and tips.
- 5
Seek feedback after applying the procedure to improve and refine your skills.
Example Answers
First, I would ask for any documentation or training materials about the new cutting procedure. Then, I'd observe an experienced cutter perform it to understand the technique. After that, I'd practice under their supervision and take notes to help me remember the important steps. Lastly, I'd ask for feedback to improve my application of the new method.
If you are behind schedule with candle cutting, what strategies would you implement to catch up?
How to Answer
- 1
Assess the current workflow to identify bottlenecks
- 2
Prioritize tasks based on urgency and output impact
- 3
Increase workforce temporarily for higher output
- 4
Optimize cutting techniques to improve speed
- 5
Communicate with the team about adjustments and priorities
Example Answers
To catch up on the schedule, I would first assess the workflow and identify where the delays are occurring. Then, I would prioritize cutting tasks that need immediate attention and possibly bring in extra hands to boost productivity. I would also look into adjusting our cutting techniques to ensure we're working as efficiently as possible.
How would you train a new employee in effective cutting techniques?
How to Answer
- 1
Start with a demonstration of the correct cutting technique, explaining each step.
- 2
Provide hands-on practice with supervision, allowing the new employee to try different cuts.
- 3
Introduce key safety measures and explain why they are important for effective cutting.
- 4
Encourage questions throughout the training process to ensure understanding.
- 5
Give feedback after practice sessions, highlighting strengths and areas for improvement.
Example Answers
I would begin by demonstrating the correct cutting technique, focusing on grip and angle. Then, I would allow the new employee to practice under my supervision, ensuring they understand safety protocols as we go.
What would you do if you encountered a technical challenge that affects the cutting quality of the candles?
How to Answer
- 1
Identify the specific issue with the cutting quality.
- 2
Evaluate the potential causes of the problem.
- 3
Test adjustments to the cutting parameters or equipment.
- 4
Consult manuals or technical resources for solutions.
- 5
Communicate with the team if assistance is needed.
Example Answers
If I notice that the cutting quality is off, I would first identify whether it's due to the blade dullness or the speed settings. Then, I would make small adjustments and test the results to see if the quality improves.
If you have a limited amount of materials for candle cutting, how would you decide on allocations?
How to Answer
- 1
Assess the demand for different candle styles and sizes.
- 2
Prioritize materials for the most popular or best-selling designs.
- 3
Consider the production efficiency and time required for each design.
- 4
Allocate materials based on customer feedback and trends.
- 5
Monitor usage and adjust allocations for future production runs.
Example Answers
To decide on allocations, I would first analyze the sales data to identify our most popular candle designs. Then, I would prioritize those designs, ensuring we have enough materials for them. I would also take into account how quickly we can produce each design to maximize output with the limited materials.
How would you monitor your cutting progress to ensure you meet production goals?
How to Answer
- 1
Set clear daily cutting targets based on production goals
- 2
Use a checklist to track each batch for accuracy
- 3
Regularly measure cut dimensions to ensure quality control
- 4
Log any discrepancies and adjust cutting techniques immediately
- 5
Communicate progress with the team during shift meetings
Example Answers
I would set clear daily targets for how many candles need to be cut. By using a checklist, I can track each batch and ensure I meet my cutting goals without compromising quality.
Don't Just Read Candle Cutter Questions - Practice Answering Them!
Reading helps, but actual practice is what gets you hired. Our AI feedback system helps you improve your Candle Cutter interview answers in real-time.
Personalized feedback
Unlimited practice
Used by hundreds of successful candidates
How would you motivate a team facing low morale due to repetitive cutting tasks?
How to Answer
- 1
Recognize and acknowledge the team's efforts regularly
- 2
Incorporate small rewards or incentives for achieving goals
- 3
Encourage team-building activities during breaks
- 4
Introduce variations in tasks to keep things interesting
- 5
Provide opportunities for skill development or training
Example Answers
I would recognize the team's efforts regularly to show appreciation for their hard work. This could be as simple as a shout-out during meetings or small rewards for hitting targets.
Candle Cutter Position Details
Related Positions
- Candle Maker
- Candle Wicker
- Chalk Cutter
- Panel Cutter
- Jamb Cutter
- Fruit Cutter
- Cherry Cutter
- Neck Cutter
- Wax Pourer
- Saw Setter
Similar positions you might be interested in.
Ace Your Next Interview!
Practice with AI feedback & get hired faster
Personalized feedback
Used by hundreds of successful candidates
Ace Your Next Interview!
Practice with AI feedback & get hired faster
Personalized feedback
Used by hundreds of successful candidates