Top 28 Wax Pourer Interview Questions and Answers [Updated 2025]
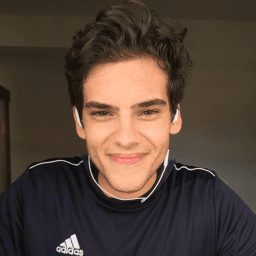
Andre Mendes
•
March 30, 2025
Preparing for a wax pourer interview can be daunting, but we're here to help you shine with confidence. In this post, we've compiled the most common interview questions for the wax pourer role, complete with example answers and tips on how to respond effectively. Whether you're a seasoned professional or new to the industry, this guide will equip you with the insights needed to succeed.
Download Wax Pourer Interview Questions in PDF
To make your preparation even more convenient, we've compiled all these top Wax Pourerinterview questions and answers into a handy PDF.
Click the button below to download the PDF and have easy access to these essential questions anytime, anywhere: