Top 31 Car Filler Interview Questions and Answers [Updated 2025]
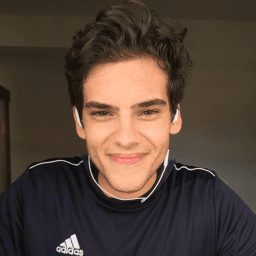
Andre Mendes
•
March 30, 2025
Are you gearing up for a Car Filler interview and want to make a standout impression? This blog post is your ultimate guide, featuring the most common interview questions for the Car Filler role. Dive into example answers and expert tips on how to respond effectively, ensuring you're well-prepared to demonstrate your skills and land the job. Get ready to boost your confidence and ace that interview!
Download Car Filler Interview Questions in PDF
To make your preparation even more convenient, we've compiled all these top Car Fillerinterview questions and answers into a handy PDF.
Click the button below to download the PDF and have easy access to these essential questions anytime, anywhere:
List of Car Filler Interview Questions
Behavioral Interview Questions
Have you ever had to lead a team in filling operations? What was the outcome?
How to Answer
- 1
Describe a specific situation where you led a team.
- 2
Highlight your role and responsibilities during the operation.
- 3
Discuss the challenges faced and how you addressed them.
- 4
Share measurable outcomes or improvements achieved.
- 5
Mention any feedback from team members or supervisors.
Example Answers
In my last job, I led a team of 5 during a peak filling operation. We faced delays due to equipment malfunction, but I organized a quick repair strategy and reallocated tasks. As a result, we completed the operation 20% faster than the previous month and received positive feedback from my manager for effective team coordination.
Can you describe a time when you had to work closely with a team to complete a car filling task?
How to Answer
- 1
Choose a specific project where teamwork was essential.
- 2
Highlight your role and contributions to the team.
- 3
Explain the challenges faced and how you overcame them.
- 4
Mention the outcome and what you learned from the experience.
- 5
Keep your answer focused on teamwork and collaboration.
Example Answers
In my previous job at XYZ Auto, we worked on a large order that required a quick filling of several cars. I coordinated with my teammates to set up an efficient filling schedule and ensured everyone knew their roles. We faced issues with equipment malfunction, but I suggested we rotate tasks, which helped us stay on track. We completed the order on time and I learned the importance of adaptability in teamwork.
Don't Just Read Car Filler Questions - Practice Answering Them!
Reading helps, but actual practice is what gets you hired. Our AI feedback system helps you improve your Car Filler interview answers in real-time.
Personalized feedback
Unlimited practice
Used by hundreds of successful candidates
Tell me about a challenging situation in the filling process you encountered and how you resolved it.
How to Answer
- 1
Choose a specific situation that illustrates a challenge.
- 2
Explain the context clearly to give background to the problem.
- 3
Describe the steps you took to resolve the issue.
- 4
Highlight what you learned from the experience.
- 5
Keep it concise and focused on your contribution.
Example Answers
During my previous job, we had a pump malfunction during a major filling operation. I quickly assessed the situation, notified my supervisor, and switched to a backup pump while the team resolved the issue. This minimized downtime and taught me the importance of having contingency plans.
Give an example of a time when your attention to detail made a difference in the quality of your work.
How to Answer
- 1
Think of a specific project where your attention to detail was crucial.
- 2
Describe the task and the potential risks of not paying attention to detail.
- 3
Explain the steps you took to ensure everything was correct.
- 4
Share the positive outcome resulting from your careful work.
- 5
Keep it concise and relevant to the role.
Example Answers
In my last job as a car filler, I noticed the paint had slight inconsistencies in color. I double-checked the paint mixing ratios and adjusted them until they matched perfectly. This attention to detail ensured that the final car finished seamlessly, preventing customer complaints about mismatched paint and enhancing our reputation.
Describe a situation where you had to quickly adapt to changes in filling procedures. How did you handle it?
How to Answer
- 1
Think of a specific change you experienced in your previous jobs.
- 2
Outline the impact that change had on your work environment.
- 3
Describe your immediate response to the change.
- 4
Highlight any specific actions you took to adapt quickly.
- 5
Mention the outcome and what you learned from the experience.
Example Answers
In my previous job at the warehouse, we suddenly switched to a new filling system due to malfunctioning equipment. I quickly learned the new system by reviewing the manual and asking a colleague for tips. I adapted by practicing on the new machines using test materials before we started actual production, which helped minimize errors. As a result, we were able to continue our operations smoothly without major delays.
How have you ensured effective communication with your team during busy filling operations?
How to Answer
- 1
Use clear and concise language when giving instructions
- 2
Establish a system for quick updates, like hand signals or short radio messages
- 3
Hold brief team huddles before shifts to discuss the plan
- 4
Be open to feedback and encourage team members to share concerns
- 5
Assign roles clearly to avoid confusion during busy periods
Example Answers
During busy filling operations, I always make sure to use clear and concise language for instructions, and I utilize hand signals for quick communication. This helps reduce misunderstandings.
Can you give an example of when you took the initiative to improve a filling process?
How to Answer
- 1
Think of a specific scenario where you identified an issue in the filling process.
- 2
Explain the steps you took to address the problem, including any tools or methods used.
- 3
Highlight the positive outcome of your initiative, such as increased efficiency or reduced waste.
- 4
Use metrics or data if possible to quantify the improvement.
- 5
Keep your answer focused and relevant to the position.
Example Answers
At my previous job, I noticed that our filling line often ran slowly due to frequent clogging. I researched and implemented a new cleaning schedule and introduced a different nozzle design. As a result, we reduced downtime by 30% and improved our overall productivity.
What motivates you to maintain high standards in your work as a car filler?
How to Answer
- 1
Connect personal pride to quality workmanship
- 2
Relate high standards to customer satisfaction
- 3
Mention safety and reliability of the vehicle
- 4
Discuss teamwork and contributing to overall success
- 5
Reflect on personal growth and skill development
Example Answers
I take pride in my work and believe that maintaining high standards ensures I deliver a quality product that customers can trust.
How do you handle feedback about your work from supervisors or peers?
How to Answer
- 1
Listen actively and take notes if necessary
- 2
Acknowledge the feedback without being defensive
- 3
Ask clarifying questions to fully understand any points
- 4
Reflect on the feedback and identify any action steps
- 5
Follow up after addressing the feedback to show improvement
Example Answers
I always listen carefully to feedback and make sure to take notes. I appreciate constructive feedback and I ask questions if anything is unclear. After that, I reflect on it and implement the changes where needed.
Don't Just Read Car Filler Questions - Practice Answering Them!
Reading helps, but actual practice is what gets you hired. Our AI feedback system helps you improve your Car Filler interview answers in real-time.
Personalized feedback
Unlimited practice
Used by hundreds of successful candidates
Describe a time when you learned a new filling technique. What impact did it have on your work?
How to Answer
- 1
Choose a specific filling technique you learned.
- 2
Explain how you learned the technique, including any challenges.
- 3
Discuss the impact on your efficiency or quality of work.
- 4
Include any positive feedback you received after implementing the new technique.
- 5
Mention how this learning experience influenced your approach to filling tasks.
Example Answers
I learned a new layering technique for filling bodywork. I watched a tutorial online and then practiced it on a few test panels. This technique improved my finish and reduced my sanding time by 30%. My supervisor praised the smoother finishes I achieved, leading to fewer corrections needed.
Technical Interview Questions
What filling techniques are you familiar with, and which do you think are the most effective?
How to Answer
- 1
List specific filling techniques you have experience with.
- 2
Explain how each technique works briefly.
- 3
Evaluate which techniques are most effective and why.
- 4
Use examples from past work to illustrate points.
- 5
Be honest about your experience level with each technique.
Example Answers
I am familiar with techniques like hot filling, cold filling, and pressure filling. Hot filling is effective because it extends shelf life, while cold filling preserves flavor. In my last job, I primarily used hot filling for sauces, achieving a 95% fill rate without contamination.
What safety protocols do you consider most important while performing your duties as a car filler?
How to Answer
- 1
Discuss personal protective equipment usage like gloves and goggles.
- 2
Mention proper handling and storage of fuel to prevent spills.
- 3
Emphasize the importance of emergency procedures for spills or accidents.
- 4
Highlight the need for clear communication with team members.
- 5
Note regular training and awareness of safety regulations.
Example Answers
I believe that using personal protective equipment like gloves and goggles is crucial to avoid exposure to harmful substances. Also, I ensure proper handling of fuel by adhering to storage guidelines to prevent any spills.
Don't Just Read Car Filler Questions - Practice Answering Them!
Reading helps, but actual practice is what gets you hired. Our AI feedback system helps you improve your Car Filler interview answers in real-time.
Personalized feedback
Unlimited practice
Used by hundreds of successful candidates
What types of filling equipment have you worked with, and what maintenance practices do you follow?
How to Answer
- 1
List specific types of filling equipment you have experience with.
- 2
Explain your role in operating or maintaining that equipment.
- 3
Mention any standard maintenance practices you follow regularly.
- 4
Include any relevant safety protocols you adhere to.
- 5
Highlight any improvements or optimizations you contributed to.
Example Answers
I have worked with piston fillers and gravity fillers. I routinely perform daily inspections and clean the equipment to ensure it operates efficiently. I also adhere to safety protocols and document any maintenance performed.
Can you explain the proper method for handling hazardous materials during the filling process?
How to Answer
- 1
Always wear appropriate personal protective equipment (PPE) such as gloves and goggles.
- 2
Confirm safety data sheets (SDS) are accessible and reviewed before starting.
- 3
Ensure proper ventilation in the filling area to avoid inhalation of fumes.
- 4
Use designated equipment for transferring hazardous materials to prevent spills.
- 5
Have emergency procedures in place for accidental exposure or spills.
Example Answers
When handling hazardous materials, I first make sure to wear the necessary PPE like gloves and goggles. I then ensure the safety data sheets are easily accessible and have been reviewed. Proper ventilation is crucial, so I confirm that the area is well-ventilated. I also only use designated equipment to avoid spills, and I'm always prepared with emergency procedures just in case.
What quality control measures do you implement to ensure that the filling is done correctly?
How to Answer
- 1
Explain the importance of following standard operating procedures.
- 2
Mention the use of measuring equipment for accuracy.
- 3
Discuss performing regular checks on filler equipment calibration.
- 4
Highlight the role of visual inspections during the filling process.
- 5
Provide examples of troubleshooting steps for discrepancies.
Example Answers
I ensure accuracy by strictly following the standard operating procedures for filling. I regularly check the calibration of our measuring equipment and conduct visual inspections every hour to catch any discrepancies early.
What industry regulations are critical for the role of a car filler?
How to Answer
- 1
Understand local environmental regulations regarding waste disposal and emissions.
- 2
Familiarize yourself with health and safety regulations related to working with chemicals and materials.
- 3
Learn about quality control standards in the automotive industry to ensure compliance during filling operations.
- 4
Stay updated on industry best practices for handling automotive paint and fillers.
- 5
Be aware of any specific manufacturer guidelines for products being used in filling processes.
Example Answers
In my role as a car filler, I ensure compliance with local environmental regulations by properly disposing of waste materials and managing emissions. I also follow safety protocols for handling chemicals according to OSHA standards.
Describe your approach to troubleshooting filling machinery issues.
How to Answer
- 1
Start by observing the machine to identify any visible issues.
- 2
Check for error codes or alerts on the control panel.
- 3
Verify that the machinery is properly maintained and calibrated.
- 4
Test the machine with a small batch to replicate the issue.
- 5
Document the troubleshooting steps and solutions for future reference.
Example Answers
I first observe the filling machine to look for any obvious issues, such as leaks or misalignment. Then, I check the control panel for any error codes. If needed, I ensure that regular maintenance has been performed. I run a small test batch to see if the issue persists, and I carefully document all my findings.
What filling standards do you believe should be met for quality assurance?
How to Answer
- 1
Define key filling standards like consistency, weight accuracy, and proper sealing.
- 2
Discuss the importance of hygiene and cleanliness during the filling process.
- 3
Mention the role of regular equipment calibration and maintenance.
- 4
Emphasize the need for training and certification for operators.
- 5
Highlight the importance of documentation and traceability for quality control.
Example Answers
I believe key filling standards should ensure consistency in product volume, precise weight for each container, and secure seals to prevent leakage. Maintaining hygiene during the process is also crucial to avoid contamination.
What practices do you follow to minimize environmental impact during car filling?
How to Answer
- 1
Use organic materials for car filling where possible
- 2
Dispose of waste materials in an environmentally friendly manner
- 3
Implement recycling practices for used filler and related materials
- 4
Minimize material waste by measuring accurately
- 5
Use less toxic fillers that have a lower environmental impact
Example Answers
I prioritize using environmentally friendly materials like organic fillers and ensure that any waste is disposed of responsibly by recycling whenever possible.
What are the testing procedures you follow to ensure proper filling before delivery?
How to Answer
- 1
Describe specific filling tests you conduct.
- 2
Mention the tools or equipment used in the testing process.
- 3
Explain how you check for consistency and quality.
- 4
Include any safety checks you perform.
- 5
Emphasize the importance of documentation and communication.
Example Answers
I conduct a series of tests to ensure proper filling, including checking fill levels with calibrated gauges and assessing product consistency visually. I use automated systems to verify that each product meets specifications, and I document all results for quality assurance.
Don't Just Read Car Filler Questions - Practice Answering Them!
Reading helps, but actual practice is what gets you hired. Our AI feedback system helps you improve your Car Filler interview answers in real-time.
Personalized feedback
Unlimited practice
Used by hundreds of successful candidates
How do you manage the supplies and materials needed for the filling process?
How to Answer
- 1
Keep an inventory list of all supplies and materials needed.
- 2
Regularly check stock levels to avoid shortages or overstock.
- 3
Establish relationships with reliable suppliers for timely delivery.
- 4
Implement a first-in, first-out system to ensure materials are used effectively.
- 5
Document and analyze usage patterns to optimize ordering.
Example Answers
I maintain a detailed inventory list and check stock levels weekly to ensure we never run out of supplies. I also have established contacts with multiple suppliers for quick reordering.
Situational Interview Questions
Imagine you notice a colleague using an incorrect filling method. How would you address this situation?
How to Answer
- 1
Observe the situation carefully and ensure you fully understand the error.
- 2
Approach your colleague privately to discuss your observations.
- 3
Provide constructive feedback and explain why the correct method is important.
- 4
Offer to help them practice the correct technique if needed.
- 5
Encourage an open dialogue to promote a culture of learning.
Example Answers
I would first watch closely to make sure I understand the mistake. Then, I would find a quiet moment to speak with my colleague and point out the error respectfully. I’d explain the correct method and why it is important for safety and quality, and offer assistance if they want to practice.
If a safety hazard is identified while filling cars, what steps would you take immediately?
How to Answer
- 1
Stop the filling operation immediately to prevent further risk.
- 2
Assess the nature and severity of the hazard calmly.
- 3
Alert your supervisor or safety officer about the situation.
- 4
Ensure that the area is secure and other workers are notified.
- 5
Follow established safety protocols for addressing the identified hazard.
Example Answers
First, I would stop the filling process right away to prevent any accidents. Then, I would assess what the hazard is and inform my supervisor immediately while ensuring others are kept away from the area.
Don't Just Read Car Filler Questions - Practice Answering Them!
Reading helps, but actual practice is what gets you hired. Our AI feedback system helps you improve your Car Filler interview answers in real-time.
Personalized feedback
Unlimited practice
Used by hundreds of successful candidates
You have multiple cars that need filling by the end of your shift. How would you prioritize your tasks?
How to Answer
- 1
Assess the current fuel levels of each car quickly.
- 2
Identify any cars that are close to empty or have urgent fuel needs.
- 3
Consider the type of cars and their usage during your shift.
- 4
Plan your route efficiently to minimize travel time between cars.
- 5
Stay organized and communicate with your team if necessary.
Example Answers
First, I would check the fuel levels of all cars and fill the ones that are nearly empty first. Then, I would fill the remaining cars based on their usage priority, ensuring I use my time effectively to make the process quick.
How would you respond if your filling team was falling behind schedule during a peak time?
How to Answer
- 1
Assess the situation quickly to identify bottlenecks
- 2
Communicate with the team to understand challenges
- 3
Prioritize tasks and redistribute responsibilities if necessary
- 4
Keep the team motivated and focused on the goal
- 5
Consider implementing temporary fixes to increase efficiency
Example Answers
I would first assess what is causing the delay and communicate with my team to gather their insights. Then, I would prioritize the most critical tasks and see if I can redistribute some responsibilities to those who are less busy.
If you encounter a malfunction in the filling equipment, what would be your first course of action?
How to Answer
- 1
Stay calm and assess the situation quickly
- 2
Check the equipment display for error messages
- 3
Isolate the equipment to ensure safety
- 4
Consult the operation manual for troubleshooting steps
- 5
Report the issue to your supervisor if necessary
Example Answers
I would first remain calm and assess what the problem is. I would check the display for any error messages and isolate the equipment for safety. Then, I would refer to the operation manual for troubleshooting steps before alerting my supervisor.
What would you do if a customer complained about filling discrepancies after service?
How to Answer
- 1
Listen carefully to the customer's complaint without interrupting.
- 2
Apologize sincerely for the inconvenience caused.
- 3
Gather all relevant information from the customer regarding the discrepancy.
- 4
Investigate the issue by checking the service records and refill amounts.
- 5
Offer a resolution, such as a refund or a complimentary service, if needed.
Example Answers
I would listen to the customer and apologize for their experience. Then I would ask for details about the discrepancy and review our records. After determining the issue, I would offer a resolution that suits the customer.
If your team is not cooperating, how would you improve team dynamics without causing conflict?
How to Answer
- 1
Identify the root cause of the lack of cooperation.
- 2
Facilitate open communication to express concerns and ideas.
- 3
Encourage collaboration through team-building activities.
- 4
Recognize and celebrate small wins to boost morale.
- 5
Get input from team members on how to improve dynamics.
Example Answers
I would first try to understand why the team is not cooperating by talking to team members individually. Then, I would organize a meeting where everyone can share their thoughts in a safe environment, promoting open communication. To foster teamwork, I might suggest a team-building exercise. Recognizing our small successes can also bring us closer together and keep spirits high.
If you have to choose between speed and quality in your filling work, how would you make your decision?
How to Answer
- 1
Assess the specific requirements of the task at hand.
- 2
Prioritize quality if the product is sensitive or impacts safety.
- 3
Consider deadlines and client expectations when deciding.
- 4
Balance speed and quality by optimizing your workflow.
- 5
Communicate with your team about which is more important in specific situations.
Example Answers
In most cases, I would prioritize quality, especially if the filling could affect the product's performance. However, if there’s a tight deadline, I might consult with my supervisor to find a balance.
How would you cope if required to work under pressure during a busy filling session?
How to Answer
- 1
Stay calm and take deep breaths to manage stress.
- 2
Prioritize tasks by focusing on the most important filling stations first.
- 3
Communicate with your team to ensure everyone stays on the same page.
- 4
Use checklists to ensure all tasks are completed efficiently.
- 5
Take short breaks if possible to recharge your focus.
Example Answers
I would stay calm and take a few deep breaths to manage my stress. Then, I would prioritize my tasks, focusing on the busiest filling stations first, and communicate with my team to keep everyone updated.
Car Filler Position Details
Related Positions
Similar positions you might be interested in.
Ace Your Next Interview!
Practice with AI feedback & get hired faster
Personalized feedback
Used by hundreds of successful candidates
Ace Your Next Interview!
Practice with AI feedback & get hired faster
Personalized feedback
Used by hundreds of successful candidates