Top 29 Clamper Interview Questions and Answers [Updated 2025]
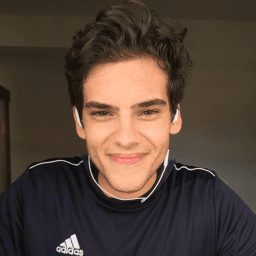
Andre Mendes
•
March 30, 2025
Preparing for a Clamper interview can be daunting, but fear not! This blog post compiles the most common interview questions for the Clamper role, offering not just questions but also example answers and insightful tips on how to respond effectively. Whether you're a seasoned professional or new to the field, this guide is designed to boost your confidence and help you stand out in your interview.
Download Clamper Interview Questions in PDF
To make your preparation even more convenient, we've compiled all these top Clamperinterview questions and answers into a handy PDF.
Click the button below to download the PDF and have easy access to these essential questions anytime, anywhere:
List of Clamper Interview Questions
Behavioral Interview Questions
Can you describe a time when you had to troubleshoot a malfunctioning clamper? What steps did you take to resolve the issue?
How to Answer
- 1
Identify the specific malfunction you encountered.
- 2
Explain your initial assessment and the tools you used.
- 3
Detail the troubleshooting steps you took to diagnose the problem.
- 4
Describe how you implemented the solution and any adjustments made.
- 5
Conclude with the outcome and what you learned from the experience.
Example Answers
In a previous role, I faced a clamper that wasn't securing properly. I first checked the hydraulic pressure and found it was low. After refilling the fluid, I tested the clamps again but noticed one was still jammed. I disassembled it, cleared out debris, and reassembled it. The clamper worked perfectly afterward, improving our efficiency by 15%.
Don't Just Read Clamper Questions - Practice Answering Them!
Reading helps, but actual practice is what gets you hired. Our AI feedback system helps you improve your Clamper interview answers in real-time.
Personalized feedback
Unlimited practice
Used by hundreds of successful candidates
Describe a situation in which you had a disagreement with a coworker regarding clamper safety practices. How did you handle the disagreement?
How to Answer
- 1
Identify the specific safety practice in question.
- 2
Explain the reasoning behind your perspective clearly.
- 3
Listen actively to your coworker's viewpoint.
- 4
Propose a compromise or a meeting with a supervisor if necessary.
- 5
Focus on maintaining a collaborative tone throughout the discussion.
Example Answers
In a recent project, a coworker wanted to bypass the double-check safety protocol. I explained the potential risks associated with skipping this step. After discussing, we both agreed to consult our supervisor to get a clear standard on safety practices.
Can you provide an example of how you effectively managed your time during a demanding clamper project?
How to Answer
- 1
Identify the specific clamper project and its challenges.
- 2
Explain the time management techniques you used, such as prioritization or scheduling.
- 3
Share how you set milestones and tracked progress.
- 4
Discuss any tools or software that helped you stay organized.
- 5
Highlight the positive outcome achieved as a result of your time management.
Example Answers
In a recent clamper project, I faced tight deadlines due to resource constraints. I created a detailed timeline, prioritizing tasks based on urgency. I used project management software to track our progress and held weekly check-ins to ensure we stayed on target, resulting in us completing the project two days early.
Describe how you have handled constructive criticism regarding your clamper operation techniques in the past.
How to Answer
- 1
Acknowledge the feedback positively
- 2
Share a specific example of the criticism received
- 3
Explain the steps you took to improve based on the feedback
- 4
Mention the outcome or results of your improvements
- 5
Highlight any ongoing adjustments you incorporate into your work
Example Answers
I received feedback from my supervisor about my clamper technique being too slow. I took their advice seriously and practiced the technique in my off-hours. As a result, my efficiency improved by 25%, and I regularly check in with my team for further tips.
Can you describe an experience where you trained a new employee on clamper operation? What did you emphasize?
How to Answer
- 1
Share a specific situation or context of the training.
- 2
Highlight key techniques or skills you emphasized for safe operation.
- 3
Discuss how you assessed their understanding during training.
- 4
Mention any feedback or adjustments made to improve their learning.
- 5
Conclude with the outcome of their training and performance.
Example Answers
During my last job, I trained a new employee on clamper operation by first demonstrating the setup process. I emphasized safety protocols, ensuring they understood the importance of securing all parts before operation. I used hands-on practice to assess their grasp of the operation and adjusted my teaching based on their questions. By the end of the training, they were confident and received positive feedback on their performance.
Have you ever led a team meeting focused on improving clamper workflows? Describe the outcome.
How to Answer
- 1
Start by briefly stating the context of the meeting.
- 2
Explain your role and what led you to lead the meeting.
- 3
Detail the specific workflow improvements discussed.
- 4
Highlight team collaboration and any tools or methods used.
- 5
Conclude with measurable outcomes or feedback received.
Example Answers
In my previous role, I led a team meeting to streamline our clamper workflow. I identified bottlenecks in the process and facilitated a discussion around potential solutions. We decided to implement a new tracking system, which improved our efficiency by 20% over the next month. The team's feedback was positive, noting better communication and clarity in tasks.
Technical Interview Questions
What safety regulations are critical to follow when operating clampers? Can you provide examples of how you ensure compliance?
How to Answer
- 1
Identify key safety regulations relevant to clampers, like OSHA standards.
- 2
Discuss safety gear usage, including hard hats and gloves.
- 3
Explain protocol for conducting pre-operation inspections.
- 4
Mention the importance of training and how you apply it.
- 5
Share an example of an incident and how you ensured compliance following it.
Example Answers
Key safety regulations like those from OSHA include proper use of personal protective equipment. I always wear a hard hat and gloves when operating clampers and ensure all team members do the same.
What regular maintenance tasks do you believe are essential for ensuring the proper functioning of clampers?
How to Answer
- 1
Inspect clampers for signs of wear or damage regularly
- 2
Ensure proper lubrication to minimize friction and prevent rust
- 3
Check electrical connections for integrity and cleanliness
- 4
Test clamp tension and alignment periodically to ensure efficiency
- 5
Schedule routine cleaning to remove debris and contaminants
Example Answers
Regular inspections are crucial. I check for wear, ensure everything is lubricated, and look at the electrical connections to avoid failures.
Don't Just Read Clamper Questions - Practice Answering Them!
Reading helps, but actual practice is what gets you hired. Our AI feedback system helps you improve your Clamper interview answers in real-time.
Personalized feedback
Unlimited practice
Used by hundreds of successful candidates
How do you ensure that the clamping process meets quality standards? What tools or checks do you utilize?
How to Answer
- 1
Describe specific quality checks you perform during clamping.
- 2
Mention any tools or equipment you use to monitor quality.
- 3
Explain how you document and track quality standards.
- 4
Discuss how you train team members on quality expectations.
- 5
Provide examples of troubleshooting when quality issues arise.
Example Answers
I perform regular visual inspections during the clamping process and use a torque wrench to ensure proper tension. I document each setup in a quality log to track compliance with standards and train new team members on these protocols.
What diagnostic tools or methods are you familiar with for diagnosing issues in clamper machinery?
How to Answer
- 1
Mention specific diagnostic tools like multimeters, oscilloscopes, and thermal cameras.
- 2
Discuss the importance of visual inspections for wear and tear.
- 3
Explain the role of software diagnostics in identifying mechanical faults.
- 4
Highlight the use of vibration analysis to detect misalignments or imbalance.
- 5
Reference any relevant experience with troubleshooting clamper systems.
Example Answers
I'm familiar with using multimeters to check electrical components and oscilloscopes for signal integrity. I always start with visual inspections to identify any obvious wear and tear. Software diagnostics have also been helpful in pinpointing issues quickly.
What steps do you take to calibrate a clamper correctly? Can you walk us through the process?
How to Answer
- 1
Identify the specific clamper model and its calibration requirements.
- 2
Use a proper measuring device to check the initial pressure readout.
- 3
Adjust the clamper settings according to the manufacturer's specifications.
- 4
Perform a functional test to ensure accurate pressure holding.
- 5
Document the calibration results and any adjustments made.
Example Answers
To calibrate a clamper, I start by identifying the model and checking its specific calibration requirements. Then, I measure the initial pressure using an appropriate device. After that, I adjust the settings as per the manufacturer's specifications. Once adjusted, I conduct a functional test to verify pressure accuracy and finally, I document the results.
Can you explain the troubleshooting process you follow when a clamper is underperforming?
How to Answer
- 1
Start by identifying the symptoms of underperformance.
- 2
Review the clamper's settings and configuration for accuracy.
- 3
Check for any physical obstructions or wear and tear.
- 4
Analyze any data or logs for patterns or anomalies.
- 5
Test the clamper in a controlled environment to pinpoint the issue.
Example Answers
First, I assess the symptoms of underperformance. Then, I double-check the settings to ensure they're correct. I inspect for any physical damage or debris. After that, I review operational data for any patterns. Finally, I run tests in isolation to see if the problem persists.
What types of control systems have you worked with in clamper operations, and what are their advantages?
How to Answer
- 1
Identify specific control systems used in clamper operations.
- 2
Explain how each system improves efficiency or safety.
- 3
Mention any relevant industry standards or regulations.
- 4
Be prepared to discuss personal experience with these systems.
- 5
Use clear examples to demonstrate your knowledge.
Example Answers
I have worked with proportional control systems in clamper operations. These systems allow for fine adjustments that enhance precision, minimizing product damage.
What industry codes or standards do you believe are essential to follow when working with clampers?
How to Answer
- 1
Research relevant industry standards like ANSI and ISO for clampers.
- 2
Mention specific safety standards such as OSHA regulations.
- 3
Discuss the importance of following manufacturer guidelines and specifications.
- 4
Highlight the significance of local regulations and compliance.
- 5
Emphasize the role of industry best practices in maintaining safety and efficiency.
Example Answers
I believe following ANSI and ISO standards is crucial when working with clampers, as they ensure quality and safety in the manufacturing process. Additionally, I always adhere to OSHA regulations to promote a safe work environment.
Discuss your familiarity with the mechanical components of a clamper. Which aspects do you feel most confident in?
How to Answer
- 1
Identify key mechanical components like the clamp pads and actuator.
- 2
Discuss how each component functions within the clamper system.
- 3
Highlight any hands-on experience with similar machinery.
- 4
Mention specific skills relevant to maintenance or operation.
- 5
Be honest about areas you are less familiar with but willing to learn.
Example Answers
I'm familiar with the key components of a clamper, such as the clamp pads and the hydraulic actuator. In my previous role, I operated similar equipment and have hands-on experience with routine maintenance tasks, leading to higher efficiency in operations.
Don't Just Read Clamper Questions - Practice Answering Them!
Reading helps, but actual practice is what gets you hired. Our AI feedback system helps you improve your Clamper interview answers in real-time.
Personalized feedback
Unlimited practice
Used by hundreds of successful candidates
Situational Interview Questions
If you noticed a clamp malfunctioning during production, what immediate steps would you take to address the problem?
How to Answer
- 1
Stop the production line to prevent further issues.
- 2
Assess the clamp for visible damage or irregularities.
- 3
Notify the production supervisor about the malfunction.
- 4
Follow safety protocols to ensure a safe working environment.
- 5
Document the issue for future reference and analysis.
Example Answers
I would immediately stop the production line to avoid any safety risks. Then, I'd inspect the clamp for any obvious problems and inform the production supervisor about the issue. After that, I'd make sure to follow safety procedures while addressing the malfunction.
Imagine you are faced with a sudden spike in workload and your clamper is unable to keep up. How would you prioritize your tasks?
How to Answer
- 1
Assess the urgency and importance of each task quickly
- 2
Identify any tasks that have deadlines or impact on others
- 3
Communicate with your team about your workload
- 4
Consider delegating tasks if possible
- 5
Focus on completing high-priority tasks first
Example Answers
I would quickly evaluate each task based on urgency and importance. I'd handle any deadline-driven tasks first, while communicating with my team to see if they can assist with anything.
Don't Just Read Clamper Questions - Practice Answering Them!
Reading helps, but actual practice is what gets you hired. Our AI feedback system helps you improve your Clamper interview answers in real-time.
Personalized feedback
Unlimited practice
Used by hundreds of successful candidates
How would you manage a situation where a team member is consistently failing to follow safety protocols while operating a clamper?
How to Answer
- 1
Address the issue directly and privately with the team member.
- 2
Listen to their perspective and understand their reasons for non-compliance.
- 3
Reiterate the importance of safety protocols clearly.
- 4
Implement a training session or refresher course if needed.
- 5
Report the behavior to a supervisor if it persists after intervention.
Example Answers
I would first have a private conversation with the team member to discuss their failure to follow safety protocols. I'd listen to their side of the story and ensure they understand why these protocols are essential. If needed, I'd suggest a training session to reinforce these safety measures.
Suppose you could redesign one aspect of the clamper process to enhance efficiency. What would it be and why?
How to Answer
- 1
Identify a specific stage in the clamper process that often causes delays.
- 2
Consider technological solutions that could streamline or automate tasks.
- 3
Focus on improving communication among team members during the process.
- 4
Highlight the expected benefits of your redesign, such as time savings or reduced errors.
- 5
Be prepared to discuss potential challenges and how to address them.
Example Answers
I would redesign the data entry stage by implementing an automated system that scans and processes documents. This would reduce manual errors and speed up the workflow, leading to faster clamp resolutions.
If a project requires multiple departments to cooperate on clamper usage, how would you ensure effective communication?
How to Answer
- 1
Establish a regular meeting schedule for all departments involved
- 2
Use a shared communication platform for updates and feedback
- 3
Define clear roles and responsibilities for each department
- 4
Create a centralized document for tracking progress and issues
- 5
Encourage open dialogue and feedback at all stages of the project
Example Answers
I would set up bi-weekly meetings with representatives from each department to discuss progress. We would use a shared platform like Slack to keep everyone updated and engaged.
How would you handle a situation where a clamper caused a minor workplace injury? What steps would you take afterward?
How to Answer
- 1
Ensure the injured person receives immediate medical attention if necessary.
- 2
Document the incident by noting details like time, location, and any witnesses.
- 3
Report the injury to your supervisor and follow company protocol.
- 4
Review the incident to determine the cause and prevent future occurrences.
- 5
Communicate with the injured employee to check on their recovery and reassure them.
Example Answers
First, I would assess the situation and ensure the injured clamper receives any necessary medical attention. Then, I would document the details of the incident and report it to my supervisor as per protocol. After that, I would analyze what led to the injury to prevent it from happening again.
If you find a discrepancy in clamping measurements during an audit, what would be your next steps?
How to Answer
- 1
Verify the accuracy of the measurements with a secondary tool.
- 2
Consult the relevant documentation for expected measurements.
- 3
Engage with team members to gather insights on potential errors.
- 4
Document the discrepancy clearly for future reference.
- 5
Report the findings to the supervisor and suggest corrective actions.
Example Answers
First, I would double-check the measurements using a calibrated tool to ensure accuracy. Then, I'd refer to the project specifications to determine the expected results. After that, I would discuss it with my colleagues to see if they noticed any issues during their measurements. Finally, I'd document everything and inform my supervisor about the discrepancy with a suggested plan to rectify it.
How would you approach coordinating a new clamper installation project from start to finish?
How to Answer
- 1
Define project scope and goals clearly with all stakeholders involved
- 2
Create a detailed timeline and task list for the installation process
- 3
Assign roles and responsibilities to team members based on expertise
- 4
Ensure effective communication channels are established for updates and issue resolution
- 5
Conduct a post-installation review to evaluate success and identify improvements
Example Answers
I would start by discussing the project objectives with stakeholders to ensure everyone is aligned. Then, I would outline a timeline and assign specific tasks to team members, making sure to maintain regular check-ins for updates and challenges. Finally, I'd organize a review meeting post-installation to gather feedback and assess our performance.
Imagine you notice an inefficiency in the clamper production line. How would you propose a solution to your supervisor?
How to Answer
- 1
Identify the specific inefficiency and its impact on production.
- 2
Gather data or observations to support your claim.
- 3
Develop a clear, practical solution addressing the inefficiency.
- 4
Consider potential challenges and prepare to discuss them.
- 5
Communicate your proposal confidently and concisely.
Example Answers
I noticed that the clamper line is often delayed due to a bottleneck at the assembly station. After observing for a week, I found that adding an extra worker during peak hours could significantly speed up the process. I would suggest this to my supervisor with data showing the time saved.
If a client reported issues with the clamps supplied, how would you handle the situation to ensure customer satisfaction?
How to Answer
- 1
Listen carefully to the client's concerns and ask clarifying questions to understand the issue.
- 2
Apologize for any inconvenience caused and reassure them you will resolve the problem.
- 3
Evaluate the issue and provide a clear solution, such as replacing the clamps or offering a refund.
- 4
Follow up with the client after the resolution to ensure they are satisfied with the outcome.
- 5
Document the issue for future reference and to prevent similar problems.
Example Answers
I would start by listening closely to the client's concerns and asking questions to fully understand the issue. Then, I'd apologize for any inconvenience and offer to replace the clamps or provide a refund. After that, I'd follow up with the client to ensure they are satisfied with the resolution.
Don't Just Read Clamper Questions - Practice Answering Them!
Reading helps, but actual practice is what gets you hired. Our AI feedback system helps you improve your Clamper interview answers in real-time.
Personalized feedback
Unlimited practice
Used by hundreds of successful candidates
Clamper Position Details
Recommended Job Boards
Randstad USA
www.randstadusa.com/jobs/search/?q=ClamperThese job boards are ranked by relevance for this position.
Related Positions
- Clamp Operator
- Tappet Adjuster
- Metal Trimmer
- Valve Maker
- Ball Holder
- Deadener
- Jointer
- Crate Maker
- Clammer
- Clam Shucker
Similar positions you might be interested in.
Ace Your Next Interview!
Practice with AI feedback & get hired faster
Personalized feedback
Used by hundreds of successful candidates
Ace Your Next Interview!
Practice with AI feedback & get hired faster
Personalized feedback
Used by hundreds of successful candidates