Top 30 Clamp Operator Interview Questions and Answers [Updated 2025]
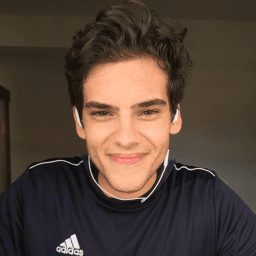
Andre Mendes
•
March 30, 2025
Preparing for a Clamp Operator interview can be daunting, but we're here to help you succeed. In this post, we've compiled the most common interview questions for this role, along with example answers and practical tips to help you respond effectively. Whether you're a seasoned operator or new to the field, this guide will equip you with the insights needed to impress your potential employers.
Download Clamp Operator Interview Questions in PDF
To make your preparation even more convenient, we've compiled all these top Clamp Operatorinterview questions and answers into a handy PDF.
Click the button below to download the PDF and have easy access to these essential questions anytime, anywhere:
List of Clamp Operator Interview Questions
Behavioral Interview Questions
Describe a time when you identified a safety hazard in your work environment and what steps you took to address it.
How to Answer
- 1
Think of a specific incident where safety was at risk
- 2
Explain how you recognized the hazard and its potential impact
- 3
Describe the immediate actions you took to mitigate the hazard
- 4
Mention any long-term solutions you implemented to prevent reoccurrence
- 5
Highlight the importance of safety in your work environment
Example Answers
At my last job, I noticed that some cables were improperly laid out on the floor, creating a tripping hazard. I immediately reported it to my supervisor and helped arrange them in a safer manner. After that, we instituted a weekly check to ensure all cables were secured correctly.
Give an example of a time you worked in a team to accomplish a goal. What was your role and how did you contribute?
How to Answer
- 1
Choose a specific project or task where teamwork was essential
- 2
Clearly define your role and responsibilities within the team
- 3
Highlight your contributions to the team's success
- 4
Mention any challenges faced and how you overcame them together
- 5
Conclude with the outcome of the project and its significance
Example Answers
In my previous job, I was part of a team tasked with improving production efficiency. I was the Clamp Operator responsible for setting up the machinery. I contributed by ensuring all equipment was properly calibrated and by suggesting a new workflow that reduced downtime. As a result, we improved efficiency by 20% within a month.
Don't Just Read Clamp Operator Questions - Practice Answering Them!
Reading helps, but actual practice is what gets you hired. Our AI feedback system helps you improve your Clamp Operator interview answers in real-time.
Personalized feedback
Unlimited practice
Used by hundreds of successful candidates
Tell me about a time you faced a significant challenge at work. How did you overcome it?
How to Answer
- 1
Think of a specific challenge related to your previous roles.
- 2
Use the STAR method: Situation, Task, Action, Result.
- 3
Highlight your problem-solving skills and teamwork.
- 4
Keep your answer focused and relevant to clamp operations.
- 5
Be honest and reflect on what you learned from the experience.
Example Answers
In my previous job as a machine operator, we faced a sudden equipment failure during a critical production run. I quickly assessed the situation, communicated with my supervisor, and coordinated with the maintenance team to prioritize repairs. We managed to fix the issue in time and met our production goals, which reinforced my ability to handle pressure.
Describe a situation where your attention to detail prevented a potential error or accident.
How to Answer
- 1
Choose a specific example from past experience.
- 2
Focus on a mistake that was avoided due to your carefulness.
- 3
Explain the steps you took to ensure accuracy.
- 4
Highlight the outcome and its importance to safety or efficiency.
- 5
Use a clear structure: Situation, Task, Action, Result (STAR).
Example Answers
In my previous role as a Clamp Operator, I noticed a small misalignment in the clamps while preparing an important load. I double-checked the measurements and found that one clamp was incorrectly calibrated. By adjusting it before loading, we avoided potential damage to the fragile materials and ensured a smooth operation.
How do you handle stressful situations at work and ensure your performance remains consistent?
How to Answer
- 1
Stay calm and take deep breaths when feeling stressed
- 2
Prioritize tasks to maintain focus on what is most important
- 3
Use a consistent routine to manage workload effectively
- 4
Communicate with team members to share challenges and solutions
- 5
Reflect on past stressful situations to develop better coping strategies
Example Answers
When I face stressful situations, I take a moment to breathe deeply and center myself. I prioritize my tasks so that I can focus on what needs to be done first. If things get overwhelming, I communicate with my team for support, which helps alleviate the pressure.
Can you describe a time when you introduced a new idea or process that improved efficiency in your job?
How to Answer
- 1
Choose a specific example from your work experience.
- 2
Explain the problem or inefficiency you noticed.
- 3
Describe the solution you proposed and how you implemented it.
- 4
Share the measurable impact or results of your idea.
- 5
Keep your answer focused and concise.
Example Answers
In my previous role, I noticed that our clamp loading process was taking too long due to manual adjustments. I suggested automating the adjustments using a simple lever mechanism. After implementing this change, we reduced loading time by 20%, which allowed us to increase production output significantly.
Provide an example of a situation where you took initiative at work and what the outcome was.
How to Answer
- 1
Think of a specific instance where you identified a problem or opportunity.
- 2
Focus on the actions you took and how they had a positive impact.
- 3
Quantify the results if possible, such as time saved or productivity increased.
- 4
Keep it concise and relevant to the Clamp Operator role.
- 5
Use the STAR method: Situation, Task, Action, Result.
Example Answers
At my previous job, we had a recurring issue with the clamping mechanism that caused delays. I took the initiative to review the process and experimented with adjustments, resulting in a 20% decrease in downtime. My supervisor appreciated the proactive approach and implemented my changes across the team.
Describe a conflict you've had with a colleague and how you resolved it.
How to Answer
- 1
Choose a specific conflict that had a positive resolution.
- 2
Focus on your role in the situation and what actions you took.
- 3
Emphasize communication and understanding as key to resolution.
- 4
Mention any compromises or solutions that worked for both parties.
- 5
Conclude by reflecting on what you learned from the experience.
Example Answers
In my last job, I had a conflict with a colleague regarding the division of labor in a project. We were both taking on overlapping tasks which led to frustration. I initiated a meeting where we openly discussed our responsibilities and found a way to divide the tasks more clearly. By the end of the conversation, we had a plan that utilized both our strengths and it improved our working relationship.
How do you stay updated with the latest techniques and best practices for operating machinery?
How to Answer
- 1
Subscribe to industry magazines and online forums
- 2
Attend workshops and training sessions regularly
- 3
Engage with colleagues to share best practices
- 4
Follow manufacturer updates and technical bulletins
- 5
Utilize online courses for skill advancement
Example Answers
I subscribe to several industry magazines and follow online forums where professionals discuss new techniques. I also regularly attend workshops that focus on the latest advancements in machinery operation.
Recall a time you identified a flaw in a process. How did you handle it to maintain quality?
How to Answer
- 1
Describe a specific process you encountered that had a flaw.
- 2
Explain how you identified the flaw with details.
- 3
Discuss the steps you took to address the flaw.
- 4
Highlight any collaboration with your team or supervisors.
- 5
Mention the outcome and how it improved quality.
Example Answers
In my previous job, I noticed that our assembly line had a recurring issue with alignment errors. I conducted a thorough observation, pinpointing where the misalignment occurred. I suggested an adjustment to the calibration process and collaborated with my team to implement a new verification step. As a result, we reduced defects by 30%.
Don't Just Read Clamp Operator Questions - Practice Answering Them!
Reading helps, but actual practice is what gets you hired. Our AI feedback system helps you improve your Clamp Operator interview answers in real-time.
Personalized feedback
Unlimited practice
Used by hundreds of successful candidates
Technical Interview Questions
Can you explain how to properly operate a clamp truck and the key controls you regularly use?
How to Answer
- 1
Start by outlining the safety checks before operation.
- 2
Explain the main controls used for lifting and maneuvering.
- 3
Describe the process of adjusting the clamp appropriately for loads.
- 4
Mention how to ensure stability during operation.
- 5
Conclude with a brief note on regular maintenance checks.
Example Answers
To operate a clamp truck safely, I first conduct safety checks such as ensuring the area is clear and checking for any potential hazards. The key controls I use include the lift function lever and the clamp release buttons. I adjust the clamp to securely grip the load before lifting, making sure it is stable. During operation, I keep the load as low as possible for stability, and I always inspect the truck for maintenance after use.
What routine maintenance checks would you perform on a clamp truck to ensure it is safe and operational?
How to Answer
- 1
Check hydraulic systems for leaks and proper fluid levels.
- 2
Inspect tires for wear and ensure proper inflation.
- 3
Examine the clamps for damage or wear and ensure they operate smoothly.
- 4
Test the brakes and steering for responsiveness and functionality.
- 5
Perform visual checks for safety features like lights and alarms.
Example Answers
I would start by checking the hydraulics for any leaks and ensuring all fluid levels are adequate. Next, I would inspect the tires for any signs of wear and make sure they are properly inflated. It's also important to examine the clamps thoroughly to confirm they are in good condition.
Don't Just Read Clamp Operator Questions - Practice Answering Them!
Reading helps, but actual practice is what gets you hired. Our AI feedback system helps you improve your Clamp Operator interview answers in real-time.
Personalized feedback
Unlimited practice
Used by hundreds of successful candidates
What factors must be considered to determine the weight capacity when using a clamp truck?
How to Answer
- 1
Understand the specifications of the clamp truck model being used.
- 2
Consider the load center distance and how it affects lifting capacity.
- 3
Account for the type of material being lifted and its weight distribution.
- 4
Ensure that the ground surface is stable and can support the weight.
- 5
Review the manufacturer's guidelines for maximum load capacity.
Example Answers
To determine the weight capacity when using a clamp truck, I first check the specifications of the truck model. Next, I look at the load center distance, as it significantly impacts the lifting capacity. I also consider the material type and weight distribution to ensure safety and stability.
How would you troubleshoot a situation where the clamp truck is not lifting correctly?
How to Answer
- 1
Check the power supply to ensure the truck is receiving electricity.
- 2
Inspect the hydraulic fluid levels and look for leaks in the system.
- 3
Examine the lift mechanisms for any visible damage or obstructions.
- 4
Test the control system and switches for any faults.
- 5
Consult the operator's manual for specific troubleshooting steps.
Example Answers
First, I would check if the clamp truck is plugged in and that there is power. Then, I would look at the hydraulic fluid levels and check for any leaks. If those are fine, I would inspect the lift mechanisms for obstructions or damage.
What are the key safety protocols you must adhere to when operating a clamp truck?
How to Answer
- 1
Always wear appropriate personal protective equipment (PPE) such as hard hats and safety shoes.
- 2
Conduct a pre-operational check of the clamp truck before use, inspecting brakes, steering, and clamps.
- 3
Be aware of your surroundings and check for overhead obstructions or nearby personnel.
- 4
Load and unload materials evenly to prevent tipping and ensure stability.
- 5
Follow the company's safety procedures and report any safety hazards immediately.
Example Answers
The key safety protocols include wearing PPE like safety shoes and hard hats, checking the clamp truck before use, staying aware of surroundings, loading materials evenly, and following established safety procedures.
Explain the steps you would take to verify that the clamp truck's hydraulic system is functioning correctly.
How to Answer
- 1
Check for hydraulic fluid leaks around the system.
- 2
Inspect hydraulic fluid levels and top off if necessary.
- 3
Test the operation of the clamps by raising and lowering them.
- 4
Listen for unusual noises during operation that may indicate a problem.
- 5
Check the hydraulic hoses for any signs of wear or damage.
Example Answers
To verify the hydraulic system, I would first check for any leaks in the fluid lines. Then, I would ensure the fluid reservoir is at the correct level. Next, I would operate the clamps to see if they function smoothly without any hitches. I would listen for any strange noises during this testing. Finally, I would inspect the hoses for any visible damage.
How do you ensure proper weight distribution when loading and transporting pallets?
How to Answer
- 1
Assess the weight of each item before placing it on the pallet.
- 2
Place heavier items at the bottom and center of the pallet.
- 3
Distribute weight evenly across the pallet's surface.
- 4
Secure the load with straps or wraps to prevent shifting.
- 5
Check the weight limits of the transport vehicle.
Example Answers
I ensure proper weight distribution by first assessing the weight of each item and placing the heaviest ones at the bottom and center of the pallet. I always secure the load with straps to keep it stable during transport.
What techniques do you use to ensure precision when positioning the clamp on a load?
How to Answer
- 1
Always assess the load's center of gravity before clamping.
- 2
Use measurement tools to verify the alignment of the clamp.
- 3
Adjust the clamp slowly to avoid misalignment.
- 4
Communicate with team members to confirm positioning.
- 5
Perform a dry run to ensure everything is in the correct position before lifting.
Example Answers
I always start by checking the load's center of gravity to determine the best clamping point, then I use a measuring tape to ensure the clamp is aligned properly.
How does your role as a clamp operator contribute to effective inventory management?
How to Answer
- 1
Emphasize the importance of accuracy in handling materials
- 2
Discuss the efficiency of loading and unloading processes
- 3
Highlight the role in reducing damage to products
- 4
Mention communication with team members for smooth operations
- 5
Relate your actions to overall inventory turnover and cost savings
Example Answers
As a clamp operator, I ensure that materials are handled accurately, which is crucial for maintaining inventory integrity and preventing stock discrepancies.
What methods do you use to ensure the security and stability of loads you transport?
How to Answer
- 1
Assess the load's weight and dimensions before transportation
- 2
Use appropriate securing devices like straps, chains, or nets
- 3
Ensure the load is balanced and evenly distributed on the transport vehicle
- 4
Regularly check load stability during transport, especially on uneven terrain
- 5
Follow all safety regulations and guidelines specific to loads and equipment
Example Answers
I always start by assessing the weight and dimensions of the load to choose the right securing devices. I use straps and ensure the load is evenly balanced on the vehicle to prevent shifting.
Don't Just Read Clamp Operator Questions - Practice Answering Them!
Reading helps, but actual practice is what gets you hired. Our AI feedback system helps you improve your Clamp Operator interview answers in real-time.
Personalized feedback
Unlimited practice
Used by hundreds of successful candidates
Situational Interview Questions
If you are asked to move a high volume of pallets with limited time, how would you prioritize your tasks?
How to Answer
- 1
Assess the total number of pallets to be moved and their locations
- 2
Identify the most efficient routes for transporting the pallets
- 3
Prioritize higher priority or time-sensitive pallets first
- 4
Communicate with team members to coordinate efforts and equipment
- 5
Regularly check progress to adjust plans and ensure time efficiency
Example Answers
I would first assess how many pallets need to be moved and their locations. Then, I would map out the most efficient routes to transport them. I’d prioritize the highest urgency pallets and communicate with my team to ensure we're working efficiently together.
Imagine the clamp delivery schedule gets delayed due to a mechanical failure. How would you handle the situation to minimize disruptions?
How to Answer
- 1
Assess the situation quickly to understand the delay impact
- 2
Communicate with supervisors and team members promptly
- 3
Implement contingency plans to keep operations running
- 4
Prioritize urgent tasks that do not require clamps
- 5
Document the issue for future reference and improvement
Example Answers
I would immediately evaluate how the delay affects our current workload. I would inform my supervisor and team, and explore using alternative tools if available. Meanwhile, I would focus on tasks that can still progress without clamps, ensuring we minimize downtime.
Don't Just Read Clamp Operator Questions - Practice Answering Them!
Reading helps, but actual practice is what gets you hired. Our AI feedback system helps you improve your Clamp Operator interview answers in real-time.
Personalized feedback
Unlimited practice
Used by hundreds of successful candidates
If you notice that a coworker is not following proper protocols, how would you address the situation?
How to Answer
- 1
Stay calm and approach the coworker privately.
- 2
Use 'I' statements to express your concern without blaming.
- 3
Provide specific examples of the protocols not being followed.
- 4
Ask if they need support or clarification on the protocols.
- 5
If necessary, inform a supervisor if the issue persists.
Example Answers
I would approach my coworker in a calm manner and say, 'I noticed that we haven't been following the safety checklist properly. I wanted to discuss it with you to ensure we both stay safe.'
You are given a new type of load that you have never handled before. How would you approach learning to handle it safely and efficiently?
How to Answer
- 1
Research the specifications and requirements of the new load.
- 2
Consult with experienced colleagues or supervisors for insights.
- 3
Review safety guidelines and handling best practices specific to the load.
- 4
Conduct a risk assessment before attempting to handle the load.
- 5
Practice with a demonstration or simulation if available.
Example Answers
I would start by researching the specifications of the load to understand its weight and dimensions. Then, I would ask my colleagues who have handled similar loads for their advice. Reviewing the safety guidelines would be next, and I would conduct a risk assessment to identify any potential hazards. If possible, I would also practice with a demonstration before handling it myself.
A client reports that their order was damaged during delivery. How would you investigate and address their concerns?
How to Answer
- 1
Ask the client for specific details about the damage.
- 2
Collect information about how the order was packaged and shipped.
- 3
Check for any internal notes on the order and delivery process.
- 4
Propose a solution, such as a replacement or refund, based on company policy.
- 5
Follow up with the client after addressing their concerns to ensure satisfaction.
Example Answers
I would start by asking the client to describe the damage in detail and any pictures they may have. Then, I would verify the shipping method and packaging used for their order. After gathering the necessary information, I would offer a replacement if policy allows, and follow up later to confirm their satisfaction.
If you encounter two conflicting tasks that need immediate attention, how do you decide which to address first?
How to Answer
- 1
Assess the urgency and impact of each task
- 2
Consider deadlines and expected outcomes
- 3
Evaluate resources and support available
- 4
Communicate with relevant stakeholders if possible
- 5
Prioritize based on company goals and values
Example Answers
I would first evaluate which task has the most immediate deadline and impact. If one task affects production directly, I would prioritize that one. I would then inform my supervisor about my decision and ensure the other task is scheduled right after.
You are running low on a critical piece of equipment, how would you ensure job continuity?
How to Answer
- 1
Assess the current supply and determine the critical level of equipment needed
- 2
Communicate with supervisors or the procurement team about the shortage
- 3
Identify alternative solutions, such as renting equipment or adjusting workflows
- 4
Prioritize tasks that can be completed with the existing equipment
- 5
Document the situation and create a plan to prevent future shortages
Example Answers
I would first assess how low we are on equipment and inform my supervisor immediately. Then, I would look into renting or borrowing equipment from nearby facilities to ensure our job continues without delays.
What steps would you take if you witnessed an accident involving a clamp truck?
How to Answer
- 1
Ensure your own safety first before approaching the scene.
- 2
Assess the situation quickly to determine if anyone is injured.
- 3
Call for emergency assistance immediately, if needed.
- 4
Provide first aid if you are trained and it is safe to do so.
- 5
Report the incident to your supervisor and document what you saw.
Example Answers
If I witnessed an accident with a clamp truck, I would first check my own safety, then quickly assess if anyone was hurt. If there were injuries, I would call for emergency help right away. After that, I would administer first aid if I was trained, and finally, I would inform my supervisor about the incident and write down what I saw.
If you notice a repetitive issue causing delays, what measures would you propose to resolve it?
How to Answer
- 1
Identify the root cause of the issue through observation and data analysis
- 2
Engage team members to gather insights and feedback about the problem
- 3
Propose practical solutions that can be implemented quickly
- 4
Suggest a plan for testing the proposed solutions on a small scale
- 5
Implement regular reviews to assess the effectiveness of changes
Example Answers
I would first analyze the delays to find the root cause. Then, I would discuss with my team to gather their input and propose a simple fix. Once we have a solution, I’d test it on a small scale to see if it resolves the issue completely.
Describe how you would manage a scenario where you're required to meet unexpected high-demand operational requirements.
How to Answer
- 1
Stay calm and assess the situation quickly.
- 2
Prioritize tasks based on urgency and impact.
- 3
Communicate clearly with your team about roles and expectations.
- 4
Utilize available resources efficiently to meet demands.
- 5
Implement a plan and be flexible to adapt as necessary.
Example Answers
In a high-demand situation, I would first assess what needs to be done immediately and prioritize those tasks. I would then communicate with my team to delegate responsibilities clearly, ensuring everyone knows their role. I would make use of all available resources to meet the demand efficiently, adapting my plan as new challenges arise.
Don't Just Read Clamp Operator Questions - Practice Answering Them!
Reading helps, but actual practice is what gets you hired. Our AI feedback system helps you improve your Clamp Operator interview answers in real-time.
Personalized feedback
Unlimited practice
Used by hundreds of successful candidates
Clamp Operator Position Details
Salary Information
Recommended Job Boards
CareerBuilder
www.careerbuilder.com/jobs-clamp-forklift-operatorZipRecruiter
www.ziprecruiter.com/Jobs/Clamp-OperatorThese job boards are ranked by relevance for this position.
Related Positions
- Clamper
- Line Operator
- Valve Maker
- Tappet Adjuster
- Control Operator
- Utility Operator
- Utilities Operator
- Block Operator
- Auxiliary Operator
- Commutator Operator
Similar positions you might be interested in.
Ace Your Next Interview!
Practice with AI feedback & get hired faster
Personalized feedback
Used by hundreds of successful candidates
Ace Your Next Interview!
Practice with AI feedback & get hired faster
Personalized feedback
Used by hundreds of successful candidates