Top 30 Line Operator Interview Questions and Answers [Updated 2025]
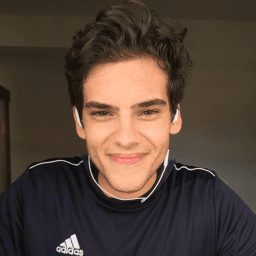
Andre Mendes
•
March 30, 2025
Preparing for a Line Operator interview? Look no further! This blog post compiles the most common questions you might face, complete with example answers and expert tips to help you respond effectively. Whether you're a seasoned professional or new to the field, these insights will guide you in showcasing your skills and confidence, setting you up for success in your next interview.
Download Line Operator Interview Questions in PDF
To make your preparation even more convenient, we've compiled all these top Line Operatorinterview questions and answers into a handy PDF.
Click the button below to download the PDF and have easy access to these essential questions anytime, anywhere: