Top 30 Compressor Operator Interview Questions and Answers [Updated 2025]
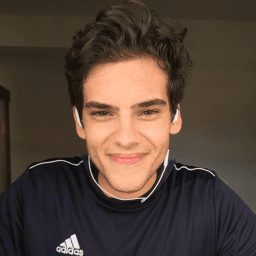
Andre Mendes
•
March 30, 2025
Navigating a compressor operator interview can be daunting, but preparation is key to success. In this updated guide, we've compiled the most common interview questions for the compressor operator role, complete with example answers and insightful tips to help you respond confidently. Whether you're a seasoned professional or new to the field, this post will equip you with the knowledge to impress your interviewer.
Download Compressor Operator Interview Questions in PDF
To make your preparation even more convenient, we've compiled all these top Compressor Operatorinterview questions and answers into a handy PDF.
Click the button below to download the PDF and have easy access to these essential questions anytime, anywhere: