Top 29 Die Technician Interview Questions and Answers [Updated 2025]
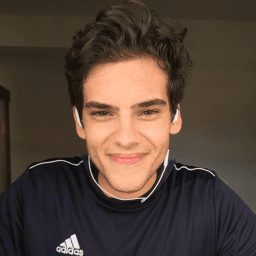
Andre Mendes
•
March 30, 2025
Preparing for a Die Technician interview can be daunting, but this blog post is here to help. It includes a comprehensive list of the most common interview questions for this specialized role, paired with example answers and tips on how to respond effectively. Whether you're a seasoned professional or a newcomer to the field, gain the insights you need to impress your interviewers and secure the job.
Download Die Technician Interview Questions in PDF
To make your preparation even more convenient, we've compiled all these top Die Technicianinterview questions and answers into a handy PDF.
Click the button below to download the PDF and have easy access to these essential questions anytime, anywhere:
List of Die Technician Interview Questions
Technical Interview Questions
How do you read and interpret technical blueprints related to die manufacturing?
How to Answer
- 1
Familiarize yourself with common blueprint symbols and terminology
- 2
Use a ruler or scale to measure dimensions accurately
- 3
Cross-reference specifications and note critical tolerances
- 4
Identify key features like holes, cutouts, and edges
- 5
Practice interpreting sample blueprints to improve accuracy
Example Answers
I start by reviewing the key symbols and terminology used in the blueprints to ensure I understand what each part represents. Then, I measure the dimensions with a scale to confirm that they match the specifications. I pay special attention to any tolerances indicated, as they are crucial for die fitting.
What are the key considerations when designing a die for a particular manufacturing process?
How to Answer
- 1
Understand the material properties of the workpiece and die.
- 2
Consider the manufacturing process requirements like tolerances and speeds.
- 3
Design for ease of maintenance and replacement of parts.
- 4
Evaluate the cooling and heating needs during production.
- 5
Account for the cost-effectiveness of the die design in relation to production volume.
Example Answers
When designing a die, I focus on the material properties to ensure compatibility with the workpiece. I also emphasize meeting the specific tolerances required for the manufacturing process, which affects the die’s precision.
Don't Just Read Die Technician Questions - Practice Answering Them!
Reading helps, but actual practice is what gets you hired. Our AI feedback system helps you improve your Die Technician interview answers in real-time.
Personalized feedback
Unlimited practice
Used by hundreds of successful candidates
Explain your process for diagnosing issues with a malfunctioning die.
How to Answer
- 1
Start by reviewing the specifications and requirements of the die.
- 2
Inspect the die for physical damage or wear.
- 3
Check the setup and alignment of the die in the machine.
- 4
Test with sample materials to identify the failure point.
- 5
Consult with team members for additional insights or experience with similar issues.
Example Answers
I begin by reviewing the die specifications to understand its intended function. Then, I visually inspect the die for any signs of wear or damage, such as cracks. Next, I check its alignment in the press and perform tests with various materials to pinpoint where the malfunction occurs. Collaboration with my colleagues often helps in diagnosing recurring problems more efficiently.
What types of materials do you typically work with when creating dies, and how do their properties affect your work?
How to Answer
- 1
Identify common materials like steel, aluminum, and plastic.
- 2
Discuss specific properties like hardness, ductility, and thermal conductivity.
- 3
Mention how these properties influence die strength and wear resistance.
- 4
Include examples of when you choose one material over another based on its characteristics.
- 5
Conclude with how material selection impacts manufacturing efficiency.
Example Answers
I typically work with tool steels and aluminum alloys. Tool steels are hard and wear-resistant, which is essential for long-lasting dies, while aluminum is lighter and easier to machine, ideal for prototype dies. I choose the material based on the production volume and required durability.
How do you ensure precision when programming CNC machines for die creation?
How to Answer
- 1
Use precise measurements and dimensions from CAD models as the basis.
- 2
Regularly calibrate CNC machines to maintain accuracy.
- 3
Perform test cuts and adjust parameters based on results.
- 4
Monitor cutting conditions and tool wear during operations.
- 5
Utilize software simulation to preview the machining process.
Example Answers
I start by importing accurate CAD models to ensure all dimensions are correct. I also calibrate the CNC machine regularly to avoid any discrepancies. Before final machining, I run test cuts to fine-tune the parameters and check for precision.
What regular maintenance tasks do you perform on dies to ensure they remain in good working condition?
How to Answer
- 1
Identify specific maintenance tasks like cleaning, lubricating, and inspecting dies regularly.
- 2
Discuss the schedule for these tasks, such as daily, weekly, or before production runs.
- 3
Mention checking for wear and tear, and how you measure and address it.
- 4
Emphasize the importance of documentation for maintenance activities to track performance.
- 5
Highlight any relevant experience with specific types of dies or materials.
Example Answers
I perform regular cleaning and lubrication of the dies after each production run to remove residues and ensure smooth operation. Typically, I inspect them for wear every week and replace components as needed.
What tools do you use for measuring accuracy in die production, and how do you ensure they are calibrated?
How to Answer
- 1
Start by naming specific measurement tools like calipers and micrometers.
- 2
Explain the importance of regular calibration for accuracy and reliability.
- 3
Mention any calibration standards you follow, such as ISO or ASTM.
- 4
Include how often you calibrate these tools and document the process.
- 5
Discuss any software or systems you use for logging measurements and calibrations.
Example Answers
I use digital calipers and micrometers for measuring the dimensions of die components, ensuring high precision. I calibrate these tools monthly according to ISO standards and maintain a log of all calibration activities.
What finishing techniques do you apply to dies, and how do they affect the final product?
How to Answer
- 1
Identify specific finishing techniques like polishing, coating, or surface hardening.
- 2
Explain how these techniques improve the die's performance or longevity.
- 3
Discuss the impact on the quality of the final product, such as surface finish and precision.
- 4
Mention any trade-offs or considerations in choosing a finishing technique.
- 5
Include examples of situations where a specific technique was crucial.
Example Answers
I commonly apply polishing and coating techniques to dies. Polishing enhances the surface finish, resulting in smoother parts, while coating can reduce wear and extend the die's lifespan. For example, a nickel plating on a die improved its durability significantly in a high-volume stamping application.
What software applications are you proficient in that relate to die design and production?
How to Answer
- 1
Identify key software used in die design and production such as CAD programs.
- 2
Mention specific tools and your level of proficiency with each.
- 3
Highlight any relevant certifications or training you've completed.
- 4
Provide examples of projects where you used the software effectively.
- 5
Be prepared to discuss how you stay updated with software advancements.
Example Answers
I am proficient in SolidWorks and AutoCAD for die design. I've used SolidWorks for over 5 years, designing intricate dies for metal stamping.
Explain the role of heat treatment in die manufacturing and how you ensure proper heat treatment is applied.
How to Answer
- 1
Explain the purpose of heat treatment, focusing on strength and durability.
- 2
Discuss various heat treatment processes like annealing, quenching, and tempering.
- 3
Mention specific materials and their heat treatment requirements.
- 4
Talk about monitoring temperature and time for effective heat treatment.
- 5
Highlight your experience with quality control during the heat treatment process.
Example Answers
Heat treatment is crucial in die manufacturing as it enhances the mechanical properties of the die materials, making them tougher and more resistant to wear. I ensure proper heat treatment by strictly following the recommended procedures for each material, using calibrated equipment to monitor temperatures carefully, and conducting regular inspections throughout the process.
Don't Just Read Die Technician Questions - Practice Answering Them!
Reading helps, but actual practice is what gets you hired. Our AI feedback system helps you improve your Die Technician interview answers in real-time.
Personalized feedback
Unlimited practice
Used by hundreds of successful candidates
Behavioral Interview Questions
Can you describe a time when you identified a significant problem with a die setup? How did you resolve it?
How to Answer
- 1
Start by clearly defining the issue you encountered with the die setup.
- 2
Explain the steps you took to diagnose the problem effectively.
- 3
Detail the solution you implemented to resolve the issue.
- 4
Mention any tools or techniques you used during the process.
- 5
Emphasize the positive outcome from your resolution efforts.
Example Answers
In a recent project, I noticed inconsistent dimensional accuracy in parts produced from a die setup. I reviewed the alignment of the die and discovered it was off by a millimeter. I recalibrated the die and adjusted the parameters, which resulted in the parts meeting all specifications.
Tell us about a time you had to work closely with other technicians or engineers. What was your role in that collaboration?
How to Answer
- 1
Choose a specific project where teamwork was essential.
- 2
Describe your role clearly and the contributions you made.
- 3
Highlight how you communicated and coordinated with others.
- 4
Mention any challenges faced and how the team overcame them.
- 5
Conclude with the outcome of the collaboration and your learnings.
Example Answers
In a recent project to improve die cutting efficiency, I worked closely with two mechanical engineers. My role involved providing feedback on die design and suggesting modifications based on production requirements. We held daily briefings to ensure alignment, which helped us identify issues early. One challenge was a delay in material delivery, but we adjusted our timeline collectively and succeeded in meeting our new schedule. The project increased efficiency by 15%, and I learned the importance of transparent communication.
Don't Just Read Die Technician Questions - Practice Answering Them!
Reading helps, but actual practice is what gets you hired. Our AI feedback system helps you improve your Die Technician interview answers in real-time.
Personalized feedback
Unlimited practice
Used by hundreds of successful candidates
Describe a situation where you disagreed with a coworker about a die design or repair process. How did you handle it?
How to Answer
- 1
Stay calm and professional during disagreements.
- 2
Listen to your coworker's perspective fully before responding.
- 3
Use specific examples to illustrate your point of view.
- 4
Suggest a compromise or a test to evaluate both ideas.
- 5
Focus on the project's objectives rather than personal opinions.
Example Answers
In my previous role, I disagreed with a coworker about the material selection for a new die. I listened to their reasoning and shared my concerns about durability. We agreed to run a small test with both materials to see which performed better, and ultimately, the test confirmed my concerns.
Can you discuss a time when you implemented a change that improved the efficiency of the die production process?
How to Answer
- 1
Identify a specific change you made in the production process.
- 2
Explain the problem that prompted the change.
- 3
Describe how you implemented the change and involved the team.
- 4
Provide measurable results to demonstrate the improvement.
- 5
Conclude with what you learned from the experience.
Example Answers
In my previous role, we were facing delays due to manual inspection of dies. I proposed and implemented a semi-automated inspection system. I worked with the team to train them on the new system, which cut our inspection time by 30%, allowing us to increase overall productivity. This experience taught me the value of automation in speeding up processes.
Have you ever taken the lead on a project involving die technology? Describe how you managed the project.
How to Answer
- 1
Begin with a clear overview of the project objectives.
- 2
Highlight your leadership role and decision-making process.
- 3
Discuss the team dynamics and how you facilitated collaboration.
- 4
Mention any technical challenges and how you overcame them.
- 5
Conclude with the project outcome and any measurable results.
Example Answers
In my previous role, I led a project to design a new die for a high-speed production line. The objective was to achieve a 20% increase in efficiency. I organized weekly meetings to ensure the team was aligned and collaborated on solutions to design challenges. We encountered a setback with wear resistance, but I coordinated with suppliers for better materials. Ultimately, we finished the project 2 weeks ahead of schedule and increased production by 25%.
What was a critical skill you learned in your last job as a die technician, and how did it benefit your work?
How to Answer
- 1
Identify a specific skill related to die technology or troubleshooting.
- 2
Explain how you acquired this skill through training or hands-on experience.
- 3
Provide a clear example of how this skill improved your work or efficiency.
- 4
Mention any positive outcomes, such as reduced downtime or improved product quality.
- 5
Keep your answer brief and focused on practical benefits.
Example Answers
In my last role, I learned precision measurement techniques. I acquired this skill through extensive training with calipers and micrometers. This improved my ability to calibrate dies accurately, resulting in a 15% reduction in faulty products and less rework.
Describe a successful project you led that involved die setting up. What were the key factors that made it successful?
How to Answer
- 1
Select a specific project where you played a key role.
- 2
Highlight your specific contributions to die setting up.
- 3
Identify the challenges faced and how you overcame them.
- 4
Mention the metrics that indicate the project's success.
- 5
Conclude with what you learned and how it can apply to future projects.
Example Answers
In my last position, I led a project to set up new dies for a high-volume production line. I coordinated with the design and engineering teams to ensure the dies met specifications. We faced alignment issues initially, but I implemented a new calibration process that reduced setup time by 30%. The project was successful, leading to a 20% increase in productivity.
Can you provide an example of when you suggested a process improvement related to die maintenance or usage?
How to Answer
- 1
Choose a specific improvement you proposed.
- 2
Explain the context and why it was needed.
- 3
Describe your thought process and research.
- 4
Share the outcome and any metrics of success.
- 5
Reflect on how this experience impacted the team or process.
Example Answers
In my previous role, I noticed that our die cleaning process was taking too long, which affected our overall production efficiency. I suggested a new cleaning solution that reduced the time needed by half. After implementing it, our maintenance team reported a significant decrease in downtime related to cleaning, improving our output by 20%.
Situational Interview Questions
Imagine you are faced with a die that has broken down in the middle of a production run. What steps would you take to handle the situation?
How to Answer
- 1
Immediately stop the production to prevent further issues.
- 2
Assess the condition of the die and identify potential causes for the breakdown.
- 3
Communicate with your supervisor or team about the situation.
- 4
Follow standard operating procedures for maintenance and repairs.
- 5
Document the incident and resolution process for future reference.
Example Answers
I would immediately halt production to avoid any damage. Then, I would inspect the die to determine what caused the breakdown before notifying my supervisor. Next, I'd follow the repair procedures outlined in our manual and ensure that everything is documented.
If a client requested a customized die that was outside of standard specifications, how would you approach this challenge?
How to Answer
- 1
Ask the client for detailed specifications and desired outcomes.
- 2
Evaluate the feasibility of the custom die based on materials and processes.
- 3
Suggest alternatives or modifications if the request is too challenging.
- 4
Communicate clearly with the client about timelines and costs.
- 5
Document the agreement and specifications to avoid misunderstandings.
Example Answers
I would start by discussing with the client to get all the necessary details about their requirements and the purpose of the custom die. After that, I would assess whether it is feasible with our current resources and if there are any materials that would work better. If the original request is too complex, I would propose some alternatives that still meet their needs. Finally, I would ensure they are aware of the timeline and costs involved before we proceed.
Don't Just Read Die Technician Questions - Practice Answering Them!
Reading helps, but actual practice is what gets you hired. Our AI feedback system helps you improve your Die Technician interview answers in real-time.
Personalized feedback
Unlimited practice
Used by hundreds of successful candidates
If you notice that a specific die design consistently fails, what steps would you take to innovate a better design?
How to Answer
- 1
Analyze failure data to identify common issues.
- 2
Consult with the team to gather diverse perspectives.
- 3
Research alternative materials or designs used in similar applications.
- 4
Prototype new designs with iterations to test improvements.
- 5
Implement a feedback loop to learn from testing and refine the design.
Example Answers
First, I would analyze the failure data to understand recurring issues. Then, I would discuss with my team to gain insights and brainstorm solutions. Based on that, I'd research better materials that offer improved durability. I would create prototypes and run tests to gauge performance, ensuring we gather feedback at every stage for continuous improvement.
You have multiple deadlines for different die setups. How do you prioritize your tasks effectively?
How to Answer
- 1
List all tasks with their deadlines and requirements
- 2
Assess the impact of each task on production and quality
- 3
Communicate with team members to understand dependencies
- 4
Use a priority matrix to categorize tasks by urgency and importance
- 5
Be prepared to adjust priorities based on feedback or changes in circumstances
Example Answers
I start by listing all my die setups along with their deadlines. I then evaluate which setups impact production the most. I communicate with my team to see if any setups rely on others, and I categorize my tasks based on urgency and importance. This allows me to focus on what's critical first.
What actions would you take if you noticed a safety hazard in the workshop related to die production?
How to Answer
- 1
Immediately assess the hazard to understand its severity.
- 2
Inform your supervisor or the safety officer without delay.
- 3
Take steps to mitigate the risk if it's safe to do so, such as marking the area.
- 4
Document the issue and actions taken for future reference.
- 5
Encourage a culture of safety by sharing the incident with team members.
Example Answers
If I noticed a safety hazard, I would first assess its severity. Then I would immediately inform my supervisor about the hazard so they can take action. If possible, I would mark the area to prevent others from accessing it.
If you discovered that a batch of dies did not meet quality standards after production, what steps would you take?
How to Answer
- 1
Immediately halt further production using the affected dies.
- 2
Conduct a thorough analysis of the defects to identify their cause.
- 3
Document the findings and the extent of the issue.
- 4
Communicate with the quality assurance team and relevant stakeholders.
- 5
Implement corrective actions to prevent future issues.
Example Answers
I would first stop any further production with the faulty dies to prevent more defective products. Then, I would analyze the defects to determine their cause and document everything for future reference. Communication with the QA team is crucial to address the situation, and I would suggest implementing corrective measures based on our findings.
How would you respond to customer feedback indicating that the dies you've produced are not meeting their expectations?
How to Answer
- 1
Acknowledge the customer's feedback immediately and thank them for sharing.
- 2
Ask specific questions to understand the issues they are facing with the dies.
- 3
Take responsibility for any shortcomings and express your commitment to resolve them.
- 4
Discuss your process for analyzing and improving the die manufacturing based on feedback.
- 5
Follow up with the customer after implementing solutions to ensure satisfaction.
Example Answers
Thank you for bringing this to my attention. I appreciate your feedback. Can you share more about the specific issues you've encountered? I take pride in my work, and I’m committed to resolving this. I'll review our processes and make necessary adjustments to meet your expectations.
If you notice that a team member is struggling with their assignment in die production, what would you do?
How to Answer
- 1
Assess the situation to understand the specific challenges they are facing
- 2
Approach them privately to offer support and discuss their difficulties
- 3
Encourage open communication so they feel comfortable sharing their issues
- 4
Suggest practical solutions or resources that could help them improve
- 5
Follow up after your discussion to see if they're making progress
Example Answers
I would first try to understand exactly what challenges my teammate is facing. Then, I would approach them directly to offer my help and discuss any solutions together. I believe that open communication is key, so I would encourage them to share their thoughts with me.
If you're given a limited budget for die production materials, how would you allocate resources effectively?
How to Answer
- 1
Prioritize materials that are essential for the initial production.
- 2
Consider the long-term cost-effectiveness of each material.
- 3
Negotiate with suppliers for discounts or batch purchasing.
- 4
Evaluate alternative materials that meet quality standards but are less expensive.
- 5
Monitor production closely to adjust resource allocation as needed.
Example Answers
I would first assess which materials are crucial for the initial production batch and allocate funds to those. Then, I would explore supplier options to negotiate better pricing to maximize our budget.
How would you handle a situation where a die you produced doesn't comply with industry regulations?
How to Answer
- 1
Acknowledge the issue promptly and professionally
- 2
Investigate the root cause of the non-compliance
- 3
Communicate transparently with your team and supervisors
- 4
Take corrective actions to rectify the situation
- 5
Implement preventive measures to avoid future occurrences
Example Answers
I would immediately acknowledge the compliance issue and investigate the die to determine the cause. After understanding what went wrong, I would inform my supervisor and discuss corrective actions. Then, I would ensure that our process includes steps to prevent similar issues in the future.
Don't Just Read Die Technician Questions - Practice Answering Them!
Reading helps, but actual practice is what gets you hired. Our AI feedback system helps you improve your Die Technician interview answers in real-time.
Personalized feedback
Unlimited practice
Used by hundreds of successful candidates
Die Technician Position Details
Recommended Job Boards
ZipRecruiter
www.ziprecruiter.com/Jobs/Die-TechnicianThese job boards are ranked by relevance for this position.
Related Positions
- Foundry Patternmaker
- Flight Technician
- Air Technician
- Tool Technician
- Database Technician
- Web Technician
- Industrial Technician
- Test Technician
- Technician
- Game Technician
Similar positions you might be interested in.
Ace Your Next Interview!
Practice with AI feedback & get hired faster
Personalized feedback
Used by hundreds of successful candidates
Ace Your Next Interview!
Practice with AI feedback & get hired faster
Personalized feedback
Used by hundreds of successful candidates