Top 30 Industrial Technician Interview Questions and Answers [Updated 2025]
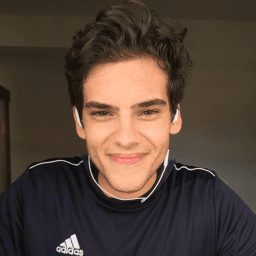
Andre Mendes
•
March 30, 2025
Navigating an interview for an Industrial Technician role can be daunting, but preparation is key to success. In this post, we delve into the most common interview questions encountered in this field, offering thoughtful example answers and invaluable tips to help you respond effectively. Whether you're a seasoned professional or new to the industry, this guide is designed to boost your confidence and enhance your interview skills.
Download Industrial Technician Interview Questions in PDF
To make your preparation even more convenient, we've compiled all these top Industrial Technicianinterview questions and answers into a handy PDF.
Click the button below to download the PDF and have easy access to these essential questions anytime, anywhere:
List of Industrial Technician Interview Questions
Situational Interview Questions
You notice a coworker is not following safety protocols. How would you address the situation?
How to Answer
- 1
Observe the safety violation clearly and ensure it's a legitimate concern
- 2
Approach the coworker privately and express your concerns calmly
- 3
Use 'I' statements to express how it affects the team and safety
- 4
Encourage them to follow protocols and offer assistance if needed
- 5
If the behavior continues, inform a supervisor to ensure safety standards are upheld
Example Answers
I noticed a coworker not using safety gear, so I approached them privately and said, 'I think it’s important we both stay safe, do you need help understanding the protocol?' This way, I raised a concern without confrontation.
Imagine you find a critical piece of machinery has stopped working suddenly. How would you handle the situation?
How to Answer
- 1
Stay calm and assess the situation quickly.
- 2
Check for any visible signs of damage or error indicators.
- 3
Consult the machinery manual for troubleshooting steps.
- 4
If unable to resolve, escalate the issue to a supervisor.
- 5
Document all findings and actions taken for future reference.
Example Answers
First, I would stay calm and quickly assess the machinery for any obvious issues. I would then check for error codes or unusual sounds. If I can't resolve it through quick checks, I would refer to the manual and follow the troubleshooting steps. Should it still be down, I would inform my supervisor immediately and document what I've done.
Don't Just Read Industrial Technician Questions - Practice Answering Them!
Reading helps, but actual practice is what gets you hired. Our AI feedback system helps you improve your Industrial Technician interview answers in real-time.
Personalized feedback
Unlimited practice
Used by hundreds of successful candidates
If you have multiple machines needing maintenance at the same time, how do you prioritize which ones to work on first?
How to Answer
- 1
Assess the impact of each machine on production output.
- 2
Consider downtime costs and urgency of repairs.
- 3
Prioritize machines that are critical for meeting deadlines.
- 4
Evaluate the complexity of repairs needed for each machine.
- 5
Communicate with team members to gather input on priorities.
Example Answers
I prioritize based on production impact. For example, if Machine A is essential for a product line that's due for delivery tomorrow, I would address it first before looking at less critical machines.
How would you respond if there was an emergency shutdown of a facility due to machinery malfunction?
How to Answer
- 1
Stay calm and assess the situation quickly.
- 2
Follow emergency shutdown procedures as outlined in the training.
- 3
Communicate with the team to ensure everyone is aware of the shutdown.
- 4
Identify the cause of the malfunction if safe to do so.
- 5
Document the incident and report to management.
Example Answers
In an emergency shutdown, I would first remain calm and assess what caused the malfunction. I would immediately follow the established emergency procedures to ensure everyone's safety and then communicate the status to my teammates. Once safe, I'd try to identify the issue and document everything for the report.
Suppose you need to train a new technician on a complex piece of equipment. How would you approach this?
How to Answer
- 1
Break down the equipment into manageable parts for easier understanding.
- 2
Use hands-on demonstrations to show how the equipment operates.
- 3
Encourage questions throughout the training process to clarify doubts.
- 4
Provide written materials or manuals for further reference.
- 5
Schedule follow-up sessions to ensure understanding and retention.
Example Answers
I would start by breaking the equipment down into its main components, explaining each part before showing how they work together. After that, I'd demonstrate the operation, allowing the trainee to practice under supervision. I’d encourage them to ask questions as we go along, and provide them with a manual for later reference.
How would you approach identifying and solving inefficiencies in a production line?
How to Answer
- 1
Conduct a thorough observation of the production line to identify bottlenecks.
- 2
Collect data on cycle times, downtime, and output rates to analyze performance.
- 3
Engage with team members to gather insights on pain points and suggestions.
- 4
Implement a trial solution to address identified inefficiencies and monitor results.
- 5
Continuously review processes and solicit feedback to make iterative improvements.
Example Answers
I would begin by observing the production line throughout various shifts to spot any bottlenecks. Next, I'd analyze performance data like cycle times and downtime. Engaging with the workers would give valuable insights, and I would pilot a solution such as adjusting workstations to see if it improves efficiency.
If several urgent maintenance requests come up simultaneously, how do you manage your time effectively?
How to Answer
- 1
Prioritize requests based on urgency and impact on operations
- 2
Communicate with your team to delegate or share workload
- 3
Set a clear timeline for addressing each request
- 4
Use a checklist to track progress and ensure nothing is overlooked
- 5
Maintain a flexible mindset to adjust priorities as needed
Example Answers
I assess each maintenance request by its urgency and the impact on production. I then communicate with my team to see if anyone can assist with lower priority tasks, allowing us to tackle the most critical issues first.
How do you handle being assigned an unexpected project with a tight deadline?
How to Answer
- 1
Stay calm and assess the situation quickly.
- 2
Prioritize tasks based on urgency and importance.
- 3
Communicate with your manager about the resources needed.
- 4
Break the project into smaller tasks to manage workload.
- 5
Keep track of your progress and adjust your plan as needed.
Example Answers
When assigned an unexpected project, I first take a deep breath to stay calm. I quickly assess what needs to be done and prioritize the tasks. I communicate with my manager to ensure I have the resources I need, and I break the project down into smaller, manageable parts.
Imagine you identify a quality issue with a product during the manufacturing process. What steps would you take?
How to Answer
- 1
Immediately halt production to prevent further defects.
- 2
Document the issue with specific details and evidence.
- 3
Communicate the problem to your supervisor and relevant team members.
- 4
Analyze the root cause of the issue with the team.
- 5
Implement corrective actions and monitor results.
Example Answers
First, I would stop the production line to avoid more defective products. Then, I would write down all the details of the quality issue and gather any evidence. Next, I'd inform my supervisor and the quality assurance team to ensure they're aware of the issue. I would then work with the team to analyze the cause of the problem and come up with a corrective plan. Finally, I would implement the solution and keep an eye on the results to make sure it resolves the issue.
A colleague in a remote facility needs support troubleshooting a machine. How would you assist them remotely?
How to Answer
- 1
Ask detailed questions to identify the problem clearly
- 2
Use visual aids like diagrams or manuals to explain solutions
- 3
Guide them through step-by-step troubleshooting over a call or chat
- 4
Encourage them to check specific indicators or settings on the machine
- 5
Offer to stay on the line until the issue is resolved if possible
Example Answers
I would start by asking my colleague to describe the issue in detail, then I would refer to the machine's manual with them, guiding them through the troubleshooting process step-by-step over a call.
Don't Just Read Industrial Technician Questions - Practice Answering Them!
Reading helps, but actual practice is what gets you hired. Our AI feedback system helps you improve your Industrial Technician interview answers in real-time.
Personalized feedback
Unlimited practice
Used by hundreds of successful candidates
Technical Interview Questions
Can you describe your experience with troubleshooting mechanical systems in industrial settings?
How to Answer
- 1
Share specific examples of systems you have worked on.
- 2
Explain the steps you followed during troubleshooting.
- 3
Mention any tools or techniques you used.
- 4
Discuss the outcomes or results of your troubleshooting efforts.
- 5
Highlight any collaboration with team members or engineers.
Example Answers
In my previous role, I worked on conveyor belt systems. When a belt slipped, I systematically checked alignment and tension, using a laser level for precision. I found that a bearing was faulty, replaced it, and improved the system's efficiency by 15%.
What methods do you use to ensure electrical systems are operating safely and efficiently?
How to Answer
- 1
Perform regular inspections to check for signs of wear or damage.
- 2
Use diagnostic tools to monitor and analyze system performance.
- 3
Follow industry safety standards and protocols strictly.
- 4
Keep detailed records of maintenance and any issues encountered.
- 5
Implement energy-saving techniques and updates when needed.
Example Answers
I conduct regular inspections to identify any wear or damage in electrical systems, and I use diagnostic tools to monitor performance and efficiency.
Don't Just Read Industrial Technician Questions - Practice Answering Them!
Reading helps, but actual practice is what gets you hired. Our AI feedback system helps you improve your Industrial Technician interview answers in real-time.
Personalized feedback
Unlimited practice
Used by hundreds of successful candidates
What is your experience with programming and troubleshooting PLCs in an industrial environment?
How to Answer
- 1
Start with your education and relevant certifications in PLC programming.
- 2
Mention specific brands of PLCs you have worked with, such as Allen-Bradley or Siemens.
- 3
Describe a particular project where you programmed or troubleshot a PLC.
- 4
Highlight any challenges faced and how you resolved them.
- 5
Conclude with the results of your work and any improvements achieved.
Example Answers
I have an associate degree in industrial automation and am certified in Allen-Bradley PLC programming. In my last role, I programmed PLCs for a bottling line and successfully troubleshot a recurrent fault in the system, improving the line's efficiency by 20%.
How do you perform diagnostics and repairs on hydraulic systems?
How to Answer
- 1
Start with a systematic approach to diagnostics.
- 2
Use pressure gauges to test hydraulic pressure levels.
- 3
Inspect hoses and fittings for leaks or wear.
- 4
Utilize a multimeter for electrical component checks.
- 5
Follow safety protocols and proper lockout/tagout procedures.
Example Answers
I begin diagnostics by checking the pressure gauges to ensure they are within normal ranges. If there’s an issue, I inspect hoses and fittings for signs of leaks. I also use a multimeter to check the electrical components connected to the hydraulic system.
What steps do you take to develop and implement a preventive maintenance schedule?
How to Answer
- 1
Identify critical equipment that requires maintenance
- 2
Review manufacturer recommendations for maintenance frequency
- 3
Create a detailed checklist of maintenance tasks for each piece of equipment
- 4
Use a maintenance management system to schedule tasks and track completion
- 5
Train the team on the importance of adherence to the maintenance schedule
Example Answers
I start by identifying the key equipment and reviewing the manufacturer’s maintenance guidelines to create a checklist of tasks. Then, I use a maintenance management system to schedule these tasks and ensure the team is trained on their importance.
What experience do you have with calibrating industrial instruments and how do you ensure accuracy?
How to Answer
- 1
Highlight specific instruments you have calibrated
- 2
Discuss the methods or standards you use for calibration
- 3
Mention any tools or equipment used in the calibration process
- 4
Explain how you document and verify the calibration results
- 5
Share an example of a calibration challenge you faced and how you resolved it
Example Answers
I have experience calibrating pressure gauges and flow meters in a manufacturing plant. I follow the manufacturer's calibration procedure, using a calibrated reference instrument for accuracy. I document all results and perform a verification check by comparing readings before and after calibration.
How do you stay updated with industrial safety standards and regulations?
How to Answer
- 1
Follow relevant safety organizations like OSHA and ANSI for updates.
- 2
Subscribe to industry newsletters or journals focusing on industrial safety.
- 3
Participate in workshops or conferences related to safety regulations.
- 4
Engage in online courses or certifications in industrial safety standards.
- 5
Network with peers in the industry to exchange knowledge on safety practices.
Example Answers
I regularly check updates from OSHA and subscribe to their newsletter to stay informed on any new regulations.
What types of welding are you proficient with, and how have you applied them in your work?
How to Answer
- 1
List specific welding techniques you are skilled in, such as MIG, TIG, or Stick welding.
- 2
Provide examples of projects where you used these techniques effectively.
- 3
Highlight any certifications or training related to welding.
- 4
Mention the types of materials you have welded, including steel, aluminum, or composites.
- 5
Discuss any safety practices you follow when welding.
Example Answers
I am proficient in MIG and TIG welding. I applied MIG welding in a recent project where I welded structural steel for a commercial building. I have completed a certified welding course specializing in these techniques.
What is your experience with managing and procuring parts needed for industrial maintenance tasks?
How to Answer
- 1
Highlight specific systems or software you used for inventory management
- 2
Mention any experience with vendor relations or negotiations
- 3
Include examples of parts you managed or procured effectively
- 4
Discuss how you ensured timely availability of parts for maintenance tasks
- 5
Share any cost-saving measures you implemented in procurement
Example Answers
In my previous role as an industrial technician, I used an inventory management system to track and order essential maintenance parts. I built strong relationships with suppliers which helped us negotiate better prices, saving the company about 15% on parts costs.
How do you go about diagnosing and repairing issues in thermal systems such as heat exchangers?
How to Answer
- 1
Start with a visual inspection of the heat exchanger for leaks or corrosion.
- 2
Check operating parameters like inlet and outlet temperatures and pressure drops.
- 3
Use diagnostic tools such as thermal imaging to identify hotspots or uneven heating.
- 4
Review maintenance logs and history to identify recurring issues.
- 5
Isolate the system and conduct pressure tests to find any blockages or failures.
Example Answers
I begin by visually inspecting the heat exchanger for any obvious signs of damage or wear. Next, I measure the inlet and outlet temperatures to check for efficiency losses. If the temperatures are off, I use thermal imaging to locate potential issues. I also review the maintenance history to see if there are patterns in the failures.
Don't Just Read Industrial Technician Questions - Practice Answering Them!
Reading helps, but actual practice is what gets you hired. Our AI feedback system helps you improve your Industrial Technician interview answers in real-time.
Personalized feedback
Unlimited practice
Used by hundreds of successful candidates
Behavioral Interview Questions
Tell me about a time you had to diagnose and solve an unexpected problem with a piece of machinery. What steps did you take?
How to Answer
- 1
Start with a brief description of the machinery and the problem.
- 2
Explain the steps you took to diagnose the issue, including any tools or methods used.
- 3
Discuss how you involved others if needed and communicated the problem.
- 4
Describe the solution you implemented and how you verified it worked.
- 5
Finish with what you learned from the experience and any changes you made to prevent it from happening again.
Example Answers
In my last job, the conveyor belt suddenly stopped. I quickly checked the power supply and found a blown fuse. I replaced the fuse and tested the machinery. It restarted, and I documented the issue for future reference.
Describe a situation where you worked with a team to complete a difficult repair task. What was your role and contribution?
How to Answer
- 1
Choose a specific repair task that was challenging for the team.
- 2
Clearly define your role and the actions you took in the repair process.
- 3
Highlight how you collaborated with others and communicated effectively.
- 4
Mention any tools or techniques you used that were crucial to the repair.
- 5
Conclude with the outcome and what you learned from the experience.
Example Answers
In my previous job, our team faced a breakdown of a critical conveyor system. I was the lead technician responsible for diagnosing the issue. After identifying a faulty motor, I worked closely with two colleagues, collaborating on the disassembly and repair. We used a torque wrench and multimeter to ensure everything was reassembled correctly. The repair was completed ahead of schedule, minimizing downtime by two hours, and I learned the importance of teamwork under pressure.
Don't Just Read Industrial Technician Questions - Practice Answering Them!
Reading helps, but actual practice is what gets you hired. Our AI feedback system helps you improve your Industrial Technician interview answers in real-time.
Personalized feedback
Unlimited practice
Used by hundreds of successful candidates
Describe a time when you had to learn a new technology or process quickly in order to complete your tasks. How did you handle it?
How to Answer
- 1
Pick a specific example from your experience.
- 2
Explain the context briefly to set the stage.
- 3
Highlight the steps you took to learn the new technology.
- 4
Mention any resources or methods you used to accelerate learning.
- 5
Conclude with the outcome and what you learned from the experience.
Example Answers
In my previous job, we implemented a new CNC machine. I had to learn its programming quickly to meet production deadlines. I spent a few hours watching tutorial videos and reached out to our equipment supplier for tips. Within a week, I was programming the machine and increased our output by 20%. This experience taught me the importance of leveraging resources when learning.
Can you give an example of how you've contributed to process improvements in your previous roles?
How to Answer
- 1
Identify a specific process you improved.
- 2
Use the STAR method: Situation, Task, Action, Result.
- 3
Quantify improvements with metrics if possible.
- 4
Emphasize teamwork and collaboration.
- 5
Ensure the example is relevant to the technician role.
Example Answers
At my previous job, we had a slow assembly line. I noticed the team was often waiting for parts. I suggested we implement a pull system for parts management. After tracking our efficiency, we reduced downtime by 30%.
Tell me about a time you had a disagreement with a colleague about a technical solution. How did you handle it?
How to Answer
- 1
Choose a specific situation that shows your conflict-resolution skills.
- 2
Explain the differing opinions clearly but without placing blame.
- 3
Describe the steps you took to resolve the disagreement.
- 4
Highlight any collaboration or compromise that occurred.
- 5
Mention the positive outcome or lesson learned from the situation.
Example Answers
In my last project, a colleague and I disagreed on the best way to implement a machine calibration process. I listened to their reasoning and shared my perspective, focusing on data and results. We decided to run a small test for both approaches. The test showed my solution worked better, and my colleague appreciated the data-driven decision.
Describe a project or initiative you've led in an industrial environment. What were the results?
How to Answer
- 1
Select a specific project where you had a leadership role
- 2
Briefly describe the goal and your role in the project
- 3
Explain the steps you took to achieve the goal
- 4
Highlight the outcomes and impact on the team or company
- 5
Use metrics or improvements to quantify the results if possible
Example Answers
I led a project to optimize our assembly line processes. My role was to coordinate between different teams and implement a new workflow. We reduced our production time by 20%, which improved our overall efficiency and boosted morale.
Give an example of a time when your attention to detail prevented a major problem from occurring.
How to Answer
- 1
Think of a specific situation in your past work experience
- 2
Describe the context and your role in it
- 3
Explain the problem that could have occurred
- 4
Highlight the specific actions you took that showed your attention to detail
- 5
Conclude with the positive outcome that resulted from your actions
Example Answers
In my previous position as a technician, I noticed a discrepancy in the measurements of a component before assembly. I double-checked the specifications and found that the part was incorrectly labeled. By correcting it, I prevented a potential malfunction of the whole system that could have led to costly repairs and downtime.
Describe a situation where you had to communicate technical information to a non-technical audience. How did you ensure understanding?
How to Answer
- 1
Identify a specific situation where you explained technical details.
- 2
Focus on simplifying complex terms into everyday language.
- 3
Use analogies or examples that relate to the audience's experiences.
- 4
Encourage questions to clarify any confusion.
- 5
Check for understanding by asking the audience to summarize what you've explained.
Example Answers
In my previous role, I had to explain a new software system to the sales team. I simplified the technical jargon into basic functions they would use, compared it to a similar tool they were familiar with, and asked them to demonstrate their understanding back to me.
Can you describe a time when you handled a customer complaint or issue effectively?
How to Answer
- 1
Focus on a specific situation where you addressed a customer complaint.
- 2
Explain the steps you took to understand the issue and resolve it.
- 3
Highlight the positive outcome and any feedback received.
- 4
Mention any skills or tools you used in the resolution process.
- 5
Keep it concise and relevant to the technician role.
Example Answers
In my previous role, a customer complained about a malfunctioning piece of equipment. I listened carefully to understand the details and then asked probing questions to gather more information. I quickly diagnosed the issue and provided a temporary fix while ordering the necessary parts. The customer appreciated my prompt response and follow-up, which restored their trust in our services.
Tell me about a time when you proposed a creative solution to a persistent technical problem.
How to Answer
- 1
Choose a specific technical problem you encountered.
- 2
Explain the context and why it was persistent.
- 3
Describe your creative solution and how you arrived at it.
- 4
Discuss the outcome and impact of your solution.
- 5
Keep it clear and focused on your role in the solution.
Example Answers
In my previous role, we faced ongoing issues with a machine frequently jamming during production. I analyzed the process and proposed modifying the feed mechanism to use a more flexible material, which reduced friction. This change decreased downtime by 30%, improving overall efficiency.
Don't Just Read Industrial Technician Questions - Practice Answering Them!
Reading helps, but actual practice is what gets you hired. Our AI feedback system helps you improve your Industrial Technician interview answers in real-time.
Personalized feedback
Unlimited practice
Used by hundreds of successful candidates
Industrial Technician Position Details
Salary Information
Recommended Job Boards
CareerBuilder
www.careerbuilder.com/jobs-industrial-technicianZipRecruiter
www.ziprecruiter.com/Jobs/Industrial-TechnicianThese job boards are ranked by relevance for this position.
Related Positions
Ace Your Next Interview!
Practice with AI feedback & get hired faster
Personalized feedback
Used by hundreds of successful candidates
Ace Your Next Interview!
Practice with AI feedback & get hired faster
Personalized feedback
Used by hundreds of successful candidates