Top 30 Industrial Engineering Technician Interview Questions and Answers [Updated 2025]
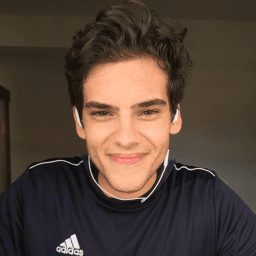
Andre Mendes
•
March 30, 2025
Navigating the interview process for an Industrial Engineering Technician role can be daunting, but preparation is key. In this post, we unveil the most common interview questions for this position, complete with example answers and insightful tips to help you respond effectively. Whether you're a seasoned professional or a newcomer, our guide will equip you with the confidence to tackle any question thrown your way.
Download Industrial Engineering Technician Interview Questions in PDF
To make your preparation even more convenient, we've compiled all these top Industrial Engineering Technicianinterview questions and answers into a handy PDF.
Click the button below to download the PDF and have easy access to these essential questions anytime, anywhere:
List of Industrial Engineering Technician Interview Questions
Technical Interview Questions
What methodologies do you use for analyzing and improving production processes?
How to Answer
- 1
Mention specific methodologies like Lean, Six Sigma, and Kaizen
- 2
Discuss how you collect and analyze data from processes
- 3
Explain how you involve team members in process improvement
- 4
Provide examples of past successes using these methodologies
- 5
Highlight your focus on continuous improvement and efficiency
Example Answers
I typically use Lean and Six Sigma methodologies. For example, in my last role, I collected process data to identify waste, leading to a 20% increase in efficiency.
Explain how you would set up a quality control process for a new manufacturing line.
How to Answer
- 1
Identify key quality metrics for the products being manufactured.
- 2
Develop standard operating procedures (SOPs) that include quality checkpoints.
- 3
Implement a training program for employees on quality standards.
- 4
Choose appropriate inspection tools and techniques for monitoring quality.
- 5
Establish a feedback loop to continuously improve the quality control process.
Example Answers
To set up a quality control process, I would first identify metrics such as defect rates and yield percentages. Then, I'd create SOPs detailing where and how to inspect products. I would ensure employees are trained on these standards and equipped with the right tools like calipers or gauges. Lastly, I'd set up regular reviews to analyze the data and make improvements.
Don't Just Read Industrial Engineering Technician Questions - Practice Answering Them!
Reading helps, but actual practice is what gets you hired. Our AI feedback system helps you improve your Industrial Engineering Technician interview answers in real-time.
Personalized feedback
Unlimited practice
Used by hundreds of successful candidates
How do you apply statistical analysis in your work as an industrial engineering technician?
How to Answer
- 1
Identify specific statistical methods you use regularly.
- 2
Explain how you gather data for your analysis.
- 3
Describe a scenario where statistical analysis improved a process.
- 4
Mention tools or software you use for statistical analysis.
- 5
Connect your statistical findings to decision-making in projects.
Example Answers
I frequently use regression analysis to identify trends in production data. For example, I collected data on cycle times and used regression to predict throughput, which helped us optimize our workflow.
Which CAD software are you proficient in, and how have you used it in your projects?
How to Answer
- 1
Identify the specific CAD software you are proficient in.
- 2
Mention the types of projects you have completed using the software.
- 3
Explain your role and contributions in those projects.
- 4
Highlight any specific features of the software that you used extensively.
- 5
Be ready to discuss the outcomes or benefits of using the software in your projects.
Example Answers
I am proficient in AutoCAD. In my last project, I designed a layout for a manufacturing floor, using features like layering and 3D modeling to optimize space utilization. My contributions helped streamline the workflow, which increased productivity by 20%.
Describe your experience with using data analysis tools to interpret production data.
How to Answer
- 1
Identify specific data analysis tools you have used such as Excel, Python, or specialized software.
- 2
Mention the types of production data you have analyzed, like efficiency, downtime, or quality metrics.
- 3
Explain the methods used in your analysis, such as statistical analysis, trend analysis, or data visualization.
- 4
Share a concrete example where your analysis led to a measurable improvement in production.
- 5
Conclude with how your analysis skills can benefit the prospective employer.
Example Answers
I have used Excel for analyzing production efficiency data over the last year. By creating pivot tables, I identified bottlenecks in our assembly line that led to a 15% increase in throughput.
What is lean manufacturing, and how have you implemented its principles in your work?
How to Answer
- 1
Define lean manufacturing clearly in one sentence
- 2
Mention specific principles like waste reduction or continuous improvement
- 3
Provide a concrete example from your experience
- 4
Explain what results you achieved through implementation
- 5
Highlight your role in the implementation process
Example Answers
Lean manufacturing is a methodology focused on reducing waste and improving processes. In my previous role at a manufacturing company, I applied lean principles by conducting a value stream mapping exercise, which identified bottlenecks. This led to a 15% reduction in lead time by reorganizing the workflow and eliminating unnecessary steps.
How do you ensure that production processes comply with industry regulations and standards?
How to Answer
- 1
Stay updated on relevant industry regulations and standards.
- 2
Implement a checklist for compliance during production.
- 3
Conduct regular training sessions for the production team.
- 4
Perform internal audits to identify and rectify non-compliance.
- 5
Document compliance procedures and keep records for inspection.
Example Answers
I ensure compliance by regularly reviewing industry standards and updating our processes accordingly. We utilize a compliance checklist during production to ensure every step meets regulatory requirements.
What steps do you take to identify the root cause of a recurring issue in the production line?
How to Answer
- 1
Gather data on the issue to understand the frequency and impact.
- 2
Use the 5 Whys technique to explore the problem deeply.
- 3
Involve team members to get different perspectives on the issue.
- 4
Conduct a process flow analysis to identify where things go wrong.
- 5
Test potential solutions on a small scale before full implementation.
Example Answers
To identify the root cause of a recurring issue, I first gather data to see how often it happens and its impact on production. Then, I apply the 5 Whys technique, asking why the issue occurs at each level until we reach the root cause. Involving my team helps bring in different perspectives that might not be obvious at first.
What role do safety protocols play in your work, and how do you ensure they are followed?
How to Answer
- 1
Emphasize the importance of safety in the workplace to protect employees and the company.
- 2
Describe specific safety protocols that are relevant to industrial engineering.
- 3
Explain how you stay informed about safety regulations and updates.
- 4
Give examples of how you personally ensure compliance among team members.
- 5
Discuss any training or workshops you have participated in related to safety protocols.
Example Answers
Safety protocols are critical in my work as they protect both employees and equipment. I prioritize them by conducting regular safety audits and ensuring everyone on the team understands their responsibilities.
Don't Just Read Industrial Engineering Technician Questions - Practice Answering Them!
Reading helps, but actual practice is what gets you hired. Our AI feedback system helps you improve your Industrial Engineering Technician interview answers in real-time.
Personalized feedback
Unlimited practice
Used by hundreds of successful candidates
How have you used automation to enhance production processes?
How to Answer
- 1
Identify a specific automation project you worked on.
- 2
Explain the problem that automation solved.
- 3
Quantify improvements, such as time saved or increased output.
- 4
Mention tools or technologies used in the automation process.
- 5
Discuss any challenges faced and how you overcame them.
Example Answers
In my previous role, I automated the inventory tracking system using barcode scanners and software integration. This reduced manual errors by 30% and sped up the inventory process by 50%.
What is your experience with ISO standards, and how do they impact your role as an industrial engineering technician?
How to Answer
- 1
Mention specific ISO standards you are familiar with
- 2
Explain how these standards apply to your daily work
- 3
Discuss any experience with audits or compliance processes
- 4
Highlight how these standards enhance quality and efficiency
- 5
Share examples of improvement projects you've led or contributed to following ISO guidelines
Example Answers
I have worked with ISO 9001 standards, focusing on quality management. In my role as a technician, I ensure that our processes meet these standards, which improves our overall product quality. For instance, I led an internal audit that identified procedural gaps and implemented corrective actions that increased efficiency by 15%.
Behavioral Interview Questions
Describe a time when you worked as part of a team to improve a production process. What was your role and what was the outcome?
How to Answer
- 1
Start with a clear, specific situation from your experience.
- 2
Explain your role and responsibilities within the team clearly.
- 3
Discuss the actions taken by the team to improve the process.
- 4
Highlight the measurable outcomes or benefits that resulted from the project's success.
- 5
Keep it concise and focus on your contributions.
Example Answers
In my previous role, our team faced a bottleneck in the assembly line. I was responsible for analyzing workflow inefficiencies. We implemented a new layout and introduced standard operating procedures. As a result, we reduced assembly time by 20%, leading to increased output and customer satisfaction.
Can you give an example of a challenging project where you had to solve a significant problem? How did you approach the situation?
How to Answer
- 1
Choose a specific project that had clear challenges.
- 2
Outline the problem you faced in detail.
- 3
Describe the steps you took to analyze and solve the problem.
- 4
Highlight the outcome and what you learned.
- 5
Use metrics or results to quantify your success.
Example Answers
In my last role, I worked on a project to optimize the layout of a manufacturing floor. The challenge was inefficient workflow leading to delays. I gathered data on work patterns and identified bottlenecks, then proposed a new layout. The result was a 20% increase in productivity, and I learned the importance of data-driven decision making.
Don't Just Read Industrial Engineering Technician Questions - Practice Answering Them!
Reading helps, but actual practice is what gets you hired. Our AI feedback system helps you improve your Industrial Engineering Technician interview answers in real-time.
Personalized feedback
Unlimited practice
Used by hundreds of successful candidates
Tell me about a time you identified an inefficiency in a process and took the initiative to improve it.
How to Answer
- 1
Select a specific example from your past experience.
- 2
Describe the context clearly, including the process and its inefficiencies.
- 3
Explain the steps you took to identify and analyze the inefficiency.
- 4
Highlight the actions you implemented to improve the process.
- 5
Conclude with the positive outcome or results of your initiative.
Example Answers
At my previous job, I noticed that our inventory management system caused delays in order fulfillment. I analyzed the process and found that manual entry errors were frequent. I proposed implementing a barcode scanning system, and after integrating it, we reduced errors by 40% and improved our order processing time by 15%.
Have you ever had to explain a complex technical concept to a non-technical audience? How did you ensure they understood it?
How to Answer
- 1
Identify a specific complex concept you explained.
- 2
Use simple language and avoid jargon.
- 3
Use analogies or examples relatable to the audience.
- 4
Check for understanding by asking questions.
- 5
Be patient and ready to clarify points as needed.
Example Answers
In a previous internship, I explained the concept of lean manufacturing to a group of managers. I used the analogy of removing clutter from a desk to represent efficiency. I asked them for their feedback to ensure they grasped the idea.
Describe a situation where you had to adapt quickly to changes in a project. How did you handle it?
How to Answer
- 1
Identify a specific project change you faced.
- 2
Explain the impact of the change on the project.
- 3
Describe the action you took to adapt.
- 4
Highlight the positive outcome of your adaptability.
- 5
Reflect on what you learned from the experience.
Example Answers
In a project to optimize a manufacturing process, we received new specifications that changed material requirements. I quickly reassessed our workflow, coordinated with suppliers, and adjusted our timelines. This led to a successful project finish, and I learned the importance of flexibility in engineering.
Describe an instance where you implemented a continuous improvement strategy in a production process.
How to Answer
- 1
Choose a specific project where you led the improvement.
- 2
Explain the problem you identified and why it was significant.
- 3
Describe the continuous improvement strategy you implemented, like Lean or Six Sigma.
- 4
Include quantitative results or outcomes that demonstrate success.
- 5
Mention how this improved efficiency, reduced costs, or enhanced quality.
Example Answers
In my last role, I noticed that our assembly line was frequently causing delays due to equipment setup times. I implemented a Lean strategy by reorganizing the workspace and standardizing tools, which reduced setup time by 30%, leading to a smoother production flow.
Can you provide an example of a time you led a team through a challenging engineering project?
How to Answer
- 1
Choose a specific project that had clear challenges.
- 2
Explain your leadership role and how you motivated the team.
- 3
Describe the specific actions you took to overcome obstacles.
- 4
Mention any tools or techniques you used to manage the project.
- 5
Conclude with the outcome and what you learned from the experience.
Example Answers
In my previous role, I led a team of 5 on a project to redesign a manufacturing process that was underperforming. We faced issues with delays and quality control. I held daily stand-up meetings to identify challenges and assigned tasks based on team strengths. We implemented a new tracking tool, which improved our communication. As a result, we completed the project 2 weeks ahead of schedule, increasing output by 20%.
Give an example of how you managed your time to meet a tight deadline on a technical project.
How to Answer
- 1
Identify a specific project with a tight deadline
- 2
Explain your planning process
- 3
Discuss prioritization of tasks
- 4
Mention any tools or methods used for time management
- 5
Highlight the outcome and what you learned
Example Answers
In my last project, I was tasked with redesigning a component under a tight deadline. I created a Gantt chart to outline tasks and deadlines. I prioritized the most critical tasks and delegated less important ones. By organizing my time effectively, I completed the redesign ahead of schedule, which allowed for thorough testing.
Have you ever caught a critical mistake in a process or design? How did you spot it, and what was the result?
How to Answer
- 1
Identify a specific mistake you found during a project.
- 2
Explain how you discovered the mistake using data or observation.
- 3
Describe the impact of the mistake on the project or process.
- 4
Discuss any actions you took to correct the issue.
- 5
Highlight the positive outcome or lesson learned from the experience.
Example Answers
In a previous project, I discovered that the calculations for a thermal process were incorrect due to outdated data. I noticed the discrepancy when comparing the results to industry standards. After addressing the mistake, we revised the design, which improved efficiency by 20%.
Situational Interview Questions
Imagine a critical machine has stopped working unexpectedly during production. What steps would you take to address the situation?
How to Answer
- 1
Assess the situation immediately to understand the scope of the problem.
- 2
Check the control panel for error messages or alerts from the system.
- 3
Contact the maintenance team to report the issue and request assistance.
- 4
Implement temporary measures to minimize downtime, if possible.
- 5
Document the incident and the steps taken for future reference.
Example Answers
First, I would assess the situation by checking the machine and control panel for any error messages. Then, I would notify the maintenance team to get their assistance. While waiting for them, I would implement any temporary measures to keep production running as best as possible. Finally, I would document everything for future reference.
You have limited resources to increase production throughput. How would you prioritize and allocate these resources?
How to Answer
- 1
Identify the bottleneck in the production process.
- 2
Evaluate the impact of each resource allocation on throughput.
- 3
Consider both short-term gains and long-term improvements.
- 4
Engage with team members to gather insights on resource needs.
- 5
Implement a trial phase to assess effectiveness before full deployment.
Example Answers
First, I would analyze the production line to identify the bottleneck. Once identified, I would allocate resources primarily to that area, as addressing the bottleneck will yield the highest increase in throughput. Additionally, I would involve my team to understand their needs and gather suggestions for improvement.
Don't Just Read Industrial Engineering Technician Questions - Practice Answering Them!
Reading helps, but actual practice is what gets you hired. Our AI feedback system helps you improve your Industrial Engineering Technician interview answers in real-time.
Personalized feedback
Unlimited practice
Used by hundreds of successful candidates
A client demands higher product quality without increasing costs. How would you approach this challenge?
How to Answer
- 1
Analyze current production processes for inefficiencies
- 2
Engage cross-functional teams to identify quality improvements
- 3
Implement lean manufacturing techniques to reduce waste
- 4
Use quality control metrics to monitor and maintain standards
- 5
Train employees on quality awareness and best practices
Example Answers
I would start by analyzing our current production processes to identify any inefficiencies. Then, I would engage with our quality and operations teams to brainstorm potential improvements. Next, I would implement lean techniques to minimize waste, while also setting up metrics to monitor product quality throughout production.
A team member disagrees with your proposed changes to a process. How would you handle this conflict?
How to Answer
- 1
Listen carefully to the team member's concerns.
- 2
Ask clarifying questions to understand their perspective.
- 3
Present your reasoning and evidence for the proposed changes.
- 4
Encourage a collaborative discussion to explore alternatives.
- 5
Aim for a solution that aligns with team goals and improves the process.
Example Answers
I would first listen to my team member's concerns to understand their perspective. Then, I'd explain my reasoning for the changes and provide any relevant data. Finally, I would suggest we discuss alternatives together to see if we can find a solution that works for both of us.
You are tasked with reducing production time for a product. Outline how you would manage this project from start to finish.
How to Answer
- 1
Identify current production processes and bottlenecks
- 2
Gather data on production times and workflow efficiency
- 3
Collaborate with team members for input and ideas
- 4
Implement improvements using techniques like lean manufacturing
- 5
Monitor results and adjust as necessary
Example Answers
First, I would analyze the current production processes to find bottlenecks. I would collect data on cycle times and workflows. Then, I would involve team members in brainstorming sessions to generate potential solutions. After identifying effective strategies, I would implement lean techniques to reduce waste. Finally, I would track the performance metrics to ensure the changes lead to reduced production time.
During a routine audit, you discover a compliance issue. How would you address it with the team and management?
How to Answer
- 1
Assess the severity of the compliance issue and gather supporting data.
- 2
Communicate the finding to the team promptly and with clarity.
- 3
Suggest a meeting with management to discuss the issue and potential solutions.
- 4
Encourage team members to provide their input on how to resolve the issue.
- 5
Follow up to ensure that corrective actions are implemented and reviewed.
Example Answers
I would first evaluate how serious the compliance issue is, collecting all relevant data before discussing it with my team. Then I would call a brief meeting to inform everyone about the situation clearly and encourage their feedback. Afterward, I would suggest to management that we have a more in-depth discussion to address solutions together.
If tasked with training new employees on a complex process, how would you ensure they understand and apply the process correctly?
How to Answer
- 1
Break down the complex process into simple, clear steps.
- 2
Use visual aids like charts or diagrams to illustrate key concepts.
- 3
Encourage hands-on practice to reinforce learning.
- 4
Ask questions to gauge understanding and address confusion.
- 5
Provide ongoing support and resources for further learning.
Example Answers
I would start by simplifying the complex process into manageable steps and create visual aids to help illustrate each step. I would then encourage new employees to practice the process hands-on while providing immediate feedback and answering any questions they may have.
A client is unhappy with the lead time for their orders. How would you address their concerns and improve their satisfaction?
How to Answer
- 1
Acknowledge the client's frustration and listen to their concerns.
- 2
Ask for specific details about their experience with lead times.
- 3
Explain any internal processes that affect lead times and potential delays.
- 4
Share steps you can take to address their concerns and enhance the process.
- 5
Follow up with the client after implementation to ensure satisfaction.
Example Answers
I would first express understanding of their frustration and ask them to share specific issues they encountered. Then, I would explain our internal processes affecting lead times, propose potential solutions to expedite their orders, and ensure I follow up after the changes to confirm their satisfaction.
You need to design a new process to increase productivity by 20%. What steps would you take to ensure the process meets this goal?
How to Answer
- 1
Conduct a thorough analysis of the current process to identify bottlenecks and inefficiencies
- 2
Engage with team members to gather input and ideas for improvements
- 3
Set clear, measurable objectives for the new process design
- 4
Develop a prototype or pilot of the new process to test its effectiveness
- 5
Monitor performance closely and adjust the process based on feedback and results
Example Answers
First, I would analyze the current process to find bottlenecks and inefficiencies. Then, I'd gather input from team members to brainstorm improvements. After setting clear goals, I'd pilot a new design and monitor its effectiveness to ensure we meet our productivity target.
Industrial Engineering Technician Position Details
Salary Information
Recommended Job Boards
These job boards are ranked by relevance for this position.
Related Positions
Ace Your Next Interview!
Practice with AI feedback & get hired faster
Personalized feedback
Used by hundreds of successful candidates
Ace Your Next Interview!
Practice with AI feedback & get hired faster
Personalized feedback
Used by hundreds of successful candidates