Top 30 Industrial Engineering Technologist Interview Questions and Answers [Updated 2025]
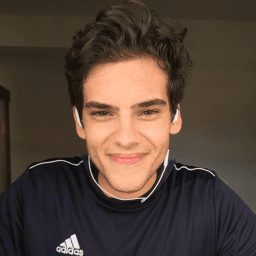
Andre Mendes
•
March 30, 2025
Navigating the interview process for an Industrial Engineering Technologist position can be daunting, but preparation is key to success. In this post, you'll find a comprehensive collection of the most common interview questions for this role, complete with example answers and actionable tips to help you respond effectively. Dive in to boost your confidence and enhance your readiness for your next career opportunity!
Download Industrial Engineering Technologist Interview Questions in PDF
To make your preparation even more convenient, we've compiled all these top Industrial Engineering Technologistinterview questions and answers into a handy PDF.
Click the button below to download the PDF and have easy access to these essential questions anytime, anywhere:
List of Industrial Engineering Technologist Interview Questions
Technical Interview Questions
How do you ensure quality control in industrial processes?
How to Answer
- 1
Implement statistical quality control methods to monitor processes.
- 2
Conduct regular audits and inspections of production processes.
- 3
Utilize process capability analysis to identify areas for improvement.
- 4
Encourage a culture of quality among all employees.
- 5
Use feedback loops to incorporate changes based on quality assessments.
Example Answers
I ensure quality control by implementing statistical process control charts to monitor key metrics. Regular audits help identify deviations early.
Why is process documentation important and how do you ensure it's maintained?
How to Answer
- 1
Explain that process documentation ensures consistency and quality in work.
- 2
Mention the role of documentation in training new employees and onboarding.
- 3
Highlight how it aids in process improvement and troubleshooting.
- 4
Discuss methods for maintaining documentation like regular reviews.
- 5
Emphasize the importance of involving team members in documenting processes.
Example Answers
Process documentation is vital because it promotes consistency and ensures every team member performs tasks the same way. I maintain it by scheduling regular reviews and encouraging the team to update documents whenever changes occur.
Don't Just Read Industrial Engineering Technologist Questions - Practice Answering Them!
Reading helps, but actual practice is what gets you hired. Our AI feedback system helps you improve your Industrial Engineering Technologist interview answers in real-time.
Personalized feedback
Unlimited practice
Used by hundreds of successful candidates
What techniques do you use to implement lean manufacturing principles within the production process?
How to Answer
- 1
Identify specific lean tools such as 5S, Kaizen, or Value Stream Mapping that you have used.
- 2
Provide examples of how you analyzed waste and identified improvement areas in production.
- 3
Discuss how you involve team members in the lean process to foster a culture of continuous improvement.
- 4
Mention measurable outcomes or results achieved through your lean initiatives.
- 5
Emphasize your understanding of the cycle of Plan-Do-Check-Act (PDCA) in implementing lean changes.
Example Answers
I regularly use 5S to maintain a clean and organized workspace. For example, in my last position, I led a 5S initiative that reduced downtime by 15%.
What tools and methods do you use for data analysis to improve industrial processes?
How to Answer
- 1
Identify specific tools you are familiar with, such as Excel, Python, or specialized software like Minitab.
- 2
Mention quantitative methods like statistical analysis, regression analysis, or Six Sigma techniques.
- 3
Discuss qualitative methods like value stream mapping or root cause analysis if applicable.
- 4
Provide a brief example of a project where you applied these tools or methods to achieve measurable improvements.
- 5
Emphasize your adaptability to learning new tools and methods as needed.
Example Answers
I regularly use Excel for data analysis, employing pivot tables and statistical functions to analyze process performance. In my last project, I utilized Six Sigma techniques to reduce waste in a production line, achieving a 15% improvement in efficiency.
Explain your approach to process optimization. How do you identify areas for improvement?
How to Answer
- 1
Start with defining what process optimization means in your context.
- 2
Discuss specific tools or methodologies you use for analysis, like Lean or Six Sigma.
- 3
Mention how you collect and analyze data to identify inefficiencies.
- 4
Talk about involving team members for insights and suggestions.
- 5
Describe a past experience where you successfully optimized a process.
Example Answers
In my view, process optimization involves streamlining workflows to reduce waste and increase efficiency. I often use Lean methodologies and conduct value stream mapping to identify bottlenecks. By analyzing cycle times and collecting data through team feedback, I pinpoint areas needing improvement. For example, in my last role, I reduced processing time by 30% by restructuring the workflow based on team suggestions.
What is your experience with CAD software? How have you used it in previous projects?
How to Answer
- 1
Identify specific CAD software you are proficient in.
- 2
Mention projects where you applied CAD software effectively.
- 3
Describe your role and contributions in using the software.
- 4
Highlight any specific features of the software that you utilized.
- 5
Emphasize the outcomes or benefits of your CAD work.
Example Answers
I have extensive experience with AutoCAD, which I used in my last project to design layouts for a manufacturing facility. I was responsible for creating detailed blueprints that improved the workflow efficiency by 20%.
How do you integrate supply chain management with production planning?
How to Answer
- 1
Understand the flow of materials from suppliers to production.
- 2
Align inventory levels with production schedules to ensure availability.
- 3
Use forecasting to predict demand and adjust production plans accordingly.
- 4
Implement communication between supply chain and production teams regularly.
- 5
Utilize software tools to track both supply chain and production metrics.
Example Answers
I integrate supply chain management with production planning by aligning our inventory levels with our production schedules to ensure we have the necessary materials on hand when needed. Additionally, I use demand forecasting to adjust our production plans based on what we expect to sell.
What project management methodologies do you apply in your engineering projects?
How to Answer
- 1
Identify specific methodologies you've used, such as Agile, Waterfall, or Lean.
- 2
Explain how you apply these methodologies in your projects.
- 3
Share an example of a project where a particular methodology led to success.
- 4
Mention any certifications or training you've received related to these methodologies.
- 5
Discuss how you adapt methodologies to fit the project's needs.
Example Answers
In my recent project for process optimization, I applied Lean methodologies to eliminate waste and streamline operations. This approach resulted in a 20% increase in efficiency.
How do you evaluate the potential benefits of automation in an industrial setting?
How to Answer
- 1
Identify specific areas where automation can improve efficiency.
- 2
Consider cost savings and return on investment from automated solutions.
- 3
Evaluate the impact on workforce and skills required for operating automated systems.
- 4
Assess how automation aligns with overall business goals and productivity.
- 5
Use data and case studies to support your evaluation.
Example Answers
I evaluate potential benefits of automation by identifying processes that are labor-intensive and could gain efficiency from automation. I look at the cost savings versus the initial investment and how it impacts productivity. For example, automating a packaging line can reduce labor costs while increasing throughput.
What safety standards and practices are important in industrial engineering environments?
How to Answer
- 1
Identify key safety regulations such as OSHA standards and ANSI guidelines.
- 2
Discuss the importance of risk assessments and hazard identification in workflows.
- 3
Highlight training programs and their role in maintaining safety awareness.
- 4
Explain the significance of proper personal protective equipment (PPE) usage.
- 5
Mention the need for regular safety audits and continuous improvement practices.
Example Answers
Key safety standards in industrial engineering include OSHA regulations that ensure a safe work environment. Regular risk assessments help identify hazards, and training programs raise safety awareness among employees.
Don't Just Read Industrial Engineering Technologist Questions - Practice Answering Them!
Reading helps, but actual practice is what gets you hired. Our AI feedback system helps you improve your Industrial Engineering Technologist interview answers in real-time.
Personalized feedback
Unlimited practice
Used by hundreds of successful candidates
What statistical methods do you find most useful in industrial engineering?
How to Answer
- 1
Identify key statistical methods relevant to industrial engineering.
- 2
Explain how you have applied these methods in past projects.
- 3
Discuss the impact of these methods on decision-making and efficiency.
- 4
Be prepared to mention specific software or tools used for these methods.
- 5
Convey examples of successful outcomes due to effective statistical analysis.
Example Answers
I find regression analysis particularly useful in industrial engineering, especially when predicting outcomes based on variable inputs. For instance, I used regression to optimize production schedules, which reduced lead time by 15%.
What strategies do you use to reduce costs in manufacturing processes?
How to Answer
- 1
Identify key areas of waste in the process
- 2
Implement lean manufacturing principles
- 3
Utilize process automation where feasible
- 4
Negotiate with suppliers for better prices
- 5
Invest in employee training to improve efficiency
Example Answers
I focus on identifying waste through value stream mapping, which helps me eliminate non-value-added activities. Recently, I implemented a lean initiative that reduced our cycle time by 15%.
Behavioral Interview Questions
Describe a time when you worked as part of a team to improve a production process. What was your role, and what was the outcome?
How to Answer
- 1
Select a specific project where teamwork was key.
- 2
Clearly define your role in the team and your contributions.
- 3
Highlight the process improvements made and how they were implemented.
- 4
Mention measurable outcomes, such as efficiency gains or cost reductions.
- 5
Use the STAR method: Situation, Task, Action, Result.
Example Answers
In my last internship, our team aimed to reduce waste in the assembly line. I was responsible for analyzing data and identifying bottlenecks. We implemented a new workflow that decreased waste by 15%, boosting overall efficiency by 10%.
Can you give an example of a time you identified a bottleneck in a process and how you resolved it?
How to Answer
- 1
Identify the process and the specific bottleneck you noticed.
- 2
Explain the impact of the bottleneck on the overall performance.
- 3
Describe the steps you took to analyze and resolve the bottleneck.
- 4
Highlight any tools or methodologies used in the resolution.
- 5
Share the outcome and any measurable improvements that resulted.
Example Answers
In my previous role, I noticed that our assembly line was frequently halted due to delays in parts supply. This bottleneck was causing a 20% slowdown in our output. I conducted a root cause analysis and discovered that our supplier had inconsistent delivery times. I proposed adjusting our inventory strategy and switched to a more reliable supplier. As a result, our production efficiency improved by 30%.
Don't Just Read Industrial Engineering Technologist Questions - Practice Answering Them!
Reading helps, but actual practice is what gets you hired. Our AI feedback system helps you improve your Industrial Engineering Technologist interview answers in real-time.
Personalized feedback
Unlimited practice
Used by hundreds of successful candidates
Tell me about a time when you had to lead a project or initiative. How did you ensure its success?
How to Answer
- 1
Choose a specific project where you took the lead
- 2
Describe your role and responsibilities clearly
- 3
Highlight key actions you took to ensure success
- 4
Mention any challenges faced and how you overcame them
- 5
Focus on the results and what you learned from the experience
Example Answers
In my last role, I led a team to improve the efficiency of our production line. I initiated a lean manufacturing project, developed a plan, and coordinated with team members. By conducting regular meetings and gathering feedback, we were able to reduce downtime by 20%. This experience taught me the importance of communication and team engagement.
Give an example of a time you had to explain complex data or ideas to stakeholders. How did you approach it?
How to Answer
- 1
Choose a specific situation where you simplified complex information.
- 2
Focus on the audience's level of understanding and tailor your explanation.
- 3
Use visuals or analogies to make the information more relatable.
- 4
Highlight the outcome and how it benefited the stakeholders.
- 5
Be concise and clear, avoiding technical jargon.
Example Answers
In my previous role, I needed to explain a complex manufacturing process to a group of non-technical managers. I created a flowchart that visually represented each step, breaking down the process into simple terms. By using analogies related to common everyday tasks, I made sure everyone understood it clearly, which helped us streamline operations based on their feedback.
Describe a situation where there was a conflict within your team. How did you handle it?
How to Answer
- 1
Identify the specific conflict clearly and concisely.
- 2
Explain your role in the situation and the steps you took to resolve it.
- 3
Highlight the importance of communication and collaboration.
- 4
Discuss the outcome and what you learned from the experience.
- 5
Make sure to reflect on how this improved team dynamics.
Example Answers
In a recent project, two team members disagreed on the best approach to optimize a process. I facilitated a meeting where both could present their views, encouraging an open dialogue. We combined elements from both proposals, which enhanced our final solution and strengthened our team's collaboration. I learned the value of mediating conflicts through communication.
Tell me about a time you had to quickly adapt to changes in a project scope or timeline. How did you manage the change?
How to Answer
- 1
Identify a specific project where change occurred.
- 2
Briefly describe the original scope and the changes made.
- 3
Explain your immediate reaction and steps taken to adapt.
- 4
Highlight any collaboration with team members or stakeholders.
- 5
Conclude with the successful outcome or what you learned.
Example Answers
In my last project, we were developing a production line layout when suddenly we were informed of a tight deadline. I quickly gathered the team to reassess our priorities and devise a streamlined plan. We redesigned the layout to fit the new timeline while ensuring that all safety standards were met. Through effective communication, we completed the project on time and received positive feedback from management.
Describe a time when you implemented a continuous improvement initiative. What challenges did you face?
How to Answer
- 1
Talk about a specific project or initiative that you led or contributed to
- 2
Outline the steps you took during the implementation process
- 3
Mention measurable results or improvements that were achieved
- 4
Discuss specific challenges you faced and how you overcame them
- 5
Explain what you learned from the experience and how it shaped your approach to continuous improvement
Example Answers
At my previous job, I noticed that our assembly line had frequent bottlenecks. I led a project to reorganize the layout, reducing cycle time by 20%. Our main challenge was resistance from some team members, but through regular meetings, I addressed their concerns and involved them in the solution. Ultimately, the new layout improved overall efficiency and teamwork.
How have you managed your time effectively to meet multiple deadlines in the past?
How to Answer
- 1
Prioritize tasks based on deadlines and importance
- 2
Use a calendar or task management tool to track deadlines
- 3
Break projects into smaller, manageable tasks
- 4
Set specific goals for each work session
- 5
Review and adjust your schedule regularly to stay on track
Example Answers
In my last project, I prioritized tasks by deadlines. I used a digital calendar to visualize my workload. This helped me focus on critical tasks first, which allowed me to submit all parts of the project on time without any last-minute rush.
Situational Interview Questions
You notice a production line is consistently failing to meet output targets. What steps would you take to diagnose and resolve the issue?
How to Answer
- 1
Observe the production line to identify bottlenecks and inefficiencies.
- 2
Collect data on output, downtime, and operations to understand performance metrics.
- 3
Engage with operators to gather insights on pain points and issues they face.
- 4
Analyze the workflow and assess if any equipment is malfunctioning or needs maintenance.
- 5
Recommend changes based on findings, such as process improvements or additional training.
Example Answers
First, I would observe the production line closely to identify any visible bottlenecks. I would then gather data on output rates and downtime incidents to pinpoint trends. By discussing with operators, I can learn about any recurring issues. Lastly, I would analyze the workflow for inefficiencies and suggest targeted improvements.
You have been given a project to improve efficiency but have limited resources. How would you prioritize your efforts?
How to Answer
- 1
Identify the key areas where efficiency can have the most impact
- 2
Conduct a quick analysis of current processes to find bottlenecks
- 3
Engage stakeholders to gather input on priorities and pain points
- 4
Focus on low-cost, high-impact improvements first
- 5
Set clear, measurable goals to track progress
Example Answers
I would start by analyzing current processes to identify major bottlenecks and inefficiencies. After that, I would gather input from stakeholders to understand which areas they feel are most critical. Then, I would prioritize low-cost, quick improvements that could yield immediate results, while setting measurable goals to track our progress.
Don't Just Read Industrial Engineering Technologist Questions - Practice Answering Them!
Reading helps, but actual practice is what gets you hired. Our AI feedback system helps you improve your Industrial Engineering Technologist interview answers in real-time.
Personalized feedback
Unlimited practice
Used by hundreds of successful candidates
An essential piece of equipment has failed unexpectedly. How would you handle this situation to minimize disruption?
How to Answer
- 1
Assess the situation immediately to understand the impact.
- 2
Communicate with the team about the failure and its implications.
- 3
Identify alternative solutions or backup equipment.
- 4
Coordinate with maintenance or technical support for repairs.
- 5
Document the incident for future reference and learning.
Example Answers
I would first assess the situation to determine which operations are affected. I would then inform my team about the issue to ensure everyone is aware. If possible, I would look for temporary solutions or backup equipment to continue operations while maintenance is called. Finally, I would follow up on the repair process and document the incident.
You're presenting a process change that has both risks and benefits. How would you communicate this to skeptical stakeholders?
How to Answer
- 1
Clearly outline both risks and benefits in a balanced manner
- 2
Use data and case studies to support your claims
- 3
Address potential concerns directly by anticipating questions
- 4
Highlight the long-term advantages that outweigh the risks
- 5
Engage stakeholders by inviting their input and feedback on the proposal
Example Answers
I would prepare a presentation that lists the benefits of the process change, backed by data from similar implementations. I would also acknowledge the risks, propose mitigation strategies, and encourage stakeholders to share their concerns.
A decision has been made to implement lean practices across the plant. What is your approach to ensure a smooth implementation?
How to Answer
- 1
Engage stakeholders early to gather input and foster buy-in.
- 2
Conduct training sessions to educate employees about lean principles.
- 3
Develop clear metrics to measure the success of lean initiatives.
- 4
Create a pilot project to test lean practices before full implementation.
- 5
Establish regular feedback loops and adjust plans based on observations.
Example Answers
I would start by involving key stakeholders to understand their concerns and suggestions. Then, I'd organize training sessions to familiarize the staff with lean concepts. After setting performance metrics, I'd initiate a pilot project to apply lean methods in a controlled area. Finally, I would collect feedback and refine our approach for broader deployment.
The company is considering adopting a new technology to increase productivity. How would you evaluate this technology and its potential impact?
How to Answer
- 1
Identify key performance metrics important for productivity.
- 2
Conduct a cost-benefit analysis comparing the new technology to current methods.
- 3
Gather data from pilot tests or case studies of similar technology in use.
- 4
Engage stakeholders to understand their needs and concerns.
- 5
Assess the scalability and compatibility of the technology with existing systems.
Example Answers
I would start by identifying metrics like production speed and error reduction. Then, I'd perform a cost-benefit analysis comparing these metrics to our current technology. Additionally, I would look for case studies where the technology has been successfully implemented elsewhere.
How would you manage multiple projects with competing deadlines to ensure all are completed successfully?
How to Answer
- 1
Prioritize projects based on urgency and importance
- 2
Break projects into smaller tasks with specific deadlines
- 3
Use project management tools to track progress and deadlines
- 4
Communicate regularly with stakeholders about project statuses
- 5
Stay organized and review your schedule daily to adjust plans
Example Answers
I prioritize projects by assessing deadlines and their impact. I then break them down into smaller tasks, allowing me to stay on track and adjust if needed. I regularly update my team on progress to ensure transparency.
Midway through a project, new environmental regulations impact your design. How do you address these constraints?
How to Answer
- 1
Evaluate the new regulations thoroughly to understand requirements
- 2
Assess the impact on the current design and identify necessary changes
- 3
Collaborate with the team to brainstorm possible adjustments
- 4
Prioritize compliance while minimizing cost and delays
- 5
Communicate changes to stakeholders early and seek their input
Example Answers
I would first review the new regulations in detail to understand how they affect our current design. Then, I would assess the impact and work with the team to identify practical adjustments we could make to comply while keeping the project on track.
You need to adjust a process based on changing customer requirements. How do you proceed without affecting current operations?
How to Answer
- 1
Identify and prioritize the new customer requirements.
- 2
Analyze the current process to find areas of flexibility.
- 3
Engage with stakeholders to gather their perspectives.
- 4
Develop a plan for implementation that includes testing phases.
- 5
Communicate changes clearly to all involved parties.
Example Answers
First, I would assess the new customer requirements and determine their priority. Then, I'd analyze our current processes to identify any areas that can be adjusted without disruption. Engaging with the team and relevant stakeholders ensures we are aligned. Following that, I would create a detailed plan that allows for gradual testing, mitigating risks to current operations.
Industrial Engineering Technologist Position Details
Salary Information
Recommended Job Boards
These job boards are ranked by relevance for this position.
Related Positions
Ace Your Next Interview!
Practice with AI feedback & get hired faster
Personalized feedback
Used by hundreds of successful candidates
Ace Your Next Interview!
Practice with AI feedback & get hired faster
Personalized feedback
Used by hundreds of successful candidates