Top 30 Production Technician Interview Questions and Answers [Updated 2025]
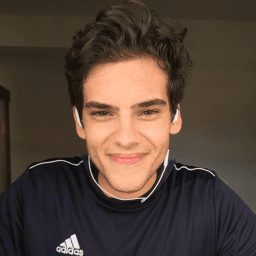
Andre Mendes
•
March 30, 2025
Preparing for a production technician interview can be daunting, but we're here to make it easier. In this post, you'll find the most common interview questions for the production technician role, complete with example answers and insightful tips on crafting your responses effectively. Whether you're a seasoned professional or a newcomer, this guide is designed to help you confidently tackle your next interview.
Download Production Technician Interview Questions in PDF
To make your preparation even more convenient, we've compiled all these top Production Technicianinterview questions and answers into a handy PDF.
Click the button below to download the PDF and have easy access to these essential questions anytime, anywhere:
List of Production Technician Interview Questions
Behavioral Interview Questions
Can you describe a time when you collaborated with a cross-functional team to improve the production process?
How to Answer
- 1
Choose a specific project where you worked with different departments.
- 2
Explain the roles of the team members involved and your contribution.
- 3
Discuss the issue with the production process and the steps taken to resolve it.
- 4
Highlight the outcome and any measurable improvements.
- 5
Reflect on what you learned from the collaboration.
Example Answers
In my previous role, I worked with the quality assurance, engineering, and supply chain teams to address a recurring issue with product defects. I coordinated meetings, gathered data from each team, and we identified the root cause linked to a supplier's material. By changing our supplier, we reduced defects by 40% in just three months.
Tell me about a time when you had to lead a team through a challenging production problem.
How to Answer
- 1
Start with the context of the production problem.
- 2
Explain your role and how you took charge.
- 3
Describe the actions you implemented to resolve the issue.
- 4
Share the outcome and what you learned from the experience.
- 5
Highlight teamwork and communication as key factors.
Example Answers
During a product launch, we faced a supply chain delay that jeopardized our timeline. I organized daily stand-up meetings to assess progress, reallocated resources, and communicated transparently with stakeholders. We ultimately met our deadline and learned the importance of flexibility and proactive communication.
Don't Just Read Production Technician Questions - Practice Answering Them!
Reading helps, but actual practice is what gets you hired. Our AI feedback system helps you improve your Production Technician interview answers in real-time.
Personalized feedback
Unlimited practice
Used by hundreds of successful candidates
Describe a situation where you had to troubleshoot a persistent production issue. What approach did you take and what was the outcome?
How to Answer
- 1
Identify the specific issue clearly
- 2
Explain the steps you took to diagnose the problem
- 3
Discuss how you collaborated with team members or departments
- 4
Highlight the tools or methods you used for troubleshooting
- 5
Conclude with the resolution and any lessons learned
Example Answers
In a recent project, we faced a recurring downtime issue due to server overload. I first gathered logs to isolate the peak times of failure, then collaborated with the engineering team. We discovered that the load balancing was misconfigured, and after adjusting the settings, we reduced downtime by 90%. This taught me the importance of thorough log analysis.
Give an example of how you handled a disagreement within your production team.
How to Answer
- 1
Identify the specific disagreement clearly
- 2
Describe your approach to facilitate discussion
- 3
Share the steps you took to resolve the issue
- 4
Emphasize the outcome and what you learned
- 5
Highlight teamwork and collaboration in the resolution
Example Answers
In a recent project, our team disagreed on the direction of the design. I organized a meeting where everyone could voice their opinions. After discussing each perspective, we focused on the project goals and agreed on a compromise that satisfied both sides. This not only resolved the issue but also strengthened our team's collaboration.
Describe a time when you had to juggle multiple production-related tasks. How did you manage your time effectively?
How to Answer
- 1
Identify specific tasks you managed simultaneously
- 2
Explain the prioritization method you used
- 3
Discuss any tools or techniques that helped you stay organized
- 4
Mention any team collaboration or communication that improved efficiency
- 5
Reflect on the outcome and what you learned from the experience
Example Answers
In my previous role, we had a tight schedule for launching three products. I listed each task, prioritized them based on deadlines, and used project management software to track progress. I held daily stand-up meetings with the team to ensure we were aligned. This approach resulted in successfully launching all products on time, and I learned the importance of clear communication.
Tell me about a situation where you had to adapt to a significant change in the production process.
How to Answer
- 1
Think of a specific change that challenged you.
- 2
Explain the context and the reason for the change.
- 3
Describe the steps you took to adapt to the change.
- 4
Share the outcome and what you learned from the experience.
- 5
Highlight your flexibility and problem-solving skills.
Example Answers
In my previous role, we switched from manual assembly to automated processes. Initially, I was unsure about the new machinery, but I took initiative by attending training sessions and collaborating with the tech team. As a result, I became proficient in using the equipment and helped train my teammates, leading to a smoother transition and improved efficiency.
Have you ever coached a less experienced team member in a production setting? What was your approach?
How to Answer
- 1
Describe a specific situation you faced when coaching.
- 2
Highlight the techniques you used to facilitate learning.
- 3
Mention the tools or resources you provided to support their growth.
- 4
Share the outcome of your coaching efforts.
- 5
Reflect on what you learned from the experience.
Example Answers
Yes, I coached a new operator who struggled with machine settings. I first observed their workflow, then provided direct feedback and demonstrated the correct settings. I also created a quick-reference guide for them. As a result, their efficiency improved by 20% within a month.
Technical Interview Questions
What strategies do you use to analyze and improve production efficiency?
How to Answer
- 1
Identify key performance indicators to measure efficiency
- 2
Conduct regular audits to find bottlenecks in production
- 3
Implement lean manufacturing principles to reduce waste
- 4
Use data analytics tools to track production metrics
- 5
Encourage team feedback for continuous improvement
Example Answers
I focus on key performance indicators like cycle time and throughput. Regular audits help me identify bottlenecks, and I apply lean principles to minimize waste.
How do you apply lean manufacturing principles to reduce waste in production?
How to Answer
- 1
Identify the key types of waste in production: overproduction, waiting, transport, extra processes, inventory, motion, and defects.
- 2
Use value stream mapping to analyze current processes and identify wasteful steps.
- 3
Implement 5S methodology to ensure a clean and organized workspace that reduces clutter and improves efficiency.
- 4
Encourage a culture of continuous improvement where all employees are empowered to suggest improvements.
- 5
Apply just-in-time production principles to align production closely with customer demand.
Example Answers
I apply lean manufacturing by using value stream mapping to pinpoint areas where time and resources are wasted, such as unnecessary transport steps. Then, I implement 5S to maintain an organized environment that prevents waste.
Don't Just Read Production Technician Questions - Practice Answering Them!
Reading helps, but actual practice is what gets you hired. Our AI feedback system helps you improve your Production Technician interview answers in real-time.
Personalized feedback
Unlimited practice
Used by hundreds of successful candidates
Can you explain the key steps in establishing an effective quality control process?
How to Answer
- 1
Define quality standards based on product requirements
- 2
Implement a process for regular quality assessments
- 3
Train staff on quality control procedures and standards
- 4
Utilize tools for tracking and analyzing quality data
- 5
Continuously improve the process based on feedback and results
Example Answers
To establish an effective quality control process, first, we need to define clear quality standards based on the specific requirements of the product. Next, we implement regular quality assessments to check if the products meet those standards. We also train our staff thoroughly on these procedures. Using tools to track quality data helps us analyze any issues. Finally, we focus on continuous improvement by using feedback from our assessments.
How do you manage supply chain challenges to ensure timely production?
How to Answer
- 1
Identify key supply chain risks and develop contingency plans.
- 2
Maintain strong relationships with suppliers for better communication.
- 3
Use data analytics to forecast demand and adjust orders accordingly.
- 4
Implement just-in-time inventory practices to reduce excess stock.
- 5
Regularly review and optimize logistics and transportation processes.
Example Answers
I manage supply chain challenges by identifying potential risks early and creating detailed contingency plans. I also maintain strong relationships with suppliers to ensure open communication, which allows us to adapt quickly when issues arise.
What safety standards are essential in a production environment, and how do you ensure compliance?
How to Answer
- 1
Identify key safety standards relevant to production, such as OSHA regulations or ISO 45001.
- 2
Discuss training programs for employees on safety protocols.
- 3
Highlight regular safety audits and inspections to ensure compliance.
- 4
Mention the importance of reporting and addressing safety incidents immediately.
- 5
Explain how to create a safety culture within the team.
Example Answers
In a production environment, essential safety standards include OSHA regulations and ISO 45001. I ensure compliance by implementing regular safety training for all employees, conducting audits every quarter, and fostering an open culture where team members can report safety concerns without fear.
How do you handle inventory control to balance stock levels without overproducing?
How to Answer
- 1
Regularly analyze sales data to forecast demand accurately
- 2
Implement a just-in-time inventory system to reduce excess stock
- 3
Utilize inventory management software to track stock levels in real-time
- 4
Communicate with suppliers for flexibility in orders based on demand
- 5
Establish safety stock levels to prevent stockouts while avoiding overstock.
Example Answers
I analyze historical sales data weekly to forecast demand, adjusting inventory levels accordingly. This ensures we maintain optimal stock without overproduction.
What role does automation play in your production strategy, and how do you determine which processes to automate?
How to Answer
- 1
Identify key areas where automation increases efficiency
- 2
Consider the cost-benefit ratio of automation
- 3
Analyze repetitive tasks that consume significant time
- 4
Evaluate the impact of automation on quality and throughput
- 5
Stay updated on technology trends to recognize new automation opportunities
Example Answers
Automation is crucial in my production strategy as it allows us to streamline repetitive tasks and improve overall efficiency. We focus on automating processes like data entry and inventory management, which are time-consuming and prone to human error. The decision to automate is based on a thorough cost-benefit analysis to ensure that the investment yields a positive return.
Describe how you manage production costs while maintaining quality.
How to Answer
- 1
Identify and analyze key cost drivers in production.
- 2
Implement lean manufacturing techniques to eliminate waste.
- 3
Regularly train employees to improve efficiency and skill levels.
- 4
Maintain transparent communication with suppliers for better pricing.
- 5
Conduct regular quality checks to ensure standards are met without excess rework.
Example Answers
I manage production costs by analyzing labor and material costs closely. By implementing lean manufacturing techniques, we identified and eliminated waste, saving 15% even while keeping product quality high. Regular skills training for staff also improved efficiency.
What experience do you have with ERP systems in managing production data?
How to Answer
- 1
Identify specific ERP systems you have worked with.
- 2
Mention your role and responsibilities involving production data.
- 3
Provide examples of how you used ERP for data management.
- 4
Discuss any improvements or efficiencies gained through your work.
- 5
Emphasize your knowledge of production planning and inventory control.
Example Answers
I have extensive experience with SAP ERP, where I managed production data to ensure accurate inventory levels and streamline production scheduling. In my last role, I implemented a process that reduced data entry errors by 30%.
How do you use production forecasting to improve operational planning?
How to Answer
- 1
Analyze historical data to identify trends and seasonal patterns.
- 2
Collaborate with sales to incorporate their insights into forecasts.
- 3
Use forecasting tools and software to generate accurate predictions.
- 4
Monitor and adjust forecasts regularly based on real-time data.
- 5
Align production schedules with forecasted demand to minimize waste.
Example Answers
I analyze past production data to spot trends and seasonal peaks, allowing me to adjust our operational plans accordingly. I also collaborate closely with the sales team to integrate their insights to enhance our forecasts.
Don't Just Read Production Technician Questions - Practice Answering Them!
Reading helps, but actual practice is what gets you hired. Our AI feedback system helps you improve your Production Technician interview answers in real-time.
Personalized feedback
Unlimited practice
Used by hundreds of successful candidates
What methods do you use for production capacity planning in high-demand scenarios?
How to Answer
- 1
Assess historical demand data to predict future needs.
- 2
Utilize flexible staffing solutions like overtime or temporary workers.
- 3
Implement just-in-time inventory management to reduce lead times.
- 4
Collaborate with supply chain partners for real-time capacity updates.
- 5
Regularly review and adjust production schedules based on demand fluctuations.
Example Answers
I analyze historical sales data to forecast demand and adjust production accordingly. I may also increase staffing during peak times by using overtime or temporary hires to ensure we meet high demand.
Situational Interview Questions
If a major production line goes down, what immediate steps would you take to mitigate the impact?
How to Answer
- 1
Assess the severity of the downtime and gather information on the cause.
- 2
Communicate with your team and relevant stakeholders about the situation.
- 3
Implement immediate corrective actions, such as restarting machines or diverting production.
- 4
Evaluate the production schedule and adjust priorities to minimize losses.
- 5
Document the incident and follow up for root cause analysis.
Example Answers
First, I would quickly assess the issue to determine the cause of the downtime. Then, I would inform my team and key stakeholders. I would attempt to restart the line if possible while considering a temporary shift of production to other lines to minimize the impact.
You have limited resources for an upcoming project. How would you prioritize resource allocation?
How to Answer
- 1
Identify the key project goals and deliverables
- 2
Assess the impact of resources on achieving those goals
- 3
Use a priority matrix to categorize tasks by urgency and importance
- 4
Engage stakeholders to get input on critical areas
- 5
Allocate resources to high-impact tasks first, ensuring deadlines are met.
Example Answers
I would start by outlining the project's main goals and identifying which tasks are crucial for achieving them. Then, I'd prioritize resources for those high-impact tasks by consulting with the team and stakeholders to ensure everyone's aligned on priorities.
Don't Just Read Production Technician Questions - Practice Answering Them!
Reading helps, but actual practice is what gets you hired. Our AI feedback system helps you improve your Production Technician interview answers in real-time.
Personalized feedback
Unlimited practice
Used by hundreds of successful candidates
How would you handle a sudden increase in production demand that exceeds current capacity?
How to Answer
- 1
Prioritize communication with team and stakeholders about the increased demand.
- 2
Assess current production capabilities and identify bottlenecks.
- 3
Explore options for increasing capacity, such as overtime or temporary staff.
- 4
Consider streamlining processes to enhance efficiency.
- 5
Develop a short-term action plan to meet the demand while maintaining quality.
Example Answers
I would first communicate with my team about the spike in demand and discuss our current capabilities. Then, I would identify any production bottlenecks and consider options like overtime or bringing in temporary workers to help meet the demand. Streamlining our processes would also be a priority to ensure we maintain quality.
If you notice a persistent bottleneck in the production line, what steps would you take to address it?
How to Answer
- 1
Identify the root cause of the bottleneck by analyzing data and observing the process.
- 2
Consult with team members who are involved in the affected area to get insights.
- 3
Implement targeted changes to address the cause, whether it be equipment, workflow, or staffing.
- 4
Monitor the results after changes are made to ensure the issue is resolved.
- 5
Document the process and outcomes for future reference and improvement.
Example Answers
First, I would observe the production line to identify where the delays are occurring and gather data on the processing times. Then, I would discuss with the team to understand their perspectives on the bottleneck. Once I identify the root cause, whether it's a machine malfunction or a staffing issue, I'd implement changes and monitor the results closely.
A key supplier has suddenly increased prices. How would you approach this situation to maintain cost-effectiveness?
How to Answer
- 1
Assess the impact of the price increase on overall production costs.
- 2
Negotiate with the supplier to explore potential discounts or payment terms.
- 3
Evaluate alternative suppliers for cost-effective options.
- 4
Consider redesigning products to use lower-cost materials without sacrificing quality.
- 5
Collaborate with the finance team to adjust the budget and identify savings in other areas.
Example Answers
I would first assess how the price increase affects our production budget. Then I would negotiate with the supplier to understand the reasons for the increase and see if we can obtain better terms. If negotiations fail, I would research alternative suppliers who can offer better pricing and explore redesigning our products to lower costs.
During a compliance audit, a non-compliance issue is identified. What actions would you take to resolve it?
How to Answer
- 1
Identify the root cause of the non-compliance issue promptly
- 2
Document all findings and involve relevant stakeholders
- 3
Develop a corrective action plan outlining steps to resolve the issue
- 4
Implement the corrective actions and monitor their effectiveness
- 5
Communicate with the audit team and ensure compliance moving forward
Example Answers
Upon identifying the non-compliance issue, I would first investigate to determine the root cause. I'd then document my findings and engage with the relevant team members to discuss corrective actions. After developing a plan, I'd implement the solutions and follow up to ensure compliance is restored.
How would you develop a training plan for a new production shift to ensure they meet performance standards?
How to Answer
- 1
Identify key performance standards and metrics for the shift
- 2
Assess the current skill levels of the new team members
- 3
Create a structured training schedule with clear objectives
- 4
Incorporate hands-on training and shadowing with experienced staff
- 5
Evaluate training effectiveness through assessments and feedback sessions
Example Answers
To develop a training plan, I would start by defining the key performance standards that the team needs to meet. Then, I would assess the current skill levels of my team and create a training schedule that includes both theory and practical hands-on sessions. Lastly, I would implement checkpoints to assess their progress and gather feedback to modify the training as needed.
You are leading a new production project. How would you establish timelines and ensure the project stays on track?
How to Answer
- 1
Define clear project milestones and deadlines.
- 2
Use project management tools to track progress and updates.
- 3
Communicate regularly with the team to align on tasks and timelines.
- 4
Anticipate potential risks and create contingency plans.
- 5
Set up periodic reviews to assess progress and adjust timelines as necessary.
Example Answers
I would begin by setting clear project milestones and deadlines that outline what needs to be achieved at each stage. Then, I would implement a project management tool to track the progress and updates from the team. Regular communication is key, so I would hold weekly check-ins to ensure everyone is aligned. I'd also prepare for potential risks by developing contingency plans. Finally, I'd schedule periodic reviews to reassess our timelines and make adjustments if needed.
Faced with implementing new production technology, how would you plan and execute the integration?
How to Answer
- 1
Assess the current production process and identify areas for improvement.
- 2
Engage stakeholders early to gather input and secure buy-in.
- 3
Develop a detailed implementation plan with timelines and milestones.
- 4
Conduct training sessions for staff to ensure smooth adoption.
- 5
Monitor progress and adapt the plan based on feedback and results.
Example Answers
First, I would assess the existing production processes to identify enhancement opportunities. Then, I would involve key stakeholders to gather their insights and ensure their support. I'll create a detailed implementation plan with clear timelines, followed by training sessions for my team to familiarize them with the new technology before we go live. Finally, I would closely monitor the integration and adjust the process as needed.
If a customer reports a defect in a product, how would you investigate and address the issue in the production process?
How to Answer
- 1
Acknowledge the customer's concern promptly
- 2
Gather detailed information about the defect from the customer
- 3
Review production records and processes related to the defective product
- 4
Conduct a root cause analysis to identify the source of the issue
- 5
Implement corrective actions and communicate with the customer about the resolution
Example Answers
I would first acknowledge the customer's report and gather as much detail about the defect as possible. Then, I would review the production logs and any quality checks that were performed before the product was shipped. After identifying the potential cause, I would work with my team to implement corrective measures and keep the customer updated throughout the process.
Don't Just Read Production Technician Questions - Practice Answering Them!
Reading helps, but actual practice is what gets you hired. Our AI feedback system helps you improve your Production Technician interview answers in real-time.
Personalized feedback
Unlimited practice
Used by hundreds of successful candidates
How would you assess and implement changes to ensure environmentally sustainable production practices?
How to Answer
- 1
Identify key performance indicators for sustainability.
- 2
Conduct an audit of current production processes for waste and resource use.
- 3
Engage team members in brainstorming solutions for sustainable practices.
- 4
Research industry best practices and technologies for eco-friendly production.
- 5
Develop a clear implementation plan with timelines and metrics for success.
Example Answers
I would start by assessing the energy and waste outputs of our current processes, aiming to identify areas of significant environmental impact. Then, I'd engage the team to gather ideas on how we can reduce waste and improve efficiency, while researching best practices to bring innovative solutions into our workflow.
Production Technician Position Details
Salary Information
Recommended Job Boards
CareerBuilder
www.careerbuilder.com/jobs/production-technicianZipRecruiter
www.ziprecruiter.com/Jobs/Production-Technician/These job boards are ranked by relevance for this position.
Related Positions
Ace Your Next Interview!
Practice with AI feedback & get hired faster
Personalized feedback
Used by hundreds of successful candidates
Ace Your Next Interview!
Practice with AI feedback & get hired faster
Personalized feedback
Used by hundreds of successful candidates