Top 29 Quality Control Technician Interview Questions and Answers [Updated 2025]
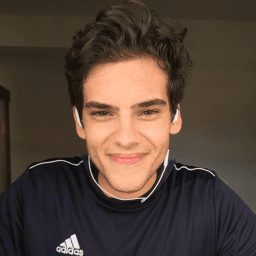
Andre Mendes
•
March 30, 2025
Are you gearing up for a Quality Control Technician interview and eager to make a great impression? Our latest blog post has you covered with the most common interview questions tailored for this pivotal role. Dive into a curated selection of questions, complete with example answers and insightful tips, designed to help you respond confidently and effectively. Get ready to showcase your skills and land that job!
Download Quality Control Technician Interview Questions in PDF
To make your preparation even more convenient, we've compiled all these top Quality Control Technicianinterview questions and answers into a handy PDF.
Click the button below to download the PDF and have easy access to these essential questions anytime, anywhere:
List of Quality Control Technician Interview Questions
Behavioral Interview Questions
Can you describe a time when you identified a critical quality issue that others missed?
How to Answer
- 1
Focus on a specific instance from your experience.
- 2
Use the STAR method: Situation, Task, Action, Result.
- 3
Highlight your attention to detail and problem-solving skills.
- 4
Emphasize the impact of your finding on the team or project.
- 5
Conclude with lessons learned or improvements made.
Example Answers
In my previous role, I noticed a recurring deviation in product measurements during routine inspections. I documented the discrepancies and informed my supervisor, prompting an in-depth review. This led to a process adjustment that improved accuracy by 15%.
Tell me about a situation where you had to collaborate with other departments to solve a quality issue.
How to Answer
- 1
Identify a specific quality issue you faced in your role.
- 2
Explain how you communicated with other departments, highlighting teamwork.
- 3
Detail the steps taken to investigate the issue collectively.
- 4
Share the outcome and what you learned from the collaboration.
- 5
Emphasize the importance of cross-departmental communication.
Example Answers
In my previous role, we had a recurring defect in one of our products. I collaborated with the engineering and production teams to trace the problem. We held a meeting, shared data, and identified a flaw in the manufacturing process. Implementing a new procedure reduced defects by 30%, and I learned the value of teamwork in problem-solving.
Good Candidates Answer Questions. Great Ones Win Offers.
Reading sample answers isn't enough. Top candidates practice speaking with confidence and clarity. Get real feedback, improve faster, and walk into your next interview ready to stand out.
Master your interview answers under pressure
Boost your confidence with real-time practice
Speak clearly and impress hiring managers
Get hired faster with focused preparation
Used by hundreds of successful candidates
Describe a challenging quality control problem you faced and how you resolved it.
How to Answer
- 1
Identify a specific quality issue you encountered.
- 2
Explain the impact of the problem on production or customers.
- 3
Describe the steps you took to investigate and resolve the issue.
- 4
Highlight any tools or methods used, like statistical analysis or root cause analysis.
- 5
Conclude with the positive outcome and any lessons learned.
Example Answers
I encountered a recurring issue with product defects that resulted in a 15% rejection rate. I gathered data to analyze defect patterns and found a correlation with a specific machine malfunction. I coordinated with maintenance to fix the issue and implemented a daily inspection protocol. The rejection rate dropped to 3% in subsequent months, and we improved overall quality.
How have you communicated difficult quality findings to your team or management?
How to Answer
- 1
Be straightforward and honest about the findings
- 2
Use data and examples to support your points
- 3
Emphasize the impact on the project or product
- 4
Suggest solutions or improvements to address the issues
- 5
Maintain a constructive and collaborative tone
Example Answers
In a recent project, I found a recurring defect in a supplier's component. I gathered data to illustrate the frequency and potential impact, then presented it to the team in a meeting, focusing on how it could affect our timelines. I suggested alternative suppliers and offered to help with the transition.
Give an example of how you have influenced others to improve quality standards in your workplace.
How to Answer
- 1
Identify a specific challenge related to quality you faced.
- 2
Describe the approach you took to address it.
- 3
Highlight how you engaged your colleagues or team members.
- 4
Include measurable results or outcomes from your efforts.
- 5
Keep the focus on your role in facilitating the improvement.
Example Answers
At my previous job, we had issues with product defects. I organized a team meeting to go over the quality control process. By presenting data on defect rates, I convinced the team to implement more rigorous checks. As a result, we reduced defects by 30% within two months.
Have you ever taken the initiative to improve a quality control process? Please provide details.
How to Answer
- 1
Identify a specific quality control process you improved.
- 2
Explain what motivated you to make changes.
- 3
Describe the actions you took to implement the improvement.
- 4
Present the measurable outcomes of your initiative.
- 5
Highlight any feedback received from supervisors or team members.
Example Answers
In my previous role, I noticed our defect tracking system was outdated. Motivated by the need for efficiency, I suggested a new software that automated tracking. After implementing it, we reduced defect resolution time by 30%. My supervisor praised the initiative for increasing our overall productivity.
Have you ever been responsible for training others on quality control procedures? How did you approach it?
How to Answer
- 1
Mention specific quality control procedures you trained others on
- 2
Describe the training materials or methods you used
- 3
Highlight how you assessed the trainees' understanding
- 4
Share any feedback you received from trainees
- 5
Explain how you followed up to ensure ongoing compliance
Example Answers
In my previous role, I trained new hires on our inspection protocols, using a combination of hands-on demonstrations and detailed manuals. I assessed their understanding through practical evaluations and adjusted my approach based on their feedback.
How do you handle feedback regarding your quality control assessments from your peers?
How to Answer
- 1
Listen actively to the feedback without interrupting
- 2
Ask clarifying questions to understand the feedback fully
- 3
Acknowledge valid points and express appreciation for the input
- 4
Reflect on the feedback and implement changes when necessary
- 5
Follow up with colleagues to discuss improvements or changes made
Example Answers
I take feedback seriously and listen carefully. If my peers point out specific issues, I ask questions to clarify their perspectives and show appreciation for their insights. I then assess the validity of their points and incorporate any necessary changes in my assessments.
What motivates you to maintain high-quality standards in your work?
How to Answer
- 1
Identify personal values that align with quality, such as integrity or excellence.
- 2
Share specific examples of past experiences where quality impacted outcomes.
- 3
Mention any professional standards or practices you adhere to.
- 4
Express a commitment to continuous improvement and learning.
- 5
Highlight the importance of teamwork and collaboration in achieving quality.
Example Answers
I believe that quality reflects my integrity and work ethic. In my last role, I saw how a small oversight affected the production line, leading to costly delays. That experience motivated me to implement checklists that improved our quality assurance process.
Good Candidates Answer Questions. Great Ones Win Offers.
Reading sample answers isn't enough. Top candidates practice speaking with confidence and clarity. Get real feedback, improve faster, and walk into your next interview ready to stand out.
Master your interview answers under pressure
Boost your confidence with real-time practice
Speak clearly and impress hiring managers
Get hired faster with focused preparation
Used by hundreds of successful candidates
Describe a situation where you received constructive criticism about your quality work. How did you react?
How to Answer
- 1
Think of a specific instance where feedback was given.
- 2
Explain the feedback and your initial reaction.
- 3
Describe the steps you took to address the feedback.
- 4
Share the outcome and what you learned from the experience.
- 5
Emphasize how it improved your work quality.
Example Answers
In my last role, I was told that I missed some details in reports. I felt a bit defensive at first but recognized the validity of the feedback. I sought clarification from my supervisor on the specific issues and revised my checking process. As a result, my subsequent reports received positive reviews, and I became more detail-oriented.
Technical Interview Questions
What quality management systems are you familiar with, and how have you implemented them?
How to Answer
- 1
Identify specific quality management systems you know, like ISO 9001 or Six Sigma
- 2
Describe a situation where you applied these systems in your previous role
- 3
Focus on the results achieved through implementation, like reduced defects or improved efficiency
- 4
Mention any tools or software you used during implementation
- 5
Keep your answer relevant to the job you're applying for
Example Answers
I am familiar with ISO 9001 and Lean Manufacturing. In my last job, I led a project to implement ISO 9001, which involved training staff and updating our documentation process. This resulted in a 20% reduction in defects over six months.
Can you explain the difference between qualitative and quantitative quality control methods?
How to Answer
- 1
Define both qualitative and quantitative methods clearly
- 2
Provide examples of each type to illustrate the differences
- 3
Highlight the strengths and weaknesses of each method
- 4
Mention situations where one method may be preferred over the other
- 5
Be concise and focused in your explanation
Example Answers
Qualitative quality control focuses on descriptive attributes and involves methods like inspections and focus groups. For example, customer feedback on product appearance is qualitative. Quantitative quality control uses measurable data, such as defect rates in manufacturing, which can be statistically analyzed. Each method has its use; qualitative provides insights into user experience, while quantitative offers hard data for process improvements.
Good Candidates Answer Questions. Great Ones Win Offers.
Reading sample answers isn't enough. Top candidates practice speaking with confidence and clarity. Get real feedback, improve faster, and walk into your next interview ready to stand out.
Master your interview answers under pressure
Boost your confidence with real-time practice
Speak clearly and impress hiring managers
Get hired faster with focused preparation
Used by hundreds of successful candidates
What tools or software are you experienced with for tracking and analyzing quality metrics?
How to Answer
- 1
Identify relevant tools you have used in your previous roles.
- 2
Mention specific software names like Excel, Minitab, or Tableau.
- 3
Highlight how you used these tools to improve quality metrics.
- 4
Provide a brief example of a project where you applied these tools.
- 5
Connect your experience with the requirements of the position.
Example Answers
In my previous role, I used Minitab for statistical analysis to track defect rates, which helped reduce them by 15%.
Describe your experience with statistical process control (SPC) and its application in quality control.
How to Answer
- 1
Explain what SPC is and its purpose in quality control
- 2
Share specific tools you've used within SPC, like control charts
- 3
Provide an example of how you applied SPC to improve a process
- 4
Mention the outcomes or improvements resulting from your SPC use
- 5
Keep your answer relevant to the job description and responsibilities
Example Answers
In my previous role, I used SPC to monitor production processes using control charts. For instance, I created control charts to identify variations in the machining process, which allowed us to reduce defects by 15%. This hands-on experience helped me understand the importance of maintaining quality standards.
How do you ensure compliance with industry standards and regulations in your quality inspections?
How to Answer
- 1
Stay updated on current industry standards and regulations relevant to your role
- 2
Utilize standardized checklists to ensure all compliance aspects are addressed
- 3
Keep detailed records of inspections and findings for accountability
- 4
Engage in regular training and workshops to enhance compliance knowledge
- 5
Collaborate with cross-functional teams to share best practices and insights
Example Answers
I regularly review industry standards to ensure I'm up-to-date. I also use checklists during inspections to cover all compliance points and document everything meticulously.
What methods do you use for conducting inspections and tests on products?
How to Answer
- 1
Identify specific tools and techniques you are familiar with
- 2
Highlight your familiarity with industry standards and protocols
- 3
Discuss how you document and report findings
- 4
Emphasize attention to detail and problem-solving skills
- 5
Mention how you ensure compliance with safety and quality regulations
Example Answers
I use calibrated measuring tools like calipers and micrometers to check dimensions. I follow ISO 9001 standards to ensure consistency. I document results meticulously and report any non-conformities promptly.
How do you maintain accurate records of quality control activities?
How to Answer
- 1
Use standardized forms or software to ensure consistency in data entry.
- 2
Regularly review and update records to reflect the most current data.
- 3
Implement a double-check system to verify data accuracy with a colleague.
- 4
Organize records systematically for easy retrieval and audits.
- 5
Conduct periodic training sessions to keep the team updated on record-keeping practices.
Example Answers
I use standardized forms for all quality control activities, which helps maintain consistency. I also review records weekly to ensure they are up-to-date and accurate.
Can you describe a time when you had to troubleshoot a quality failure? What methods did you use?
How to Answer
- 1
Identify a specific quality failure you encountered
- 2
Explain the steps you took to analyze the problem
- 3
Describe the tools or methods you used for troubleshooting
- 4
Highlight the outcome and any improvements made
- 5
Keep your answer concise and focused on your role
Example Answers
In my previous job, we noticed a batch of products had higher rejection rates. I reviewed the process logs, identified a machine calibration issue, and used a multimeter to check voltage levels. After recalibrating the machine, the rejection rate dropped by 30%.
What measurement techniques do you employ to ensure product specifications are met?
How to Answer
- 1
Discuss specific measurement techniques you use, such as calipers or gauges
- 2
Mention the importance of statistical process control
- 3
Highlight your experience with using quality standards like ISO or Six Sigma
- 4
Explain how you document and analyze measurement results
- 5
Share an example of adapting measurement techniques to specific products
Example Answers
I utilize a variety of measurement tools such as calipers and micrometers to ensure dimensions meet specifications. I often apply statistical process control to monitor quality and make adjustments as needed.
What certifications do you hold that relate to quality control and how have they benefited your work?
How to Answer
- 1
Identify relevant certifications specific to quality control, such as Six Sigma or ASQ.
- 2
Explain how each certification has enhanced your skills or knowledge.
- 3
Provide specific examples of how these skills were applied in your previous roles.
- 4
Link the certification benefits directly to quality outcomes in past projects.
- 5
Keep your response focused and concise to maintain the interviewer's interest.
Example Answers
I hold a Six Sigma Green Belt certification, which has strengthened my ability to analyze processes and reduce defects. For instance, I led a project where we improved a production line, resulting in a 15% decrease in error rates.
Good Candidates Answer Questions. Great Ones Win Offers.
Reading sample answers isn't enough. Top candidates practice speaking with confidence and clarity. Get real feedback, improve faster, and walk into your next interview ready to stand out.
Master your interview answers under pressure
Boost your confidence with real-time practice
Speak clearly and impress hiring managers
Get hired faster with focused preparation
Used by hundreds of successful candidates
Situational Interview Questions
If you find a defect in a product during inspection that has already been approved, how would you handle it?
How to Answer
- 1
Immediately document the defect and gather evidence.
- 2
Notify the relevant supervisor or quality manager promptly.
- 3
Assess whether the defect affects customer safety or compliance.
- 4
Propose corrective actions to prevent recurrence.
- 5
Communicate transparently with the team about the issue.
Example Answers
I would document the defect with photos and notes, then inform my supervisor right away. It's vital to assess if the defect poses any risks before we decide on corrective actions.
Imagine you are under pressure to meet production deadlines. A quality issue arises. What steps would you take?
How to Answer
- 1
Assess the severity of the quality issue immediately.
- 2
Communicate the issue to your team and management without delay.
- 3
Identify the root cause of the problem using data and testing.
- 4
Implement a quick corrective action to minimize impact on production.
- 5
Document the issue and solution for future reference and process improvement.
Example Answers
First, I would evaluate how severe the quality issue is and its potential impact on production. Then, I would inform my team and management right away. Next, I would investigate the root cause, and based on that, implement a temporary fix to keep the production on track.
Good Candidates Answer Questions. Great Ones Win Offers.
Reading sample answers isn't enough. Top candidates practice speaking with confidence and clarity. Get real feedback, improve faster, and walk into your next interview ready to stand out.
Master your interview answers under pressure
Boost your confidence with real-time practice
Speak clearly and impress hiring managers
Get hired faster with focused preparation
Used by hundreds of successful candidates
How would you approach a situation where your team disagrees on the severity of a quality defect?
How to Answer
- 1
Listen to all team members' perspectives on the defect
- 2
Gather data and evidence to assess the defect's impact
- 3
Facilitate a discussion to reach a consensus on severity
- 4
Refer to industry standards or company guidelines for clarity
- 5
Document the decision process and agreed actions
Example Answers
I would start by listening to my team to understand everyone's viewpoint. Then, I would collect data on the defect's impact and present it during a team discussion. This way, we can align on the severity based on facts.
If you are asked to improve a quality process that is not yielding results, what would be your plan?
How to Answer
- 1
Conduct a root cause analysis to identify the underlying issues
- 2
Gather data and feedback from key stakeholders involved in the process
- 3
Evaluate existing procedures and documentation for gaps or inconsistencies
- 4
Implement small-scale changes and monitor their impact
- 5
Review results and adjust strategies based on performance metrics
Example Answers
First, I would conduct a root cause analysis to pinpoint the issues in the current process. Then, I'd gather input from team members to understand their challenges. Next, I would analyze existing documentation for inconsistencies. I would implement changes on a small scale and track their effects, adjusting as necessary based on the outcomes.
You are tasked with presenting quality metrics to senior management. How would you prepare for this?
How to Answer
- 1
Identify key quality metrics relevant to the audience's interests
- 2
Gather and analyze data to support your metrics
- 3
Create clear visualizations to represent the data effectively
- 4
Prepare a concise narrative to explain the significance of the metrics
- 5
Anticipate potential questions and prepare thoughtful responses
Example Answers
I would start by determining which quality metrics, like defect rates and customer satisfaction scores, are most relevant to senior management. Next, I would collect and analyze the data to ensure accuracy. Then, I'd create graphs and charts that present the information clearly. Lastly, I'd prepare a brief story around the metrics to explain their importance and be ready to answer any questions.
If a quality audit reveals several lapses in your current processes, how would you respond?
How to Answer
- 1
Acknowledge the findings without being defensive
- 2
Assess the specific lapses to understand root causes
- 3
Involve team members to gather insights and solutions
- 4
Develop an action plan with clear timelines and responsibilities
- 5
Communicate the plan to stakeholders and monitor progress
Example Answers
I would first acknowledge the audit findings and thank the auditors for their insights. Then, I would analyze the lapses to identify root causes. Together with my team, I’d brainstorm solutions and develop a detailed action plan to address the issues. Finally, I’d keep stakeholders informed throughout the process.
If a new piece of equipment malfunctions and affects quality, what steps would you take?
How to Answer
- 1
Identify and document the specific malfunction immediately
- 2
Isolate the equipment to prevent further production impact
- 3
Inform relevant team members or supervisors about the issue
- 4
Conduct a root cause analysis to understand why the malfunction occurred
- 5
Implement corrective actions and monitor the results closely
Example Answers
First, I would document the malfunction and isolate the affected equipment to ensure no further products are made. Then, I would notify my supervisor and team. Afterward, I would analyze the root cause of the malfunction and work on corrective measures to resolve the issue effectively.
Quality Control Technician Position Details
Recommended Job Boards
These job boards are ranked by relevance for this position.
Related Positions
Good Candidates Answer Questions. Great Ones Win Offers.
Master your interview answers under pressure
Boost your confidence with real-time practice
Speak clearly and impress hiring managers
Get hired faster with focused preparation
Used by hundreds of successful candidates
Good Candidates Answer Questions. Great Ones Win Offers.
Master your interview answers under pressure
Boost your confidence with real-time practice
Speak clearly and impress hiring managers
Get hired faster with focused preparation
Used by hundreds of successful candidates