Top 28 Quality Controller Interview Questions and Answers [Updated 2025]
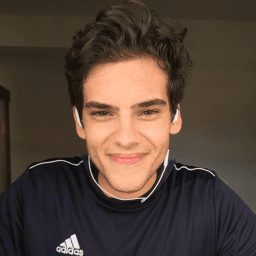
Andre Mendes
•
March 30, 2025
Navigating the path to becoming a Quality Controller can be challenging, but preparation is key to success. This blog post compiles the most common interview questions for the Quality Controller role, providing insightful example answers and practical tips on how to respond effectively. Whether you're a seasoned professional or an aspiring candidate, these insights will help you confidently tackle your next interview and stand out to potential employers.
Download Quality Controller Interview Questions in PDF
To make your preparation even more convenient, we've compiled all these top Quality Controllerinterview questions and answers into a handy PDF.
Click the button below to download the PDF and have easy access to these essential questions anytime, anywhere:
List of Quality Controller Interview Questions
Behavioral Interview Questions
Can you describe a time when you identified a significant quality issue in a project? What steps did you take to resolve it?
How to Answer
- 1
Select a specific project and issue.
- 2
Explain how you identified the quality problem.
- 3
Outline the steps you took to address the issue.
- 4
Highlight the outcome and any lessons learned.
- 5
Keep the focus on your role in the resolution process.
Example Answers
In a software development project, I noticed recurring bugs during testing phases. I documented each bug, increased communication with the developers, and facilitated a root cause analysis. This led to implementing additional code reviews and reduced bugs by 30% in the next release.
Tell me about a time you worked with a team to improve a quality control process. What was your role and what was the outcome?
How to Answer
- 1
Start with a brief context of the project or process.
- 2
Clearly define your role and responsibilities in the team.
- 3
Explain the changes or improvements implemented.
- 4
Share specific outcomes or metrics that resulted from the improvements.
- 5
Reflect on any lessons learned or skills gained during the process.
Example Answers
In my previous job, our team identified a high defect rate in our assembly line. As the lead quality controller, I organized a brainstorming session to identify key issues. We implemented a new checklist system for quality checks. This reduced defects by 30% over three months, improving overall product satisfaction.
Don't Just Read Quality Controller Questions - Practice Answering Them!
Reading helps, but actual practice is what gets you hired. Our AI feedback system helps you improve your Quality Controller interview answers in real-time.
Personalized feedback
Unlimited practice
Used by hundreds of successful candidates
Describe an instance when you had to lead a team through a challenging quality control situation. What strategies did you use?
How to Answer
- 1
Identify a specific quality issue you faced and explain the context.
- 2
Describe your leadership role and how you motivated the team.
- 3
Explain the strategies you implemented to address the issue.
- 4
Share the outcome and what you learned from the experience.
- 5
Keep it concise and focus on your contribution and results.
Example Answers
In a previous role, our team faced a major defect in product batches. I organized a meeting to analyze the data, motivating my team to share insights and solutions. We implemented a new inspection process which reduced defects by 30%. This taught me the importance of collaboration and data-driven decision making.
Give an example of how you communicated quality concerns to non-technical stakeholders. How did you ensure they understood the implications?
How to Answer
- 1
Identify the specific concern and its impact on the project or product
- 2
Use simple language without jargon to explain the issue
- 3
Provide visual aids or examples to illustrate the concern
- 4
Link the quality issue to business objectives or outcomes
- 5
Encourage questions to ensure understanding and address concerns
Example Answers
In my previous role, I noticed that a supplier's materials failed our quality tests, potentially affecting product safety. I created a visual report highlighting test results and estimated cost implications. I presented this to the team, emphasizing how this could delay product launch and affect sales. I invited questions to clarify their concerns and ensured everyone was aligned on the next steps.
Can you provide an example of a time when you had to adapt your quality control approach due to unforeseen circumstances? What did you learn?
How to Answer
- 1
Think of a specific situation where you faced a challenge.
- 2
Describe the unforeseen circumstance clearly and concisely.
- 3
Explain how you adjusted your approach to maintain quality.
- 4
Highlight the outcome and what skills or insights you gained.
- 5
Keep your answer focused on your role and contributions.
Example Answers
In my previous role, we discovered a significant defect rate in a batch of products just before a major shipment. I quickly gathered the team to analyze the issue and we decided to implement additional quality checks. This not only helped us identify the root cause but also ensured that we delivered a flawless batch in the end. I learned the importance of quick decision-making and teamwork under pressure.
Describe a time when your attention to detail made a difference in a project. What was the situation?
How to Answer
- 1
Choose a specific project where detail was crucial.
- 2
Clearly explain the problem that arose due to a lack of attention to detail.
- 3
Describe your actions and how you caught or corrected the issue.
- 4
Highlight the positive outcome and how it benefited the project.
- 5
Use metrics or feedback if possible to support your impact.
Example Answers
In a recent quality control project, I noticed discrepancies in the materials list for a product. By double-checking each item, I discovered several incorrect specifications that would have led to product defects. My corrections ensured we met quality standards, which resulted in a 20% reduction in rework costs.
Can you tell me about a mistake you made in quality control? How did it affect your perspective on quality management?
How to Answer
- 1
Choose a specific, relevant mistake that had an impact.
- 2
Explain the context and what led to the mistake clearly.
- 3
Describe the immediate consequences of the mistake.
- 4
Share the lessons learned and how you've applied them since.
- 5
Discuss how this experience has shaped your approach to quality management.
Example Answers
In a previous role, I missed a critical ingredient during a quality check, which led to a batch of non-compliant products. This mistake taught me the importance of checklist usage and thorough documentation, reinforcing my commitment to preventative measures in quality control.
How do you typically receive and respond to feedback regarding your quality control processes?
How to Answer
- 1
Acknowledge feedback as an opportunity to improve
- 2
Provide specific examples of past feedback you've received
- 3
Explain how you implemented changes based on the feedback
- 4
Emphasize the positive outcomes from your adjustments
- 5
Mention how you encourage ongoing feedback from your team
Example Answers
I always view feedback as a valuable chance to enhance my processes. For instance, after receiving input about documentation clarity, I revised our templates, which significantly reduced misunderstandings in the team.
What motivates you to maintain high standards in quality control, and how do you inspire others to do the same?
How to Answer
- 1
Identify personal values tied to quality, like integrity or responsibility.
- 2
Share specific examples of how your motivation has improved processes.
- 3
Explain methods you use to inspire team members, like leading by example.
- 4
Highlight the importance of teamwork in achieving quality goals.
- 5
Discuss the impact of quality on customer satisfaction and company success.
Example Answers
I am motivated by a sense of responsibility to deliver the best products possible. For instance, in my previous role, I introduced a peer review system that encouraged collaboration and improved quality. I inspire my team by setting high standards myself and recognizing their efforts.
Don't Just Read Quality Controller Questions - Practice Answering Them!
Reading helps, but actual practice is what gets you hired. Our AI feedback system helps you improve your Quality Controller interview answers in real-time.
Personalized feedback
Unlimited practice
Used by hundreds of successful candidates
Describe a time when you had to lead a team through a challenging quality control situation. What strategies did you use?
How to Answer
- 1
Select a specific situation where you faced a quality control challenge.
- 2
Explain your role and the team's dynamics.
- 3
Outline the strategies you implemented, such as communication, training, or process adjustments.
- 4
Emphasize the outcome and what you learned from the experience.
- 5
Keep the response structured: situation, action, result.
Example Answers
In a previous role, our team faced a major defect in our product due to supply chain issues. I organized daily stand-up meetings to improve communication and set clear quality standards. We retrained the team on inspection protocols, which led to a 30% decrease in defects over two months, strengthening our process.
Technical Interview Questions
What quality standards or methodologies are you most familiar with, and how have you applied them in your previous roles?
How to Answer
- 1
Identify key quality standards relevant to your field, like ISO 9001 or Six Sigma
- 2
Share specific examples where you implemented these methods successfully
- 3
Discuss measurable outcomes or improvements from your actions
- 4
Show your understanding of the principles behind each standard or methodology
- 5
Be prepared to explain how you stay updated on quality trends
Example Answers
I am familiar with ISO 9001, which I applied in my previous role by leading a team to streamline processes. This resulted in a 20% reduction in errors, improving overall product quality.
What tools or software have you used for quality control measurements? Can you describe how you utilized these tools in your work?
How to Answer
- 1
Mention specific tools or software you are familiar with.
- 2
Explain how you used each tool in a practical context.
- 3
Include any measurable outcomes or improvements you achieved.
- 4
Be prepared to discuss your experience collaborating with team members using these tools.
- 5
Use examples that reflect the requirements of the Quality Controller position.
Example Answers
I have used Minitab for statistical analysis, where I analyzed data trends to implement quality control processes. This led to a 15% reduction in defects over six months.
Don't Just Read Quality Controller Questions - Practice Answering Them!
Reading helps, but actual practice is what gets you hired. Our AI feedback system helps you improve your Quality Controller interview answers in real-time.
Personalized feedback
Unlimited practice
Used by hundreds of successful candidates
What experience do you have with statistical quality control techniques? Which do you find most useful?
How to Answer
- 1
Identify specific statistical quality control techniques you have used.
- 2
Mention any relevant projects where these techniques were applied.
- 3
Discuss the impact of these techniques on quality improvement.
- 4
Select one or two techniques you find most effective and explain why.
- 5
Be ready to provide examples or results achieved through these techniques.
Example Answers
In my previous role, I used control charts and process capability analysis to monitor production quality. These techniques helped reduce defects by 20%, which significantly improved overall efficiency. I find control charts particularly useful as they provide real-time insights.
What role does documentation play in quality control, and how have you managed documentation in your past positions?
How to Answer
- 1
Explain how documentation ensures consistency and traceability in quality control.
- 2
Highlight the importance of accurate records for compliance and audits.
- 3
Discuss how you have organized documentation systems for easy access.
- 4
Include examples of specific tools or methods you used for documentation.
- 5
Mention how you trained team members in documentation best practices.
Example Answers
Documentation is crucial in quality control as it helps maintain consistency and traceability. In my last role, I used a cloud-based system to organize quality checklists and inspection reports, making it easy for the team to access the latest documents. I also conducted training sessions on proper documentation procedures, ensuring everyone understood their importance.
What types of inspection techniques have you used in the past, and how did they improve quality?
How to Answer
- 1
Mention specific inspection techniques such as visual inspection, ultrasonic testing, or statistical process control.
- 2
Explain how each technique contributed to identifying defects or inefficiencies.
- 3
Include any improvements in product quality, reduced error rates, or enhanced compliance.
- 4
Relate your experiences to the specific industry or context of the job you are applying for.
- 5
Use metrics or examples to quantify the impact of the inspection techniques.
Example Answers
In my previous role, I utilized visual inspection to check for surface defects, which decreased defects by 20%. This led to higher customer satisfaction and fewer returns.
What is your experience with failure analysis, and how do you conduct it when quality issues arise?
How to Answer
- 1
Start with a specific instance where you performed failure analysis.
- 2
Explain the steps you took to identify the root cause of the issue.
- 3
Discuss the methods or tools you used during the analysis process.
- 4
Highlight the corrective actions implemented and their outcomes.
- 5
Reflect on what you learned from the experience and how it improved your approach.
Example Answers
In my previous role, we faced a recurring defect in a product line. I led a root cause analysis using a fishbone diagram to identify factors. Through testing and data analysis, we discovered a calibration error in equipment. We recalibrated and implemented a new verification process, reducing defects by 40%. This taught me the importance of proactive maintenance checks.
Do you hold any quality control certifications? If so, how have they enhanced your role as a Quality Controller?
How to Answer
- 1
Identify specific certifications you hold relevant to quality control.
- 2
Explain how each certification directly applies to your work.
- 3
Share any skills or methodologies gained from the certification.
- 4
Mention any improvements in processes or results due to the certification.
- 5
Keep your answer focused and relevant to the role.
Example Answers
I hold a Six Sigma Green Belt certification, which has equipped me with tools to optimize processes effectively. This training has enhanced my ability to identify defects and reduce variations, leading to a 15% increase in product quality over the past year.
How do you stay updated on the latest trends and technologies in quality control and assurance?
How to Answer
- 1
Subscribe to industry newsletters and journals for regular updates
- 2
Participate in webinars and online courses to learn from experts
- 3
Join professional organizations or forums to network and share knowledge
- 4
Attend conferences and workshops for hands-on experience and insights
- 5
Follow thought leaders on social media to get quick updates on trends
Example Answers
I subscribe to several industry newsletters and journals, which keeps me informed about the latest innovations and standards in quality control. Additionally, I regularly attend webinars to gain insights from experts in the field.
Situational Interview Questions
Imagine you found a critical defect in a product just before it was scheduled to launch. What steps would you take to handle the situation?
How to Answer
- 1
Immediately document the defect with clear details and evidence.
- 2
Inform relevant stakeholders including management and development teams.
- 3
Assess the impact of the defect on the launch timeline and product quality.
- 4
Propose potential solutions or corrective actions to address the defect.
- 5
Follow up to ensure the defect is resolved and verify quality before any further actions.
Example Answers
I would first document the defect thoroughly, noting its specifics and potential impact. Then, I'd immediately inform the project manager and the development team. Together, we'd evaluate if the launch needs to be postponed and explore options to fix the defect before moving forward.
If you had to choose between delaying a shipment due to quality concerns or meeting the deadline, how would you approach this decision?
How to Answer
- 1
Evaluate the severity of the quality issue and its impact on the customer.
- 2
Communicate transparently with all stakeholders about the concerns.
- 3
Prioritize long-term reputation over short-term deadlines.
- 4
Consider potential solutions to resolve quality issues quickly.
- 5
Document the decision-making process for future reference.
Example Answers
I would first assess the quality issue's severity. If it poses a risk to customer satisfaction, I would delay the shipment and inform all relevant parties of this decision to ensure transparency.
Don't Just Read Quality Controller Questions - Practice Answering Them!
Reading helps, but actual practice is what gets you hired. Our AI feedback system helps you improve your Quality Controller interview answers in real-time.
Personalized feedback
Unlimited practice
Used by hundreds of successful candidates
You have multiple quality issues reported from different sources. How would you prioritize which issues to address first?
How to Answer
- 1
Identify the impact on customer satisfaction for each issue
- 2
Assess the severity of each issue using a scoring system
- 3
Consider the frequency of each issue's occurrence
- 4
Evaluate resources available for resolving issues
- 5
Communicate with stakeholders for insights on urgency
Example Answers
First, I would analyze each quality issue by determining how it affects customer satisfaction. Then I would rate the severity and frequency, assigning scores. After that, I'd prioritize the issues with the highest scores to address them effectively.
If you are working with a team that resists your quality improvement recommendations, how would you handle the situation?
How to Answer
- 1
Listen to team concerns and understand their perspective.
- 2
Communicate the benefits of the recommendations clearly.
- 3
Provide data or examples to support your proposal.
- 4
Encourage collaborative discussion to find a compromise.
- 5
Follow up and show results after implementing changes.
Example Answers
I would first listen to the team's concerns to understand their resistance. Then, I would explain how the recommendations can lead to better outcomes and back it up with relevant data. By fostering an open discussion, we could address any reservations together, leading to a mutually beneficial solution.
Your team is behind schedule on a quality improvement project. What actions would you take to get back on track?
How to Answer
- 1
Assess the current project status and identify specific delays.
- 2
Communicate with the team to understand challenges and gather input.
- 3
Prioritize tasks that will have the biggest impact on project timelines.
- 4
Set clear, realistic deadlines for the prioritized tasks.
- 5
Implement regular check-ins to monitor progress and make adjustments.
Example Answers
First, I would evaluate where the delays are coming from by reviewing the project timeline. Then, I would have a meeting with the team to address any roadblocks they are facing and ensure we all understand the priorities. After that, I would focus on the most critical tasks that need to be completed to regain lost time and set specific deadlines for those tasks. Finally, I would schedule short daily check-ins to track our progress and make necessary adjustments.
If you discovered that a colleague was cutting corners in quality control to save time, how would you handle that situation?
How to Answer
- 1
Address the issue directly with your colleague first
- 2
Express concern for quality and team standards
- 3
Emphasize the long-term impact of poor quality
- 4
Suggest constructive solutions or improvements
- 5
If necessary, escalate to a manager with factual evidence
Example Answers
I would first talk to my colleague privately and point out the specific areas where I noticed they were cutting corners. I would explain how this could compromise our product and the potential long-term risks involved.
How would you implement a new quality control initiative that has not been tried before in your organization?
How to Answer
- 1
Research current quality control methods to identify gaps or areas for improvement
- 2
Engage stakeholders early to gather insights and support for the initiative
- 3
Pilot the initiative on a small scale to test its effectiveness
- 4
Gather data and feedback during the pilot phase to make necessary adjustments
- 5
Develop a clear communication plan to ensure everyone is informed of changes
Example Answers
I would start by analyzing our existing quality control processes to find areas where the new initiative could add value. Then, I would engage with team members and management to gather their input and buy-in. After that, I'd run a small pilot project, collect feedback, and adjust as needed before rolling out the initiative organization-wide.
You receive a customer complaint about a past product quality issue. How would you address the complaint and prevent similar issues in the future?
How to Answer
- 1
Acknowledge the complaint promptly and thank the customer for their feedback
- 2
Investigate the issue by reviewing production records and quality checks
- 3
Communicate the findings and resolution to the customer transparently
- 4
Implement corrective actions and document changes in quality processes
- 5
Conduct training sessions for staff to prevent recurrence of similar issues
Example Answers
I would first respond to the customer to acknowledge their complaint and thank them for bringing it to our attention. Then, I would investigate the issue by reviewing our quality checks and production records to identify the root cause. Next, I would inform the customer of our findings and the actions we will take to resolve it. Finally, I would ensure our team is trained on the new procedures to avoid a repeat of this problem.
Quality Controller Position Details
Recommended Job Boards
ZipRecruiter Remote
www.ziprecruiter.com/Jobs/Remote-Quality-ControlCareerBuilder
www.careerbuilder.com/jobs/quality-control-inspectorThese job boards are ranked by relevance for this position.
Related Positions
Ace Your Next Interview!
Practice with AI feedback & get hired faster
Personalized feedback
Used by hundreds of successful candidates
Ace Your Next Interview!
Practice with AI feedback & get hired faster
Personalized feedback
Used by hundreds of successful candidates