Top 26 Quality Control Specialist Interview Questions and Answers [Updated 2025]
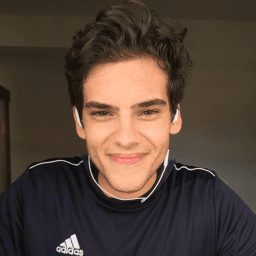
Andre Mendes
•
March 30, 2025
Navigating the competitive landscape of quality control requires not only technical expertise but also adept communication skills. In this post, we unravel the most common interview questions for the Quality Control Specialist role, providing sample answers and insightful tips to help you respond with confidence and precision. Prepare to elevate your interview game and make a lasting impression on potential employers.
Download Quality Control Specialist Interview Questions in PDF
To make your preparation even more convenient, we've compiled all these top Quality Control Specialistinterview questions and answers into a handy PDF.
Click the button below to download the PDF and have easy access to these essential questions anytime, anywhere:
List of Quality Control Specialist Interview Questions
Behavioral Interview Questions
Can you describe a time when you identified a significant quality issue? What steps did you take to resolve it?
How to Answer
- 1
Start with a specific example of the quality issue.
- 2
Explain how you discovered the issue, emphasizing your attention to detail.
- 3
Outline the steps you took to address the issue, including collaboration with others if applicable.
- 4
Discuss the outcome and any improvements made as a result.
- 5
Highlight any skills or tools you used during the resolution process.
Example Answers
In my previous role, I noticed a recurring defect rate in our product line that exceeded acceptable levels. I conducted a thorough review of the production logs and found a pattern linked to a specific machine. I coordinated with the maintenance team to perform an inspection, which revealed a calibration error. After recalibration, the defect rate dropped by 30%, improving overall quality.
Give an example of a time you worked as part of a quality control team. What was your role and contribution to the team?
How to Answer
- 1
Identify a specific project or situation where you collaborated with others in quality control.
- 2
Clearly define your role and responsibilities in the team.
- 3
Highlight your specific contributions and the impact they had on the project.
- 4
Use quantitative results or feedback to illustrate the success of your efforts.
- 5
Keep your answer focused and relevant to the role you're applying for.
Example Answers
In my previous role at XYZ Manufacturing, I was part of a quality control team tasked with reducing defect rates. I led the analysis of product samples, identifying key patterns in defects. My recommendations helped reduce defects by 15% over three months, significantly improving customer satisfaction.
Don't Just Read Quality Control Specialist Questions - Practice Answering Them!
Reading helps, but actual practice is what gets you hired. Our AI feedback system helps you improve your Quality Control Specialist interview answers in real-time.
Personalized feedback
Unlimited practice
Used by hundreds of successful candidates
Can you provide an instance where your attention to detail made a crucial difference in a project?
How to Answer
- 1
Think of a specific project or task where detail was key
- 2
Explain the situation clearly and concisely
- 3
Describe your actions with specific focus on attention to detail
- 4
Highlight the positive outcome or impact of your actions
- 5
Keep it relevant to quality control and measurable results
Example Answers
In a recent project, I was responsible for reviewing a batch of products before shipment. I noticed a small error in labeling that could have led to misdeliveries. By catching it early, we prevented potential customer complaints and saved the company from a costly recall.
Tell me about a situation where you had to communicate a difficult message regarding quality to a team member or stakeholder.
How to Answer
- 1
Prepare a specific example demonstrating the issue and its impact.
- 2
Stay calm and empathetic; focus on the facts.
- 3
Use clear and concise language to explain the quality issue.
- 4
Suggest constructive ways to improve the situation together.
- 5
Follow up to ensure understanding and encouragement.
Example Answers
In my previous role, I noticed a recurring defect in our product line. I scheduled a one-on-one with the team member to discuss the issue, outlining the impact on our delivery timelines. By focusing on the data and offering to support with additional training, we collaboratively developed a stricter quality check that reduced defects by 30%.
Describe a time when you had to adapt your quality control processes due to unexpected changes. How did you manage this?
How to Answer
- 1
Identify a specific instance with clear details.
- 2
Explain the unexpected change and its impact on your processes.
- 3
Describe the steps you took to adapt effectively.
- 4
Highlight the outcome and lessons learned.
- 5
Keep it concise and focused on your role.
Example Answers
Last year, we faced a sudden supplier issue that affected our raw materials. I quickly gathered the team to reassess our quality control checkpoints. We implemented alternate materials while adjusting our testing protocols to ensure standards were still met. The result was minimal disruption and we maintained quality across the board.
Explain a situation where you had a disagreement with a colleague about a quality control procedure. How did you resolve it?
How to Answer
- 1
Describe the disagreement clearly and factually
- 2
Focus on your role and responsibilities in the situation
- 3
Emphasize the steps you took to address the disagreement
- 4
Highlight the outcome and any positive results
- 5
Show your ability to work collaboratively in resolving conflicts
Example Answers
In a recent project, a colleague insisted on using a specific testing method that I believed was outdated. I proposed that we review recent evidence and benchmarks together. After discussing our perspectives, we reached a compromise by integrating new techniques, which improved our efficiency by 15%.
Describe a time when you took the lead on a quality control project. What challenges did you face and how did you overcome them?
How to Answer
- 1
Choose a specific project where you had clear leadership.
- 2
Identify the main challenges you encountered during the project.
- 3
Explain the steps you took to address these challenges.
- 4
Highlight the outcome and any measurable improvements.
- 5
Emphasize teamwork and communication throughout the process.
Example Answers
In my previous role, I led a quality control initiative to reduce product defects by 15%. One challenge was pushback from the production team regarding new processes. I organized a series of workshops to demonstrate the benefits, resulting in a 20% reduction in defects within three months.
Technical Interview Questions
What quality control standards and methodologies are you familiar with? Can you explain how you have applied them in your work?
How to Answer
- 1
Identify key quality control standards like ISO 9001 or Six Sigma.
- 2
Provide specific examples of how you've implemented these standards.
- 3
Highlight measurable outcomes or improvements from your work.
- 4
Keep your explanation clear and focused on relevant experiences.
- 5
Connect your knowledge to the needs of the company you are applying to.
Example Answers
I am familiar with ISO 9001 and Six Sigma methodologies. In my previous role, I led a project to reduce defects by implementing Six Sigma techniques, which resulted in a 20% decrease in errors over six months.
What techniques do you use for inspecting and testing products for quality assurance? Can you provide examples?
How to Answer
- 1
Discuss specific inspection techniques like visual inspection, measurements, and functional tests.
- 2
Mention any tools or equipment you commonly use, such as calipers or gauges.
- 3
Provide examples of quality standards you follow, like ISO or Six Sigma.
- 4
Talk about how you document your findings and report issues.
- 5
Emphasize collaboration with other departments for continuous improvement.
Example Answers
I use visual inspections to identify defects, along with calipers for precise measurements. For instance, in my last role, I conducted functional tests on electronic components and ensured compliance with ISO 9001 standards, logging all results for transparency.
Don't Just Read Quality Control Specialist Questions - Practice Answering Them!
Reading helps, but actual practice is what gets you hired. Our AI feedback system helps you improve your Quality Control Specialist interview answers in real-time.
Personalized feedback
Unlimited practice
Used by hundreds of successful candidates
How comfortable are you with statistical analysis tools? Can you discuss a specific instance where you used data to support quality decisions?
How to Answer
- 1
Identify key statistical tools you are familiar with, such as Excel, Minitab, or R.
- 2
Share a specific project or situation where you applied these tools effectively.
- 3
Emphasize how the data you analyzed influenced quality outcomes or decisions.
- 4
Be ready to discuss any metrics or results that demonstrate your impact.
- 5
Conclude with what you learned from the experience and how it improved your skills.
Example Answers
I am very comfortable using Excel and Minitab for statistical analysis. In a recent project, I analyzed defect rates over three months. By applying control charts, I identified trends that led to adjustments in our processes, reducing defects by 15%. This experience helped me enhance my analytical skills and understand the importance of data in quality control.
Can you detail your experience with documentation and reporting in quality control? What tools have you utilized?
How to Answer
- 1
Outline specific documentation practices you've used in quality control.
- 2
Mention relevant reporting tools or software you've worked with.
- 3
Include examples of how your documentation improved quality outcomes.
- 4
Highlight any experience with regulatory compliance documentation.
- 5
Keep your answer focused on results and impact on quality assurance.
Example Answers
In my previous role, I maintained detailed inspection reports using Microsoft Excel and created quality dashboards that tracked non-conformance data, leading to a 15% improvement in product quality over six months.
Can you discuss any process improvement initiatives you have led or contributed to in a quality control context?
How to Answer
- 1
Identify a specific initiative you took part in.
- 2
Use the STAR method: Situation, Task, Action, Result.
- 3
Focus on measurable outcomes to show impact.
- 4
Highlight teamwork and any tools or techniques used.
- 5
Connect improvement to overall quality goals.
Example Answers
In my previous role, we faced issues with high defect rates in a key product line. I led a cross-functional team to analyze the QC process using Six Sigma techniques. We identified root causes and implemented a new testing protocol, which reduced defects by 25% over three months.
Explain your understanding of regulatory compliance in quality control, and provide an example of how you ensured compliance in a previous role.
How to Answer
- 1
Define regulatory compliance and its importance in quality control.
- 2
Mention specific regulations relevant to your industry.
- 3
Describe a specific situation where you identified a compliance issue.
- 4
Explain the steps you took to address the issue and ensure compliance.
- 5
Highlight the outcome and its impact on the organization.
Example Answers
Regulatory compliance in quality control ensures products meet safety and quality standards. In my previous role at XYZ Corp, we followed FDA guidelines for medical devices. I noticed discrepancies in our labeling process. I initiated a review, updated our procedures, and trained staff on compliance. This resulted in a successful FDA audit with zero findings.
What quality control tools or equipment have you operated? Describe your experience with them.
How to Answer
- 1
Identify specific tools you've used in your previous positions
- 2
Mention your level of proficiency with each tool
- 3
Explain how these tools contributed to quality assurance processes
- 4
Provide examples of successful outcomes achieved using these tools
- 5
Be prepared to discuss any training or certifications related to the tools
Example Answers
I have extensive experience using calipers and micrometers for measuring dimensions in parts inspections. I became proficient in using these tools during my time at XYZ Manufacturing, where I reduced measurement errors by 15%.
Situational Interview Questions
Imagine you discover a product defect just before a shipment. What steps would you take to handle this situation?
How to Answer
- 1
Identify the nature and scope of the defect immediately
- 2
Communicate the issue to your supervisor and relevant team members
- 3
Document the defect details and impact on the shipment
- 4
Evaluate potential solutions or corrective actions
- 5
Decide on the best course of action to prevent future occurrences
Example Answers
I would first assess the defect to understand its implications. Then, I would promptly inform my supervisor and team. After documenting the issue, I would analyze possible solutions, such as reworking the products or holding the shipment until the defect is resolved.
If you are faced with multiple quality issues occurring at once, how would you prioritize which issue to address first?
How to Answer
- 1
Assess the impact of each issue on product safety and compliance
- 2
Evaluate the severity and frequency of each issue reported
- 3
Consider customer complaints and their potential effect on satisfaction
- 4
Determine resource availability to address each issue effectively
- 5
Use a priority matrix to visually rank issues based on the above factors
Example Answers
I would first evaluate which quality issues pose the greatest risk to safety and compliance. Then I would look at the frequency of each issue and prioritize those that occur more often. If any issues have resulted in customer complaints, those would be addressed immediately to maintain satisfaction.
Don't Just Read Quality Control Specialist Questions - Practice Answering Them!
Reading helps, but actual practice is what gets you hired. Our AI feedback system helps you improve your Quality Control Specialist interview answers in real-time.
Personalized feedback
Unlimited practice
Used by hundreds of successful candidates
How would you approach a scenario where a team member is frequently making mistakes in quality checks?
How to Answer
- 1
Observe the team member's process to identify specific mistakes
- 2
Provide constructive feedback in a private setting
- 3
Offer additional training or resources if needed
- 4
Encourage open communication for questions or concerns
- 5
Monitor improvement over time and recognize positive changes
Example Answers
I would first observe the team member's quality check process to pinpoint where they are making mistakes. Then, I would sit down with them privately to discuss my observations and offer constructive feedback. If the issues persist, I would suggest additional training to reinforce their skills.
If you need to give feedback to a supplier regarding the quality of materials they've provided, how would you handle the conversation?
How to Answer
- 1
Prepare specific examples of quality issues before the conversation.
- 2
Use clear and professional language to communicate the concerns.
- 3
Focus on the impact of the quality issues on production and deadlines.
- 4
Encourage a collaborative approach to resolve the issues.
- 5
Follow up with a summary email to ensure clarity and documentation.
Example Answers
I would start the conversation by referencing specific quality issues we've encountered, like the batch that had inconsistent sizing. Then, I'd explain how this affects our production and timelines. I would suggest we meet to discuss potential solutions together.
What would your response be if a major quality issue led to a product recall? Describe your recovery plan.
How to Answer
- 1
Acknowledge the gravity of the situation with empathy for affected customers
- 2
Outline immediate actions like halting production and ensuring safety
- 3
Detail communication strategies for informing stakeholders and customers
- 4
Describe steps for investigating the root cause to prevent recurrence
- 5
Explain how you would implement corrective actions and monitor results
Example Answers
If a major quality issue occurred, I would first ensure that production stops immediately to prevent further distribution of the defective product. I would then communicate transparently with customers and stakeholders, prioritizing their safety and informing them about the recall process. After gathering the necessary data, I would conduct a thorough investigation to identify the root cause of the problem and implement corrective actions, ensuring that we monitor the effectiveness of these changes going forward.
If you were tasked with training new hires in quality control protocols, how would you structure your training program?
How to Answer
- 1
Start with an overview of quality control principles and their importance
- 2
Incorporate hands-on activities to practice protocols in real scenarios
- 3
Utilize visual aids and documentation to reinforce key concepts
- 4
Provide regular feedback and opportunities for questions
- 5
End with assessments to evaluate understanding and retention
Example Answers
I would begin the training by explaining the core principles of quality control and why they matter. Then, I would conduct hands-on activities where new hires can apply these principles. Incorporating visual aids like charts or guides would help them understand better. Throughout the training, I would encourage questions and provide feedback. Finally, I would assess their understanding with a quiz or practical demonstration.
How would you manage quality control processes if your team were suddenly reduced in size and resources?
How to Answer
- 1
Prioritize key quality control processes to focus on critical areas.
- 2
Leverage technology and automation to streamline tasks.
- 3
Encourage team collaboration to share workload effectively.
- 4
Implement rigorous training to maintain quality standards.
- 5
Regularly review data and feedback to adapt quickly to changes.
Example Answers
If our team were reduced, I would first identify the most critical quality control processes that directly impact product quality. Then, I would look into automating routine tasks to save time and allow my team to focus on high-priority areas. Collaboration would be key, encouraging everyone to share responsibilities and ensure nothing falls through the cracks.
What would you do if you identified a potential risk in the production process that could affect product quality?
How to Answer
- 1
Immediately report the risk to your supervisor and relevant teams
- 2
Gather data to understand the impact of the risk on product quality
- 3
Propose a corrective action plan to mitigate the risk
- 4
Collaborate with the team to implement the proposed changes
- 5
Follow up to ensure the risk is resolved and monitor for any future issues
Example Answers
If I identified a potential risk in the production process, I would promptly inform my supervisor and gather the necessary data to assess its impact. Then, I would suggest a corrective action plan and work with my team to implement it, ensuring we monitor the situation afterwards.
If your company decided to implement a new quality management software, how would you approach the transition?
How to Answer
- 1
Assess current quality processes and identify specific needs
- 2
Involve stakeholders early to gather input and support
- 3
Create a detailed implementation plan with timelines and responsibilities
- 4
Provide comprehensive training for all users
- 5
Monitor and gather feedback post-implementation to make adjustments
Example Answers
I would start by evaluating our current quality processes to understand gaps. Then, I'd gather input from team members and stakeholders to ensure the new software meets our needs. After creating a clear implementation timeline, I'd focus on training everyone effectively before going live. Finally, I'd monitor its performance and collect feedback for any necessary tweaks.
How would you facilitate collaboration within your team to ensure that quality standards are met consistently?
How to Answer
- 1
Encourage open communication and regular feedback among team members
- 2
Implement team meetings to discuss quality goals and challenges
- 3
Use collaborative tools for tracking quality metrics and progress
- 4
Assign specific roles and responsibilities to promote accountability
- 5
Celebrate successes and learn from mistakes as a team
Example Answers
I would set up weekly team meetings to discuss our quality goals and any challenges we face, ensuring everyone has a voice.
Don't Just Read Quality Control Specialist Questions - Practice Answering Them!
Reading helps, but actual practice is what gets you hired. Our AI feedback system helps you improve your Quality Control Specialist interview answers in real-time.
Personalized feedback
Unlimited practice
Used by hundreds of successful candidates
Quality Control Specialist Position Details
Salary Information
Recommended Job Boards
These job boards are ranked by relevance for this position.
Related Positions
Ace Your Next Interview!
Practice with AI feedback & get hired faster
Personalized feedback
Used by hundreds of successful candidates
Ace Your Next Interview!
Practice with AI feedback & get hired faster
Personalized feedback
Used by hundreds of successful candidates