Top 30 Quality Specialist Interview Questions and Answers [Updated 2025]
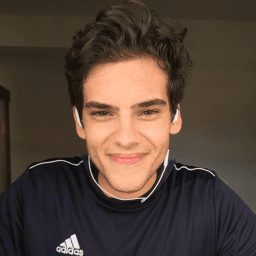
Andre Mendes
•
March 30, 2025
Preparing for a Quality Specialist interview can be daunting, but we're here to help you shine! In this blog post, you'll find the most common interview questions for the Quality Specialist role, complete with example answers and insightful tips to help you respond effectively. Whether you're a seasoned professional or just starting, this guide will equip you with the confidence to excel in your interview.
Download Quality Specialist Interview Questions in PDF
To make your preparation even more convenient, we've compiled all these top Quality Specialistinterview questions and answers into a handy PDF.
Click the button below to download the PDF and have easy access to these essential questions anytime, anywhere:
List of Quality Specialist Interview Questions
Behavioral Interview Questions
Can you tell me about a time when you identified a significant quality issue in a project and how you resolved it?
How to Answer
- 1
Choose a specific project where a quality issue was present
- 2
Describe the issue clearly and concisely
- 3
Explain how you identified the issue using data or testing
- 4
Detail the steps you took to resolve the issue
- 5
Reflect on the positive outcome and what you learned
Example Answers
In a previous project, we discovered late in development that a key feature was causing crashes in user environments. I identified this through rigorous testing and user feedback. I escalated the issue to the team, led a focused troubleshooting session, and we resolved the problem by rewriting the affected code segment, which improved stability and user satisfaction.
Describe a situation where you worked with a cross-functional team to improve product quality. What was your role?
How to Answer
- 1
Choose a specific project and clearly define your role.
- 2
Highlight collaboration with other team members and departments.
- 3
Mention the quality issue you were addressing and the methods used to improve it.
- 4
Include measurable results or impacts of the improvements made.
- 5
Reflect on what you learned from the experience.
Example Answers
In a recent project, I was part of a cross-functional team where we identified a recurring defect in our software product. As the Quality Engineer, I collaborated with developers and product managers to analyze the root cause. We implemented a new testing protocol that reduced the defect rate by 30% over the next release cycle. This experience taught me the importance of teamwork in quality improvement.
Don't Just Read Quality Specialist Questions - Practice Answering Them!
Reading helps, but actual practice is what gets you hired. Our AI feedback system helps you improve your Quality Specialist interview answers in real-time.
Personalized feedback
Unlimited practice
Used by hundreds of successful candidates
Tell me about a time when you had a disagreement with a coworker over a quality standard. How did you handle it?
How to Answer
- 1
Describe the situation clearly without placing blame.
- 2
Focus on how you communicated your perspective calmly.
- 3
Emphasize your willingness to find common ground.
- 4
Talk about the resolution and any changes implemented.
- 5
Highlight what you learned from the experience.
Example Answers
In a team project, a coworker preferred a more lenient quality standard than I believed was necessary. I arranged a meeting where we discussed our perspectives openly. I presented data supporting stricter standards, and we eventually agreed on a compromise that satisfied both sides. This experience taught me the importance of collaboration and evidence-based discussions.
Can you give an example of a time you led an initiative to improve the quality process in your team?
How to Answer
- 1
Identify a specific quality issue your team faced.
- 2
Explain the initiative you proposed to address this issue.
- 3
Describe your role in leading this initiative.
- 4
Highlight the impact and results of your initiative.
- 5
Use metrics or feedback to demonstrate improvement.
Example Answers
In my previous role, we had frequent bugs in the software releases. I led an initiative to implement a peer code review process where every code change had to be reviewed by at least two team members. As a result, we saw a 30% reduction in bugs in our next release cycle.
Describe a time when your attention to detail caught a potential defect or issue before it became a problem.
How to Answer
- 1
Think of a specific project where attention to detail was crucial
- 2
Explain the context and what you were responsible for
- 3
Describe the defect or issue you identified
- 4
Highlight the action you took to address it
- 5
Note the positive outcome and any feedback you received
Example Answers
In a previous project, while testing a new software version, I noticed a misalignment in the user interface that could confuse users. I immediately reported it to the development team and it was corrected before launch. This attention to detail ensured a smoother user experience and received praise from both my team and management.
Can you describe a time when you had to quickly learn a new skill or tool to maintain quality standards?
How to Answer
- 1
Choose a specific instance where you had to learn quickly.
- 2
Explain why the new skill or tool was needed to maintain quality.
- 3
Describe your learning process and the resources you used.
- 4
Share the outcome of your efforts and how it benefited the project.
- 5
Reflect on what you learned from the experience for future situations.
Example Answers
In my last job, we transitioned to a new test automation tool, Selenium. I quickly enrolled in an online course and practiced through hands-on projects. This allowed me to write new automated tests, which we needed to meet our release deadlines. As a result, our bug detection rate improved significantly.
Tell me about a time when you realized customer feedback was crucial to improving product quality. How did you act on it?
How to Answer
- 1
Identify a specific instance where customer feedback highlighted a product issue.
- 2
Describe the issue and the customer feedback that brought it to your attention.
- 3
Explain the steps you took to address the feedback and improve the product.
- 4
Highlight the outcomes of your actions and any follow-up you did with customers.
- 5
Emphasize the importance of customer input in quality assurance processes.
Example Answers
In my previous role, we received feedback that a particular feature was confusing to users. I organized a meeting with the development team to discuss these issues and we implemented a redesign based on user suggestions. After the changes, we saw a 30% decrease in support tickets related to that feature, showing the impact of user feedback.
Have you ever implemented a novel technique to solve a recurring quality issue? What was the result?
How to Answer
- 1
Identify a specific recurring quality issue you faced.
- 2
Describe the novel technique you implemented clearly.
- 3
Explain the process you followed to apply this technique.
- 4
Share measurable outcomes or improvements that resulted from this action.
- 5
Highlight any skills or tools you utilized in the process.
Example Answers
In my previous role, we faced a recurring issue with product defects during assembly. I implemented a new automated inspection technique using machine learning. We trained a model on historical defect data, enabling real-time feedback during production. As a result, we reduced defects by 30% in three months.
Describe a time when you had to adapt to a major change in quality requirements or standards. How did you handle it?
How to Answer
- 1
Identify a specific instance where quality requirements changed.
- 2
Explain the new requirements and why they were necessary.
- 3
Describe the steps you took to adapt to the changes.
- 4
Highlight any challenges you faced and how you overcame them.
- 5
Conclude with the results and what you learned from the experience.
Example Answers
In my previous role, we had a shift to ISO 9001 standards. I organized training sessions for our team to understand the new requirements. We updated our processes and documentation accordingly. This helped us pass the certification audit on our first attempt, and our defect rates improved significantly.
Technical Interview Questions
What quality management systems and standards are you most familiar with, and how have you applied them?
How to Answer
- 1
Identify key quality management systems like ISO 9001 or Six Sigma.
- 2
Relate your experience with specific projects where you implemented these standards.
- 3
Discuss tools or methodologies you used in line with these systems.
- 4
Highlight the impact of these systems on project outcomes.
- 5
Be prepared to discuss challenges faced and how you overcame them.
Example Answers
I am most familiar with ISO 9001 and used it in my previous job to streamline our documentation process, which reduced errors by 15%. I implemented regular audits to ensure compliance.
How do you use data analysis to assess product quality, and which tools do you prefer?
How to Answer
- 1
Identify key quality metrics relevant to the product
- 2
Explain how you gather and analyze data on these metrics
- 3
Discuss any statistical methods or tools you use, like Minitab or Excel
- 4
Mention how you present data findings to stakeholders
- 5
Share an example of a data-driven decision you made related to product quality
Example Answers
I track metrics like defect rates and customer feedback scores. I use Excel for data analysis and create pivot tables to summarize the data. Once analyzed, I present my findings in charts to help the team make informed decisions about product improvements.
Don't Just Read Quality Specialist Questions - Practice Answering Them!
Reading helps, but actual practice is what gets you hired. Our AI feedback system helps you improve your Quality Specialist interview answers in real-time.
Personalized feedback
Unlimited practice
Used by hundreds of successful candidates
What techniques do you use for root cause analysis when a defect is found?
How to Answer
- 1
Start with defining the problem clearly and gather relevant data.
- 2
Use techniques like the 5 Whys or Fishbone Diagram to identify underlying causes.
- 3
Involve cross-functional teams to gain different perspectives.
- 4
Document findings and develop an action plan to address the root cause.
- 5
Follow up to ensure the solution was effective and the issue does not recur.
Example Answers
When a defect is identified, I first gather all related data to define the issue clearly. I often use the 5 Whys technique, digging deep into each answer until we reach the core problem. Then, I collaborate with my team to brainstorm solutions and document our findings to implement an action plan.
Explain a process improvement method you have used in your previous work and its impact.
How to Answer
- 1
Identify a specific process improvement method you used.
- 2
Describe the context or problem that prompted the improvement.
- 3
Explain the steps you took to implement the improvement.
- 4
Quantify the impact or results of the improvement where possible.
- 5
Keep your answer structured and to the point.
Example Answers
In my previous role, I applied the Lean Six Sigma methodology to reduce the cycle time in our testing process. We identified bottlenecks that caused delays, implemented a more streamlined workflow, and reduced cycle time by 30%, which significantly improved our delivery timelines.
What are the key inspection methods you use to evaluate product quality?
How to Answer
- 1
Identify the inspection methods relevant to your experience such as visual inspection, testing, and measurements.
- 2
Explain the purpose of each method in ensuring quality standards are met.
- 3
Mention any specific tools or software you use during inspections.
- 4
Discuss how you document inspection results and follow up on defects.
- 5
Relate your methods to the specific industry or products relevant to the role.
Example Answers
I primarily use visual inspection for identifying surface defects, along with measurement tools like calipers for dimensional accuracy. I also employ automated testing methods and document all findings in our quality management system.
How do you ensure that your project complies with relevant quality and safety regulations?
How to Answer
- 1
Identify all applicable regulations early in the project.
- 2
Incorporate compliance checks into your project timeline.
- 3
Engage with regulatory bodies for updates and clarifications.
- 4
Conduct regular audits and reviews during the project lifecycle.
- 5
Train your team on relevant quality and safety standards.
Example Answers
I begin by researching all relevant regulations for the project scope, then create a compliance checklist. I integrate regular compliance reviews into our project meetings to ensure we stay aligned.
Can you explain how you apply statistical process control in quality engineering?
How to Answer
- 1
Define statistical process control (SPC) succinctly.
- 2
Explain how you use control charts to monitor process variation.
- 3
Discuss the role of data collection and analysis in SPC.
- 4
Give examples of how SPC has improved quality in past projects.
- 5
Mention any specific tools or software you use for SPC.
Example Answers
Statistical process control involves using statistical methods to monitor and control a process. I use control charts to visualize data and detect any variations outside the control limits. For example, in my last role, we reduced defects by implementing weekly control chart analysis.
What tools or frameworks have you used to ensure software quality in product development?
How to Answer
- 1
Identify specific tools you have used directly in your projects.
- 2
Mention frameworks that facilitate testing, code quality, or continuous integration.
- 3
Highlight your role in implementing or using these tools effectively.
- 4
Connect tools to the quality outcomes they helped achieve.
- 5
Be ready to discuss a particular project where these were applied.
Example Answers
In my last role, I extensively used Selenium for automated testing of our web applications. It streamlined our testing process and helped reduce bugs in production.
How do you approach developing a comprehensive test plan for a new product?
How to Answer
- 1
Understand the product requirements and specifications clearly
- 2
Identify key areas of risk and focus on those
- 3
Define the scope of testing, including types and levels of testing
- 4
Determine the necessary resources and timelines for testing
- 5
Create a structured format for the test plan that includes objectives, strategies, and metrics.
Example Answers
I start by reviewing the product requirements to ensure I understand what needs to be tested. Then, I identify the most critical features and potential risks. I outline the scope of testing, like functional and performance tests, and I allocate resources accordingly. Finally, I compile a test plan that documents all these elements clearly.
What strategies do you use in defect tracking and reporting?
How to Answer
- 1
Leverage tools like JIRA or Bugzilla for efficient tracking
- 2
Prioritize defects based on severity and impact
- 3
Ensure clear, concise documentation of each defect
- 4
Provide regular updates and summaries to the team
- 5
Collaborate with developers for quick resolution of critical issues
Example Answers
I use JIRA for tracking defects, focusing on severity to prioritize them. I document each defect with clear steps to reproduce and ensure I communicate updates during stand-ups.
Don't Just Read Quality Specialist Questions - Practice Answering Them!
Reading helps, but actual practice is what gets you hired. Our AI feedback system helps you improve your Quality Specialist interview answers in real-time.
Personalized feedback
Unlimited practice
Used by hundreds of successful candidates
Describe your experience with quality automation tools and scripting.
How to Answer
- 1
Start by listing the specific automation tools you have used.
- 2
Mention the types of projects or applications where you applied these tools.
- 3
Highlight any scripting languages you are proficient in, such as Python or JavaScript.
- 4
Include examples of how your automation improved the testing process or product quality.
- 5
Conclude with any certifications or training related to quality automation.
Example Answers
I have experience using Selenium and JUnit for automation testing in web applications. On a project, I created test scripts in Java that reduced manual testing by 40%. I am also proficient in Python, which I used to automate API testing with requests and unittest.
How do you ensure quality control across a diverse supply chain?
How to Answer
- 1
Establish clear quality standards for all suppliers and communicate them effectively
- 2
Implement regular audits and inspections to monitor compliance with quality standards
- 3
Utilize quality management tools like Six Sigma or ISO standards for consistent processes
- 4
Foster strong relationships with suppliers to encourage transparency and continuous improvement
- 5
Leverage data analytics to track quality metrics and identify trends or areas of concern
Example Answers
To ensure quality control across a diverse supply chain, I establish clear quality standards for all suppliers and communicate those effectively. I also implement regular audits to monitor compliance and use data analytics to track quality metrics across the chain.
Situational Interview Questions
Imagine a situation where a product is behind schedule and quality might be compromised. How would you manage this risk?
How to Answer
- 1
Assess the specific quality risks associated with the delay.
- 2
Communicate transparently with stakeholders about potential impacts.
- 3
Prioritize critical quality features before minor ones.
- 4
Implement additional testing strategies to mitigate risks.
- 5
Suggest a phased approach to release that maintains quality standards.
Example Answers
I would first identify the key quality risks due to delays, then inform the team about these risks. By prioritizing the most critical features, we can focus resources effectively. I would propose increasing our testing frequency to catch any quality issues early. Finally, I would suggest a phased release allowing us to deliver a product without compromising on essential quality aspects.
You are asked to propose a new quality assurance technology that could benefit your team. How would you approach this task?
How to Answer
- 1
Research current trends in quality assurance technologies.
- 2
Identify a specific challenge your team is facing.
- 3
Suggest a technology that addresses the identified challenge.
- 4
Explain the potential impact on efficiency or quality.
- 5
Be prepared to discuss implementation considerations.
Example Answers
I would propose implementing a test automation tool like Selenium. Our team struggles with manual testing efficiency, and automation can significantly reduce time spent on repetitive tasks, ensuring faster delivery.
Don't Just Read Quality Specialist Questions - Practice Answering Them!
Reading helps, but actual practice is what gets you hired. Our AI feedback system helps you improve your Quality Specialist interview answers in real-time.
Personalized feedback
Unlimited practice
Used by hundreds of successful candidates
A client reports that a product does not meet their quality expectations. How would you address this situation?
How to Answer
- 1
Acknowledge the client's concern immediately
- 2
Gather detailed information about the specific quality issues
- 3
Analyze the product and the reported issues critically
- 4
Communicate with relevant team members to investigate causes
- 5
Provide a clear plan of action and follow up with the client
Example Answers
I would first acknowledge the client's concerns and thank them for bringing it to my attention. Then, I would ask for specific details regarding the quality issues they are experiencing. After gathering this information, I would coordinate with the engineering team to analyze the product and identify any potential defects. Finally, I would present a corrective action plan to the client and ensure I follow up to confirm their satisfaction.
A product is failing after being released into the market. What steps would you take to investigate and resolve the issue?
How to Answer
- 1
Gather data on the failures reported by users.
- 2
Analyze the product's specifications and requirements to identify gaps.
- 3
Conduct root cause analysis to determine the underlying issues.
- 4
Communicate with stakeholders for insights and possible solutions.
- 5
Implement a testing phase for the fixes before re-releasing the product.
Example Answers
I would first gather all user reports and data related to the product failures. Then, I'd analyze the product against its initial requirements to see where it may have fallen short. Using root cause analysis, I'd identify the main issues, engage with the stakeholders for their input, and then develop a test plan for the fixes before the relaunch.
A project deadline is fast approaching, but you discover a major quality issue. How do you balance the urgency versus ensuring quality?
How to Answer
- 1
Assess the severity of the quality issue immediately
- 2
Communicate the issue to stakeholders transparently
- 3
Propose a timeline with options to address the issue
- 4
Prioritize critical fixes that impact overall quality
- 5
Consider temporary workarounds if absolutely necessary
Example Answers
I would quickly assess the severity of the issue and communicate it to my team and stakeholders. Then, I would propose a plan to fix the issue while considering the project's timeline.
If given limited resources, how would you prioritize quality activities in your project?
How to Answer
- 1
Identify the critical quality activities that impact customer satisfaction the most
- 2
Assess the risk of defects and focus on high-risk areas first
- 3
Leverage automation for repetitive testing to save time and resources
- 4
Engage the team in prioritization discussions to align on key quality goals
- 5
Continuously monitor and adjust priorities based on project feedback
Example Answers
I would first identify the key quality activities that directly affect customer satisfaction, such as functional testing of critical features. Then, I'd assess risk areas and prioritize testing in those high-risk zones. I would also implement automation for regression tests to maximize efficiency.
How would you handle a situation where a supplier consistently provides subpar components that affect product quality?
How to Answer
- 1
Document specific instances of poor quality from the supplier
- 2
Communicate directly with the supplier to address the issues
- 3
Implement a quality assurance process to monitor their components
- 4
Suggest corrective actions and offer assistance to help improve their processes
- 5
Consider alternative suppliers if improvements are not made within a reasonable timeframe
Example Answers
I would first document the specific instances of subpar components and then set up a meeting with the supplier to discuss the impacts on our product quality. I'd work with them to implement corrective actions and maintain close communication during this process.
A critical quality failure has occurred. The CEO wants a report immediately. How do you handle this pressure?
How to Answer
- 1
Stay calm and assess the situation quickly.
- 2
Gather relevant data and facts about the failure.
- 3
Identify the root cause or potential causes of the failure.
- 4
Prioritize key information that the CEO needs to know.
- 5
Communicate clearly and concisely in your report.
Example Answers
I would take a deep breath to remain calm, then quickly gather data on the failure. I’d analyze it for root causes and draft a concise report that highlights the issue, potential impacts, and initial remedies.
Your team is understaffed in one area of quality inspection. How would you ensure quality standards are maintained?
How to Answer
- 1
Prioritize critical inspections that directly impact product quality.
- 2
Implement streamlined processes to enhance efficiency in quality checks.
- 3
Utilize automated tools or software to assist in inspections.
- 4
Foster a collaborative environment and involve cross-functional team members for support.
- 5
Continuously monitor and evaluate quality metrics to identify areas needing attention.
Example Answers
I would start by identifying the most critical inspections and focus on those. Streamlining processes and using automated tools can help us maintain efficiency. Additionally, I would communicate with other team members to see if anyone can assist, ensuring we cover the essentials.
Quality Specialist Position Details
Recommended Job Boards
CareerBuilder
www.careerbuilder.com/jobs-quality-specialistZipRecruiter
www.ziprecruiter.com/Jobs/Quality-SpecialistThese job boards are ranked by relevance for this position.
Related Positions
Ace Your Next Interview!
Practice with AI feedback & get hired faster
Personalized feedback
Used by hundreds of successful candidates
Ace Your Next Interview!
Practice with AI feedback & get hired faster
Personalized feedback
Used by hundreds of successful candidates