Top 30 Production Analyst Interview Questions and Answers [Updated 2025]
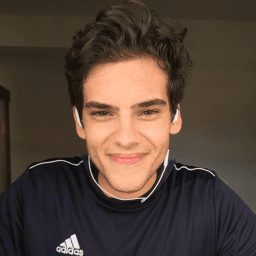
Andre Mendes
•
March 30, 2025
Preparing for a Production Analyst interview can be daunting, but we're here to help. In this post, you'll find a curated list of the most common interview questions for the Production Analyst role, complete with example answers and practical tips for responding effectively. Whether you're a seasoned professional or just starting, this guide will equip you with the insights needed to ace your interview with confidence.
Download Production Analyst Interview Questions in PDF
To make your preparation even more convenient, we've compiled all these top Production Analystinterview questions and answers into a handy PDF.
Click the button below to download the PDF and have easy access to these essential questions anytime, anywhere:
List of Production Analyst Interview Questions
Technical Interview Questions
How do you ensure accuracy and clarity in your production analysis reports?
How to Answer
- 1
Use standardized templates for consistency in reports
- 2
Perform data validation checks before analysis
- 3
Incorporate visual aids such as charts for clarity
- 4
Collaborate with team members for feedback on reports
- 5
Regularly review and update reporting processes based on lessons learned
Example Answers
I ensure accuracy by performing thorough data validation checks before starting the analysis and using standardized templates to maintain consistency. I also incorporate visual aids like charts to help illustrate key points clearly.
What tools and techniques do you typically use when conducting production data analysis?
How to Answer
- 1
Mention specific tools you use, like Excel, SQL, or data visualization software.
- 2
Explain techniques such as statistical analysis, trend analysis, or forecasting.
- 3
Discuss how you validate and clean data before analysis.
- 4
Highlight any collaboration with teams for gathering requirements.
- 5
Provide examples of how your analysis led to actionable insights.
Example Answers
I typically use SQL for querying databases and Excel for data manipulation. I perform trend analysis to identify patterns, and I always clean my data to ensure accuracy. Last quarter, my analysis helped reduce downtime by 15%.
Don't Just Read Production Analyst Questions - Practice Answering Them!
Reading helps, but actual practice is what gets you hired. Our AI feedback system helps you improve your Production Analyst interview answers in real-time.
Personalized feedback
Unlimited practice
Used by hundreds of successful candidates
How proficient are you with SQL and Excel, and how have you used these tools in your previous roles as a Production Analyst?
How to Answer
- 1
Clearly state your proficiency level with SQL and Excel, be specific about your skills.
- 2
Provide specific examples of tasks you completed using SQL and Excel.
- 3
Mention any relevant projects or reports you generated with these tools.
- 4
Highlight how your skills positively impacted the production processes.
- 5
If applicable, indicate any certifications or trainings related to SQL and Excel.
Example Answers
I am highly proficient in SQL, having regularly used it to query large datasets for trend analysis and reporting. For example, in my previous role, I wrote complex SQL queries that helped identify production bottlenecks, leading to a 15% reduction in downtime. Additionally, I am very comfortable with Excel, utilizing it for data visualization and creating dashboards to present key performance indicators to management.
What key performance indicators (KPIs) do you consider essential for evaluating production performance?
How to Answer
- 1
Identify KPIs relevant to production goals.
- 2
Mention specific metrics like efficiency, yield, and downtime.
- 3
Explain the importance of each KPI in context.
- 4
Use examples from past experiences if possible.
- 5
Conclude by linking KPIs to overall production improvement.
Example Answers
I consider efficiency, yield, and downtime as essential KPIs. Efficiency measures how well resources are utilized, yield shows the quality of the output, and downtime assesses how often production is halted. Tracking these helps identify areas for improvement.
What statistical methods do you use to analyze production data, and can you give an example of how you've applied these methods?
How to Answer
- 1
Identify specific statistical methods you are familiar with, such as regression analysis or time series analysis.
- 2
Explain how you have used these methods in past roles or projects with concrete examples.
- 3
Mention any software tools you used to perform these analyses, like Excel, R, or Python.
- 4
Focus on results and impact your analysis had on production efficiency or quality.
- 5
Be ready to discuss how you interpreted the results and made recommendations based on your findings.
Example Answers
In my previous role, I frequently used regression analysis to examine the relationship between machine settings and production output. For instance, I analyzed data from our assembly line and discovered that adjusting the speed of one machine by 10% could increase output by 15%. I presented this finding to the engineering team, and we implemented the changes, which improved our overall production efficiency.
What experience do you have with managing production databases, and how do you ensure data integrity?
How to Answer
- 1
Highlight specific databases you have worked with.
- 2
Mention tools or technologies used in database management.
- 3
Describe your strategies for maintaining data accuracy.
- 4
Include examples of challenges faced and solutions implemented.
- 5
Emphasize your attention to backup and recovery processes.
Example Answers
In my previous role, I managed SQL Server databases where I implemented strict data validation rules and conducted regular audits to ensure data integrity.
What is your process for conducting root cause analysis in production issues?
How to Answer
- 1
Define the problem clearly with specific examples
- 2
Gather and analyze relevant data to find patterns
- 3
Identify possible root causes through brainstorming
- 4
Validate these root causes with testing or further analysis
- 5
Implement corrective actions and monitor results
Example Answers
I start by clearly defining the production issue and gathering data to understand the scope. Then I look for patterns in that data. Next, I brainstorm possible root causes and validate them through tests or simulations. Finally, I implement a solution and monitor the outcome to ensure effectiveness.
How familiar are you with Lean manufacturing principles, and how have you applied them in your work?
How to Answer
- 1
Understand key Lean principles like value stream mapping, Kaizen, and waste reduction
- 2
Provide specific examples from your previous jobs
- 3
Explain the impact of your actions on efficiency or productivity
- 4
Mention any relevant tools or techniques you used
- 5
Be ready to discuss outcomes or metrics that illustrate success
Example Answers
In my previous role as a production technician, I facilitated a Kaizen workshop which helped identify and eliminate overstock issues, reducing our inventory by 20%.
How do you identify opportunities for process improvement in production, and can you share an example?
How to Answer
- 1
Analyze production data for inefficiencies and bottlenecks.
- 2
Engage with team members for insights and suggestions on current processes.
- 3
Implement small pilot projects to test improvements before full-scale changes.
- 4
Continuously monitor results to ensure improvements are effective.
- 5
Document processes and changes to maintain clarity and consistency.
Example Answers
I routinely review production metrics to find bottlenecks. Last quarter, I noticed a delay in machine setup times, so I gathered input from operators and we streamlined the setup process, reducing downtime by 15%.
What is your experience with Six Sigma methodologies, and how have you used them in production analysis?
How to Answer
- 1
Discuss specific projects where you applied Six Sigma.
- 2
Explain the process improvements you achieved using Six Sigma.
- 3
Mention any certifications or training in Six Sigma methodologies.
- 4
Provide metrics or data that showcase the impact of your work.
- 5
Link your experience back to the production analyst role and its requirements.
Example Answers
In my previous role, I led a Six Sigma project to reduce defects in our production line. By applying DMAIC, we identified root causes and implemented process changes, reducing defects by 30%.
Don't Just Read Production Analyst Questions - Practice Answering Them!
Reading helps, but actual practice is what gets you hired. Our AI feedback system helps you improve your Production Analyst interview answers in real-time.
Personalized feedback
Unlimited practice
Used by hundreds of successful candidates
Behavioral Interview Questions
Tell me about a time when you had to work closely with a team to analyze production data. What role did you play and what was the outcome?
How to Answer
- 1
Think of a specific project involving production data analysis.
- 2
Describe your role clearly and your contributions to the team.
- 3
Focus on teamwork and collaboration aspects.
- 4
Mention any tools or methods used in the analysis.
- 5
Highlight the positive outcome and its impact on production efficiency.
Example Answers
In my last position, our team was tasked with analyzing production downtime data. I coordinated with the data analysts to gather the necessary metrics and used Excel to create a dashboard to visualize the bottlenecks. Together, we identified recurring issues that reduced efficiency by 15%, which we presented to management. As a result, they initiated a new maintenance schedule and we saw a 20% increase in productivity over the following months.
Describe a time when you identified a small error in production data that had a significant impact. How did you handle it?
How to Answer
- 1
Start by briefly describing the context and the data involved.
- 2
Clearly explain the small error you found and why it was significant.
- 3
Discuss the steps you took to address the error.
- 4
Highlight any collaboration with team members to resolve the issue.
- 5
Conclude with the outcome and any improvements made to prevent future errors.
Example Answers
In my previous role, I was analyzing production data when I noticed a discrepancy in the output numbers. The error was a single digit wrong in our monthly report, leading to a 10% overestimation of our output. I immediately alerted my supervisor and we convened a meeting with the data team. We corrected the report and adjusted next month’s targets accordingly. As a result, we improved our data validation process to catch such errors early.
Don't Just Read Production Analyst Questions - Practice Answering Them!
Reading helps, but actual practice is what gets you hired. Our AI feedback system helps you improve your Production Analyst interview answers in real-time.
Personalized feedback
Unlimited practice
Used by hundreds of successful candidates
Can you describe a challenging problem in production analysis that you solved successfully? What steps did you take to solve it?
How to Answer
- 1
Identify a specific challenge you faced in production analysis.
- 2
Explain the context and why it was a problem.
- 3
Detail the steps you took to investigate and analyze the issue.
- 4
Discuss the solution you implemented and its outcomes.
- 5
Reflect on what you learned from the experience.
Example Answers
In my previous role, we faced discrepancies in our inventory data. I analyzed the production reports and realized the counting method was flawed. I collaborated with the warehouse team to revamp the counting procedure, implemented regular audits, and trained staff. This reduced discrepancies by 30% and improved overall data accuracy.
Give an example of how you prioritize your tasks when you have multiple deadlines approaching.
How to Answer
- 1
Identify the most urgent tasks based on deadlines and impact.
- 2
Use a task management tool to list and categorize tasks.
- 3
Allocate time blocks to each high-priority task.
- 4
Communicate with team members to clarify priorities if needed.
- 5
Stay flexible and ready to adjust priorities as new information emerges.
Example Answers
I list all my tasks and deadlines, then use a priority matrix to identify which tasks are urgent and important. For example, if a report is due tomorrow while other tasks have later deadlines, I focus my efforts on completing the report first.
Describe a time when you had a disagreement with a colleague about a production analysis finding. How did you resolve it?
How to Answer
- 1
Focus on a specific instance and clearly outline the disagreement.
- 2
Explain the analysis finding and your perspective.
- 3
Describe how you listened to your colleague and considered their viewpoint.
- 4
Highlight the steps you took to resolve the disagreement, such as collaborating on further analysis.
- 5
Conclude with the outcome and what you learned from the experience.
Example Answers
In my previous role, I disagreed with a colleague about the interpretation of production SLA data. I took the time to clarify my analysis and listened to their perspective. We agreed to review the data together and found additional metrics to consider. This collaboration led us to a shared conclusion that improved our reporting process.
Tell me about a time you took the initiative to improve a production process. What actions did you take and what was the impact?
How to Answer
- 1
Choose a specific process you improved, focus on one example.
- 2
Clearly outline the problem that needed improvement.
- 3
Describe the steps you took to address the problem.
- 4
Mention any data or metrics that show the impact of your actions.
- 5
Keep it concise and to the point, focusing on your initiative.
Example Answers
At my previous job, I noticed the inventory tracking was inaccurate, causing delays in production. I suggested implementing a new software system that integrated with our existing tools. I drove the software adoption and trained the team, leading to a 30% reduction in inventory discrepancies and improved delivery times.
Give an example of a time you led a project to improve production efficiency. What challenges did you face and how did you overcome them?
How to Answer
- 1
Start with a clear project description and your role.
- 2
Describe specific efficiency metrics or goals you aimed to achieve.
- 3
Highlight the main challenges you encountered during the project.
- 4
Explain the strategies you implemented to overcome these challenges.
- 5
Conclude with the outcomes or results of the project.
Example Answers
In my previous role at XYZ Company, I led a project to streamline our production line, aiming to reduce cycle time by 20%. One challenge was resistance from the team, as they were accustomed to the old processes. I organized workshops to demonstrate the benefits of the new approach and involved team members in the decision-making process. Ultimately, we achieved a 25% reduction in cycle time and heightened team morale.
Describe a situation where a sudden change impacted your production analysis work. How did you adapt?
How to Answer
- 1
Think of a specific example from your past experiences.
- 2
Explain the nature of the sudden change clearly.
- 3
Describe the actions you took to adapt to the change.
- 4
Focus on the outcomes of your actions and what you learned.
- 5
Keep it concise and relevant to production analysis.
Example Answers
In my previous role, our production schedule was suddenly moved up by two weeks due to a client request. I quickly assessed the current production data and prioritized tasks to meet the new deadline. I communicated with the team to ensure everyone was aligned and we managed to meet the deadline while maintaining quality. This taught me the importance of flexibility and effective communication in production analysis.
Can you provide an example of how your critical thinking helped solve a production problem?
How to Answer
- 1
Identify a specific production problem you faced
- 2
Explain your thought process in analyzing the issue
- 3
Describe the steps you took to address the problem
- 4
Highlight the outcome and any metrics or improvements
- 5
Keep it concise and focused on your critical thinking skills
Example Answers
In my previous role, we faced a delay in production due to equipment malfunction. I analyzed the malfunction patterns and discovered they were correlated with a specific operating condition. By adjusting the settings according to manufacturer recommendations, we resolved the issue and increased output by 20%.
Talk about an experience where collaboration led to improved production outcomes.
How to Answer
- 1
Describe a specific project or situation
- 2
Highlight your role and contributions in the collaboration
- 3
Explain how teamwork improved processes or results
- 4
Provide quantifiable outcomes if possible
- 5
Reflect on what you learned about collaboration
Example Answers
In my last role, I worked on a cross-functional team to streamline our production scheduling. By collaborating with the supply chain and sales teams, we identified bottlenecks that were causing delays. My contribution involved analyzing production data and suggesting a new scheduling approach. As a result, we reduced our lead time by 20%, improving our on-time delivery metrics significantly.
Don't Just Read Production Analyst Questions - Practice Answering Them!
Reading helps, but actual practice is what gets you hired. Our AI feedback system helps you improve your Production Analyst interview answers in real-time.
Personalized feedback
Unlimited practice
Used by hundreds of successful candidates
Situational Interview Questions
Imagine there is a sudden drop in production efficiency, and you need to identify the root cause. How would you approach this situation?
How to Answer
- 1
Start by gathering data on production metrics before and after the drop.
- 2
Identify key variables that may have changed, such as machinery, labor, or materials.
- 3
Conduct interviews with team members to get insights on observed issues.
- 4
Use root cause analysis tools like the 5 Whys or Fishbone diagram for structured investigation.
- 5
Implement short-term fixes while working on a long-term solution to prevent recurrence.
Example Answers
First, I would analyze production data to pinpoint when the drop began and compare it with previous performance. Next, I would check for any changes in equipment usage or material quality. Then, I would talk to the team to gather their observations. Using the 5 Whys method, I would analyze potential causes, and implement quick fixes in the meantime.
You have conflicting reports from two different data sources regarding production yield. How would you decide which one to trust?
How to Answer
- 1
Verify the reliability of each data source by checking their history and accuracy.
- 2
Look for recent updates or versions of the data that might explain discrepancies.
- 3
Cross-reference the reports with additional metrics or third-party data if available.
- 4
Consult with stakeholders or team members who may have insights on the data.
- 5
Document the decision-making process to ensure transparency on which source is trusted.
Example Answers
First, I would evaluate the credibility of both data sources by reviewing their past accuracy. Then, I would check if both reports were pulled from the same time frame or if one is more current. If discrepancies persist, I'd consult the production team to see if they experienced any operational changes that could affect yield.
Don't Just Read Production Analyst Questions - Practice Answering Them!
Reading helps, but actual practice is what gets you hired. Our AI feedback system helps you improve your Production Analyst interview answers in real-time.
Personalized feedback
Unlimited practice
Used by hundreds of successful candidates
You are tasked with finding ways to reduce production costs without affecting quality. What approach would you take?
How to Answer
- 1
Analyze current production processes to identify inefficiencies
- 2
Engage with team to gather ideas on cost-saving measures
- 3
Invest in training to improve workforce productivity
- 4
Explore suppliers for better material costs without compromising quality
- 5
Implement technology solutions to streamline operations
Example Answers
I would start by analyzing the current processes and looking for bottlenecks that waste resources. Engaging with team members can provide insights on potential improvements. Additionally, I would explore new technologies that can automate parts of production, thereby reducing labor costs and increasing efficiency.
A non-technical manager asks you to explain a complex data analysis finding. How would you communicate this information?
How to Answer
- 1
Use simple language to avoid technical jargon
- 2
Break down the findings into key points
- 3
Use analogies or examples relatable to the manager's experience
- 4
Focus on the implications of the findings, not just the data
- 5
Encourage questions to gauge understanding and clarify if needed
Example Answers
I would start by summarizing the main finding in one sentence, then explain it in terms of its impact on the team, using an analogy like comparing data trends to seasonal changes in sales.
How would you handle a situation where production resources are being underutilized?
How to Answer
- 1
Analyze data to identify patterns of underutilization
- 2
Engage with team members to understand bottlenecks or issues
- 3
Propose actionable changes to improve resource allocation
- 4
Monitor the impact of changes to ensure effectiveness
- 5
Report findings and improvements to management for transparency
Example Answers
I would first analyze production data to see where the underutilization is occurring. Then, I would talk to the team to see if there are any obstacles they face. Based on that, I would suggest reallocating resources or adjusting schedules to maximize usage.
How would you approach forecasting production trends in a new market with limited data?
How to Answer
- 1
Identify key indicators relevant to the market and similar industries.
- 2
Use qualitative research methods, such as interviews and surveys, to gather insights.
- 3
Leverage existing data from similar markets or historical trends to inform forecasts.
- 4
Engage with stakeholders for a deeper understanding of market dynamics.
- 5
Utilize forecasting models that can account for uncertainty, such as scenarios or Monte Carlo simulations.
Example Answers
To forecast production trends in a new market with limited data, I would start by analyzing available indicators from similar industries. Next, I would conduct interviews with local experts and potential consumers to gather qualitative insights. Additionally, I'd review historical data from analogous markets to build a comparative framework for my forecasts.
If you notice a decline in product quality, what steps would you take to address and resolve the issue?
How to Answer
- 1
Assess the data to identify specific quality issues
- 2
Gather feedback from the production team and stakeholders
- 3
Investigate root causes through a thorough analysis
- 4
Develop a corrective action plan with clear steps
- 5
Implement changes and monitor product quality closely
Example Answers
First, I would analyze production data to pinpoint what specific quality metrics have declined. Then, I would hold a meeting with the production team to gather insights and identify potential root causes. Next, I'd use techniques like the 5 Whys to drill down to the underlying issues, and finally, I would create a targeted action plan to improve quality and track the results over the next few production cycles.
You've been asked to present production data to stakeholders. How would you visually communicate this information?
How to Answer
- 1
Identify the key data points that the stakeholders care about
- 2
Choose appropriate visualizations such as charts, graphs, or dashboards
- 3
Keep visuals simple and direct to enhance understanding
- 4
Highlight trends and insights that are relevant to the stakeholders
- 5
Prepare to explain the visuals clearly and concisely during the presentation
Example Answers
I would start by identifying the key metrics that stakeholders need, such as production volume and efficiency trends. I would use line charts to show trends over time and pie charts for share distribution. Keeping it simple helps in quickly conveying the main message.
Consider a scenario where you need to assess the risk of a new production method. What factors would you analyze?
How to Answer
- 1
Identify potential safety risks to workers and equipment.
- 2
Evaluate the impact on production efficiency and output quality.
- 3
Analyze the cost implications and return on investment.
- 4
Assess compliance with industry regulations and standards.
- 5
Gather insights from stakeholders and expert opinions.
Example Answers
I would first evaluate any safety risks to workers and equipment, ensuring the new method complies with safety standards. Next, I would assess how it impacts production efficiency and output quality to avoid disruptions. Additionally, analyzing cost implications and ROI is crucial to ensure financial viability.
Describe how you would handle a situation where there is an unexpected halt in the production line.
How to Answer
- 1
Stay calm and assess the situation quickly.
- 2
Gather information from the team about the cause of the halt.
- 3
Prioritize resolving the issue based on its impact on production.
- 4
Communicate clearly with all stakeholders about the status.
- 5
Implement a solution and monitor the line until it is stable again.
Example Answers
First, I would stay calm and try to quickly gather information from my team to understand the cause of the production halt. Then, I would assess the impact of the issue and prioritize resolving it. I’d clearly communicate the status to both my team and management. Once a solution is implemented, I would monitor the production line to ensure stability.
Don't Just Read Production Analyst Questions - Practice Answering Them!
Reading helps, but actual practice is what gets you hired. Our AI feedback system helps you improve your Production Analyst interview answers in real-time.
Personalized feedback
Unlimited practice
Used by hundreds of successful candidates
Production Analyst Position Details
Salary Information
Recommended Job Boards
CareerBuilder
www.careerbuilder.com/jobs/production-analystZipRecruiter
www.ziprecruiter.com/Jobs/Production-AnalystThese job boards are ranked by relevance for this position.
Related Positions
Ace Your Next Interview!
Practice with AI feedback & get hired faster
Personalized feedback
Used by hundreds of successful candidates
Ace Your Next Interview!
Practice with AI feedback & get hired faster
Personalized feedback
Used by hundreds of successful candidates