Top 30 Industrial Technologist Interview Questions and Answers [Updated 2025]
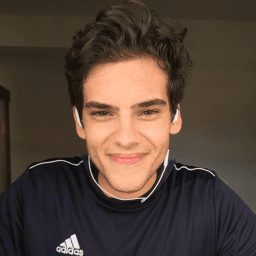
Andre Mendes
•
March 30, 2025
Preparing for an industrial technologist interview can be daunting, but we're here to help you navigate the process with confidence. In this updated guide for 2025, we delve into the most common interview questions faced by candidates in this dynamic field. You'll find example answers and insightful tips on how to effectively respond, equipping you with the tools to impress your potential employers and land your dream job.
Download Industrial Technologist Interview Questions in PDF
To make your preparation even more convenient, we've compiled all these top Industrial Technologistinterview questions and answers into a handy PDF.
Click the button below to download the PDF and have easy access to these essential questions anytime, anywhere:
List of Industrial Technologist Interview Questions
Technical Interview Questions
How do you implement quality control measures in a production environment?
How to Answer
- 1
Identify key quality metrics relevant to the production process
- 2
Implement regular inspections and testing at critical points
- 3
Utilize statistical process control to monitor production
- 4
Ensure team training on quality standards and procedures
- 5
Collect and analyze feedback for continuous improvement
Example Answers
I implement quality control by first identifying metrics like defect rates and product specifications. Then, I set up inspections at each stage of production to catch issues early.
What project management tools and methodologies do you use to handle industrial projects?
How to Answer
- 1
Mention specific tools like Microsoft Project or Trello.
- 2
Discuss methodologies such as Agile, Six Sigma, or Lean.
- 3
Explain how you choose tools based on project requirements.
- 4
Give an example of a successful project where you used these tools.
- 5
Emphasize your adaptability to learn new tools if necessary.
Example Answers
I typically use Microsoft Project for timeline management and Agile methodologies for flexible project execution. In my last project, we used Trello to track tasks, which improved our team's efficiency significantly.
Don't Just Read Industrial Technologist Questions - Practice Answering Them!
Reading helps, but actual practice is what gets you hired. Our AI feedback system helps you improve your Industrial Technologist interview answers in real-time.
Personalized feedback
Unlimited practice
Used by hundreds of successful candidates
What strategies do you use for maintaining manufacturing equipment to minimize downtime?
How to Answer
- 1
Implement a routine preventive maintenance schedule.
- 2
Utilize predictive maintenance tools to analyze equipment health.
- 3
Train operators on basic troubleshooting techniques.
- 4
Keep an inventory of critical spare parts.
- 5
Document maintenance activities for future reference.
Example Answers
I implement a preventive maintenance schedule that outlines regular checks and servicing of all equipment, which helps prevent unexpected breakdowns.
Explain how you might conduct a process optimization study.
How to Answer
- 1
Define the process to be optimized and gather baseline data.
- 2
Identify key performance indicators that measure process success.
- 3
Engage stakeholders to get insights and gather support for optimization.
- 4
Use data analysis methods to identify bottlenecks and inefficiencies.
- 5
Develop and test solutions, then measure the impact against the KPIs.
Example Answers
To conduct a process optimization study, I would start by outlining the specific process I want to improve and collect relevant baseline metrics. Next, I’d define key performance indicators related to efficiency and quality. I would involve team members to gain insights on pain points, then analyze the data to highlight bottlenecks. Finally, I would implement targeted solutions and evaluate their impact using the KPIs established earlier.
What experience do you have with lean manufacturing principles?
How to Answer
- 1
Identify specific lean tools you have used, like 5S or Kaizen.
- 2
Share concrete examples of how you applied these principles in past roles.
- 3
Explain the outcomes or improvements that resulted from implementing lean practices.
- 4
Highlight collaboration with team members or departments in your lean initiatives.
- 5
Mention any training or certifications in lean manufacturing you've completed.
Example Answers
In my previous role at XYZ Corp, I implemented 5S in our assembly line, which improved efficiency by 20%. We organized the workspace, reducing time spent searching for tools.
How proficient are you with CAD software for developing product or equipment designs?
How to Answer
- 1
Identify specific CAD software you are familiar with.
- 2
Mention your years of experience and types of projects done.
- 3
Highlight any advanced features you have used.
- 4
Share examples of successful designs made using CAD.
- 5
Express willingness to learn new software if needed.
Example Answers
I am proficient in AutoCAD and SolidWorks with over 4 years of experience. I have developed several mechanical components and assemblies, including a pump housing project where I utilized features like parametric modeling.
What safety standards and practices do you apply when working on industrial projects?
How to Answer
- 1
Identify relevant safety regulations relevant to your field
- 2
Explain how you implement personal protective equipment (PPE)
- 3
Discuss regular safety audits and risk assessments
- 4
Mention training programs for team members
- 5
Highlight your commitment to a safety-first culture
Example Answers
I ensure compliance with OSHA standards by conducting regular site inspections and using appropriate PPE like gloves and helmets. I also organize weekly safety briefings for the team.
Describe your experience with implementing automation systems in manufacturing.
How to Answer
- 1
Start with a brief overview of your relevant experience.
- 2
Mention specific automation technologies you have worked with.
- 3
Include metrics or outcomes from the projects to demonstrate impact.
- 4
Discuss collaboration with cross-functional teams during implementation.
- 5
Conclude with lessons learned or future applications of automation.
Example Answers
In my previous role as a manufacturing engineer, I implemented a robotic arm system for assembly. This system reduced assembly time by 30% and improved quality control. I collaborated with IT and production teams to ensure seamless integration.
How do you use data analysis to improve production efficiency and quality?
How to Answer
- 1
Identify key performance metrics relevant to production.
- 2
Use statistical tools to analyze production data for trends.
- 3
Implement changes based on data findings to streamline processes.
- 4
Monitor the results of changes with follow-up data analysis.
- 5
Communicate insights with the team to foster a data-driven culture.
Example Answers
I analyze key metrics like cycle time and defect rates. For instance, I used statistical process control to identify trends in defect rates, which led us to adjust our quality checks and improve efficiency by 15%.
What knowledge do you have regarding the selection and testing of materials in manufacturing processes?
How to Answer
- 1
Identify key material properties such as strength, ductility, and corrosion resistance
- 2
Discuss methods of material testing such as tensile tests or hardness tests
- 3
Mention the importance of cost-effectiveness and availability in material selection
- 4
Relate how material properties affect manufacturing processes like machining and welding
- 5
Give examples of materials used in specific manufacturing contexts, such as metals or polymers
Example Answers
I understand that selecting materials involves evaluating their properties like strength and ductility. For instance, in automotive manufacturing, steel is often chosen for its high strength-to-weight ratio. Testing methods like tensile tests help ensure the materials can withstand operational demands.
Don't Just Read Industrial Technologist Questions - Practice Answering Them!
Reading helps, but actual practice is what gets you hired. Our AI feedback system helps you improve your Industrial Technologist interview answers in real-time.
Personalized feedback
Unlimited practice
Used by hundreds of successful candidates
Describe a time you successfully integrated a new system into existing manufacturing processes.
How to Answer
- 1
Choose a specific project where you led the integration.
- 2
Explain the challenges of the existing system and why change was necessary.
- 3
Discuss your role in planning, executing, and training staff on the new system.
- 4
Highlight measurable outcomes like increased efficiency or reduced costs.
- 5
Focus on teamwork and communication throughout the process.
Example Answers
In my previous role at XYZ Manufacturing, we faced frequent downtime due to outdated machinery. I led a team to integrate a new automated control system. First, I assessed the needs by gathering input from operators. We then developed a training program which brought efficiency improvements of 20% and reduced our maintenance costs significantly.
Behavioral Interview Questions
Can you describe a time when you successfully collaborated with engineers and production staff to solve a production issue?
How to Answer
- 1
Identify a specific production issue you faced.
- 2
Explain your role in the collaboration process.
- 3
Describe the actions taken with engineers and production staff.
- 4
Highlight the outcome and any measurable improvements.
- 5
Reflect on what you learned from this collaboration.
Example Answers
At my previous job, we faced a significant bottleneck in our assembly line. I initiated a meeting with production staff and engineers to identify the root cause. Together, we recognized a misalignment in the workflow and adjusted the layout, resulting in a 15% increase in output. This experience taught me the value of teamwork and open communication.
Tell me about a challenging technical problem you faced and how you approached solving it.
How to Answer
- 1
Identify a specific problem related to your field
- 2
Explain the context and why it was challenging
- 3
Describe the steps you took to solve it
- 4
Highlight any tools or methods you used
- 5
Share the outcome and what you learned
Example Answers
In my previous role, we faced a significant issue with machine calibration that was affecting production quality. I gathered data on the existing calibration methods, consulted with the team for insights, and implemented a new calibration protocol using a more precise measuring tool. This reduced our defect rate by 15% and improved overall efficiency. The experience taught me the importance of collaboration and continuous improvement.
Don't Just Read Industrial Technologist Questions - Practice Answering Them!
Reading helps, but actual practice is what gets you hired. Our AI feedback system helps you improve your Industrial Technologist interview answers in real-time.
Personalized feedback
Unlimited practice
Used by hundreds of successful candidates
Describe a project where you took the lead to implement an improvement in manufacturing processes.
How to Answer
- 1
Start with a clear project description.
- 2
Explain your role and responsibilities.
- 3
Highlight specific improvements made and their impact.
- 4
Use metrics to quantify the results if possible.
- 5
Reflect on what you learned from the experience.
Example Answers
In my last role, I led a project to optimize our assembly line by reducing the setup time. I analyzed the existing process, identified bottlenecks, and implemented a new scheduling system. This resulted in a 20% reduction in downtime and increased overall productivity by 15%. I learned the importance of involving the team for feedback.
Can you provide an example of a time when you had to innovate in your role as an industrial technologist?
How to Answer
- 1
Think of a specific project or task where you introduced a new method or technology.
- 2
Describe the challenge you faced and the reason for the innovation.
- 3
Explain the steps you took to implement the innovative solution.
- 4
Highlight the results or improvements that came from your innovation.
- 5
Be ready to discuss what you learned from the experience.
Example Answers
In a previous role, we faced production delays due to outdated machinery. I researched and suggested using a new automated assembly system. I led the pilot program, trained staff, and within a month, we reduced assembly time by 30% and increased overall efficiency.
Give an example of a situation where you had to resolve a conflict between team members in a technical setting.
How to Answer
- 1
Identify a specific conflict situation you faced.
- 2
Explain the roles of the team members involved.
- 3
Describe the steps you took to resolve the conflict.
- 4
Highlight the outcome and how it benefited the project.
- 5
Reflect on what you learned from the experience.
Example Answers
In a project, two engineers disagreed about the implementation of a new software module. I scheduled a meeting to let them present their viewpoints. I facilitated the discussion, emphasizing common goals. We reached a compromise that incorporated both their ideas, leading to a more robust solution and a stronger team dynamic.
How have you demonstrated adaptability when facing rapidly changing production requirements?
How to Answer
- 1
Provide a specific example from your past experience.
- 2
Highlight the changes in production requirements you faced.
- 3
Explain the actions you took to adapt to those changes.
- 4
Describe the positive outcomes of your adaptability.
- 5
Reflect on what you learned from the experience.
Example Answers
In my previous role, our production demands changed weekly due to client requests. When we had to switch to a new product line on short notice, I coordinated with the team to reallocate resources and adjusted the production schedule. This ensured minimal downtime and helped us meet client deadlines, increasing our monthly output by 15%.
Tell me about a time when you had to manage multiple projects with tight deadlines.
How to Answer
- 1
Identify a specific situation where you managed multiple projects.
- 2
Explain how you prioritized tasks based on deadlines and importance.
- 3
Discuss any tools or methods you used for organization.
- 4
Highlight the outcome and what you learned from the experience.
- 5
Keep your answer focused and concise.
Example Answers
In my last role, I had to manage three projects simultaneously. I created a priority matrix to identify key deadlines, which allowed me to allocate resources effectively. By using project management software, I tracked progress and kept all stakeholders informed. All projects were completed on time, and I learned the importance of clear communication.
How have you contributed to a culture of continuous improvement in a previous role?
How to Answer
- 1
Share a specific example of an improvement initiative you led or participated in
- 2
Explain the process you used to identify areas for improvement
- 3
Discuss how you engaged your team or stakeholders in the improvement efforts
- 4
Mention the outcome of the initiative and any metrics that demonstrate success
- 5
Highlight what you learned from the experience and how it influenced your approach to future improvements
Example Answers
In my previous role as a process technician, I noticed our production line had frequent downtime. I initiated a meeting with my team to brainstorm and we implemented a weekly maintenance schedule. This reduced downtime by 30% and improved our overall efficiency. I learned the importance of proactive maintenance and team involvement.
Describe a situation where your communication skills helped resolve a technical issue.
How to Answer
- 1
Choose a specific example with clear context.
- 2
Highlight the technical issue and the communication breakdown.
- 3
Explain how you communicated clearly to resolve the issue.
- 4
Mention the outcome and any improvements made.
- 5
Keep it concise and focused on your role.
Example Answers
In my last project, we faced a software integration issue. I organized a meeting with the developers and the QA team, clearly outlining the problem. By facilitating a discussion, we identified the root cause and implemented a solution. This not only resolved the issue but also improved our communication for future projects.
Situational Interview Questions
If a critical piece of equipment fails, what steps would you take to address the issue and minimize production impact?
How to Answer
- 1
Identify the specific failure quickly to understand the root cause.
- 2
Communicate immediately with relevant teams to inform them of the issue.
- 3
Isolate the equipment if possible to prevent further issues.
- 4
Implement a temporary workaround to maintain production flow.
- 5
Coordinate with maintenance for urgent repair actions.
Example Answers
I would first identify the failure to understand what went wrong, then communicate with my team and relevant departments to keep everyone informed. Next, I would isolate the equipment to prevent any further complications. If possible, I would implement a temporary solution to keep production running, and finally, I would coordinate with maintenance to schedule repairs as quickly as possible.
How would you evaluate and implement a new technology in the production process?
How to Answer
- 1
Identify the needs of the production process and the specific problem the technology addresses
- 2
Conduct a cost-benefit analysis comparing potential technologies
- 3
Pilot the technology on a small scale before full implementation
- 4
Gather feedback from users and measure performance metrics
- 5
Train staff thoroughly to ensure smooth integration into existing processes
Example Answers
I would start by determining the specific challenges in the production line and how the new technology can solve them. Then, I'd perform a cost-benefit analysis to see if the investment is justified. After that, I would test the technology on a small scale, collect feedback from the team, and adjust as necessary before rolling it out completely.
Don't Just Read Industrial Technologist Questions - Practice Answering Them!
Reading helps, but actual practice is what gets you hired. Our AI feedback system helps you improve your Industrial Technologist interview answers in real-time.
Personalized feedback
Unlimited practice
Used by hundreds of successful candidates
A production line is consistently missing its targets. How would you approach improving its performance?
How to Answer
- 1
Analyze data to identify specific bottlenecks in the production process
- 2
Engage with team members to gather insights on obstacles they face
- 3
Implement process improvements using lean manufacturing principles
- 4
Test changes on a small scale before full implementation
- 5
Monitor results and adjust strategies as needed
Example Answers
I would start by analyzing production data to pinpoint where the delays are happening. After identifying bottlenecks, I'd consult with the team for their perspectives on challenges, then apply lean principles to streamline the process and test changes gradually.
How would you handle a situation where a necessary upgrade is required but the budget is limited?
How to Answer
- 1
Prioritize the most critical upgrades that align with operational needs.
- 2
Explore alternative solutions, such as phased upgrades or lower-cost options.
- 3
Involve the team to gather ideas for cost-effective approaches.
- 4
Communicate the potential risks of not upgrading to stakeholders clearly.
- 5
Seek additional funding sources or justify the upgrade with a cost-benefit analysis.
Example Answers
I would start by identifying the most crucial upgrades needed and prioritize those. Then, I'd explore ways to implement these upgrades in phases to spread out costs.
Imagine there is a disagreement between engineers and technicians about the source of a production problem. How would you resolve it?
How to Answer
- 1
Listen to both sides to understand their perspectives
- 2
Facilitate a meeting where both teams share their findings
- 3
Encourage open communication and avoid placing blame
- 4
Propose a joint analysis or investigation to identify the root cause
- 5
Work towards a solution that incorporates input from both parties
Example Answers
First, I would hold a meeting with both engineers and technicians to hear their views. I would ensure everyone feels heard and respected. Then, we could review the data together and conduct a joint analysis to pinpoint the issue. This collaborative approach helps in building a solution everyone supports.
What steps would you take following a safety incident in the manufacturing plant?
How to Answer
- 1
Immediately ensure the safety of all personnel involved
- 2
Report the incident to the appropriate management and safety officer
- 3
Gather facts about the incident by interviewing witnesses and reviewing footage if available
- 4
Implement temporary measures to prevent further incidents while a full investigation occurs
- 5
Document everything thoroughly for future reference and compliance
Example Answers
First, I would ensure that everyone is safe and secure the area. Then, I would notify my supervisor and the safety officer about the incident. I would collect information from witnesses and review any security footage to understand what happened. Next, I'd put in place temporary safety measures to address immediate hazards, and finally, I'd document the incident completely for our records.
How would you respond to negative feedback from a customer regarding product quality?
How to Answer
- 1
Listen actively to the customer's concerns without interrupting.
- 2
Acknowledge the issue and express understanding of their frustration.
- 3
Ask clarifying questions to gather more details and show you care.
- 4
Provide a solution or explain how you will address the problem.
- 5
Follow up with the customer after the resolution to ensure satisfaction.
Example Answers
I would listen closely to the customer's feedback to fully understand their concerns. I would acknowledge their frustration and ask more questions to clarify the issue. Then, I'd discuss how we can resolve the problem and follow up to ensure they are satisfied with the outcome.
How would you ensure compliance with new environmental regulations impacting your current production processes?
How to Answer
- 1
Review the specific regulations carefully to understand the requirements.
- 2
Conduct a gap analysis to identify current practices versus what is required.
- 3
Engage with key stakeholders to align on compliance strategies.
- 4
Develop a training program for employees on new compliance measures.
- 5
Establish a monitoring system to regularly check for compliance.
Example Answers
I would begin by thoroughly reviewing the new regulations to identify our compliance obligations. Then, I'd perform a gap analysis of our production processes to identify any non-compliance areas. Next, I'd involve the team to devise strategies to meet or exceed these regulations, while also training them on the new practices. Finally, I would implement a regular monitoring system to ensure we stay compliant over time.
If faced with a shortage of a key resource, how would you prioritize operations?
How to Answer
- 1
Identify the most critical operations impacted by the shortage.
- 2
Assess the potential impact of the shortage on production and deadlines.
- 3
Communicate with stakeholders about the situation and proposed priorities.
- 4
Explore alternative resources or methods to mitigate the shortage effects.
- 5
Implement a phased approach to prioritize tasks based on urgency and importance.
Example Answers
In case of a resource shortage, I would first identify which operations are most critical to meet our deadlines. Then, I would communicate with the team to realign priorities and explore if we can use alternative materials to keep production going.
How would you design a training program to upskill production staff in the use of new machinery?
How to Answer
- 1
Assess current skill levels to identify gaps.
- 2
Develop a curriculum that includes both theoretical knowledge and hands-on practice.
- 3
Incorporate multimedia resources like videos and manuals for diverse learning styles.
- 4
Schedule regular assessments to measure progress and adapt the program.
- 5
Engage experienced staff as mentors for peer-to-peer training.
Example Answers
First, I would conduct a skills assessment to understand the existing levels of the staff. Then, I would create a comprehensive curriculum that includes safety protocols, operational procedures, and hands-on training sessions. Utilizing videos and manuals would help accommodate various learning preferences, and I would implement regular assessments to track progress.
Don't Just Read Industrial Technologist Questions - Practice Answering Them!
Reading helps, but actual practice is what gets you hired. Our AI feedback system helps you improve your Industrial Technologist interview answers in real-time.
Personalized feedback
Unlimited practice
Used by hundreds of successful candidates
Industrial Technologist Position Details
Recommended Job Boards
CareerBuilder
www.careerbuilder.com/jobs/industrial-technologistThese job boards are ranked by relevance for this position.
Related Positions
Ace Your Next Interview!
Practice with AI feedback & get hired faster
Personalized feedback
Used by hundreds of successful candidates
Ace Your Next Interview!
Practice with AI feedback & get hired faster
Personalized feedback
Used by hundreds of successful candidates