Top 31 Exhauster Interview Questions and Answers [Updated 2025]
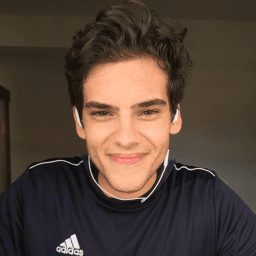
Andre Mendes
•
March 30, 2025
Preparing for an Exhauster role interview can be daunting, but we've got you covered with this comprehensive guide. Dive into the most common interview questions you might encounter, complete with example answers and insightful tips on delivering them effectively. Whether you're a seasoned professional or new to the field, this post will equip you with the knowledge and confidence to ace your interview.
Download Exhauster Interview Questions in PDF
To make your preparation even more convenient, we've compiled all these top Exhausterinterview questions and answers into a handy PDF.
Click the button below to download the PDF and have easy access to these essential questions anytime, anywhere:
List of Exhauster Interview Questions
Behavioral Interview Questions
Can you describe a time when you worked closely with other technicians to address an urgent issue with an exhauster?
How to Answer
- 1
Set the context with a brief description of the situation.
- 2
Explain the specific roles of you and your team members.
- 3
Describe the actions taken as a group to resolve the issue.
- 4
Highlight the outcome and any lessons learned.
- 5
Keep it concise and focused on teamwork and problem-solving.
Example Answers
During a routine inspection, we noticed that the exhauster was not performing efficiently. I coordinated with two other technicians to assess the situation. We divided the tasks: one checked the motor, while another inspected the filters. I monitored the pressure readings. Together, we identified a clogged filter that was restricting airflow. After replacing it, the exhauster's performance improved significantly, demonstrating the importance of teamwork in troubleshooting.
Tell me about a particularly challenging problem you faced while operating or maintaining exhaust systems and how you solved it.
How to Answer
- 1
Identify a specific challenging problem you encountered.
- 2
Explain the impact this problem had on operations.
- 3
Describe the steps you took to analyze and solve the issue.
- 4
Highlight any tools or techniques you used.
- 5
Conclude with the results and what you learned from the experience.
Example Answers
While maintaining an exhaust system, I faced a severe blockage in the ductwork due to accumulated debris, which caused overheating. I analyzed the layout, used a camera inspection tool to locate the blockage, and used pneumatic tools to clear it. This restored proper airflow and I documented the maintenance procedures to prevent future occurrences.
Don't Just Read Exhauster Questions - Practice Answering Them!
Reading helps, but actual practice is what gets you hired. Our AI feedback system helps you improve your Exhauster interview answers in real-time.
Personalized feedback
Unlimited practice
Used by hundreds of successful candidates
Describe an instance when you identified a safety hazard in the workplace related to exhaust systems and how you handled it.
How to Answer
- 1
Think of a specific situation where you noticed a safety hazard.
- 2
Describe the type of hazard you identified, such as a leak or improper ventilation.
- 3
Explain the steps you took to address the issue, including reporting it or making changes.
- 4
Mention any collaboration with team members or supervisors to resolve the hazard.
- 5
Conclude with the positive outcome of your actions in ensuring safety.
Example Answers
In a previous role, I noticed that the exhaust system in our workshop had a leak. I reported it to my supervisor immediately and secured the area to prevent any breathing hazards. Together, we scheduled a maintenance check, which led to a timely repair and improved air quality in the workspace.
Have you ever had to lead a team during a critical maintenance situation? What approach did you take?
How to Answer
- 1
Describe a specific situation clearly and briefly
- 2
Explain the urgency and impact of the maintenance issue
- 3
Highlight your leadership actions and decision-making process
- 4
Discuss team communication and collaboration methods used
- 5
Mention the outcome and any lessons learned
Example Answers
In a recent critical maintenance situation, we faced a major pump failure at the plant. I quickly assessed the severity and organized an emergency team meeting to delegate tasks. We communicated via radios to ensure everyone was informed about their responsibilities. After 4 hours of focused effort, we successfully repaired the pump and minimized downtime. This taught me the importance of clear communication during crises.
Have you ever trained others on exhauster operations or maintenance? What was your approach?
How to Answer
- 1
Highlight specific training experiences or sessions you conducted.
- 2
Explain your method of breaking down complex processes into simple steps.
- 3
Emphasize the use of hands-on training or simulations.
- 4
Mention how you assessed trainees' understanding and progress.
- 5
Share any feedback or improvements made based on training outcomes.
Example Answers
Yes, I trained new operators on exhauster operations using a step-by-step approach. I created a detailed manual and led hands-on sessions where trainees operated the equipment under supervision, allowing them to ask questions in real-time. I assessed their understanding through practical evaluations and encouraged feedback.
Can you provide an example of a proactive measure you took that improved the performance or safety of an exhauster?
How to Answer
- 1
Identify a specific problem related to exhauster performance or safety.
- 2
Describe the proactive measure you implemented.
- 3
Include the results of the action taken.
- 4
Focus on measurable improvements, such as reduced downtime or enhanced safety metrics.
- 5
Use clear and concise language to communicate your actions and their impact.
Example Answers
In my previous role, I noticed that the exhauster was frequently overheating due to clogged filters. I initiated a routine maintenance schedule for filter checks and replacements, which reduced overheating incidents by 40% and improved overall performance.
Explain a time when you had to report maintenance issues to management. How did you present your findings?
How to Answer
- 1
Identify the specific maintenance issue clearly and concisely.
- 2
Describe the impact of the issue on operations or safety.
- 3
Explain how you gathered data or evidence to support your findings.
- 4
Present your findings to management in a structured manner, possibly using visuals.
- 5
Follow up after reporting to ensure the issue is addressed.
Example Answers
At my previous job, we experienced a recurring issue with the exhaust system causing inefficiencies. I documented incident occurrences and their impact on production loss, then presented a report along with charts to the management, highlighting the urgency of repairs. By following up regularly, we secured the necessary maintenance action in a timely manner.
Describe a situation where effective communication led to a better outcome in your work with exhaust systems.
How to Answer
- 1
Identify a specific project where communication was key.
- 2
Describe who you communicated with and the challenges faced.
- 3
Explain the outcome of the improved communication.
- 4
Highlight any tools or methods used to facilitate this communication.
- 5
Conclude with what you learned and how it improved future projects.
Example Answers
In a recent project, our team faced delays in exhaust system installation due to unclear specifications. I organized daily briefings with the engineering team and the contractors to clarify requirements. This led to a 20% reduction in installation time and improved overall project efficiency.
Can you discuss a time when you received feedback regarding your exhauster performance and how you applied it?
How to Answer
- 1
Reflect on specific feedback, highlight what was said about your performance
- 2
Explain how you understood the feedback and why it was important
- 3
Describe the specific steps you took to improve your performance
- 4
Share the outcome after implementing the changes
- 5
Keep the example relatable and relevant to the role of exhauster
Example Answers
In my previous role, I received feedback that my exhauster settings were not optimized for efficiency. I took this seriously and reviewed the manufacturer’s guidelines. I adjusted the settings according to the recommendations, and afterwards, I noticed a significant decrease in processing time by 15%. This not only improved efficiency but also enhanced our team’s productivity.
Don't Just Read Exhauster Questions - Practice Answering Them!
Reading helps, but actual practice is what gets you hired. Our AI feedback system helps you improve your Exhauster interview answers in real-time.
Personalized feedback
Unlimited practice
Used by hundreds of successful candidates
Technical Interview Questions
What are the key components of an exhauster system and what is the function of each?
How to Answer
- 1
Start by listing the main components of an exhauster system.
- 2
Briefly describe the function of each component.
- 3
Use clear and technical terms relevant to the field.
- 4
Keep your answer structured and focused.
- 5
Prepare to answer follow-up questions about each component.
Example Answers
The key components of an exhauster system include the blower, discharge piping, and filter. The blower generates the necessary suction to remove air or gases, the discharge piping directs the flow of expelled materials, and the filter captures particulates from the air stream to ensure cleaner output.
What is your approach to routine maintenance checks for exhaust systems?
How to Answer
- 1
Start with outlining a scheduled maintenance plan for checks.
- 2
Emphasize the importance of safety measures while conducting maintenance.
- 3
Identify key components of the exhaust system to inspect regularly.
- 4
Discuss how to document findings and track maintenance history.
- 5
Mention any industry standards or regulations that guide your maintenance approach.
Example Answers
I follow a scheduled maintenance plan, performing checks monthly. I ensure to inspect the muffler, pipes, and hangers for wear and damage, adhering to safety measures. I document all findings in a maintenance log to track performance over time.
Don't Just Read Exhauster Questions - Practice Answering Them!
Reading helps, but actual practice is what gets you hired. Our AI feedback system helps you improve your Exhauster interview answers in real-time.
Personalized feedback
Unlimited practice
Used by hundreds of successful candidates
How do you troubleshoot an exhauster that is not performing to specifications?
How to Answer
- 1
Start by verifying power and controls to ensure the exhauster is receiving adequate power.
- 2
Check for blockages in the intake or exhaust that could restrict airflow.
- 3
Assess the motor and mechanical components for unusual noises or vibrations indicating wear or failure.
- 4
Examine the settings and controls to confirm they are set correctly for the operational requirements.
- 5
Collect performance data to compare with specifications and identify specific areas of underperformance.
Example Answers
First, I would check that the exhauster is powered properly and the controls are functioning. Next, I would inspect for any blockages in the intake or exhaust that could hinder performance. Additionally, I’d listen for any unusual sounds from the motor and look for mechanical issues.
What regulations and standards govern the operation of exhaust systems, and how do you ensure compliance?
How to Answer
- 1
Identify key regulations related to exhaust systems like EPA standards and ANSI requirements.
- 2
Discuss how to stay updated on changes in regulations and industry standards.
- 3
Explain the processes in place for regular monitoring and documentation of compliance.
- 4
Mention training and certification of staff to handle exhaust systems properly.
- 5
Describe any specific experiences where you ensured compliance in previous roles.
Example Answers
I follow EPA regulations and industry standards like ANSI for exhaust systems, regularly check for updates, and maintain a compliance log. I also ensure my team is trained in these standards.
Can you explain the process you follow for calibrating an exhauster?
How to Answer
- 1
Start with safety protocols to ensure a safe working environment
- 2
Describe how to check and set the baseline measurements for the exhauster
- 3
Include the steps for adjusting the operational parameters according to manufacturer specifications
- 4
Explain how to verify the accuracy of measurements after calibration
- 5
Mention the importance of documenting the calibration process for future reference
Example Answers
To calibrate an exhauster, I first ensure all safety measures are in place. Then, I check the baseline measurements against the specifications provided by the manufacturer. Next, I adjust the airflow and pressure settings as needed, and afterwards, I verify the accuracy using calibrated tools. Finally, I document the results and any adjustments made for future reference.
What are some common causes of exhauster failures, and how would you mitigate these risks?
How to Answer
- 1
Identify common mechanical issues like bearing failures and alignment problems.
- 2
Discuss operational causes such as improper loading or flow restrictions.
- 3
Mention points related to maintenance practices like inadequate lubrication.
- 4
Outline strategies for monitoring performance and implementing regular inspections.
- 5
Propose training for operators to recognize early signs of failure.
Example Answers
Common causes of exhauster failures include bearing wear and misalignment. To mitigate these risks, I would ensure regular alignment checks and use vibration analysis to monitor bearing health.
Describe your experience with diagnosing and repairing mechanical components of an exhauster.
How to Answer
- 1
Focus on specific experiences you've had with exhaust systems.
- 2
Mention tools and techniques you used to diagnose issues.
- 3
Include a brief example of a successful repair.
- 4
Discuss any relevant training or certifications you have.
- 5
Emphasize your problem-solving skills and attention to detail.
Example Answers
In my previous role, I diagnosed issues in exhaust systems by using diagnostic tools like pressure gauges and flow meters. For instance, I identified a blockage causing low pressure — I disassembled the relevant components, cleaned them, and restored proper function, which improved efficiency by 20%.
How do you conduct inspections on exhaust systems to ensure they are operating efficiently?
How to Answer
- 1
Start by visually inspecting the exhaust system for any visible damage or corrosion.
- 2
Check for proper installation and alignment of all components.
- 3
Measure exhaust flow and temperature to ensure they are within expected ranges.
- 4
Inspect and replace any clogged or damaged filters and components.
- 5
Document findings and adjustments made during the inspection for future reference.
Example Answers
I begin with a visual inspection, checking for any signs of wear or corrosion. Then, I measure the exhaust flow and temperature to ensure they're within specifications. Lastly, I replace any clogged filters as needed and document my findings.
What software tools or systems do you use for monitoring and managing exhaust systems?
How to Answer
- 1
Identify specific software applications you have used in the past.
- 2
Highlight your familiarity with data logging and analysis tools.
- 3
Mention any industry-specific software relevant to exhaust systems.
- 4
Discuss how you utilize these tools for efficiency and effectiveness.
- 5
Share examples of successes you've had using these tools.
Example Answers
I commonly use Siemens' LNF software for monitoring exhaust emissions and ensuring compliance with regulations, which helped reduce downtime by 20%.
What performance metrics do you typically monitor for exhauster efficiency?
How to Answer
- 1
Identify key efficiency metrics specific to exhausters such as flow rate, pressure ratio, and energy consumption.
- 2
Discuss the importance of monitoring operational parameters regularly to ensure optimal performance.
- 3
Mention metrics like maintenance downtime and maintenance costs to evaluate reliability and cost-effectiveness.
- 4
Emphasize the need for trend analysis of these metrics to identify potential issues before they arise.
- 5
Be prepared to give examples of how you have used these metrics to optimize exhauster operations.
Example Answers
I typically monitor metrics like flow rate, which indicates how efficiently the exhauster is processing air, and the pressure ratio to ensure it's operating within optimal limits. Additionally, energy consumption is critical as it affects operational costs.
Don't Just Read Exhauster Questions - Practice Answering Them!
Reading helps, but actual practice is what gets you hired. Our AI feedback system helps you improve your Exhauster interview answers in real-time.
Personalized feedback
Unlimited practice
Used by hundreds of successful candidates
How do you stay updated on the latest developments and technologies in exhauster operations?
How to Answer
- 1
Follow industry journals and publications relevant to exhauster technology.
- 2
Join professional associations or groups focused on exhaust systems.
- 3
Attend relevant trade shows and conferences to network and learn.
- 4
Participate in online forums or discussion groups related to exhauster operations.
- 5
Take courses or webinars to stay informed about new technologies and techniques.
Example Answers
I subscribe to industry journals like the Journal of Clean Air Technology and follow updates on exhauster technology. I also attend the annual Exhaust Systems Conference to network with professionals and learn about the latest advancements.
Situational Interview Questions
You receive a call that the exhaust system has failed during operation. What steps do you take immediately?
How to Answer
- 1
Assess the safety of the area and ensure no personnel are in danger
- 2
Immediately notify your supervisor and relevant team members about the failure
- 3
Retrieve the operational manual for the exhaust system to understand failure protocols
- 4
Shut down the system if it's safe to do so to prevent further damage
- 5
Gather necessary tools and equipment to begin troubleshooting after ensuring safety measures are in place
Example Answers
First, I would ensure the safety of personnel in the area before anything else. Then, I would notify my supervisor about the situation. Next, I would check the operational manual to find the emergency protocols for a system failure. If it's safe, I would shut down the exhaust system to prevent further issues. Finally, I'd prepare any tools I might need for troubleshooting once the area is secured.
If you and a colleague strongly disagree on the solution to a problem with an exhauster, how would you handle the situation?
How to Answer
- 1
Stay calm and listen to your colleague's perspective.
- 2
Present your reasoning clearly without being confrontational.
- 3
Seek common ground and identify shared goals.
- 4
Suggest discussing the issue with a third party if needed.
- 5
Be open to compromise and alternative solutions.
Example Answers
I would first ensure to listen to my colleague's viewpoint and understand their reasoning. Then, I’d present my thoughts clearly and respectfully. We can discuss what aspects of our solutions align and which do not, and if necessary, involve a supervisor for additional insight.
Don't Just Read Exhauster Questions - Practice Answering Them!
Reading helps, but actual practice is what gets you hired. Our AI feedback system helps you improve your Exhauster interview answers in real-time.
Personalized feedback
Unlimited practice
Used by hundreds of successful candidates
Imagine you notice unusual vibrations from the exhauster. What actions do you take to investigate and rectify the issue?
How to Answer
- 1
Assess the situation to identify the severity of the vibrations
- 2
Check the exhauster's manual for troubleshooting steps
- 3
Inspect the unit for loose bolts or connections
- 4
Run diagnostics to identify any mechanical issues
- 5
If necessary, consult with a supervisor before taking further action
Example Answers
First, I would assess the vibrations to determine if they are severe. Then, I would consult the exhauster's manual for specific troubleshooting advice. Next, I would physically inspect the unit for any loose bolts or connections. If I still can't find the issue, I would run diagnostics to check for mechanical faults. Finally, I would report to my supervisor if the problem persists.
If a client complains about the performance of an exhaust system, how would you address their concerns?
How to Answer
- 1
Listen actively to the client's concerns and take notes.
- 2
Ask specific questions to understand the exact nature of the performance issue.
- 3
Reassure the client that you will investigate the problem thoroughly.
- 4
Explain any immediate steps you will take to assess the system.
- 5
Provide a timeline for follow-up and resolution.
Example Answers
I would start by listening carefully to the client's complaints and taking detailed notes. Then, I would ask specific questions to pinpoint the issue, assuring them that I'll investigate thoroughly. I would explain that I will check the exhaust settings and components immediately, and I'll follow up with them in two days with my findings.
You are assigned a limited budget for exhauster repairs. How would you prioritize the repairs needed?
How to Answer
- 1
Assess the urgency of each repair based on safety and operational impact.
- 2
Evaluate the cost-effectiveness of repairs versus replacement.
- 3
Identify repairs that will prevent further damage and save costs long-term.
- 4
Consider the operational schedule and prioritize repairs that minimize downtime.
- 5
Consult with team members and gather data on past issues to inform decisions.
Example Answers
I would first assess which repairs are critical for safety, such as fixing leaks or failures that could lead to hazardous situations. Next, I would look at the costs and determine if any repairs can prevent more expensive future issues, such as fixing worn parts that could lead to system failures. Finally, I'd prioritize repairs that allow the exhauster to operate efficiently without excessive downtime.
You are leading a team to fix a critical failure in the exhauster. How do you ensure the team works efficiently?
How to Answer
- 1
Identify the critical issues quickly and communicate them clearly to the team.
- 2
Delegate tasks based on each team member's strengths and expertise.
- 3
Maintain open channels of communication for updates and questions.
- 4
Set short-term goals to track progress and adjust plans if needed.
- 5
Schedule regular check-ins to monitor team morale and address any roadblocks.
Example Answers
I would quickly assess the critical issues, communicate a clear action plan to the team, and assign roles based on each person's strengths. Then, I would hold regular check-ins to address any emerging issues and ensure we stay on track.
You have multiple exhaust systems that need maintenance. How do you prioritize which ones to work on first?
How to Answer
- 1
Assess the safety risks associated with each system
- 2
Identify systems that are critical to operations or production
- 3
Check the operational history for previous issues
- 4
Evaluate the maintenance schedule to meet compliance
- 5
Consider the availability of parts and personnel for repairs
Example Answers
I prioritize systems based on safety; any that present a risk to workers or the environment are addressed first. After that, I look at which systems are essential for ongoing operations and have had recent issues.
If a new technician joins your team, how would you ensure they are properly trained on exhauster operations?
How to Answer
- 1
Start with a structured onboarding plan for the new technician.
- 2
Assign a mentor who has extensive experience with exhauster operations.
- 3
Provide hands-on training with the exhauster under supervision.
- 4
Schedule regular check-ins to assess progress and address questions.
- 5
Incorporate safety training specific to exhauster operations.
Example Answers
I would create a detailed onboarding plan that outlines the training process. I’d pair the new technician with a mentor who has a strong background in exhauster operations. They would provide hands-on training and we would have regular check-ins to ensure the new hire is comfortable with all procedures.
Imagine you have the opportunity to implement a new technology in exhauster maintenance. What would it be and why?
How to Answer
- 1
Identify a specific technology that enhances efficiency or safety.
- 2
Explain how the technology improves current maintenance practices.
- 3
Consider cost-effectiveness and ease of implementation.
- 4
Discuss potential benefits such as reduced downtime or better performance.
- 5
Be prepared to address possible challenges in adopting the new technology.
Example Answers
I would implement predictive maintenance software using IoT sensors. This technology would allow us to monitor exhausters in real-time, predicting failures before they happen, which reduces downtime and maintenance costs significantly.
During an unexpected breakdown of an exhauster, how would you coordinate the response to minimize downtime?
How to Answer
- 1
Assess the situation quickly and identify the issue.
- 2
Communicate immediately with relevant team members and management.
- 3
Organize resources for repair, including spare parts and tools.
- 4
Implement a troubleshooting protocol to diagnose the problem.
- 5
Keep all stakeholders updated on progress and expected downtime.
Example Answers
In case of an exhauster breakdown, I would quickly assess the issue and gather the team for a quick briefing. I'd then assign roles for diagnosing the problem and sourcing parts. Communication is key, so I would keep everyone informed as we work on repairs.
Don't Just Read Exhauster Questions - Practice Answering Them!
Reading helps, but actual practice is what gets you hired. Our AI feedback system helps you improve your Exhauster interview answers in real-time.
Personalized feedback
Unlimited practice
Used by hundreds of successful candidates
Exhauster Position Details
Related Positions
- Oil Extractor
- Ventilator
- Drainer
- Extruder Operator
- Soot Blower
- Washer
- Digester
- Fish Drier
- Garment Steamer
- Meat Washer
Similar positions you might be interested in.
Ace Your Next Interview!
Practice with AI feedback & get hired faster
Personalized feedback
Used by hundreds of successful candidates
Ace Your Next Interview!
Practice with AI feedback & get hired faster
Personalized feedback
Used by hundreds of successful candidates