Top 31 Extruder Operator Interview Questions and Answers [Updated 2025]
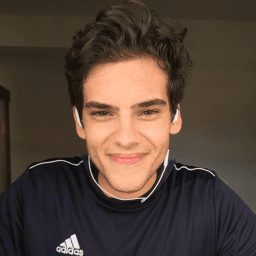
Andre Mendes
•
March 30, 2025
Navigating the job market as an Extruder Operator can be challenging, but being well-prepared for interviews can make all the difference. In this post, we've compiled the most common interview questions for this role, complete with example answers and effective answering tips. Whether you're a seasoned professional or a newcomer, this guide will help you confidently tackle your next interview and land the job.
Download Extruder Operator Interview Questions in PDF
To make your preparation even more convenient, we've compiled all these top Extruder Operatorinterview questions and answers into a handy PDF.
Click the button below to download the PDF and have easy access to these essential questions anytime, anywhere:
List of Extruder Operator Interview Questions
Technical Interview Questions
What regular maintenance routines do you perform on an extruder to ensure optimal performance?
How to Answer
- 1
Check and clean the feed throat to prevent blockages.
- 2
Inspect barrel temperature sensors and calibrate as needed.
- 3
Lubricate moving parts according to the manufacturer's schedule.
- 4
Examine and replace worn screws or barrels to maintain efficiency.
- 5
Perform routine checks on the cooling system to prevent overheating.
Example Answers
I ensure optimal performance by checking and cleaning the feed throat regularly to avoid material blockages.
What types of extruders have you worked with, and what are their key operational parameters?
How to Answer
- 1
Identify the types of extruders you have experience with by name.
- 2
Briefly describe the specific applications of each type you have used.
- 3
Mention key operational parameters such as temperature, pressure, and speed.
- 4
Include any relevant certifications or training in operating the extruders.
- 5
Be prepared to discuss how you optimized or troubleshot these parameters.
Example Answers
I have worked primarily with twin-screw and single-screw extruders. The twin-screw extruder is used for compounding plastics and operates at temperatures between 200 to 250 degrees Celsius and speeds of 50 to 400 RPM. The single-screw extruder, used for basic extrusion processes, typically runs at lower temperatures and around 20 to 120 RPM.
Don't Just Read Extruder Operator Questions - Practice Answering Them!
Reading helps, but actual practice is what gets you hired. Our AI feedback system helps you improve your Extruder Operator interview answers in real-time.
Personalized feedback
Unlimited practice
Used by hundreds of successful candidates
How do different raw materials affect the extrusion process, and how do you adjust settings accordingly?
How to Answer
- 1
Identify common raw materials used in extrusion like PVC, ABS, or polyethylene.
- 2
Explain how the properties of these materials, such as viscosity and melting temperature, impact the extrusion process.
- 3
Discuss specific adjustments to temperature, pressure, and speed based on the material's characteristics.
- 4
Mention the importance of monitoring the extrusion output for quality control.
- 5
Highlight your experience or examples where you successfully managed different materials in past roles.
Example Answers
Different raw materials like PVC and polyethylene have varying melting points and viscosities. For example, with PVC, I adjust the temperature settings higher to ensure complete melting, and I may slow down the screw speed to prevent degradation.
How do you monitor and ensure the quality of the extruded products?
How to Answer
- 1
Conduct regular visual inspections of the extruded products.
- 2
Utilize measurement tools to check dimensions and tolerances.
- 3
Implement in-line testing methods to assess physical properties.
- 4
Keep records of production data and quality checks for analysis.
- 5
Communicate with the team about quality issues and solutions.
Example Answers
I monitor quality by performing visual inspections for surface defects and ensuring that products meet dimensional specifications using calipers and gauges throughout the production run.
Can you explain how you would optimize the extrusion process for a new product?
How to Answer
- 1
Understand the material requirements for the new product
- 2
Monitor the extrusion temperature and pressure for optimal flow
- 3
Adjust the screw speed and design based on the product specifications
- 4
Conduct trial runs to identify bottlenecks and inefficiencies
- 5
Gather feedback from quality control to refine the process
Example Answers
To optimize the extrusion process for a new product, I would first analyze the material requirements, then set the appropriate temperature and pressure. After that, I'd adjust the screw speed based on product specs and run trials to find any inefficiencies.
What safety protocols do you follow when operating extrusion machinery?
How to Answer
- 1
Always wear appropriate personal protective equipment such as gloves, goggles, and ear protection
- 2
Conduct a pre-operation safety check of the machine including emergency stops
- 3
Ensure all safety guards are in place before starting the machinery
- 4
Maintain a clean and organized work area to prevent accidents
- 5
Follow lockout/tagout procedures when performing maintenance or repairs
Example Answers
I always wear safety goggles and gloves, check that all safety guards are secure, and make sure my work area is free of hazards before starting the extrusion machine.
What steps do you take to troubleshoot extruder malfunctions?
How to Answer
- 1
Start with a visual inspection of the extruder for obvious signs of trouble.
- 2
Check the material feed to ensure it is flowing correctly and is not clogged.
- 3
Review operating parameters such as temperature and pressure settings against specifications.
- 4
Examine the control panel for any error codes or alarms that can indicate the issue.
- 5
Consult equipment manuals for troubleshooting instructions specific to the malfunction.
Example Answers
First, I perform a visual inspection of the extruder for any obvious issues. Then, I check that the material feed is uninterrupted and not clogged. I also look at the temperature and pressure settings to ensure they're correct.
Can you explain how the screw design of an extruder can affect the extrusion outcome?
How to Answer
- 1
Discuss the role of screw geometry in melting and mixing materials.
- 2
Explain how different flight designs influence material movement and pressure.
- 3
Mention the impact of screw length-to-diameter ratio on processing efficiency.
- 4
Refer to how the pitch of the screw affects material feed rate.
- 5
Include examples of specific applications and desired outcomes influenced by screw design.
Example Answers
The screw design greatly influences the melting and mixing of materials. A barrier screw, for instance, can help achieve a better melt by controlling material flow and temperature. Additionally, a longer screw increases residence time, leading to better homogenization.
How do you use production data to inform your extrusion operations?
How to Answer
- 1
Analyze historical data to identify trends in production output.
- 2
Use real-time monitoring to adjust settings for optimal performance.
- 3
Track downtime and correlate it with production data to find root causes.
- 4
Implement quality control metrics to assess batch quality against production data.
- 5
Regularly review data with the team to foster continuous improvement.
Example Answers
I analyze historical production data to understand output trends and make necessary adjustments. For instance, if I notice a drop in output, I check machine settings or material quality.
What recent advancements in extrusion technology have you found most impactful in the industry?
How to Answer
- 1
Research the latest trends in extrusion technology.
- 2
Focus on advancements that improve efficiency and product quality.
- 3
Consider mentioning sustainable practices or materials.
- 4
Provide specific examples of technologies or equipment.
- 5
Show how these advancements can benefit production processes.
Example Answers
I recently read about using AI for process optimization in extrusion. It improves efficiency by predicting faults before they occur, which is critical in maintaining product quality.
Don't Just Read Extruder Operator Questions - Practice Answering Them!
Reading helps, but actual practice is what gets you hired. Our AI feedback system helps you improve your Extruder Operator interview answers in real-time.
Personalized feedback
Unlimited practice
Used by hundreds of successful candidates
What is the role of cooling in the extrusion process and how do you manage it?
How to Answer
- 1
Cooling solidifies the extrudate by lowering its temperature.
- 2
It prevents warping and ensures dimensional stability of the final product.
- 3
Use water baths or air cooling systems effectively during extrusion.
- 4
Monitor cooling rates to match material specifications and output rates.
- 5
Adjust cooling systems based on extruded material characteristics and ambient temperature.
Example Answers
Cooling is crucial as it solidifies the material and ensures the proper shape of the extrudate. I typically use water baths to manage the cooling process, adjusting the flow rate to match the output speed for optimal results.
Situational Interview Questions
If a safety alarm goes off in the extrusion area, what immediate actions would you take?
How to Answer
- 1
Stay calm and assess the situation carefully.
- 2
Immediately check the alarm type to understand the potential hazard.
- 3
Follow established safety protocols for the specific alarm.
- 4
Evacuate personnel from the area if necessary and ensure everyone's safety.
- 5
Report the situation to the supervisor and follow their instructions.
Example Answers
I would remain calm, quickly identify the alarm type, and follow the appropriate safety protocols. If it indicates a risk, I would ensure everyone evacuates the area safely and then notify my supervisor.
If you noticed the extruded material had inconsistent thickness, what would be your first steps to address this?
How to Answer
- 1
Check the feed material for size and quality issues.
- 2
Examine the machine settings and ensure they are within specifications.
- 3
Look for blockages in the die or adjustments to the die gap.
- 4
Monitor the temperature settings and adjust if necessary.
- 5
Conduct a quick inspection of the forming tooling for wear or damage.
Example Answers
First, I would check the quality of the feed material to ensure it's uniform. Then, I'd inspect the machine settings to confirm they meet specifications for production.
Don't Just Read Extruder Operator Questions - Practice Answering Them!
Reading helps, but actual practice is what gets you hired. Our AI feedback system helps you improve your Extruder Operator interview answers in real-time.
Personalized feedback
Unlimited practice
Used by hundreds of successful candidates
How would you prioritize tasks if you are behind schedule in production due to machine downtime?
How to Answer
- 1
Assess the immediate situation and identify the most critical tasks.
- 2
Communicate with the team about the delay and re-prioritize based on urgency.
- 3
Focus on high-impact tasks that can help catch up on production.
- 4
Utilize downtime to perform maintenance or preparation for upcoming tasks.
- 5
Monitor progress closely and adjust priorities as required.
Example Answers
In a situation of machine downtime, I would first assess which tasks are most critical to production. Then, I would communicate with my team to ensure everyone understands the new priorities. I would focus on tasks that can help us quickly catch up, and if possible, use any downtime to prepare for tasks ahead, ensuring we keep moving forward.
What would you do if you believe that another operator is not following the proper operating procedures?
How to Answer
- 1
Stay calm and assess the situation objectively
- 2
Gather specific observations or evidence of the procedures being ignored
- 3
Approach the operator privately and express your concerns respectfully
- 4
Encourage a discussion about safety and procedure adherence
- 5
If issues persist, report the matter to a supervisor or manager
Example Answers
If I notice another operator not following procedures, I would first observe and gather specific examples. Then, I would approach them privately to discuss what I've seen, emphasizing the importance of following the procedures for safety and quality. If necessary, I would bring it to the attention of a supervisor.
How would you handle a situation where team members are not cooperating during a high-pressure task?
How to Answer
- 1
Stay calm and assess the situation quickly.
- 2
Communicate clearly what the goals and tasks are.
- 3
Encourage open dialogue to understand underlying issues.
- 4
Reinforce teamwork and highlight the importance of cooperation.
- 5
Offer support or delegate tasks to relieve pressure.
Example Answers
I would first remain calm and quickly assess why cooperation is lacking. Then, I would clearly communicate the immediate goals, encouraging team members to talk openly about any challenges. By reinforcing the importance of teamwork, I would remind everyone that success depends on our collaboration.
If you had to adjust the temperature settings on the extruder during a run, how would you ensure that quality is not compromised?
How to Answer
- 1
Monitor the output quality continuously during the adjustment
- 2
Make small incremental changes to the temperature
- 3
Document the baseline temperatures for reference
- 4
Use a quality control checklist to assess product consistency
- 5
Communicate with the team about adjustments to align processes
Example Answers
I would start by closely monitoring the output quality, making small adjustments to the temperature, and checking the product for consistency after each change. I would also keep my team informed about the changes I make.
If you received negative feedback on your extrusion production rate, how would you respond?
How to Answer
- 1
Acknowledge the feedback without being defensive
- 2
Ask for specific examples or details about the feedback
- 3
Discuss your willingness to improve and adapt processes
- 4
Mention any steps you would take to analyze the issue
- 5
Emphasize teamwork and collaboration in addressing challenges
Example Answers
I appreciate the feedback and understand the importance of production rates. I would like to know specific areas where I can improve. I'm committed to reviewing our processes and would involve the team in brainstorming solutions to enhance efficiency.
How would you cope if a major breakdown occurred just before meeting a deadline?
How to Answer
- 1
Stay calm and assess the situation quickly
- 2
Prioritize immediate actions to minimize downtime
- 3
Communicate with team members and management about the issue
- 4
Implement a contingency plan if available
- 5
Document the issue for future reference and prevent recurrence
Example Answers
If a major breakdown happened, I would first stay calm to think clearly. I would quickly assess the nature of the breakdown and prioritize necessary repairs. I would inform the team and management to get support if needed, then follow our contingency plan to minimize lost time and output. Lastly, I would document the situation to discuss improvements later.
If a client has specific requirements for a new product, how would you approach the extrusion process to meet their needs?
How to Answer
- 1
Start by clarifying the client's specific requirements closely.
- 2
Assess the raw materials that will be used and their compatibility with the requirements.
- 3
Adjust the extrusion parameters like temperature, speed, and pressure based on the product specs.
- 4
Conduct small-scale trials to validate the adjustments before full production.
- 5
Communicate regularly with the client to ensure their needs are consistently met.
Example Answers
I would begin by discussing the client's specific requirements in detail to ensure I clearly understand their needs. After that, I would evaluate the materials we have and make any necessary adjustments to the extrusion settings like temperature and speed. Then, I'd run a few small-scale tests to see if we meet the specifications before moving to full-scale production, keeping the client updated at every step.
What steps would you take if production data indicated a decline in output quality?
How to Answer
- 1
Analyze the production data to identify the specific quality issues.
- 2
Inspect the machinery and equipment for any malfunctions or maintenance needs.
- 3
Review the raw materials for consistency and quality standards.
- 4
Consult with the production team to gather input on potential changes.
- 5
Implement necessary adjustments and monitor the output closely for improvements.
Example Answers
First, I would analyze the production data to pinpoint where the quality issues are occurring. Then, I would check the equipment for any malfunctions and assess the raw materials for quality. After gathering feedback from the team, I would make necessary adjustments and closely monitor the output.
Don't Just Read Extruder Operator Questions - Practice Answering Them!
Reading helps, but actual practice is what gets you hired. Our AI feedback system helps you improve your Extruder Operator interview answers in real-time.
Personalized feedback
Unlimited practice
Used by hundreds of successful candidates
If you were promoted to lead a team of operators, what would be your first priority?
How to Answer
- 1
Focus on team communication and establish open lines for feedback
- 2
Evaluate current processes to identify areas for improvement
- 3
Ensure safety procedures are being followed and understood by all team members
- 4
Set clear goals and expectations for the team to achieve
- 5
Foster a supportive and collaborative team culture
Example Answers
My first priority would be to enhance communication within the team. I would hold a meeting to encourage everyone to share their thoughts and feedback on current operations.
Behavioral Interview Questions
Can you describe a time when you identified a problem in the extrusion process? How did you address it?
How to Answer
- 1
Start with a specific problem you encountered.
- 2
Explain the steps you took to identify the root cause.
- 3
Discuss the solution you implemented to fix the issue.
- 4
Mention any tools or techniques you used.
- 5
Conclude with the outcome or improvement resulting from your actions.
Example Answers
In my last job, we noticed inconsistent product thickness during extrusion. I analyzed the process and found that the temperature was fluctuating too much. I adjusted the heating system settings and implemented regular monitoring. This stabilized the temperature, and we saw a 20% decrease in product defects.
Give an example of a successful team project you were involved in. What was your role?
How to Answer
- 1
Identify a specific project where you contributed to success
- 2
Explain your individual role and responsibilities clearly
- 3
Highlight how teamwork and collaboration helped achieve goals
- 4
Mention any challenges faced and how the team overcame them
- 5
Conclude with the results or outcomes of the project
Example Answers
In a recent project to improve production efficiency, I was responsible for monitoring the extruder settings. I collaborated closely with the quality control team to make adjustments based on real-time feedback, which led to a 15% reduction in waste over three months.
Don't Just Read Extruder Operator Questions - Practice Answering Them!
Reading helps, but actual practice is what gets you hired. Our AI feedback system helps you improve your Extruder Operator interview answers in real-time.
Personalized feedback
Unlimited practice
Used by hundreds of successful candidates
Describe a time when you had to lead a team during a challenging production situation. What was the outcome?
How to Answer
- 1
Start with the specific situation to set the context.
- 2
Explain the challenges you faced clearly.
- 3
Describe your leadership actions and decisions.
- 4
Highlight the impact of your leadership on the team.
- 5
Conclude with the positive outcome and what you learned.
Example Answers
In a previous role, our extruder experienced a significant malfunction during a crucial production run. I quickly organized an emergency team meeting to brainstorm solutions. By delegating tasks and ensuring clear communication, we managed to fix the issue within two hours, and we met our production deadline. It taught me the importance of staying calm and leading effectively under pressure.
Tell me about a time when you had to adapt to a significant change in the production process or equipment.
How to Answer
- 1
Choose a specific example from your experience.
- 2
Highlight the change and why it was significant.
- 3
Describe how you responded to the change.
- 4
Emphasize the positive outcome or what you learned.
- 5
Keep it concise and focused on your role.
Example Answers
In my previous job, the company switched to a new extrusion line that required a different setup. I quickly learned the new operating procedures and led training sessions for my colleagues, which helped us adapt faster. As a result, we maintained productivity and improved efficiency within a few weeks.
Have you ever had a disagreement with a colleague about how to operate the extruder? How did you resolve it?
How to Answer
- 1
Stay calm and professional while discussing the disagreement
- 2
Focus on facts and operational procedures rather than personal opinions
- 3
Listen actively to your colleague's perspective
- 4
Seek a compromise or solution that benefits production efficiency
- 5
Reflect on what you learned from the experience
Example Answers
Yes, my colleague and I disagreed about the ideal temperature settings for the extruder. I listened to his reasoning and shared the data from our past production runs. We agreed to run a few tests at different settings and evaluate the results. It improved our output quality, and I learned the importance of collaboration.
Provide an example of a situation where your attention to detail prevented a potential issue in production.
How to Answer
- 1
Think of a specific instance from your previous experience.
- 2
Focus on an incident where detail spotting avoided a major problem.
- 3
Include what you noticed and the steps you took.
- 4
Describe the outcome and significance of your action.
- 5
Keep it concise and relevant to the role of an Extruder Operator.
Example Answers
In my last job, I noticed that the temperature settings on the extruder were fluctuating beyond the recommended range. I immediately reported it to my supervisor, and we adjusted the settings before continuing production. This prevented any quality issues in the final product.
Describe a time when you took initiative to improve the extrusion process. What impact did it have?
How to Answer
- 1
Start with a specific situation where you noticed a problem in the extrusion process.
- 2
Explain the initiative you took to address the issue, mentioning any methods or tools used.
- 3
Discuss the outcome of your actions, focusing on measurable improvements or benefits.
- 4
Highlight any recognition or feedback you received from your team or management.
- 5
Keep it concise and ensure your passion for improvement shines through.
Example Answers
In my previous job, I noticed that the extrusion temperatures were frequently fluctuating which affected product quality. I took the initiative to recalibrate the temperature controls and established a routine check. As a result, we saw a 20% decrease in product defects and received positive feedback from our quality control department.
Tell me about a creative solution you implemented in your previous role as an extruder operator.
How to Answer
- 1
Think of a specific problem you faced while operating the extruder.
- 2
Describe the creative solution you came up with to address that problem.
- 3
Explain how you implemented the solution and its impact on the production process.
- 4
Be clear about your role in the solution and any collaboration with others.
- 5
Use metrics or results to quantify the success of your solution if possible.
Example Answers
In my previous role, we had an issue with material consistency leading to production delays. I designed a modified blending process that allowed us to mix additives more effectively. This reduced our scrap rate by 15% and improved overall throughput, allowing us to meet our deadlines consistently.
Have you ever trained a new extruder operator? How did you approach it?
How to Answer
- 1
Explain your training philosophy and focus on hands-on experience.
- 2
Describe how you introduced equipment and processes gradually.
- 3
Mention how you encouraged questions and created a supportive learning environment.
- 4
Give an example of how you assessed their progress and provided feedback.
- 5
Highlight any specific methods or resources you used to aid training.
Example Answers
Yes, I trained a new extruder operator by starting with an overview of the machine's components. I allowed them to observe while I operated the extruder, then gradually had them take over while I supervised, ensuring they felt comfortable. I welcomed their questions and provided feedback on their performance regularly.
Extruder Operator Position Details
Recommended Job Boards
CareerBuilder
www.careerbuilder.com/jobs/extruder-operatorZipRecruiter
www.ziprecruiter.com/Jobs/Extruder-OperatorThese job boards are ranked by relevance for this position.
Related Positions
Ace Your Next Interview!
Practice with AI feedback & get hired faster
Personalized feedback
Used by hundreds of successful candidates
Ace Your Next Interview!
Practice with AI feedback & get hired faster
Personalized feedback
Used by hundreds of successful candidates