Top 32 Corrugator Operator Interview Questions and Answers [Updated 2025]
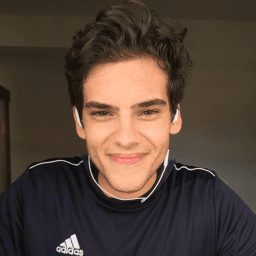
Andre Mendes
•
March 30, 2025
Are you preparing for a Corrugator Operator interview and want to stand out from the competition? This blog post is designed to help you ace your interview with ease by covering the most common questions you might face. Dive in to discover insightful example answers and practical tips on how to respond effectively, ensuring you present yourself as the ideal candidate for the role.
Download Corrugator Operator Interview Questions in PDF
To make your preparation even more convenient, we've compiled all these top Corrugator Operatorinterview questions and answers into a handy PDF.
Click the button below to download the PDF and have easy access to these essential questions anytime, anywhere:
List of Corrugator Operator Interview Questions
Behavioral Interview Questions
Can you describe a time when you had to work closely with a team to meet a production goal?
How to Answer
- 1
Choose a specific instance that highlights teamwork.
- 2
Describe the goal, your role, and the team's effort.
- 3
Include challenges faced and how you overcame them together.
- 4
Emphasize communication and collaboration among team members.
- 5
Conclude with the outcome and what you learned from the experience.
Example Answers
In my previous job, our team was tasked with increasing production output by 20% within a month. I took the lead in organizing weekly meetings where we discussed our strategies and progress. When we encountered a bottleneck in machinery, we worked together to develop a new workflow. Ultimately, we exceeded our goal by 5%, and it taught me the importance of open communication and adaptability.
Tell me about a significant challenge you faced as a Corrugator Operator and how you overcame it.
How to Answer
- 1
Identify a specific technical or operational challenge you faced.
- 2
Explain the actions you took to address the challenge clearly.
- 3
Highlight any teamwork, tools, or strategies used during the solution process.
- 4
Mention the outcome and what you learned from the experience.
- 5
Keep your answer concise and relevant to the role of a Corrugator Operator.
Example Answers
In my previous position, we had a major machine breakdown that halted production. I quickly assessed the situation and collaborated with the maintenance team to diagnose the issue. By coordinating repairs and reallocating tasks among colleagues, we resumed production within hours. This experience taught me the importance of teamwork and effective communication in crisis situations.
Don't Just Read Corrugator Operator Questions - Practice Answering Them!
Reading helps, but actual practice is what gets you hired. Our AI feedback system helps you improve your Corrugator Operator interview answers in real-time.
Personalized feedback
Unlimited practice
Used by hundreds of successful candidates
Describe a situation where you had to adjust to changes in the production process quickly.
How to Answer
- 1
Think of a specific experience in your previous job.
- 2
Focus on the change you faced and why it was necessary.
- 3
Explain the steps you took to adapt to the change.
- 4
Highlight your quick decision-making and teamwork if applicable.
- 5
Conclude with the outcome and what you learned from it.
Example Answers
In my previous role, we had a sudden machinery breakdown during a shift. I quickly informed the supervisor and worked with the maintenance team to troubleshoot while reallocating tasks among the operators. We managed to keep production running at a reduced rate until repairs were completed, which minimized downtime.
Have you ever taken the lead on a project or initiative in the plant? How did you motivate your team?
How to Answer
- 1
Identify a specific project where you showed leadership.
- 2
Explain your role and responsibilities during the project.
- 3
Describe how you engaged and motivated your team members.
- 4
Mention any challenges and how you overcame them.
- 5
Conclude with the positive outcome of the project.
Example Answers
Last year, I led a safety initiative to improve equipment inspections. I organized weekly meetings to involve everyone and encouraged open discussions, which helped the team feel invested. We created a checklist that everyone could follow, and as a result, we reduced safety incidents by 30%.
Can you provide an example of how you communicated effectively with maintenance staff about machine issues?
How to Answer
- 1
Choose a specific incident to describe
- 2
Explain the communication method used (verbal, written, etc.)
- 3
Highlight the outcome of the communication
- 4
Mention any tools or systems that facilitated communication
- 5
Discuss any follow-up actions taken
Example Answers
In my previous role, we had a significant issue with the corrugator's alignment. I immediately communicated with our maintenance team verbally and followed up with an email detailing the symptoms. This clear communication helped them understand the urgency, and they resolved the issue within hours, preventing further downtime.
Tell me about a time when your team achieved outstanding results. What contributed to this success?
How to Answer
- 1
Choose a specific project or goal your team accomplished.
- 2
Focus on your role and contributions to the team's success.
- 3
Highlight teamwork and collaboration as key factors.
- 4
Mention specific outcomes or metrics that demonstrate success.
- 5
Reflect on lessons learned and how they can apply to future projects.
Example Answers
In a recent packaging project, our team increased output by 30% while reducing waste. My role as the lead corrugator operator involved coordinating closely with the logistics team to ensure materials were delivered on time. The outstanding results were due to our strong communication and teamwork, allowing us to troubleshoot issues quickly and efficiently.
Describe how you collaborate with Quality Control to maintain production standards.
How to Answer
- 1
Emphasize communication with Quality Control routinely.
- 2
Provide examples of joint inspections and feedback sessions.
- 3
Discuss how you adapt processes based on QC findings.
- 4
Highlight the importance of teamwork in problem-solving.
- 5
Mention any specific tools or systems used for collaboration.
Example Answers
I communicate daily with Quality Control to ensure we're aligned on standards. For instance, when QC identifies a defect, we conduct a joint inspection to understand the issue and implement corrective measures immediately.
Describe a time when you went above and beyond your job requirements.
How to Answer
- 1
Think of a specific instance where you exceeded expectations.
- 2
Focus on actions that directly benefited your team or employer.
- 3
Use the STAR method: Situation, Task, Action, Result.
- 4
Emphasize the positive impact of your actions.
- 5
Be honest and choose a real scenario.
Example Answers
In my previous job, our deadline was moved up unexpectedly. I volunteered to stay late for a week to help my team meet this new deadline. As a result, we completed the project on time, and the client was very satisfied.
Don't Just Read Corrugator Operator Questions - Practice Answering Them!
Reading helps, but actual practice is what gets you hired. Our AI feedback system helps you improve your Corrugator Operator interview answers in real-time.
Personalized feedback
Unlimited practice
Used by hundreds of successful candidates
Technical Interview Questions
What are the key components of a corrugator machine, and how do they function together?
How to Answer
- 1
Identify the main components like the single facer, bridge, and double backer.
- 2
Explain the role of each component clearly and simply.
- 3
Describe how the components work together in the corrugation process.
- 4
Use specific terms related to corrugation to show your knowledge.
- 5
Keep your answer structured and easy to follow.
Example Answers
The key components of a corrugator machine include the single facer, which corrugates the liner board, the bridge that allows the paper to travel smoothly, and the double backer, which adds the second liner. Together, they create the corrugated sheet by applying heat and pressure, ensuring strong bonding.
How do you perform troubleshooting when a corrugator machine experiences operational issues?
How to Answer
- 1
Identify the problem by observing the machine's operation and listening for unusual sounds.
- 2
Consult the machine's control panel for error codes or alarms that provide specific information.
- 3
Check the machine's manual for troubleshooting steps related to the error code or symptoms.
- 4
Inspect key components like rollers, belts, and sensors for any visible signs of wear or misalignment.
- 5
Test the machine after making adjustments to ensure the issue is resolved and document the process.
Example Answers
When troubleshooting a corrugator, I first observe the operation and listen for any unusual sounds. Then, I check the control panel for error codes, review the machine manual for guidance, and inspect critical components for any signs of wear. Finally, I test the machine to confirm the issue is resolved.
Don't Just Read Corrugator Operator Questions - Practice Answering Them!
Reading helps, but actual practice is what gets you hired. Our AI feedback system helps you improve your Corrugator Operator interview answers in real-time.
Personalized feedback
Unlimited practice
Used by hundreds of successful candidates
What quality control measures do you implement while operating a corrugator?
How to Answer
- 1
Start by discussing regular monitoring of machine settings
- 2
Emphasize conducting visual inspections of the corrugated boards
- 3
Mention keeping records of production metrics for analysis
- 4
Highlight the importance of maintaining material quality and consistency
- 5
Talk about troubleshooting and adjusting processes to correct defects
Example Answers
I regularly monitor the machine settings like temperature and pressure to ensure they are within specified ranges, and I conduct visual checks on the boards to catch any defects early.
Can you explain the corrugation process step-by-step?
How to Answer
- 1
Start with the type of material used, typically paper.
- 2
Describe the process of heating the paper to create a fluted shape.
- 3
Explain how the fluted paper is glued to flat sheets.
- 4
Mention the cutting and shaping of the corrugated board.
- 5
Conclude with quality checks and packaging processes.
Example Answers
The corrugation process begins with large rolls of paper. The paper is heated and passed through rollers to create flutes. Glue is applied to attach the flutes to flat sheets. After that, the board is cut to size and checked for quality before packaging.
What types of paper materials are typically used in corrugation, and how do their properties affect production?
How to Answer
- 1
Identify the main types of paper used in corrugation, such as linerboard and medium.
- 2
Explain the properties of these materials, like thickness and strength.
- 3
Discuss how these properties influence the corrugation process and final product quality.
- 4
Mention any specific grades of paper that are commonly used.
- 5
Be prepared to provide examples of applications for different types of corrugated materials.
Example Answers
In corrugation, we typically use linerboard and medium. Linerboard is strong and provides structure, while medium is fluted which provides cushioning. The thickness affects the stacking strength and ability to resist compression, impacting production efficiency and product integrity.
What routine maintenance tasks do you perform on a corrugator machine?
How to Answer
- 1
Mention checking and replacing worn parts regularly.
- 2
Include cleaning the rollers and belts to prevent buildup.
- 3
Discuss lubricating moving parts as part of maintenance.
- 4
Emphasize the importance of checking fluid levels and refilling as necessary.
- 5
Explain how to inspect electrical connections and sensors for proper operation.
Example Answers
I perform routine maintenance by checking and replacing any worn parts, cleaning the rollers and belts to prevent buildup, and lubricating all moving parts regularly.
What safety protocols do you follow while operating heavy machinery like a corrugator?
How to Answer
- 1
Always wear personal protective equipment such as gloves, goggles, and hard hats.
- 2
Conduct a pre-operation inspection of the machinery to ensure everything is functioning properly.
- 3
Follow lockout/tagout procedures before performing any maintenance or troubleshooting.
- 4
Stay aware of your surroundings and ensure there are no hazards or personnel in the vicinity when operating the machine.
- 5
Report any safety concerns immediately to a supervisor or safety officer.
Example Answers
I follow strict safety protocols including wearing all required PPE and conducting pre-operation inspections to ensure the corrugator is safe to use.
What strategies do you use to optimize the corrugation process?
How to Answer
- 1
Regularly calibrate the corrugator equipment to maintain precision.
- 2
Monitor temperature and humidity levels closely to ensure material stability.
- 3
Implement preventive maintenance schedules to reduce downtime.
- 4
Analyze production data to identify bottlenecks and inefficiencies.
- 5
Train operators on best practices for handling materials and equipment.
Example Answers
I regularly calibrate the equipment to ensure it operates within the required specifications, which helps maintain consistency in the corrugation process.
How do you adjust machinery settings for different types of corrugated board?
How to Answer
- 1
Identify the specific requirements for the type of corrugated board being produced.
- 2
Refer to the manufacturer's specifications for optimal settings.
- 3
Adjust the pressure and speed settings based on board thickness and flute type.
- 4
Test and monitor the output for quality before finalizing adjustments.
- 5
Document the settings for future reference and consistency.
Example Answers
To adjust settings for different types of corrugated board, I first check the manufacturer's guidelines, then set the pressure and speed according to the board's flute type and thickness, and finally run tests to ensure quality before finalizing the settings.
What common defects can occur in corrugated material and how do you identify them?
How to Answer
- 1
List common defects such as crushing, delamination, and uneven flute height
- 2
Explain how to identify defects visually or through touch
- 3
Mention any tools or methods used for measuring quality
- 4
Discuss the impact of defects on functionality and printing
- 5
Emphasize the importance of quality control checks
Example Answers
Common defects in corrugated material include crushing, which can be identified by checking for flat areas, delamination, noticeable through peeling layers, and uneven flute heights, detectable with a ruler. It's essential to conduct regular quality checks to ensure optimal performance.
Don't Just Read Corrugator Operator Questions - Practice Answering Them!
Reading helps, but actual practice is what gets you hired. Our AI feedback system helps you improve your Corrugator Operator interview answers in real-time.
Personalized feedback
Unlimited practice
Used by hundreds of successful candidates
What is the importance of calibrating the corrugator, and how do you ensure it's properly calibrated?
How to Answer
- 1
Explain that proper calibration ensures product quality and consistency.
- 2
Mention safety and efficiency as key reasons for calibration.
- 3
Describe the frequency of calibration checks based on production needs.
- 4
Outline specific steps taken to calibrate, such as measuring key parameters.
- 5
Highlight the use of standardized tools and following manufacturer guidelines.
Example Answers
Calibrating the corrugator is vital to ensure that the product is produced consistently and meets quality standards. I check the alignment and pressure settings regularly, ensuring they match the manufacturer's specifications to prevent issues during production.
What type of data do you record during your shift, and why is it important?
How to Answer
- 1
Identify key metrics you monitor, such as production rates and downtime.
- 2
Explain how the data helps improve efficiency and safety.
- 3
Mention any tools or software you use for data recording.
- 4
Emphasize the importance of accuracy in tracking production data.
- 5
Discuss how you use this data to report trends or address issues.
Example Answers
During my shift, I record production rates, machine downtime, and any quality control issues. This data is important because it helps us identify patterns that can improve efficiency and ensure product quality.
Situational Interview Questions
If you notice a significant delay in production due to a machine malfunction, what actions would you take?
How to Answer
- 1
Stay calm and assess the situation immediately.
- 2
Notify your supervisor about the delay and the suspected cause.
- 3
Follow your training procedures to troubleshoot the machine if qualified.
- 4
Document the issue and any actions taken for future reference.
- 5
Coordinate with maintenance personnel to resolve the malfunction quickly.
Example Answers
I would first evaluate the machine to understand the issue. If I determine it’s a malfunction, I’d notify my supervisor and document the problem. Then, I would assist maintenance in fixing it as soon as possible.
How would you respond if you found that the product output did not meet quality standards?
How to Answer
- 1
Immediately halt production to prevent further defects
- 2
Analyze the issue to identify the root cause
- 3
Communicate with team members about the problem
- 4
Implement corrective actions and adjustments
- 5
Document the issue and steps taken for future reference
Example Answers
If I found that the product output did not meet quality standards, I would stop production right away. Then, I would investigate to find out what caused the problem, collaborating with my team to ensure we understand the issue. Next, I would take corrective steps to fix the issue and document everything for future reference.
Don't Just Read Corrugator Operator Questions - Practice Answering Them!
Reading helps, but actual practice is what gets you hired. Our AI feedback system helps you improve your Corrugator Operator interview answers in real-time.
Personalized feedback
Unlimited practice
Used by hundreds of successful candidates
What would you do if a critical machine fails during peak production hours?
How to Answer
- 1
Stay calm and assess the situation quickly.
- 2
Notify your supervisor about the machine failure.
- 3
Attempt to troubleshoot the issue if you are trained to do so.
- 4
Implement contingency plans to minimize downtime.
- 5
Communicate with the team to manage workflow and expectations.
Example Answers
I would first remain calm and evaluate the issue. Then, I would inform my supervisor immediately so that we can follow our emergency protocols. If I have the training, I would attempt a quick troubleshooting step before we escalate to maintenance.
How would you handle a disagreement with a colleague about the operation of machinery?
How to Answer
- 1
Stay calm and listen to your colleague's perspective.
- 2
Stay focused on the machinery operation and facts, not personal issues.
- 3
Suggest a collaborative approach to test each argument.
- 4
Refer to the machinery's manual or standard operating procedures for clarity.
- 5
If needed, involve a supervisor for an unbiased opinion.
Example Answers
I would first listen to my colleague's concerns to understand their viewpoint. Then, I would suggest we review the machinery's manual together to find the best solution based on the procedure.
If a new operator joins your team, how would you ensure they are trained effectively?
How to Answer
- 1
Start with a comprehensive orientation about the corrugator machine and its operation.
- 2
Pair the new operator with an experienced mentor for hands-on training.
- 3
Provide clear training materials, including manuals and checkpoints.
- 4
Encourage questions and provide feedback during training sessions.
- 5
Perform regular evaluations to assess the new operator's understanding and skills.
Example Answers
I would begin by giving the new operator a thorough orientation on the machine, covering its key components. Then, I would assign them to work with a seasoned operator for practical training. I would also supply training manuals and encourage them to ask questions throughout their training.
How would you react if management decided to implement a new production method that you are unfamiliar with?
How to Answer
- 1
Stay positive and open-minded about the change
- 2
Express willingness to learn and adapt quickly
- 3
Ask for training or resources to understand the new method
- 4
Suggest a team collaboration to share knowledge
- 5
Share past experiences of adapting to new processes successfully
Example Answers
I would approach the change with an open mind, eager to learn the new method. I would ask management for any training opportunities to ensure I understand how to implement it correctly. I've effectively adapted to new processes in the past, and I'm confident I can do it again.
Imagine you are tasked with following multiple orders simultaneously, each with tight deadlines. How would you prioritize your work?
How to Answer
- 1
Assess the urgency of each order based on deadlines.
- 2
Determine the complexity of each order and the time required.
- 3
Communicate with your supervisor about prioritization if needed.
- 4
Focus on the orders that impact customer satisfaction the most.
- 5
Use tools like a checklist or digital planner to keep track of progress.
Example Answers
I would start by reviewing all the orders and assessing their deadlines. I'd prioritize the ones due soonest and check if any are more complex and might require more time. If I'm unsure, I would consult my supervisor for confirmation on priorities. Throughout the process, I would track my progress using a checklist to ensure nothing is overlooked.
If you were under pressure to meet an urgent deadline but a machine broke down, how would you handle the situation?
How to Answer
- 1
Stay calm and assess the situation quickly
- 2
Identify the root cause of the machine failure
- 3
Communicate with your supervisor and team about the issue
- 4
Prioritize tasks to maximize productivity while resolving the issue
- 5
Implement a backup plan or alternative solutions if necessary
Example Answers
I would first remain calm and quickly assess what caused the machine breakdown. I would inform my supervisor and team about the situation. While waiting for repairs, I would focus on preparing other tasks that can be done without the machine to keep progress moving.
How would you handle a situation where materials are running low and you need them for production?
How to Answer
- 1
Assess current inventory and usage rates to understand the extent of the shortage.
- 2
Communicate with your supervisor or manager immediately to inform them of the situation.
- 3
Check with the purchasing department or suppliers to see if materials can be expedited.
- 4
Prioritize production tasks based on available materials to minimize downtime.
- 5
Document the issue and follow up to ensure it doesn’t happen again in the future.
Example Answers
First, I would check our inventory records and assess how much material we have left. Then, I would inform my supervisor about the low supply. I would also reach out to our suppliers to see if they can ship more materials quickly. In the meantime, I would prioritize the production tasks that require less material.
If a machine is running too slowly, what steps would you take to diagnose and resolve the issue?
How to Answer
- 1
Check the machine's settings to ensure they are configured correctly.
- 2
Inspect for any mechanical obstructions or wear that may slow down operation.
- 3
Review the input materials for consistency and quality that might affect performance.
- 4
Consult the machine's diagnostic tools or logs for error messages.
- 5
Collaborate with team members to gather insights based on their experiences.
Example Answers
I would first verify that the machine settings are correctly adjusted for optimal speed. Then, I would inspect the components for any mechanical wear or obstructions. If nothing is visible, I would check the material quality as it can impact the machine's efficiency.
Don't Just Read Corrugator Operator Questions - Practice Answering Them!
Reading helps, but actual practice is what gets you hired. Our AI feedback system helps you improve your Corrugator Operator interview answers in real-time.
Personalized feedback
Unlimited practice
Used by hundreds of successful candidates
Corrugator Operator Position Details
Salary Information
Recommended Job Boards
CareerBuilder
www.careerbuilder.com/jobs/corrugator-operatorZipRecruiter
www.ziprecruiter.com/Jobs/Corrugator-OperatorThese job boards are ranked by relevance for this position.
Related Positions
- Edge Roller
- Extruder Operator
- Roll Operator
- Perforator
- Mill Operator
- Turning Machine Operator
- Pipe Roller
- Commutator Operator
- Cross Roller
- Wire Roller
Similar positions you might be interested in.
Ace Your Next Interview!
Practice with AI feedback & get hired faster
Personalized feedback
Used by hundreds of successful candidates
Ace Your Next Interview!
Practice with AI feedback & get hired faster
Personalized feedback
Used by hundreds of successful candidates