Top 32 Cross Roller Interview Questions and Answers [Updated 2025]
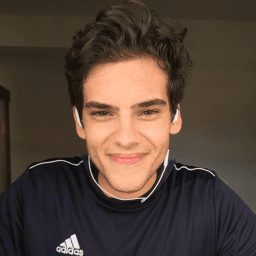
Andre Mendes
•
March 30, 2025
Preparing for a Cross Roller interview? This blog post is your ultimate guide to acing it. We've compiled the most common interview questions for the Cross Roller role, complete with example answers and insightful tips to help you respond effectively. Whether you're a seasoned professional or new to the field, this resource will equip you with the confidence and knowledge you need to impress your interviewers. Dive in and get ready to succeed!
Download Cross Roller Interview Questions in PDF
To make your preparation even more convenient, we've compiled all these top Cross Rollerinterview questions and answers into a handy PDF.
Click the button below to download the PDF and have easy access to these essential questions anytime, anywhere:
List of Cross Roller Interview Questions
Behavioral Interview Questions
Describe a time when you worked on a team project as a Cross Roller. What was your role and what challenges did the team face?
How to Answer
- 1
Identify a specific project and your role in it
- 2
Explain the challenges your team encountered
- 3
Describe how you contributed to solving those challenges
- 4
Highlight the results or outcomes of the project
- 5
Keep your answer structured: Situation, Task, Action, Result
Example Answers
In a recent project to develop a new software feature, I was a Cross Roller coordinating between the development and marketing teams. We faced communication challenges as priorities differed. I organized joint meetings to align goals and created shared timelines. As a result, we launched the feature on schedule, which boosted user engagement by 25%.
Can you give an example of a complex problem you encountered while operating a cross roller and how you resolved it?
How to Answer
- 1
Choose a specific incident that demonstrates your problem-solving skills.
- 2
Explain the context clearly for better understanding.
- 3
Outline the steps you took to identify the issue.
- 4
Describe the resolution process and any teamwork involved.
- 5
Conclude with the outcome and lessons learned.
Example Answers
While operating the cross roller, I encountered an issue where the machine's roller alignment was off, causing uneven surface finishing. I noticed the problem during a routine check and consulted the operation manual to verify the specifications. After making the necessary adjustments to the alignment, I ran tests on sample materials. The outcome was a smooth finish, and I learned the importance of regular equipment checks.
Don't Just Read Cross Roller Questions - Practice Answering Them!
Reading helps, but actual practice is what gets you hired. Our AI feedback system helps you improve your Cross Roller interview answers in real-time.
Personalized feedback
Unlimited practice
Used by hundreds of successful candidates
Tell me about a time when you had to prioritize safety over production needs. How did you handle the situation?
How to Answer
- 1
Choose a specific situation where safety was at risk.
- 2
Explain the circumstances that led to your decision.
- 3
Describe the actions you took to prioritize safety.
- 4
Discuss the outcome and any lessons learned.
- 5
Emphasize the importance of safety in your decision-making process.
Example Answers
In my previous job at the manufacturing plant, we had a situation where a machine malfunctioned, creating an unsafe environment. I immediately stopped the production line to ensure no one got hurt, even though it would lead to delays. I reported the issue to maintenance, and once they resolved it, we resumed production safely. This experience reinforced my belief that safety must come first.
Describe an instance where you had to adapt to a significant change in your work environment as a Cross Roller.
How to Answer
- 1
Choose a specific example that illustrates a significant change.
- 2
Explain the context and what triggered the change.
- 3
Detail your initial reaction and how you adjusted your approach.
- 4
Highlight any skills you used or developed during the adaptation.
- 5
Conclude with the positive outcome that resulted from your adaptation.
Example Answers
At my previous job, we switched from manual operations to an automated system. The change was sudden, and I initially felt overwhelmed. I took the initiative to attend training sessions and practiced on the new equipment. This helped me become proficient quickly, and I was able to assist my teammates in adapting as well. Ultimately, our productivity improved significantly.
Have you ever taken the lead in a project involving cross rollers? What approach did you take?
How to Answer
- 1
Identify a specific project where you led cross roller implementation.
- 2
Describe your role and responsibilities clearly.
- 3
Highlight the challenges faced and how you overcame them.
- 4
Emphasize the collaboration with team members and stakeholders.
- 5
Share the outcome and what you learned from the experience.
Example Answers
In my previous role, I led a project to integrate cross rollers into our production line. I was responsible for coordinating with the engineering team to ensure dimensions were accurate. We faced initial resistance to change, but by involving operators in the process, we got their feedback and improved the design. As a result, we increased efficiency by 20% and reduced downtime.
Give an example of how you have contributed to innovation or efficiency in cross roller operations.
How to Answer
- 1
Identify a specific project or initiative where you improved processes.
- 2
Quantify the results to show impact on efficiency or innovation.
- 3
Focus on your role and the actions you took.
- 4
Mention any collaboration or teamwork that enhanced the outcome.
- 5
Consider changes in technology or procedures that led to better results.
Example Answers
I led a project to optimize the cross roller alignment process, using a new laser measurement technique. This reduced setup time by 30% and decreased errors by 25%.
Discuss a time when you trained a new employee on cross roller operation. What did you focus on?
How to Answer
- 1
Describe the training context clearly and specifically.
- 2
Focus on key skills you taught related to cross roller operation.
- 3
Emphasize safety protocols and operational efficiency.
- 4
Mention any tools or materials you used during training.
- 5
Conclude with how you assessed the trainee's progress.
Example Answers
I trained a new employee on cross roller operation during a busy production week. I focused on the basics of machine controls and emphasized the importance of safety checks before operation. I used a checklist for operational procedures and monitored their progress closely, ensuring they could safely operate the machinery by the end of the week.
What has been your greatest achievement when operating a cross roller and why?
How to Answer
- 1
Identify a specific achievement related to operating a cross roller
- 2
Explain the context or challenge you faced during this achievement
- 3
Highlight the skills or techniques you employed
- 4
Discuss the positive outcome or impact of your achievement
- 5
Reflect on what you learned from the experience
Example Answers
Successfully completed a large asphalt project within a tight deadline using the cross roller. The challenge was to ensure even compaction despite weather issues. I used precise control and careful planning to achieve a perfect result, which led to a client satisfaction rating of 95%.
What motivates you in your role as a Cross Roller and how do you maintain that motivation even in challenging times?
How to Answer
- 1
Identify specific aspects of the job that inspire you, such as teamwork or skill development.
- 2
Share personal stories that illustrate your passion for the role.
- 3
Discuss techniques you use to stay focused, like setting small goals or maintaining a positive mindset.
- 4
Mention the support systems you leverage, such as colleagues or mentors.
- 5
Emphasize your commitment to personal and professional growth even in tough situations.
Example Answers
I am motivated by the opportunity to work closely with my team to achieve our goals. When challenges arise, I focus on celebrating small wins and supporting each other to stay motivated and resilient.
Don't Just Read Cross Roller Questions - Practice Answering Them!
Reading helps, but actual practice is what gets you hired. Our AI feedback system helps you improve your Cross Roller interview answers in real-time.
Personalized feedback
Unlimited practice
Used by hundreds of successful candidates
Technical Interview Questions
What is the operational procedure for setting up a cross roller machine for optimal performance?
How to Answer
- 1
Start by ensuring the machine is clean and free from debris.
- 2
Check and calibrate the alignment of the rollers before use.
- 3
Set the parameters according to the material specifications.
- 4
Conduct a trial run with lower speeds to ensure stability.
- 5
Monitor performance and make adjustments as necessary during operation.
Example Answers
To set up a cross roller machine, first, I clean the machine and check for any debris. Then, I align the rollers to ensure they are correctly positioned. After that, I adjust the settings based on the material specifications. I run a test at a lower speed to see if everything is stable and monitor the performance closely.
What regular maintenance tasks are critical for ensuring the cross roller operates efficiently?
How to Answer
- 1
Check lubrication regularly to prevent friction and wear.
- 2
Inspect bearings for signs of damage or wear and replace as needed.
- 3
Clean the roller surface to remove debris and contaminants.
- 4
Monitor alignment and calibration to ensure optimal performance.
- 5
Perform routine operational tests to identify any issues early.
Example Answers
Regular lubrication of the cross roller is crucial to minimize friction. I also ensure to inspect the bearings for wear and replace them when necessary.
Don't Just Read Cross Roller Questions - Practice Answering Them!
Reading helps, but actual practice is what gets you hired. Our AI feedback system helps you improve your Cross Roller interview answers in real-time.
Personalized feedback
Unlimited practice
Used by hundreds of successful candidates
Explain how you would diagnose a failure in a cross roller. What steps would you take?
How to Answer
- 1
Identify the symptoms of the failure such as noise or improper movement.
- 2
Check for any visible signs of wear or damage on the cross roller assembly.
- 3
Evaluate the lubrication level and condition to ensure it is adequate.
- 4
Use diagnostic tools to measure performance metrics if applicable.
- 5
Consult technical documentation to compare symptoms with known failure modes.
Example Answers
I would start by listening for any unusual noises and observe the cross roller's movement for irregularities. Then, I would visually inspect the assembly for any signs of damage or wear.
What safety standards must be adhered to when operating a cross roller?
How to Answer
- 1
Familiarize yourself with OSHA regulations specific to heavy machinery.
- 2
Discuss the importance of wearing personal protective equipment (PPE).
- 3
Mention the necessity of conducting pre-operation inspections.
- 4
Explain the significance of understanding load capacities and operating limits.
- 5
Highlight the requirement for training and certification for operators.
Example Answers
When operating a cross roller, it's crucial to adhere to OSHA regulations, wear appropriate PPE like hard hats and high-visibility vests, and conduct thorough pre-operation inspections to ensure safety.
What types of materials are commonly processed using a cross roller and how do they affect operations?
How to Answer
- 1
Identify common materials for cross roller processing such as metals, plastics, and composites.
- 2
Discuss how material properties like hardness and viscosity influence processing speed and quality.
- 3
Mention considerations for compatibility of materials with the cross roller design.
- 4
Highlight the importance of material thickness for the efficiency of operations.
- 5
Provide examples of specific industries that utilize cross rollers for processing.
Example Answers
Cross rollers are typically used for processing materials such as metals, plastics, and composites. The hardness of these materials affects not only the speed of processing but also the wear on the equipment. For example, harder metals may require slower processing speeds to avoid damage.
What software or technology do you use to monitor cross roller operations and production metrics?
How to Answer
- 1
Mention specific software you have used such as SCADA or MES.
- 2
Discuss your experience with data analysis tools.
- 3
Explain how you track KPIs and production metrics.
- 4
Highlight any automation or real-time monitoring technologies.
- 5
Emphasize your ability to adapt to new technologies quickly.
Example Answers
I have used SCADA systems to monitor cross roller operations, which allows for real-time tracking of production metrics and performance indicators.
Describe the calibration process for ensuring a cross roller is accurately setting the desired specifications.
How to Answer
- 1
Start by explaining the importance of calibration for accuracy.
- 2
Outline the tools and equipment used in the calibration process.
- 3
Describe the step-by-step process of calibrating a cross roller.
- 4
Mention how to verify if the calibration is successful.
- 5
Discuss the frequency of calibration checks that should be performed.
Example Answers
Calibration is crucial to ensure the cross roller is accurate. First, I use a calibrated gauge to measure the setting. Then, I adjust the roller according to the specifications, checking with the gauge at each stage. Once adjusted, I run a test to confirm results are within acceptable limits. I recommend performing this calibration monthly to maintain accuracy.
What key performance indicators do you monitor while working with cross rollers?
How to Answer
- 1
Identify relevant KPIs specific to cross roller performance
- 2
Emphasize production efficiency metrics
- 3
Include maintenance and downtime statistics
- 4
Mention quality control measures
- 5
Show how KPIs improve safety and operational excellence
Example Answers
I monitor production speed and efficiency which lets us optimize output per hour.
How do you ensure that the output from a cross roller meets quality assurance standards?
How to Answer
- 1
Regularly inspect and calibrate the cross roller to maintain accuracy
- 2
Implement a checklist for quality checks during production
- 3
Conduct random sampling of outputs for thorough quality assessment
- 4
Train team members on quality standards and procedures
- 5
Document quality control processes for continuous improvement
Example Answers
I ensure quality by routinely calibrating the cross roller and maintaining an inspection checklist for every production run.
How do you utilize data analysis to improve the operational efficiency of a cross roller?
How to Answer
- 1
Identify key performance indicators relevant to cross roller operations.
- 2
Collect data on production cycles, downtime, and maintenance events.
- 3
Analyze patterns to pinpoint inefficiencies and areas for improvement.
- 4
Implement changes based on data insights and monitor the outcomes.
- 5
Regularly update data analysis processes to adapt to new operational challenges.
Example Answers
I track key performance indicators such as production speed and downtime. By analyzing the data, I've identified that maintenance events often coincide with drops in efficiency. Implementing a predictive maintenance schedule based on this data has significantly reduced downtime.
Don't Just Read Cross Roller Questions - Practice Answering Them!
Reading helps, but actual practice is what gets you hired. Our AI feedback system helps you improve your Cross Roller interview answers in real-time.
Personalized feedback
Unlimited practice
Used by hundreds of successful candidates
What industry regulations must you comply with as a Cross Roller operator?
How to Answer
- 1
Familiarize yourself with OSHA regulations related to heavy equipment operation.
- 2
Understand local and state transportation safety laws that apply to cross roller usage.
- 3
Be aware of industry-specific standards, such as those from ARA or ANSI.
- 4
Know the maintenance and inspection regulations for cross rollers.
- 5
Stay updated on any changes in legislation that could affect your operations.
Example Answers
As a Cross Roller operator, I adhere to OSHA safety regulations, ensuring compliance with all operational safety guidelines. I also follow local transportation laws that affect how I transport materials.
What steps do you take to perform a failure analysis after a malfunction in a cross roller operation?
How to Answer
- 1
Gather all data related to the malfunction, including operating conditions and machine settings.
- 2
Inspect the cross roller components for visible wear or damage.
- 3
Consult maintenance logs for any previous issues or repairs related to the malfunction.
- 4
Simulate the operation in a controlled environment to replicate the failure, if possible.
- 5
Document findings and propose specific improvements to prevent future failures.
Example Answers
First, I gather all relevant data about the malfunction, such as operating conditions and settings. Next, I inspect the components for any signs of damage. I also check the maintenance logs for previous similar issues.
Situational Interview Questions
You notice that a colleague is not following the safety protocols while operating a cross roller. How would you address this situation?
How to Answer
- 1
Address the issue promptly and calmly without confrontation
- 2
Ask your colleague if they are aware of the safety protocols
- 3
Provide helpful reminders or guidance about the protocols
- 4
Suggest ways to improve safety awareness in the team
- 5
Report to a supervisor if the behavior persists to ensure safety compliance
Example Answers
I would approach my colleague privately and ask if they know the safety protocols for using the cross roller. I would gently remind them of the importance of these protocols for their safety and the safety of others. If they are unaware, I would offer to explain the protocols further.
If you are given a tight deadline to complete a project with a cross roller, how would you ensure you meet the deadline without compromising quality?
How to Answer
- 1
Prioritize tasks based on importance and urgency
- 2
Communicate with your team for support and resources
- 3
Break the project into smaller, manageable tasks
- 4
Set clear milestones to track progress effectively
- 5
Regularly review work to maintain quality standards
Example Answers
I would start by breaking the project into smaller tasks and prioritizing them. Then, I would communicate with my team to delegate responsibilities and ensure we have all necessary resources. Setting clear milestones would help us track our progress and make adjustments if needed.
Don't Just Read Cross Roller Questions - Practice Answering Them!
Reading helps, but actual practice is what gets you hired. Our AI feedback system helps you improve your Cross Roller interview answers in real-time.
Personalized feedback
Unlimited practice
Used by hundreds of successful candidates
Suppose the cross roller suddenly stops functioning during an essential operation. What immediate actions would you take?
How to Answer
- 1
Assess the situation to identify any visible issues with the cross roller.
- 2
Stop the operation immediately to prevent further damage or safety hazards.
- 3
Check for any error indicators or alarms that might provide insights into the malfunction.
- 4
Consult the operation manual for troubleshooting steps specific to the cross roller.
- 5
Communicate with team members and report the issue to a supervisor for assistance.
Example Answers
First, I would assess the cross roller to look for any visible problems or unusual sounds. Then, I would stop the operation to ensure safety. I would check for any alarms or error messages, and then refer to the troubleshooting section of the manual for guidance before seeking help from a supervisor.
If a new operational procedure is introduced, how would you ensure that all team members are informed and trained?
How to Answer
- 1
Communicate the new procedure clearly through a team meeting.
- 2
Provide detailed training materials such as manuals or videos.
- 3
Organize hands-on training sessions for practical understanding.
- 4
Encourage questions and offer one-on-one support if needed.
- 5
Set up a follow-up plan to check comprehension and address issues.
Example Answers
I would start by holding a team meeting to explain the changes and share the new procedure document. Then, I’d create training materials including a video tutorial and a Q&A session to ensure everyone understands.
Imagine you've completed a roll, but upon inspection, it doesn't meet quality standards. What steps would you take next?
How to Answer
- 1
Immediately assess the nature of the quality issue
- 2
Document the specific shortcomings identified during inspection
- 3
Communicate the issue to the relevant team members or supervisors
- 4
Determine the root cause of the problem through analysis
- 5
Plan corrective actions and implement changes to prevent recurrence
Example Answers
First, I would check what specific quality standards were not met and assess the extent of the issue. Then, I would document these findings and share them with my team to ensure everyone is aware. Next, I would analyze what caused the problem, such as machine settings or material quality, and then implement the necessary changes to meet standards in future rolls.
You are operating a cross roller when you notice a safety equipment failure. What steps would you take?
How to Answer
- 1
Immediately stop the operation of the cross roller
- 2
Notify your supervisor or safety officer about the failure
- 3
Conduct a visual inspection of the equipment to identify the issue
- 4
Follow the company's safety protocol for equipment failure
- 5
Document the incident and report it as required
Example Answers
I would stop the cross roller immediately to prevent any accidents. Then, I would notify my supervisor about the safety equipment failure. After that, I would visually inspect the equipment to see if I can identify the problem, and finally, I would follow company protocol for reporting the failure.
Describe how you would work with other departments to improve the effectiveness of cross rolling processes.
How to Answer
- 1
Identify key departments involved in the cross rolling process.
- 2
Establish regular communication channels for updates and feedback.
- 3
Collaborate on cross-departmental training to align goals.
- 4
Use data analysis to identify bottlenecks and test improvements.
- 5
Create cross-functional teams to address specific challenges.
Example Answers
I would start by identifying the key departments like production and quality control. Then, I would set up weekly meetings to discuss the progress and gather feedback. Additionally, I would organize joint training sessions to ensure everyone is aligned on the cross rolling process.
If a supervisor provides critical feedback on your cross roller operations, how would you respond?
How to Answer
- 1
Listen carefully to the feedback without interrupting.
- 2
Acknowledge the feedback and thank the supervisor for it.
- 3
Ask clarifying questions if something is not clear to you.
- 4
Reflect on the feedback and describe how you will implement changes.
- 5
Show commitment to improving your performance based on the feedback.
Example Answers
I appreciate the feedback from my supervisor. I would listen closely and ensure I understand their concerns. If needed, I would ask questions to clarify and then outline how I plan to adjust my operations to improve in those areas.
If resources are limited, how would you prioritize tasks for operating the cross roller?
How to Answer
- 1
Assess the most critical tasks that ensure safe operation and maintenance.
- 2
Identify which tasks directly impact productivity and quality.
- 3
Consider the urgency of tasks based on deadlines or project needs.
- 4
Evaluate which tasks can be deferred without significant impact.
- 5
Communicate with the team to gather input and consensus on priorities.
Example Answers
I would first prioritize critical safety checks and maintenance tasks to ensure the cross roller operates safely. Then, I would focus on tasks that maximize productivity, such as preparing the site for optimal operation. Lastly, I would review less urgent tasks and consider team input to manage our limited resources effectively.
How would you handle a situation where team members disagree on the best approach to operating the cross roller?
How to Answer
- 1
Encourage open communication to understand all perspectives.
- 2
Facilitate a discussion to evaluate pros and cons of each approach.
- 3
Seek input from team members with relevant experience.
- 4
Aim for a consensus or a compromise that incorporates key ideas.
- 5
Document the agreed approach and establish clear roles for implementation.
Example Answers
I would first hold a team meeting to let everyone express their viewpoints openly. Then, we would list the pros and cons of each suggested method. If needed, I would bring in a team member who has operated the cross roller before for their insights. My goal would be to find a solution that everyone is comfortable with.
Don't Just Read Cross Roller Questions - Practice Answering Them!
Reading helps, but actual practice is what gets you hired. Our AI feedback system helps you improve your Cross Roller interview answers in real-time.
Personalized feedback
Unlimited practice
Used by hundreds of successful candidates
Cross Roller Position Details
Recommended Job Boards
CareerBuilder
www.careerbuilder.com/jobs-cross-rollerZipRecruiter
www.ziprecruiter.com/Jobs/Cross-Roller/These job boards are ranked by relevance for this position.
Related Positions
- Edge Roller
- Counter Roller
- Hand Roller
- Wire Roller
- Tube Roller
- Pipe Roller
- Roll Wrapper
- Roll Operator
- Plastic Roller
- Wheel Roller
Similar positions you might be interested in.
Ace Your Next Interview!
Practice with AI feedback & get hired faster
Personalized feedback
Used by hundreds of successful candidates
Ace Your Next Interview!
Practice with AI feedback & get hired faster
Personalized feedback
Used by hundreds of successful candidates