Top 30 Edge Roller Interview Questions and Answers [Updated 2025]
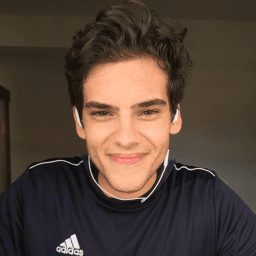
Andre Mendes
•
March 30, 2025
Navigating an Edge Roller interview can be challenging, but being well-prepared makes all the difference. In this post, we delve into the most common interview questions for the Edge Roller role, providing you with example answers and practical tips to help you respond effectively. Whether you're a seasoned professional or a newcomer, these insights will equip you to confidently tackle your next interview.
Download Edge Roller Interview Questions in PDF
To make your preparation even more convenient, we've compiled all these top Edge Rollerinterview questions and answers into a handy PDF.
Click the button below to download the PDF and have easy access to these essential questions anytime, anywhere:
List of Edge Roller Interview Questions
Technical Interview Questions
How do you ensure the products processed through edge rollers meet quality standards?
How to Answer
- 1
Regularly inspect edge roller settings and calibrations
- 2
Conduct routine quality checks on processed products
- 3
Implement a feedback loop for adjustments based on production outcomes
- 4
Train staff on quality control protocols specific to edge rolling
- 5
Maintain detailed records of quality assessments and results
Example Answers
I ensure quality by regularly checking the calibration of the edge rollers and conducting routine inspections on the final products. This way, I can catch any issues early.
What types of edge roller machinery are you familiar with, and what are their key operational requirements?
How to Answer
- 1
Identify specific types of edge roller machinery you have experience with.
- 2
Describe the key operational requirements for each type.
- 3
Include any maintenance or safety protocols you followed.
- 4
Share examples of how you used the machinery in past roles.
- 5
Be prepared to discuss any troubleshooting experiences.
Example Answers
I am familiar with automatic edge rollers and manual edge rollers. The automatic ones require regular calibration and a power source, while the manual require a knowledgeable operator and regular checks on the rollers. I operated these in a manufacturing setting, ensuring compliance with safety protocols.
Don't Just Read Edge Roller Questions - Practice Answering Them!
Reading helps, but actual practice is what gets you hired. Our AI feedback system helps you improve your Edge Roller interview answers in real-time.
Personalized feedback
Unlimited practice
Used by hundreds of successful candidates
What safety protocols do you follow while operating edge roller machinery?
How to Answer
- 1
Always wear appropriate personal protective equipment (PPE) such as gloves, goggles, and hearing protection.
- 2
Conduct a pre-operation inspection of the edge roller to ensure it's in good working condition.
- 3
Follow lockout/tagout procedures before performing any maintenance or adjustments on the machine.
- 4
Be aware of your surroundings and communicate effectively with team members during operation.
- 5
Stay within the designated safety zones and follow all safety signage and instructions.
Example Answers
I always wear my PPE, including gloves and goggles, and I check the machine for any issues before starting it.
Can you describe the routine maintenance tasks you perform on edge rollers?
How to Answer
- 1
Start by mentioning the importance of routine maintenance for edge rollers.
- 2
List specific tasks like cleaning, lubrication, and checking for wear.
- 3
Include the frequency of these tasks to show a proactive approach.
- 4
Mention any tools or equipment used during maintenance.
- 5
Highlight any safety protocols you follow while performing maintenance.
Example Answers
I perform routine maintenance on edge rollers by cleaning the rollers weekly, lubricating bearings every month, and inspecting for any wear or damage during each maintenance cycle. I use a pressure washer for cleaning and a lubrication system for applying grease. Safety protocols include wearing protective gear and ensuring the machine is powered off during maintenance.
How do you diagnose issues with edge roller performance?
How to Answer
- 1
Start by gathering data on the performance metrics of the edge roller.
- 2
Inspect physical components for wear and misalignment.
- 3
Analyze the surrounding system to identify external factors affecting performance.
- 4
Run diagnostic tests or simulations to isolate issues.
- 5
Consult maintenance logs to check for previous issues and resolutions.
Example Answers
To diagnose edge roller performance issues, I first review performance metrics such as speed and load. Then, I inspect the roller and its components for any signs of wear or misalignment. Next, I analyze the surrounding process to ensure there are no external factors affecting performance. I use diagnostic tests to pinpoint specific problems and check maintenance logs for past issues.
What software or technical tools do you use to track production and maintenance of edge rollers?
How to Answer
- 1
Mention specific software you have experience with.
- 2
Include any specialized tools or systems relevant to edge rollers.
- 3
Explain how you use these tools to improve efficiency.
- 4
Highlight any data tracking or reporting features that are important.
- 5
If possible, relate a personal success story using these tools.
Example Answers
I regularly use CMMS software like Hippo to track the maintenance schedules and production metrics for edge rollers. This helps streamline our work orders and reduce downtime effectively.
What industry standards do you follow while operating or maintaining edge rollers?
How to Answer
- 1
Mention applicable industry standards like ISO or ANSI related to edge roller safety.
- 2
Explain the importance of routine maintenance schedules based on these standards.
- 3
Discuss the use of personal protective equipment as recommended by industry guidelines.
- 4
Reference compliance with manufacturer instructions and technical documentation.
- 5
Highlight the role of training and certification in maintaining safety standards.
Example Answers
I follow ANSI B20.1 standards for edge rollers, ensuring that all safety measures are adhered to. I also implement regular maintenance checks as recommended by the manufacturer to ensure optimal performance.
What are the most common troubleshooting issues you've encountered with edge rollers, and how did you resolve them?
How to Answer
- 1
Identify specific common issues such as uneven tension or misalignment.
- 2
Describe the methodical approach you took to troubleshoot each issue.
- 3
Mention any tools or techniques you used in your resolutions.
- 4
Include a brief outcome or results of your troubleshooting efforts.
- 5
Relate your experience to the company's edge roller applications if possible.
Example Answers
One common issue I've encountered is uneven tension across the roller. I resolved this by carefully adjusting the tension mechanisms, ensuring all rollers were calibrated to the same force. After the adjustment, the material flow improved significantly.
Describe your experience with control systems used in automated edge rolling processes.
How to Answer
- 1
Focus on specific control systems you have used, like PLCs or SCADA.
- 2
Mention how you have implemented or optimized these systems in edge rolling.
- 3
Include any relevant metrics that demonstrate success or improvements.
- 4
Discuss your experience with troubleshooting and problem-solving in these systems.
- 5
Talk about any collaboration with teams to enhance the automation process.
Example Answers
I have worked extensively with PLCs in automated edge rolling processes, particularly implementing programs that improved production efficiency by 20%. I regularly collaborated with engineering teams to optimize the control logic.
What do you think are the most critical parameters to monitor during edge roller operations?
How to Answer
- 1
Identify key performance indicators like speed and pressure settings.
- 2
Discuss the importance of material consistency for optimal operation.
- 3
Mention the need for regular monitoring of temperature to prevent overheating.
- 4
Consider discussing vibration analysis to detect mechanical issues.
- 5
Emphasize the significance of maintenance logs for tracking operational trends.
Example Answers
I believe the most critical parameters are speed, pressure settings, and temperature. Monitoring these ensures the edge roller operates within safe limits and maintains quality.
Don't Just Read Edge Roller Questions - Practice Answering Them!
Reading helps, but actual practice is what gets you hired. Our AI feedback system helps you improve your Edge Roller interview answers in real-time.
Personalized feedback
Unlimited practice
Used by hundreds of successful candidates
Behavioral Interview Questions
Can you describe a situation where you had to work closely with a difficult colleague? How did you handle it?
How to Answer
- 1
Choose a specific incident that highlights your communication skills.
- 2
Focus on the steps you took to improve the working relationship.
- 3
Emphasize any positive outcomes resulting from your actions.
- 4
Use 'I' statements to show personal accountability.
- 5
Keep it professional; avoid personal attacks or negative language.
Example Answers
I once worked on a project with a colleague who was often dismissive of others’ ideas. I decided to set up a one-on-one meeting to discuss how we could collaborate better. I expressed my concerns respectfully and we set guidelines for our meetings to ensure everyone's input was valued. This transformed our communication and led to a successful project.
Tell me about a time when you encountered a significant problem while operating machinery. What steps did you take to resolve it?
How to Answer
- 1
Start with a specific incident involving a machinery problem.
- 2
Briefly describe the situation and what went wrong.
- 3
Explain the steps you took to identify and address the issue.
- 4
Highlight any tools or methods you used to solve the problem.
- 5
Conclude with the outcome and what you learned from the experience.
Example Answers
During my last job, I operated a conveyor belt that suddenly stopped due to a power failure. I immediately checked the main power supply and the emergency shutoff switch. After determining it was a blown fuse, I replaced it using a spare from our maintenance kit. The conveyor resumed operation, minimizing downtime, and I learned the importance of routine checks on electrical components.
Don't Just Read Edge Roller Questions - Practice Answering Them!
Reading helps, but actual practice is what gets you hired. Our AI feedback system helps you improve your Edge Roller interview answers in real-time.
Personalized feedback
Unlimited practice
Used by hundreds of successful candidates
Give an example of a time you had to lead a team to meet a tight deadline. What strategies did you employ?
How to Answer
- 1
Identify a specific project with a deadline.
- 2
Explain your role in leading the team.
- 3
Discuss how you organized tasks and prioritized work.
- 4
Mention communication strategies used to keep the team on track.
- 5
Highlight any tools or methods you used to manage the deadline.
Example Answers
In my last project, we had to deliver a software update in two weeks. I scheduled a kickoff meeting to clarify goals and delegate tasks based on team strengths. I used a shared task management tool to track progress and held daily check-ins to address any issues promptly. We completed the update ahead of schedule, which improved our client's satisfaction.
Describe an instance where you had to learn a new skill quickly to complete a task. How did you approach it?
How to Answer
- 1
Identify a specific skill and task context.
- 2
Explain why learning the skill was necessary.
- 3
Detail the steps you took to learn the skill quickly.
- 4
Highlight the results of your efforts.
- 5
Reflect on what you learned from the experience.
Example Answers
In my previous job, I had to learn Python quickly to automate a data task. I enrolled in a weekend crash course to cover the basics, practiced with real datasets during my breaks, and consulted with colleagues who were experienced in Python. I successfully completed the automation within a week, saving our team many hours of manual work.
Can you provide an example of a conflict you faced on the job and how you resolved it?
How to Answer
- 1
Choose a specific conflict relevant to your role.
- 2
Explain the situation briefly, focusing on the conflict.
- 3
Describe the steps you took to resolve the issue.
- 4
Highlight the positive outcome of your resolution.
- 5
Mention any lessons learned from the experience.
Example Answers
In my previous job, a team member disagreed with my approach on a project. I scheduled a meeting to discuss our perspectives openly. We listened to each other and combined our ideas, which led to a more effective solution that satisfied both of us. Ultimately, it strengthened our collaboration.
What steps have you taken to improve your skills as an edge roller operator?
How to Answer
- 1
Identify specific training programs or certifications you've completed.
- 2
Mention any workshops or hands-on experience that enhanced your skills.
- 3
Discuss any feedback you’ve received and how you applied it.
- 4
Share how you keep up with industry trends or new technologies.
- 5
Highlight collaborative efforts with experienced operators to learn techniques.
Example Answers
I completed a certification course in advanced edge rolling techniques and regularly participate in hands-on workshops to refine my skills.
How do you prioritize tasks when working multiple edge roller machines?
How to Answer
- 1
Assess which machine has the highest production demand.
- 2
Identify tasks that require immediate attention due to deadlines.
- 3
Use a checklist to track progress on each machine.
- 4
Communicate with the team to stay updated on changes in priorities.
- 5
Evaluate machine performance and downtime to adjust priorities as needed.
Example Answers
I prioritize tasks by first evaluating which edge roller machine has the highest production demand and focusing on that. I then assess any urgent tasks that must be done immediately due to deadlines, and I keep a checklist to monitor the progress across all machines.
Have you ever trained someone new on edge roller operations? What was your approach?
How to Answer
- 1
Describe your training methodology, such as hands-on practice or shadowing.
- 2
Mention how you assessed the new trainee's understanding and progress.
- 3
Explain any supportive materials or resources you provided.
- 4
Share an example of a challenge faced during training and how you overcame it.
- 5
Highlight the importance of safety and efficiency in your training approach.
Example Answers
Yes, I trained a new operator by first having them shadow me for a day. Then we moved to hands-on operation where I guided them through each step while explaining the safety protocols. I regularly checked in to assess their understanding and provided a checklist to help them remember key steps.
Can you provide an example of how you have received and acted upon feedback in the workplace?
How to Answer
- 1
Choose a specific example where feedback was given.
- 2
Explain the type of feedback received and who provided it.
- 3
Discuss how you processed the feedback and what actions you took.
- 4
Highlight the positive outcomes or changes resulting from your actions.
- 5
Keep it focused and concise, ideally within a couple of minutes.
Example Answers
In my previous role as a project coordinator, my manager noted that I was taking too long to respond to team emails. I took this feedback seriously, organized my email management, and set specific times to check and respond to emails. As a result, our team communication improved significantly, and deadlines were met more efficiently.
Don't Just Read Edge Roller Questions - Practice Answering Them!
Reading helps, but actual practice is what gets you hired. Our AI feedback system helps you improve your Edge Roller interview answers in real-time.
Personalized feedback
Unlimited practice
Used by hundreds of successful candidates
What motivates you to perform well in your role as an edge roller operator?
How to Answer
- 1
Focus on specific aspects of the role that excite you.
- 2
Connect your motivations to achieving team and company goals.
- 3
Mention how quality and efficiency drive your performance.
- 4
Consider personal satisfaction and pride in your work.
- 5
Emphasize the importance of safety and precision in your role.
Example Answers
I am motivated by the challenge of meeting production targets while ensuring the highest quality. I take pride in my ability to maintain efficiency and safety standards, which contributes to the team’s success.
Situational Interview Questions
If you notice that the edge roller is producing defects in the product, what immediate actions would you take?
How to Answer
- 1
Immediately stop the machine to prevent further defects.
- 2
Inspect the edge roller for visible signs of damage or misalignment.
- 3
Check the settings and parameters to ensure they are correct.
- 4
Consult with team members for additional insights on the problem.
- 5
Document the issue and any actions taken for future reference.
Example Answers
I would first stop the machine to avoid producing more defective products. Next, I would check the edge roller for any damage or misalignment before reviewing the machine settings to ensure they are correctly configured.
Imagine you are behind schedule on a production run. What measures would you implement to accelerate your output?
How to Answer
- 1
Assess current workflow and identify bottlenecks.
- 2
Prioritize tasks that can yield the quickest results.
- 3
Communicate with the team about the urgency and plan of action.
- 4
Consider adding temporary resources or overtime if feasible.
- 5
Implement quality checks throughout to reduce rework.
Example Answers
I would first analyze the production line to spot any bottlenecks; then I would focus on reallocating resources to critical tasks that can be completed quickly. I'd also communicate with my team to ensure everyone is aligned with our new urgency.
Don't Just Read Edge Roller Questions - Practice Answering Them!
Reading helps, but actual practice is what gets you hired. Our AI feedback system helps you improve your Edge Roller interview answers in real-time.
Personalized feedback
Unlimited practice
Used by hundreds of successful candidates
You witness a colleague ignoring safety protocols while operating an edge roller. What do you do?
How to Answer
- 1
Assess the situation quickly to determine the severity of the safety violation
- 2
Approach the colleague calmly and discreetly to discuss the concern
- 3
Remind them of the importance of safety protocols for their personal safety and that of others
- 4
If they refuse to comply, report the incident to a supervisor or safety officer
- 5
Document the incident and your actions for future reference
Example Answers
I would first assess if anyone is in immediate danger. If not, I would approach my colleague and politely remind them about the safety protocols and why they are important. If they continue ignoring the protocols, I would report it to a supervisor for further action.
You are asked to collaborate with the engineering team to improve an edge roller process. How would you approach this?
How to Answer
- 1
Assess the current edge roller process and gather data on its performance
- 2
Engage with the engineering team to understand their perspectives and challenges
- 3
Identify specific areas for improvement based on collected data and team input
- 4
Propose actionable solutions and collaborate on implementing changes
- 5
Follow up with metrics to measure the impact of the improvements
Example Answers
I would start by reviewing the performance data of the current edge roller process to identify any bottlenecks. Then, I would meet with the engineering team to discuss their insights and challenges. Together, we could pinpoint specific areas for improvement and brainstorm effective solutions. After implementing any changes, I would track the results to ensure the enhancements are beneficial.
If the edge roller suddenly fails during peak production, what steps would you take to address the issue?
How to Answer
- 1
Quickly assess the situation and identify the cause of failure
- 2
Communicate with the team to inform them of the issue and prevent further complications
- 3
Implement immediate temporary measures to minimize production downtime
- 4
Follow standard operating procedures to initiate repairs or a replacement
- 5
Document the failure and analyze it later to prevent future occurrences
Example Answers
First, I would stop the production line to ensure safety and prevent damage. Then, I'd quickly diagnose the issue while informing the team about the situation. If it's a simple fix, I'd address it immediately; otherwise, I'd initiate our emergency protocol to get a replacement roller as fast as possible. After resolving the issue, I would document everything for future reference.
How would you handle being assigned to operate two edge rollers at once during a demanding production run?
How to Answer
- 1
Prioritize safety and ensure both machines are functioning correctly before starting.
- 2
Communicate with your team about the dual operation and any challenges you anticipate.
- 3
Develop a systematic approach to monitor both machines, such as setting specific intervals to check each one.
- 4
Stay organized and focused to prevent mistakes during the high-pressure scenario.
- 5
Be prepared to ask for assistance if the workload becomes overwhelming.
Example Answers
I would start by checking that both edge rollers are in good working condition. Then, I would communicate with my team to make sure everyone is aware of the situation. I would also set specific intervals to monitor the performance of each roller, ensuring I remain organized throughout the production run.
If you have a shortage of materials needed for the edge roller process, how would you handle the situation?
How to Answer
- 1
Assess the extent of the material shortage immediately
- 2
Communicate with suppliers to understand lead times for new materials
- 3
Explore alternative materials that can be used in the process
- 4
Adjust production schedules to manage the impact of the shortage
- 5
Document the situation for future reference and analysis
Example Answers
I would first assess how much material is missing and how it affects production. Then, I would contact our suppliers to get an estimated delivery date. If the delay is significant, I would look for alternative materials that meet our standards. Meanwhile, I would adjust the production schedule to minimize downtime.
If a major safety incident occurred during edge rolling operations, what steps would you take immediately following the incident?
How to Answer
- 1
Ensure the immediate safety of all personnel by evacuating the area if necessary.
- 2
Contact emergency services if there are injuries or significant risks.
- 3
Secure the incident scene to preserve evidence for investigation.
- 4
Notify your supervisor and follow company protocol for incident reporting.
- 5
Document the incident details accurately while they are fresh in your mind.
Example Answers
First, I would ensure that everyone is safe by evacuating the area if needed. Next, I would call emergency services for any injuries and secure the incident site. After that, I would inform my supervisor about the situation and begin to document the facts surrounding the incident.
If a customer requests a modification in the product specifications after production has started, how would you respond?
How to Answer
- 1
Acknowledge the customer's request and show understanding.
- 2
Assess the impact of the modification on production timelines.
- 3
Communicate transparently about feasibility and potential costs.
- 4
Offer alternatives if the requested modification is not possible.
- 5
Ensure follow-up to keep the customer informed on decisions.
Example Answers
I would first acknowledge the customer's request and thank them for their feedback. Then, I would review the impact on our current production schedule. If feasible, I would explain any additional costs and timeframes involved. If the modification isn't possible, I would suggest a workable alternative and keep them updated throughout the process.
Edge Roller Position Details
Related Positions
- Wire Roller
- Hand Roller
- Cross Roller
- Tube Roller
- Counter Roller
- Pipe Roller
- Roll Wrapper
- Roll Operator
- Plastic Roller
- Edge Worker
Similar positions you might be interested in.
Ace Your Next Interview!
Practice with AI feedback & get hired faster
Personalized feedback
Used by hundreds of successful candidates
Ace Your Next Interview!
Practice with AI feedback & get hired faster
Personalized feedback
Used by hundreds of successful candidates