Top 30 Roll Operator Interview Questions and Answers [Updated 2025]
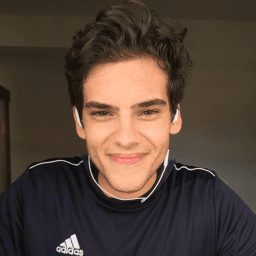
Andre Mendes
•
March 30, 2025
Preparing for a Roll Operator interview can be daunting, but we've got you covered. In this updated guide for 2025, we've compiled the most common interview questions for the Roll Operator role, along with insightful example answers and practical tips to help you respond effectively. Whether you're a seasoned professional or new to the field, this post will equip you with the confidence and knowledge to ace your interview.
Download Roll Operator Interview Questions in PDF
To make your preparation even more convenient, we've compiled all these top Roll Operatorinterview questions and answers into a handy PDF.
Click the button below to download the PDF and have easy access to these essential questions anytime, anywhere:
List of Roll Operator Interview Questions
Situational Interview Questions
If a machine breaks down unexpectedly during your shift, what steps would you take to handle the situation?
How to Answer
- 1
Remain calm and assess the situation quickly.
- 2
Check the machine for obvious issues and safety hazards.
- 3
Notify your supervisor or maintenance team immediately.
- 4
Document the breakdown details and any steps taken.
- 5
Follow company protocols for machine downtime.
Example Answers
I would first stay calm and assess the machine to see if there’s an obvious issue. Then, I would notify my supervisor and let the maintenance team handle the repairs while I document the problem.
Imagine you discover a defect in the finished rolls. How would you address this issue with your team?
How to Answer
- 1
Identify the defect clearly and gather all relevant information.
- 2
Communicate the issue to the team promptly and transparently.
- 3
Encourage a collaborative approach to find a solution.
- 4
Discuss potential preventive measures to avoid future defects.
- 5
Follow up on the implementation of solutions and review outcomes.
Example Answers
I would first identify the specific defect and gather any data related to it. Then, I would call a team meeting to discuss the issue openly, ensuring everyone understands the problem. We'd work together to brainstorm solutions and decide on immediate actions, and later I would check in to see how well our solutions worked.
Don't Just Read Roll Operator Questions - Practice Answering Them!
Reading helps, but actual practice is what gets you hired. Our AI feedback system helps you improve your Roll Operator interview answers in real-time.
Personalized feedback
Unlimited practice
Used by hundreds of successful candidates
If you witness a colleague ignoring safety protocols while operating the roll, what would you do?
How to Answer
- 1
Stay calm and assess the situation before acting.
- 2
Prioritize immediate safety and intervene if necessary.
- 3
Speak to your colleague privately to address the concern.
- 4
If the behavior continues, report it to a supervisor.
- 5
Focus on promoting a culture of safety and support.
Example Answers
I would first observe the situation carefully and ensure that no one is in immediate danger. If I felt that safety was being compromised, I would approach my colleague and politely remind them of the safety protocol they were ignoring. If they continued to disregard safety measures, I would escalate the issue to a supervisor to ensure everyone's safety.
How would you communicate with your supervisor if you feel the rolling specifications are unrealistic?
How to Answer
- 1
Be clear and precise about what specifications seem unrealistic
- 2
Provide specific examples of the issues you see
- 3
Suggest possible alternatives or solutions
- 4
Express your commitment to quality and safety
- 5
Be open to discussion and feedback from your supervisor
Example Answers
I would schedule a time to speak with my supervisor and explain that based on my experience, the current rolling specifications seem challenging. I would provide specific examples of previous rolls that led to defects under these specifications and suggest adjusting the parameters or discussing alternative approaches. My goal would be to maintain quality and productivity.
You notice a conflict between two team members during a shift. How would you intervene to resolve it?
How to Answer
- 1
Assess the situation discreetly before intervening.
- 2
Listen to both sides of the conflict separately.
- 3
Encourage open communication between the team members.
- 4
Facilitate a solution that works for both parties.
- 5
Follow up to ensure the resolution was effective.
Example Answers
I would first observe the conflict to understand its nature. Once I have context, I would speak to each team member individually to hear their perspective. Then, I would bring them together to discuss the issue in a respectful manner, guiding them toward a compromise, and finally check in later to ensure they're working well together again.
How do you handle stress when production demands increase unexpectedly?
How to Answer
- 1
Stay calm and assess the situation to prioritize tasks
- 2
Communicate clearly with team members to delegate responsibilities
- 3
Use a checklist to track progress on urgent tasks
- 4
Take short breaks to maintain focus and reduce stress
- 5
Seek assistance if the workload is unmanageable
Example Answers
When production demands increase, I first take a moment to assess the situation and prioritize which tasks need immediate attention. I then communicate with my team to delegate responsibilities effectively, ensuring we all work together efficiently.
If you need input from another department to complete a rolling project, how would you collaborate with them?
How to Answer
- 1
Identify the specific input you need from the other department
- 2
Reach out directly to the appropriate contacts in that department
- 3
Clearly communicate the timelines and importance of their input
- 4
Set up a meeting to discuss the project and gather their insights
- 5
Follow up with progress updates and express gratitude for their assistance
Example Answers
I would first identify the specific data I need from the engineering department. Then, I would reach out to the project manager and explain our timeline. I would suggest setting up a meeting to discuss any challenges they foresee that could affect the rolling project.
If you accidentally set the wrong parameters on the roll machine, how would you rectify this mistake?
How to Answer
- 1
Stay calm and assess the situation immediately.
- 2
Identify the incorrect parameters and the potential impact on the project.
- 3
Reset the machine to the correct settings following standard operating procedures.
- 4
Communicate the mistake to your supervisor and team to keep them informed.
- 5
Monitor the machine closely after adjustments to ensure proper operation.
Example Answers
If I set the wrong parameters, I would first remain calm and check what settings were incorrect. I would then safely reset the parameters to the correct values using the machine's guide. After making changes, I would inform my supervisor and observe the machine to ensure it runs properly.
How would you decide which resources to allocate when multiple operations are in progress?
How to Answer
- 1
Assess the urgency and importance of each operation.
- 2
Evaluate the current resource availability and demands.
- 3
Consider the impact of resource allocation on overall productivity.
- 4
Communicate with team members to understand their needs.
- 5
Make data-driven decisions based on operational performance metrics.
Example Answers
I would first evaluate which operations are critical to meeting deadlines. Then, I’d check resource availability and prioritize those operations that have the highest impact.
If you are tasked with overseeing multiple rolling projects, how would you prioritize them?
How to Answer
- 1
Assess deadlines for each project and prioritize those with the soonest completion dates.
- 2
Evaluate the resources available and allocate them based on project demands.
- 3
Consider the impact of each project on overall operations and customer satisfaction.
- 4
Communicate with stakeholders to understand their priorities and expectations.
- 5
Regularly review and adjust priorities as project statuses change.
Example Answers
I would first look at the deadlines of each project, prioritizing those that need to be completed soonest. Then, I’d review the resources we have on hand and adjust allocations based on the demands of each project.
Don't Just Read Roll Operator Questions - Practice Answering Them!
Reading helps, but actual practice is what gets you hired. Our AI feedback system helps you improve your Roll Operator interview answers in real-time.
Personalized feedback
Unlimited practice
Used by hundreds of successful candidates
Behavioral Interview Questions
Can you describe a time when you worked closely with a team to resolve a manufacturing issue?
How to Answer
- 1
Select a specific manufacturing issue you faced as a team.
- 2
Explain your role and how you contributed to the resolution.
- 3
Highlight collaboration and communication among team members.
- 4
Describe the outcome and improvements achieved through the teamwork.
- 5
Keep your answer concise and focused on your contribution.
Example Answers
In my previous role, our team faced a problem with a high defect rate in product assembly. I coordinated a team meeting to identify the root cause, which was a misalignment in machine settings. By providing training on proper setup and creating a checklist, we reduced defects by 30%.
Tell me about a time when you identified a problem in the rolling process and how you addressed it.
How to Answer
- 1
Start with a specific problem you identified.
- 2
Explain how you noticed the issue and what impact it had.
- 3
Describe the steps you took to investigate and resolve the problem.
- 4
Highlight any tools or techniques you used in the process.
- 5
Share the outcome and what you learned from the experience.
Example Answers
In my previous role, I noticed an inconsistent thickness in the rolled materials. After monitoring the process, I realized that the temperature settings were fluctuating. I collaborated with the maintenance team to recalibrate the heating elements, which stabilized the temperature. As a result, the thickness variance dropped significantly, improving product quality.
Don't Just Read Roll Operator Questions - Practice Answering Them!
Reading helps, but actual practice is what gets you hired. Our AI feedback system helps you improve your Roll Operator interview answers in real-time.
Personalized feedback
Unlimited practice
Used by hundreds of successful candidates
Describe an incident when you had to prioritize safety over production. What was the outcome?
How to Answer
- 1
Think of a specific situation from your past experience.
- 2
Explain the safety concern you identified.
- 3
Describe why you chose safety over meeting production targets.
- 4
Highlight the positive outcome or lesson learned.
- 5
Be honest and show your commitment to safety protocols.
Example Answers
In my previous role, I noticed a colleague working too close to a moving machine without proper guards. I halted production immediately to ensure everyone was safe. This decision reinforced the importance of safety for our team and prevented potential injuries.
Tell me about a time when you had to meet a tight deadline while operating rolls. How did you manage your time?
How to Answer
- 1
Identify a specific situation where you faced a deadline.
- 2
Explain the steps you took to prioritize your tasks.
- 3
Mention any tools or techniques you used to stay organized.
- 4
Discuss how you communicated with your team during the process.
- 5
Reflect on the outcome and what you learned from the experience.
Example Answers
In my previous job, we had a tight deadline to complete a large order for rolled materials. I prioritized tasks by tackling the most critical rolls first and used a checklist to keep track of progress. I also communicated regularly with my team to ensure we stayed on track. We managed to complete the order on time, and I learned the importance of effective time management under pressure.
Describe a time when you took the lead on a project involving roll operations. What was your approach?
How to Answer
- 1
Choose a specific project that highlights your leadership in roll operations.
- 2
Explain your role and the challenges you faced during the project.
- 3
Describe the steps you took to overcome those challenges and lead the team.
- 4
Highlight the outcome and what you learned from the experience.
- 5
Use metrics or results to demonstrate the success of your leadership.
Example Answers
In my previous position, I led a project to optimize our roll-to-roll process for a new product line. My approach involved analyzing the current workflow, identifying bottlenecks, and coordinating with my team to implement changes. We successfully reduced production time by 20%, which improved our delivery schedule.
Can you give an example of when you took initiative to improve a process in the rolling department?
How to Answer
- 1
Think of a specific process in the rolling department you noticed could be improved.
- 2
Describe the problem clearly and explain why it was an issue.
- 3
Detail the steps you took to implement your improvement.
- 4
Highlight the outcome and any measurable successes that resulted from your initiative.
- 5
Mention any teamwork or collaboration involved in the process improvement.
Example Answers
In my previous position, I noticed that the downtime during roll changes was affecting overall production efficiency. I proposed a new checklist for the roll change process to ensure that all necessary tools were ready before beginning the change. This reduced our downtime by about 30%.
What motivates you to perform well in the role of a roll operator?
How to Answer
- 1
Focus on safety and quality in production.
- 2
Highlight teamwork and collaboration as key motivators.
- 3
Discuss personal growth and skill enhancement.
- 4
Emphasize meeting targets and contributing to success.
- 5
Mention pride in producing high-quality products.
Example Answers
I am motivated by the importance of safety and quality in every roll I produce. Meeting production targets while ensuring everything meets the highest standards drives me to perform well.
Can you tell me about a time you received constructive feedback? How did you respond to it?
How to Answer
- 1
Choose a specific example that had a positive outcome.
- 2
Describe the feedback clearly and how you felt about it initially.
- 3
Explain the steps you took to improve based on the feedback.
- 4
Share the results of your actions and any accolades received after making the changes.
- 5
Highlight how this experience has shaped your approach to receiving feedback.
Example Answers
In my previous role as a machine operator, my supervisor pointed out that I was too focused on speed and sometimes compromised quality. Initially, I felt defensive, but I took time to reflect on the feedback. I started to pay more attention to the quality checks and even implemented a checklist before finalizing my work. As a result, my error rate dropped significantly and I received praise for my improved accuracy in the following months.
Have you ever trained a new employee on the rolling process? What did you focus on?
How to Answer
- 1
Share a specific example of training a new employee.
- 2
Highlight key aspects of the rolling process you taught.
- 3
Mention any safety practices emphasized during training.
- 4
Discuss how you assessed their understanding or skills.
- 5
Include how you provided ongoing support after initial training.
Example Answers
Yes, I trained a new employee on the rolling process last year. I focused on proper machine operation, safety protocols, and quality checks to ensure they understood each step. I also checked their progress by observing their work and offered feedback.
Don't Just Read Roll Operator Questions - Practice Answering Them!
Reading helps, but actual practice is what gets you hired. Our AI feedback system helps you improve your Roll Operator interview answers in real-time.
Personalized feedback
Unlimited practice
Used by hundreds of successful candidates
Technical Interview Questions
What types of rolling equipment are you familiar with, and what is your experience operating them?
How to Answer
- 1
List specific rolling equipment you have operated.
- 2
Mention the types of materials you've worked with.
- 3
Describe your level of experience, such as years or specific projects.
- 4
Highlight any safety protocols you follow when operating equipment.
- 5
Emphasize any relevant certifications or training you have.
Example Answers
I have operated cold roll mills and hot roll mills for over 5 years, primarily working with steel and aluminum. I ensure I follow all safety protocols and have completed a training course on machinery operation.
Explain the basic principles of the rolling process and how different factors can affect the outcome.
How to Answer
- 1
Start with a clear definition of the rolling process.
- 2
Mention the types of rolling processes, such as hot rolling and cold rolling.
- 3
Explain factors that affect rolling, like temperature and material properties.
- 4
Discuss the importance of roll spacing and speed.
- 5
Conclude with how adjustments can improve quality.
Example Answers
The rolling process involves deforming metal using a pair of rolls to reduce thickness and shape it. There are hot rolling and cold rolling, which differ in temperature. Factors like temperature can affect material flow, while roll spacing and speed influence surface finish and dimensions.
Don't Just Read Roll Operator Questions - Practice Answering Them!
Reading helps, but actual practice is what gets you hired. Our AI feedback system helps you improve your Roll Operator interview answers in real-time.
Personalized feedback
Unlimited practice
Used by hundreds of successful candidates
What routine maintenance practices do you follow to ensure rolling equipment is functioning properly?
How to Answer
- 1
Inspect equipment daily for signs of wear or damage.
- 2
Follow a scheduled lubrication routine to reduce friction.
- 3
Check and maintain proper alignment to avoid uneven wear.
- 4
Monitor operating temperatures and listen for unusual sounds.
- 5
Document all maintenance activities for future reference.
Example Answers
I perform daily inspections for wear and tear. Regularly, I lubricate critical parts to prevent friction issues and check alignment to ensure smooth operation.
How do you assess the quality of the rolled product during the production process?
How to Answer
- 1
Discuss the importance of visual inspection for defects on the surface
- 2
Emphasize the use of measuring tools for checking thickness and dimensions
- 3
Mention the significance of monitoring mechanical properties like strength and ductility
- 4
Explain the role of feedback from downstream processes on product quality
- 5
Highlight the importance of recording data for analysis and continuous improvement
Example Answers
I assess the quality of the rolled product by first conducting a visual inspection for any surface defects. I then use calipers to measure the thickness and dimensions to ensure they meet specifications. Additionally, I monitor the mechanical properties through tests, and I keep track of feedback from the next production stages to identify potential quality issues.
What steps do you take to troubleshoot when product specs are not being met during the rolling operation?
How to Answer
- 1
Check the machine settings against the specifications needed.
- 2
Inspect the raw materials for quality and consistency.
- 3
Monitor the rolling process for any abnormal sounds or vibrations.
- 4
Review historical data for similar issues and their resolutions.
- 5
Collaborate with team members to gather insights and suggestions.
Example Answers
First, I verify that the machine settings align with the desired specifications. If the settings are correct, I inspect the raw materials to ensure they meet quality standards. I also listen for unusual sounds during the operation that might indicate a fault.
Can you explain how you calibrate the rolling machine for a new type of product?
How to Answer
- 1
Understand the specifications of the new product and its materials.
- 2
Adjust the rolling machine settings such as speed, pressure, and temperature based on product requirements.
- 3
Use precision measuring tools to check the initial output and ensure it meets tolerances.
- 4
Conduct test rolls and monitor the product for quality and dimensions.
- 5
Make iterative adjustments based on the test results and product feedback.
Example Answers
First, I gather the product specifications and material properties. Then, I adjust the speed and pressure settings of the rolling machine. After this, I measure the first few rolls to ensure they meet the required dimensions, making further adjustments if necessary.
What types of materials have you rolled in the past, and how do they differ in handling?
How to Answer
- 1
Identify specific materials you've worked with, such as metal, plastic, or paper.
- 2
Explain the characteristics of each material that affect rolling, like thickness and hardness.
- 3
Discuss any special techniques or precautions for handling each material.
- 4
Mention any relevant equipment you used for rolling different materials.
- 5
Keep your answer structured and concise, highlighting key differences.
Example Answers
In my previous role, I rolled steel, aluminum, and plastic sheets. Steel required more pressure due to its hardness, while aluminum was easier to manipulate. For plastics, I had to control the temperature to avoid warping.
What kind of records do you maintain while operating rolling machinery?
How to Answer
- 1
List the specific types of records you keep, such as production output, machine maintenance logs, and safety checks.
- 2
Emphasize the importance of accuracy in record-keeping for operational efficiency and safety.
- 3
Mention documenting any issues or downtime to help with troubleshooting and future improvements.
- 4
Talk about how you utilize records for quality control and ensuring consistency in production.
- 5
Be prepared to explain how you track and report data to supervisors or management.
Example Answers
I maintain detailed logs of daily production output, including the quantity produced, any defects, and of course, the operational hours of the machinery. This helps in monitoring performance and planning maintenance.
Describe the setup process for preparing a production run on the rolling machine.
How to Answer
- 1
Review the production schedule and determine the specifications for the material to be processed.
- 2
Gather all necessary tools and materials, including the correct dies and safety equipment.
- 3
Adjust the machine settings according to the material type and required thickness.
- 4
Perform a test run with scrap material to ensure settings are correct before actual production.
- 5
Conduct a final safety check and ensure all safety guards are in place before starting the production run.
Example Answers
To set up a production run on the rolling machine, I first review the production schedule to get the specifications. Then, I gather the necessary tools, like the right dies. After that, I adjust the machine settings for the material type and thickness. I always run a test with scrap material to check the settings before starting production. Lastly, I perform a safety check to ensure everything is secure before operating the machine.
What troubleshooting methods do you employ if a roll is not meeting size specifications?
How to Answer
- 1
Check the machine settings for correct specifications.
- 2
Examine the materials being used for consistency and quality.
- 3
Monitor the temperature and speed settings during production.
- 4
Inspect the rollers for wear or damage that might affect output.
- 5
Document adjustments made and results for future reference.
Example Answers
I first check the machine settings to ensure they are aligned with the required specifications. If everything looks correct, I then inspect the materials for any quality issues. I also monitor temperature and speed to make sure they are within optimal ranges.
Don't Just Read Roll Operator Questions - Practice Answering Them!
Reading helps, but actual practice is what gets you hired. Our AI feedback system helps you improve your Roll Operator interview answers in real-time.
Personalized feedback
Unlimited practice
Used by hundreds of successful candidates
Roll Operator Position Details
Recommended Job Boards
Indeed (Roll Forming Operator)
www.indeed.com/q-roll-forming-operator-jobs.htmlZipRecruiter
www.ziprecruiter.com/Jobs/Roll-OperatorThese job boards are ranked by relevance for this position.
Related Positions
- Roll Wrapper
- Mill Operator
- Edge Roller
- Hand Roller
- Counter Roller
- Cross Roller
- Utility Operator
- Spinner Operator
- Tube Roller
- Wire Roller
Similar positions you might be interested in.
Ace Your Next Interview!
Practice with AI feedback & get hired faster
Personalized feedback
Used by hundreds of successful candidates
Ace Your Next Interview!
Practice with AI feedback & get hired faster
Personalized feedback
Used by hundreds of successful candidates