Top 34 Wire Roller Interview Questions and Answers [Updated 2025]
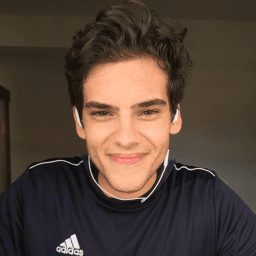
Andre Mendes
•
March 30, 2025
Are you preparing for a Wire Roller job interview and want to make a great impression? This post is your ultimate guide, featuring the most common questions asked in Wire Roller interviews. We provide example answers and tips on how to respond effectively, equipping you with the confidence and knowledge to excel. Dive in to discover how to articulate your skills and experience with precision and clarity.
Download Wire Roller Interview Questions in PDF
To make your preparation even more convenient, we've compiled all these top Wire Rollerinterview questions and answers into a handy PDF.
Click the button below to download the PDF and have easy access to these essential questions anytime, anywhere:
List of Wire Roller Interview Questions
Behavioral Interview Questions
Can you describe a time when you worked as part of a team to complete a complex wire rolling project?
How to Answer
- 1
Choose a specific project with clear roles.
- 2
Describe the team's objectives and your contribution.
- 3
Emphasize collaboration and communication.
- 4
Highlight any challenges and solutions you encountered.
- 5
Conclude with the outcome and what you learned.
Example Answers
During a project to roll custom wires for an automotive client, our team of five focused on specific roles. I coordinated the quality control checks and communicated closely with the machine operators. We faced a challenge when a wire batch had inconsistencies, so we held a team meeting to adjust our rolling parameters, leading to a successful output that met our client's specifications. This taught me the value of teamwork under pressure.
Tell me about a time when you had to adapt to a significant change in a work process in wire rolling.
How to Answer
- 1
Think of a specific change in wire rolling processes you've encountered.
- 2
Describe how you recognized the need for adaptation.
- 3
Explain the steps you took to adjust to the change.
- 4
Highlight any positive outcomes from your adaptation.
- 5
Keep it concise and focused on your role in the process.
Example Answers
In my previous role, we switched from manual to automated wire rolling. I attended training sessions to learn the new machine. I also worked closely with the team to troubleshoot issues early on, which helped us meet production targets effectively.
Don't Just Read Wire Roller Questions - Practice Answering Them!
Reading helps, but actual practice is what gets you hired. Our AI feedback system helps you improve your Wire Roller interview answers in real-time.
Personalized feedback
Unlimited practice
Used by hundreds of successful candidates
Describe a challenging situation you encountered while operating wire rolling machinery and how you resolved it.
How to Answer
- 1
Identify a specific challenging situation you faced.
- 2
Explain the steps you took to assess the problem.
- 3
Detail the actions you implemented to resolve the issue.
- 4
Discuss the outcome and what you learned from it.
- 5
Keep the answer focused on your role and contributions.
Example Answers
While operating the wire rolling machine, I noticed that the wire was consistently coming out uneven. I assessed the rollers and found that one was misaligned. I adjusted the alignment and tested the output, which resolved the issue and improved the quality of the wire.
Give an example of when your attention to detail caught a mistake in the wire rolling process before it became a bigger issue.
How to Answer
- 1
Think of a specific instance where you identified a mistake.
- 2
Describe what the mistake was and how you noticed it.
- 3
Highlight the actions you took to address the mistake.
- 4
Explain the impact of your actions on the production process.
- 5
Keep your answer structured: Situation, Task, Action, Result.
Example Answers
In my previous role, I noticed that a batch of wire was improperly labeled with the wrong gauge. While conducting my quality checks, I compared the physical wire to the specifications on the label and realized the discrepancy. I immediately contacted my supervisor, and we corrected the labels before the wire was rolled further. This prevented a potential quality issue in the final product and ensured our production schedule remained on time.
Can you provide an example of how you ensured safety while performing wire rolling operations?
How to Answer
- 1
Start with a specific safety protocol you followed.
- 2
Mention any personal protective equipment you wore.
- 3
Describe a situation where you identified a potential hazard.
- 4
Explain how you communicated safety rules to the team.
- 5
Conclude with the positive outcome of prioritizing safety.
Example Answers
In my previous role, I strictly followed the safety protocol by always wearing appropriate PPE, including gloves and safety glasses. During a routine wire rolling operation, I noticed that the area was cluttered with tools. I reported it immediately, and we cleared the space, preventing any accidents during the work.
Describe a time you had a disagreement with a coworker regarding wire specifications. How did you resolve it?
How to Answer
- 1
Focus on a specific instance that highlights your communication skills.
- 2
Explain the disagreement clearly without assigning blame.
- 3
Detail the steps you took to resolve the issue amicably.
- 4
Highlight the positive outcome of the resolution.
- 5
Show how the experience improved future collaboration.
Example Answers
In a project, a coworker and I disagreed on the gauge for a wire needed. I suggested we review the specifications together, which we did while referring to the project's requirements. We found that my choice was better suited for the load, and I explained my reasoning. Ultimately, we adopted my suggestion, which resulted in a successful final product and better teamwork going forward.
Describe a situation where you led a team during a wire rolling project. What was the outcome?
How to Answer
- 1
Choose a specific project with clear roles and goals
- 2
Highlight your leadership techniques and communication methods
- 3
Discuss challenges faced and how they were resolved
- 4
Emphasize the successful outcomes and team collaboration
- 5
Mention any metrics or positive feedback received after the project
Example Answers
In my previous role, I led a team of 5 on a wire rolling project where we needed to optimize production time. I organized daily stand-ups to keep everyone aligned. We faced supply delays, but by collaborating with our suppliers, we reduced downtime by 15%. The project finished two weeks early, leading to a cost savings of 10%.
Can you discuss a new skill or technique you have learned recently that improved your wire rolling capabilities?
How to Answer
- 1
Identify a specific skill or technique related to wire rolling.
- 2
Explain how you learned this skill, such as training or hands-on practice.
- 3
Discuss the impact of this skill on your work efficiency or output.
- 4
Use a concrete example to illustrate the improvement.
- 5
Keep your answer focused and relevant to the wire roller position.
Example Answers
Recently, I learned a new technique for adjusting the tension on the wire during the rolling process. I attended a workshop where experts demonstrated various methods. Implementing this technique improved my ability to achieve consistent diameter and reduced waste significantly.
Don't Just Read Wire Roller Questions - Practice Answering Them!
Reading helps, but actual practice is what gets you hired. Our AI feedback system helps you improve your Wire Roller interview answers in real-time.
Personalized feedback
Unlimited practice
Used by hundreds of successful candidates
How do you contribute to a positive workplace culture in a wire rolling environment?
How to Answer
- 1
Promote teamwork by encouraging collaboration among colleagues.
- 2
Maintain open communication to address issues promptly.
- 3
Recognize and celebrate the achievements of team members.
- 4
Practice safety and encourage others to prioritize safety.
- 5
Be approachable and offer support to newcomers.
Example Answers
I contribute to a positive workplace culture by fostering teamwork. I often organize small team meetings where we can share our challenges and support each other.
Can you give an example of how you received negative feedback and how you applied it to your work in wire rolling?
How to Answer
- 1
Choose a specific instance of feedback you received in wire rolling.
- 2
Explain the context and why the feedback was necessary.
- 3
Describe the steps you took to improve based on that feedback.
- 4
Highlight the positive outcome or improvement that resulted from your actions.
- 5
Keep your answer focused and concise, demonstrating accountability.
Example Answers
In my last position as a wire roller, I received feedback that my rolling speed was too slow, affecting production targets. I took this feedback seriously and worked on my technique, practicing to find a better rhythm. After a few weeks, I managed to increase my speed by 20%, which not only improved my productivity but also helped my team meet our goals.
Technical Interview Questions
What specific types of wire rolling machines are you familiar with, and how have you operated them in the past?
How to Answer
- 1
Identify specific wire rolling machines you have used.
- 2
Describe your role or tasks while operating these machines.
- 3
Mention any relevant certifications or training.
- 4
Provide examples of projects where you used these machines.
- 5
Highlight your problem-solving skills related to machine operation.
Example Answers
I have experience with Reid Wire Rollers and Hille Rolling Mills. I operated these machines primarily for shaping wire into specific profiles for manufacturing. I completed a training course on wire rolling operations, which enhanced my skills.
What types of materials do you have experience working with in wire rolling, and how do they affect the rolling process?
How to Answer
- 1
Identify specific types of wire materials you have worked with such as aluminum, stainless steel, or copper.
- 2
Explain how these materials have different properties that affect rolling, such as hardness or ductility.
- 3
Share any techniques you used to accommodate the specific properties of each material in the rolling process.
- 4
Mention any challenges you faced with certain materials and how you overcame them.
- 5
Conclude with how your experience with different materials has made you adaptable in wire rolling.
Example Answers
I have primarily worked with aluminum and copper in wire rolling. Aluminum is softer and has excellent ductility, which allows for easier shaping but requires careful temperature management to avoid deformation. In contrast, copper is harder and requires more force during rolling, but it provides better electrical conductivity. I adapted my rolling speeds and pressures according to the material characteristics to maintain quality.
Don't Just Read Wire Roller Questions - Practice Answering Them!
Reading helps, but actual practice is what gets you hired. Our AI feedback system helps you improve your Wire Roller interview answers in real-time.
Personalized feedback
Unlimited practice
Used by hundreds of successful candidates
What experience do you have with the maintenance and troubleshooting of wire rolling equipment?
How to Answer
- 1
Highlight any direct hands-on experience with wire rolling equipment.
- 2
Mention specific maintenance tasks you performed regularly.
- 3
Include any troubleshooting examples you encountered.
- 4
Emphasize your ability to work with technical manuals and schematics.
- 5
Discuss teamwork in maintenance efforts, if applicable.
Example Answers
I have worked directly with wire rolling equipment for over 3 years, performing regular maintenance such as oiling gears and replacing worn rollers. One example of troubleshooting I handled involved diagnosing a speed issue by checking the motor connections and adjusting the control settings, which resolved the problem quickly.
How do you perform quality checks on rolled wire, and what standards do you follow?
How to Answer
- 1
Explain the specific types of quality checks you perform on the rolled wire.
- 2
Mention industry standards you adhere to, such as ASTM or ISO standards.
- 3
Describe any tools or equipment you use during quality checks.
- 4
Provide examples of defects you look for in the rolled wire.
- 5
Highlight the importance of these checks for safety and compliance.
Example Answers
I perform visual inspections to check for surface defects like cracks or kinks, and I use calipers to measure the wire diameter against ASTM standards to ensure it meets specifications.
What processes do you follow to optimize wire rolling operations for efficiency?
How to Answer
- 1
Analyze current rolling speeds and adjust to minimize downtime.
- 2
Implement regular maintenance schedules to prevent machinery failures.
- 3
Train staff on best practices for setting up and operating equipment.
- 4
Use data tracking to identify bottlenecks in the rolling process.
- 5
Adjust material input parameters to enhance the flow and reduce waste.
Example Answers
To optimize wire rolling operations, I focus on adjusting the rolling speeds dynamically based on real-time monitoring and establishing maintenance schedules to avoid machinery breakdowns.
How do you keep records of your wire rolling operations and what information do you consider essential?
How to Answer
- 1
Mention the tools or software you use for recording data
- 2
Specify the types of information you track, such as batch numbers and materials
- 3
Emphasize the importance of accuracy and consistency in data entry
- 4
Explain how you use the records for quality control or process improvement
- 5
Discuss how you ensure records are accessible for audits or reviews
Example Answers
I use a digital logbook to keep records of all wire rolling operations. I track essential information like batch numbers, wire types, and production times. Accurate entries help maintain quality standards and streamline future processes.
What technical standards do you follow in wire rolling and how do you stay updated with industry practices?
How to Answer
- 1
Identify specific technical standards relevant to wire rolling, like ASTM or ISO.
- 2
Mention company policies and best practices that you adhere to.
- 3
Discuss how you engage in ongoing training or certifications.
- 4
Explain how you keep informed about new technologies and methods, such as industry publications or networking.
- 5
Provide examples of how you've implemented these standards in past roles.
Example Answers
I follow ASTM A555 as a standard for wire rolling to ensure quality. I also adhere to safety protocols set by OSHA. To stay updated, I participate in workshops and read journals like the Wire Journal International.
What techniques do you use to ensure the accuracy of wire dimensions during the rolling process?
How to Answer
- 1
Use calibrated measuring tools regularly to check wire dimensions.
- 2
Implement consistent monitoring and adjustments during the rolling process.
- 3
Keep a detailed log of measurements and adjustments for analysis.
- 4
Conduct routine maintenance on rolling equipment to ensure accuracy.
- 5
Train staff on proper techniques and the importance of precision.
Example Answers
I ensure accuracy by using calibrated measuring tools at each stage of the rolling process. I also monitor wire dimensions continuously and make adjustments when needed.
How do you analyze problems that occur during the wire rolling process to find effective solutions?
How to Answer
- 1
Identify the specific issue and gather data on its occurrence
- 2
Break down the rolling process into stages to isolate where the problem arises
- 3
Consult with team members who may have experienced similar issues
- 4
Test potential solutions on a small scale before full implementation
- 5
Document successful solutions and problematic trends for future reference
Example Answers
When I encounter a problem in the wire rolling process, I first pinpoint the specific issue by analyzing production data. I then break down the process into stages to see where the issue is most prominent. Collaboration with my team helps to bring different perspectives, and I always test solutions in small batches to ensure effectiveness before rolling them out fully.
What do you consider the most critical stages in the wire rolling process and why?
How to Answer
- 1
Identify the key stages in wire rolling such as initial setup, rolling, cooling, and inspection.
- 2
Explain the purpose of each stage clearly and concisely.
- 3
Emphasize the importance of precision and quality control in the process.
- 4
Consider mentioning potential problems that can arise if each stage is not executed properly.
- 5
Use specific examples from past experience if relevant.
Example Answers
The most critical stages in wire rolling include the initial setup to ensure equipment is calibrated, the rolling itself where the wire is formed to size, and cooling to maintain the integrity of the material. Each stage must be done with precision to prevent defects that could lead to product failure.
Don't Just Read Wire Roller Questions - Practice Answering Them!
Reading helps, but actual practice is what gets you hired. Our AI feedback system helps you improve your Wire Roller interview answers in real-time.
Personalized feedback
Unlimited practice
Used by hundreds of successful candidates
Can you explain how you manage tension levels while rolling wire?
How to Answer
- 1
Observe the wire feed and adjust the rollers for optimal tension.
- 2
Use the tension gauges available to monitor levels during the process.
- 3
Adjust the speed of the rolling machine to maintain consistent tension.
- 4
Regularly check for any kinks or irregularities in the wire as you work.
- 5
Communicate with the team to ensure consistent practices in tension management.
Example Answers
I regularly monitor the tension gauges and adjust the rollers as needed to keep the wire moving smoothly.
Situational Interview Questions
If you notice that the wire rolling process is producing inconsistent results, what steps would you take to address the issue?
How to Answer
- 1
Observe the rolling process to identify specific points of inconsistency
- 2
Check equipment settings and calibrations for accuracy
- 3
Inspect the wire material for quality and defects
- 4
Review and train staff on proper operating procedures
- 5
Implement a testing phase after adjustments to monitor improvements
Example Answers
I would start by closely observing the wire rolling process to pinpoint where the inconsistencies occur. Then, I would check the equipment settings to ensure everything is calibrated correctly. Next, I would inspect the wire material itself for any defects that might be causing issues.
Imagine you are leading a team of wire rollers, and one team member is underperforming. How would you handle the situation?
How to Answer
- 1
Assess the reasons for underperformance with a private conversation
- 2
Set clear expectations for performance and productivity
- 3
Offer support and training tailored to their needs
- 4
Monitor progress regularly and provide constructive feedback
- 5
If necessary, identify alternative roles or resources for improvement
Example Answers
I would first have a one-on-one discussion with the team member to identify any obstacles they are facing. Then, I would set clear performance goals and work with them to create a plan for improvement. Regular check-ins would ensure they stay on track, and I'd offer additional training if needed.
Don't Just Read Wire Roller Questions - Practice Answering Them!
Reading helps, but actual practice is what gets you hired. Our AI feedback system helps you improve your Wire Roller interview answers in real-time.
Personalized feedback
Unlimited practice
Used by hundreds of successful candidates
If you see a colleague bypassing safety procedures, how would you react?
How to Answer
- 1
Stay calm and assess the situation quickly
- 2
Privately approach the colleague to discuss your concerns
- 3
Emphasize the importance of safety for all workers
- 4
If the behavior continues, report it to a supervisor or safety officer
- 5
Always prioritize safety over friendships or peer pressure
Example Answers
I would first talk to my colleague privately, explaining the risks involved with bypassing safety procedures. I would stress that it affects everyone's safety and urge them to follow the protocols.
How would you prioritize your tasks if you were given a tight deadline to complete a large wire rolling order?
How to Answer
- 1
Assess the overall deadline and specific milestones needed.
- 2
Identify critical tasks that impact the completion time.
- 3
Break down the order into manageable sections to tackle one at a time.
- 4
Communicate with team members to delegate tasks effectively.
- 5
Adjust priorities as needed based on progress and any arising issues.
Example Answers
To prioritize tasks efficiently, I would first review the overall deadline and set specific milestones. I'd focus on the critical tasks that directly affect the production timeline, like preparing the rolling machine and ensuring materials are ready. Then, I'd break the order down into smaller sections, completing one at a time. I would also involve my team for better task delegation and adjust our plan as we make progress.
What would you do if a wire rolling machine suddenly malfunctions during a critical production run?
How to Answer
- 1
Stay calm and assess the situation quickly
- 2
Notify your supervisor immediately of the malfunction
- 3
Check for any obvious issues or error codes on the machine
- 4
Implement any safety protocols if necessary
- 5
Document the incident for future reference and follow up with maintenance
Example Answers
In the event of a malfunction, I would first remain calm and assess whether it poses any immediate safety risks. Then, I would alert my supervisor and check the machine for any obvious issues, such as error codes or unusual sounds, while following safety protocols.
If you were tasked with selecting a machine for a new wire rolling project, what factors would you consider?
How to Answer
- 1
Assess the wire material and its specifications including tensile strength and ductility
- 2
Evaluate the production volume and speed requirements for the project
- 3
Consider the available budget and return on investment for the machine
- 4
Check for available features like automation, precision control, and ease of operation
- 5
Examine supplier support and maintenance services for long-term reliability
Example Answers
I would start by analyzing the wire material to ensure the machine can handle its specifications like tensile strength. Then, I'd look at how quickly we need to produce to meet demand, followed by our budget for the machine. It's also important to consider automation features to improve efficiency. Finally, I'd check the support options from the supplier.
If a customer reported issues with the wire produced, how would you address their concerns?
How to Answer
- 1
Listen carefully to the customer's complaint for details
- 2
Acknowledge the issue and express understanding
- 3
Ask clarifying questions to gather more information
- 4
Provide a solution or proposal to resolve the problem
- 5
Follow up with the customer to ensure satisfaction
Example Answers
I would listen to the customer's concerns attentively and acknowledge their frustration. Then, I would ask specific questions to understand the issue better. Once I have the details, I would suggest a possible solution, such as redoing the wire or investigating the production process. Finally, I would follow up to make sure they are satisfied with the resolution.
How would you approach training a new team member on wire rolling machinery and practices?
How to Answer
- 1
Start with a thorough overview of the machinery and its components
- 2
Use hands-on demonstrations to illustrate key techniques
- 3
Encourage the new team member to practice under supervision
- 4
Provide written instructions or manuals for reference
- 5
Schedule regular check-ins to assess progress and address questions
Example Answers
I would begin by giving a detailed overview of the wire rolling machinery, explaining each part and its function. Then, I would demonstrate the rolling process step-by-step, allowing the new team member to observe closely. After that, I’d let them try operating the machinery while I supervise and give feedback. Finally, I would provide them with a written guide to help reinforce their learning.
How would you facilitate collaboration between different departments that depend on the wire rolling process?
How to Answer
- 1
Encourage regular cross-departmental meetings to discuss progress and challenges
- 2
Implement a shared digital platform for updates and document sharing
- 3
Define clear roles and responsibilities for each department in the wire rolling process
- 4
Collect feedback from all departments to continuously improve the collaboration
- 5
Establish metrics to track collaboration effectiveness and make adjustments as needed
Example Answers
I would set up bi-weekly meetings where representatives from each department can discuss their needs and feedback on the wire rolling process. This would help us align our goals and address any issues quickly.
What would you do if you found that key resources needed for a wire rolling job were running low?
How to Answer
- 1
Assess current inventory levels of key resources
- 2
Communicate with your supervisor or manager about the shortage
- 3
Identify alternative suppliers or sources for the materials
- 4
Propose a plan to prioritize production based on resource availability
- 5
Document the situation and steps taken for future reference
Example Answers
I would first check the inventory to confirm the levels of the essential resources. Then I would inform my supervisor about the shortage so that we can address it together. I would also start looking for alternative suppliers that could provide the materials quickly, and suggest adjustments to our production schedule if necessary.
Don't Just Read Wire Roller Questions - Practice Answering Them!
Reading helps, but actual practice is what gets you hired. Our AI feedback system helps you improve your Wire Roller interview answers in real-time.
Personalized feedback
Unlimited practice
Used by hundreds of successful candidates
If you were asked to evaluate the performance of the wire rolling team over the past quarter, what metrics would you consider?
How to Answer
- 1
Identify key production metrics such as output volume and quality metrics.
- 2
Consider operational efficiency indicators like downtime and cycle time.
- 3
Look at team performance metrics including safety incidents and employee feedback.
- 4
Include cost analysis metrics such as material waste and labor costs.
- 5
Combine quantitative data with qualitative observations for a comprehensive evaluation.
Example Answers
I would focus on output volume to see how much wire was produced, quality metrics to assess product standards, and factors like downtime which indicate operational efficiency. Additionally, I would review safety incidents to understand team performance and analyze costs associated with material waste.
Wire Roller Position Details
Related Positions
- Edge Roller
- Hand Roller
- Pipe Roller
- Tube Roller
- Cross Roller
- Wire Spinner
- Counter Roller
- Plastic Roller
- Wire Drawer
- Wire Brusher
Similar positions you might be interested in.
Ace Your Next Interview!
Practice with AI feedback & get hired faster
Personalized feedback
Used by hundreds of successful candidates
Ace Your Next Interview!
Practice with AI feedback & get hired faster
Personalized feedback
Used by hundreds of successful candidates