Top 32 Stamping Machine Operator Interview Questions and Answers [Updated 2025]
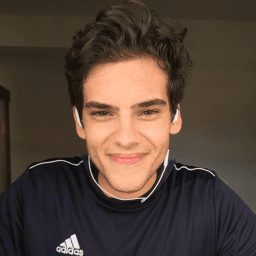
Andre Mendes
•
March 30, 2025
Preparing for a stamping machine operator interview can be daunting, but we're here to help you succeed. This blog post compiles the most common questions you're likely to encounter, complete with example answers and practical tips to help you respond effectively. Whether you're a seasoned operator or new to the field, these insights will boost your confidence and readiness for the big day.
Download Stamping Machine Operator Interview Questions in PDF
To make your preparation even more convenient, we've compiled all these top Stamping Machine Operatorinterview questions and answers into a handy PDF.
Click the button below to download the PDF and have easy access to these essential questions anytime, anywhere:
List of Stamping Machine Operator Interview Questions
Behavioral Interview Questions
Can you describe a time you encountered a mechanical failure while operating a stamping machine? How did you handle it?
How to Answer
- 1
Identify a specific incident with clear details.
- 2
Explain the nature of the mechanical failure.
- 3
Describe the steps you took to diagnose and fix the issue.
- 4
Mention any collaboration with colleagues or maintenance staff.
- 5
Highlight what you learned from the experience.
Example Answers
While operating the stamping machine, I noticed it stopped suddenly due to a jam. I quickly turned off the machine and investigated the cause. I found a piece of scrap material lodged in the dies. After clearing the jam, I performed a quick check to ensure everything was functioning correctly before restarting. This incident taught me the importance of monitoring the machine closely.
Tell me about a time when you worked with a team to improve the efficiency of a stamping process. What role did you play?
How to Answer
- 1
Start with a specific project or initiative related to stamping.
- 2
Clearly define your role and responsibilities within the team.
- 3
Discuss the strategies or methods the team used to improve efficiency.
- 4
Mention specific outcomes or improvements achieved.
- 5
Keep your response focused and on-topic.
Example Answers
In my previous role, our team identified that the changeover time between different stamping jobs was impacting productivity. I led a team to analyze the process, and we implemented a standardized procedure for quicker tool adjustments. As a result, we reduced changeover time by 30%, significantly increasing overall machine uptime.
Don't Just Read Stamping Machine Operator Questions - Practice Answering Them!
Reading helps, but actual practice is what gets you hired. Our AI feedback system helps you improve your Stamping Machine Operator interview answers in real-time.
Personalized feedback
Unlimited practice
Used by hundreds of successful candidates
Describe a situation where your attention to detail prevented a significant error in the stamping process.
How to Answer
- 1
Think of a specific instance where your attention made a difference.
- 2
Explain the context of the stamping process you were involved in.
- 3
Describe the error that could have occurred without your attention.
- 4
Share the steps you took to ensure accuracy during the process.
- 5
Highlight the positive outcome resulting from your vigilance.
Example Answers
During a production run, I noticed that the material thickness was slightly off from specifications. I double-checked the measurements and halted the machine, preventing faulty products from being processed.
Can you provide an example of a safety issue you identified on the shop floor? What steps did you take to resolve it?
How to Answer
- 1
Identify a specific safety issue you noticed in your experience
- 2
Describe the impact of the safety issue on workers or operations
- 3
Outline the steps you took to address the issue clearly and concisely
- 4
Mention any follow-up actions or preventive measures you implemented
- 5
Conclude with the outcome of your actions, emphasizing safety improvement
Example Answers
While working as a machine operator, I noticed that some tools were left out in the open, creating a tripping hazard. I immediately reported it to my supervisor and organized the work area to ensure tools were stored properly. Afterward, we held a team meeting to discuss safety protocols and reinforce the importance of a clean and safe workspace. As a result, incidents of tripping decreased significantly.
Describe a time you took the initiative to enhance machine operations. What was the outcome?
How to Answer
- 1
Think of a specific example where you identified a problem with machine operations.
- 2
Detail the steps you took to address the issue or improve efficiency.
- 3
Mention any collaboration or team involvement that was necessary.
- 4
State the measurable outcome or improvement that resulted from your actions.
- 5
Highlight any recognition you received for your initiative.
Example Answers
At my previous job, I noticed that the stamping machine was frequently producing scrap due to misalignment. I took the initiative to adjust the alignment setup and trained my coworkers on the new process. As a result, our scrap rate dropped by 15%, and we were recognized by management for improving productivity.
Can you give an example of how you have received and used feedback on your work?
How to Answer
- 1
Think of a specific instance when you received feedback.
- 2
Describe the feedback clearly and what it was about.
- 3
Explain how you implemented the feedback in your work.
- 4
Share the positive results from using the feedback.
- 5
Keep it concise and relevant to the stamping machine operator role.
Example Answers
In my last job, my supervisor pointed out that my stamping precision could be improved. I took this feedback seriously and practiced calibrating the machine more thoroughly. As a result, my error rate dropped significantly, and I contributed to a smoother production process.
Tell me about a specific goal you set for yourself in your role and how you achieved it.
How to Answer
- 1
Choose a specific goal related to your work as a stamping machine operator.
- 2
Explain why this goal was important to you and the company.
- 3
Detail the steps you took to achieve this goal, including any challenges you faced.
- 4
Share the outcome and any metrics that show your success.
- 5
Reflect on what you learned from this experience.
Example Answers
In my previous role, I set a goal to increase my machine's production efficiency by 15% over three months. I analyzed my workflow, identified bottlenecks, and collaborated with my supervisor to optimize settings. I met the goal by consistently tracking output and making adjustments, ultimately boosting efficiency by 18%. This taught me the value of continuous improvement.
Can you describe a situation where you demonstrated a strong work ethic on the job?
How to Answer
- 1
Think of a specific instance when you went above and beyond your duties.
- 2
Focus on your commitment to quality and reliability in your work.
- 3
Mention any challenges you faced and how you overcame them.
- 4
Emphasize teamwork and helping others if relevant.
- 5
Conclude with the positive outcome of your actions.
Example Answers
In my previous job, we had a tight deadline to complete a project. I worked late and collaborated with colleagues to ensure we met the target without compromising quality. As a result, our team finished a day early, impressing the management.
Technical Interview Questions
What types of stamping machines have you operated in the past, and what are the differences between them?
How to Answer
- 1
List specific types of stamping machines you have experience with
- 2
Explain the primary purpose of each type you mention
- 3
Highlight key differences in functionality or design
- 4
Mention any relevant safety or operational protocols
- 5
Be prepared to discuss your level of proficiency with each type
Example Answers
I have operated mechanical stamping presses and hydraulic stamping machines. Mechanical presses are typically faster and used for high-volume production, while hydraulic presses allow for more flexibility in force and are better for intricate shapes.
What regular maintenance tasks do you perform on stamping machines to ensure they operate efficiently?
How to Answer
- 1
Discuss checking and replacing worn parts regularly
- 2
Mention lubricating moving components as needed
- 3
Include inspecting and cleaning filters and air supply systems
- 4
Talk about performing routine calibration of the machine settings
- 5
Emphasize keeping a log of maintenance activities
Example Answers
I perform regular checks on the dies for wear and replace them as needed, lubricate the moving parts weekly, and clean the filters to ensure proper airflow.
Don't Just Read Stamping Machine Operator Questions - Practice Answering Them!
Reading helps, but actual practice is what gets you hired. Our AI feedback system helps you improve your Stamping Machine Operator interview answers in real-time.
Personalized feedback
Unlimited practice
Used by hundreds of successful candidates
How do you determine the appropriate stamping tool for a specific job?
How to Answer
- 1
Review the specifications and requirements of the job to understand the material and design.
- 2
Consider the thickness and type of material to choose the appropriate die.
- 3
Check if the part requires precision or complex shapes and select a custom die if necessary.
- 4
Evaluate the production volume to decide between standard or specialized tools.
- 5
Consult with engineers or experienced operators about past successful setups.
Example Answers
To determine the right stamping tool, I start by reviewing the job specifications to understand the material and design requirements. Then, I consider the material's thickness to choose the appropriate die. For high precision parts, I might evaluate the need for a custom die.
What quality control measures do you implement while operating stamping machines?
How to Answer
- 1
Describe daily inspections of machinery before operation
- 2
Explain monitoring material quality before stamping
- 3
Discuss maintaining accurate measurements of stamped parts
- 4
Mention routine calibration of stamping machines
- 5
Highlight documentation of quality checks for traceability
Example Answers
I perform daily inspections of the stamping machine, checking for any wear or damage, and ensure that all safety features are functioning correctly. Additionally, I verify the quality of the raw materials before they enter the stamping process to prevent defects.
How would you troubleshoot a stamping machine that produces defective parts?
How to Answer
- 1
Check the machine setup and ensure all parameters are set correctly
- 2
Inspect raw materials for defects or inconsistencies
- 3
Examine punches and dies for wear or damage
- 4
Monitor the machine operation to identify unusual noises or behaviors
- 5
Review maintenance logs to determine if there were recent issues or repairs
Example Answers
First, I would start by checking the machine setup to ensure all parameters are correctly configured. Next, I would inspect the raw materials to verify they meet specifications. If everything seems fine there, I’d examine the punches and dies for any wear that might affect production.
Have you ever had to program a CNC stamping machine? Describe your experience.
How to Answer
- 1
Start with a brief overview of your programming experience.
- 2
Mention specific machinery you have worked with if possible.
- 3
Highlight any successful projects or outcomes from your programming.
- 4
Discuss your familiarity with software or tools related to CNC programming.
- 5
Emphasize your problem-solving skills during programming challenges.
Example Answers
I have programmed CNC stamping machines for three years. At my previous job, I used a Mitsubishi CNC to create precision parts, improving production speed by 20%. I am experienced with CAD/CAM software and enjoy tackling programming challenges.
What types of materials have you worked with in stamping, and how do they affect the process?
How to Answer
- 1
Identify specific materials you have experience with, such as steel, aluminum, or plastics.
- 2
Explain how different materials affect the stamping process, like hardness and ductility.
- 3
Mention any specific challenges you've faced with certain materials and how you overcame them.
- 4
Discuss how you ensure quality and precision based on the material used.
- 5
Include any safety considerations that are material-specific.
Example Answers
I have primarily worked with stainless steel and aluminum. Stainless steel requires higher tonnage due to its hardness, which affects die wear. I ensure precision by using slower speeds during stamping to maintain quality.
Can you explain the process you follow for setting up a die in a stamping machine?
How to Answer
- 1
Review the die specifications and ensure all components are present
- 2
Securely fasten the die to the machine bed using appropriate tools
- 3
Adjust the die settings according to the material and thickness
- 4
Perform a trial run with scrap material to check alignment and operation
- 5
Double-check all safety features before starting production
Example Answers
First, I review the die specifications to confirm all components are available. Then I secure the die to the machine bed, making sure it's tight. After that, I adjust the settings based on the material we're using. I always do a trial run with scrap material to ensure everything is aligned correctly. Finally, I check all safety features before starting production.
What safety regulations should a stamping machine operator be aware of?
How to Answer
- 1
Know the specific OSHA regulations related to machine safety.
- 2
Understand lockout/tagout procedures to prevent accidental start-up during maintenance.
- 3
Be familiar with personal protective equipment (PPE) requirements such as gloves and eye protection.
- 4
Recognize safety features on the machine, such as emergency stop buttons and guards.
- 5
Stay updated on workplace safety training and reporting procedures for hazards.
Example Answers
As a stamping machine operator, I am aware of OSHA regulations that ensure our machines are properly maintained and operated safely. I prioritize lockout/tagout procedures to ensure no unexpected starts during maintenance.
What production rates do you typically achieve while operating stamping machines, and how do you maintain them?
How to Answer
- 1
Mention specific production rates from previous experiences.
- 2
Explain processes you follow to achieve and maintain these rates.
- 3
Discuss the importance of machine maintenance and inspections.
- 4
Include any techniques for optimizing efficiency during operation.
- 5
Highlight teamwork or collaboration with other staff for improved output.
Example Answers
In my previous role, I typically achieved production rates of 200 parts per hour while operating the stamping machine. I maintained these rates by ensuring regular maintenance checks and minor adjustments during shifts to keep the machine running smoothly.
Don't Just Read Stamping Machine Operator Questions - Practice Answering Them!
Reading helps, but actual practice is what gets you hired. Our AI feedback system helps you improve your Stamping Machine Operator interview answers in real-time.
Personalized feedback
Unlimited practice
Used by hundreds of successful candidates
How comfortable are you with reading and interpreting engineering blueprints or schematics?
How to Answer
- 1
Mention any formal training you have in reading blueprints.
- 2
Describe your experience with specific types of schematics relevant to stamping machines.
- 3
Explain how you have used blueprints in previous jobs to complete tasks.
- 4
Discuss your ability to learn quickly if you encounter unfamiliar schematics.
- 5
Highlight the importance of accuracy when interpreting engineering documents.
Example Answers
I have completed a course in blueprint reading, focusing on mechanical systems. In my last job, I regularly interpreted blueprints to set up stamping machines accurately and made adjustments based on the specifications.
What key performance indicators do you think are essential to track for a stamping machine operation?
How to Answer
- 1
Identify production efficiency metrics to measure output against targets.
- 2
Track downtime to understand and reduce machine failures or maintenance issues.
- 3
Monitor scrap rates to assess material waste and quality control.
- 4
Include cycle time to evaluate the time taken for each stamping process.
- 5
Consider employee safety and incident rates to maintain a safe working environment.
Example Answers
I believe essential KPIs for stamping operations include production efficiency, as it helps to track if we are meeting our output targets. Additionally, monitoring downtime due to maintenance can help identify areas for improvement. Scrap rates are also crucial to ensure high-quality production.
What should an operator be aware of regarding environmental compliance in stamping operations?
How to Answer
- 1
Understand regulations on waste disposal and chemicals used in the stamping process
- 2
Be familiar with noise and emission standards to minimize environmental impact
- 3
Implement recycling practices for metal scraps and materials
- 4
Ensure proper storage and labeling of hazardous materials
- 5
Participate in safety and compliance training regularly
Example Answers
An operator should know the local regulations regarding hazardous waste disposal to prevent contamination. Recycling metal scraps is also important to minimize waste and comply with environmental standards.
Situational Interview Questions
If you noticed smoke coming from a stamping machine, what immediate actions would you take?
How to Answer
- 1
Turn off the machine immediately if safe to do so
- 2
Alert your supervisor or the responsible personnel right away
- 3
Evacuate the area if smoke is excessive or indicates a fire risk
- 4
Use a fire extinguisher if trained and safe to suppress small flames
- 5
Do not attempt to diagnose the issue until the machine is inspected
Example Answers
I would immediately turn off the machine to prevent further issues, then alert my supervisor to ensure they are aware of the potential hazard.
Imagine there is a backlog of orders due to machine downtime. How would you prioritize your workload?
How to Answer
- 1
Assess the urgency of each order based on deadlines.
- 2
Consider the size and complexity of the orders.
- 3
Communicate with supervisors or team members for input.
- 4
Focus on high-demand products first.
- 5
Utilize available resources for maximum efficiency.
Example Answers
I'd start by reviewing the order list and identifying which orders are closest to their due dates. Then, I'd prioritize larger orders that might take more time to complete, ensuring that I communicate any challenges to my supervisor.
Don't Just Read Stamping Machine Operator Questions - Practice Answering Them!
Reading helps, but actual practice is what gets you hired. Our AI feedback system helps you improve your Stamping Machine Operator interview answers in real-time.
Personalized feedback
Unlimited practice
Used by hundreds of successful candidates
You and a coworker disagree on how to set up a stamping machine for a new product. How would you handle the situation?
How to Answer
- 1
Listen carefully to your coworker's perspective and rationale.
- 2
Present your viewpoint clearly, focusing on facts and data.
- 3
Suggest collaborating on a test run or trial setup to see which method performs better.
- 4
Remain respectful and professional throughout the discussion.
- 5
Document the agreed approach and results for future reference.
Example Answers
I would first listen to my coworker's reasoning to understand their point of view. Then I would share my own ideas based on previous experience and relevant data. I would propose conducting a test run to compare both methods and decide which is more effective.
A customer has an urgent request for a custom stamped part. How would you manage this request alongside your regular duties?
How to Answer
- 1
Assess the urgency of the request and clarify the deadline with the customer.
- 2
Prioritize tasks based on deadlines and impact on operations.
- 3
Communicate with your team about the urgent request and seek their input for support.
- 4
Look for efficiencies in regular duties to make time for the urgent request.
- 5
Document the request and your actions, keeping the customer informed throughout.
Example Answers
I would first confirm the deadline with the customer to understand how urgent the request is. Then, I would prioritize my tasks by determining what can be delegated or postponed. I would communicate this situation with my team to see if anyone can assist in managing my regular workload.
You have ideas for improving the stamping process that are different from your supervisor's approach. How would you present your suggestions?
How to Answer
- 1
Make sure to clearly understand your supervisor's current approach before suggesting changes
- 2
Prepare your suggestions with specific reasoning and data to support your ideas
- 3
Choose an appropriate time and method to discuss your suggestions, like during a team meeting or one-on-one
- 4
Be respectful and open-minded during the discussion, encouraging feedback
- 5
Emphasize the benefits of your suggestions for the team and the company
Example Answers
I would first ensure I fully understand my supervisor's current methods. Then, I would prepare data that supports my suggestions and present them during our next team meeting, focusing on how these changes could improve efficiency and quality.
If a team member regularly misses quality checks, how would you address the issue with them?
How to Answer
- 1
Schedule a private conversation to discuss the issue directly.
- 2
Use specific examples of missed quality checks to illustrate the concern.
- 3
Ask open-ended questions to understand their perspective and challenges.
- 4
Offer support and resources to help them improve their performance.
- 5
Agree on a follow-up plan to monitor progress and provide feedback.
Example Answers
I would first have a private conversation with my team member to address the missed quality checks. I would bring up specific instances and ask if there were any challenges they were facing. Then, I would offer my help and share resources they might find useful. Finally, we could set a follow-up date to review their progress together.
You are nearing the end of your shift when a last-minute order is sent to you. Explain how you would handle it.
How to Answer
- 1
Assess the new order's urgency and requirements quickly.
- 2
Communicate with your supervisor about the order and workload.
- 3
Prioritize the order based on deadlines and machine availability.
- 4
Ensure that the necessary materials and tools are ready.
- 5
Stay focused on quality while working efficiently to meet the deadline.
Example Answers
I would quickly assess the order and determine its urgency. I'd inform my supervisor and see if we need to adjust my end-of-shift tasks. After prioritizing the order, I'd gather the required materials and start working while ensuring that I maintain high quality.
If you have to shut down a machine for an unscheduled repair, what steps do you take to inform your team?
How to Answer
- 1
Immediately notify your supervisor about the machine shutdown.
- 2
Inform team members who operate adjacent machines.
- 3
Use a communication tool like a team chat or email for immediate alerts.
- 4
Document the reason for the shutdown and expected repair time for future reference.
- 5
Ensure that safety protocols are followed during the shutdown process.
Example Answers
I would first notify my supervisor and let them know about the reason for the shutdown. Then, I would inform my teammates who work with or around that machine. I'd send an alert through our team chat to ensure everyone is aware and also document the issue for later reference.
How would you resolve a disagreement with a supervisor regarding machine operation methods?
How to Answer
- 1
Listen carefully to the supervisor's perspective
- 2
Share your concerns respectfully without being confrontational
- 3
Provide evidence or reasoning for your method
- 4
Seek a compromise that maintains safety and efficiency
- 5
Be open to feedback and willing to learn from the discussion
Example Answers
I would first listen to my supervisor's reasoning on their method, then share my perspective by explaining my approach with supporting examples. If we still disagree, I'd propose a trial run of both methods to see which one yields better results.
You need to learn a new stamping technique that you are unfamiliar with. How would you approach this?
How to Answer
- 1
Research the new stamping technique online through videos and articles.
- 2
Ask experienced colleagues for tips and insights on the technique.
- 3
Request formal training sessions or demos from the equipment manufacturer.
- 4
Practice with the technique under supervision to build confidence.
- 5
Take notes on what works and any troubleshooting tips encountered.
Example Answers
I would start by researching the new technique online to understand its fundamentals. Then, I would reach out to my experienced colleagues to gather their insights. If possible, I'd arrange a training session to see the technique in action before practicing it myself.
Don't Just Read Stamping Machine Operator Questions - Practice Answering Them!
Reading helps, but actual practice is what gets you hired. Our AI feedback system helps you improve your Stamping Machine Operator interview answers in real-time.
Personalized feedback
Unlimited practice
Used by hundreds of successful candidates
Stamping Machine Operator Position Details
Recommended Job Boards
ZipRecruiter
www.ziprecruiter.com/Jobs/Stamping-OperatorThese job boards are ranked by relevance for this position.
Related Positions
Ace Your Next Interview!
Practice with AI feedback & get hired faster
Personalized feedback
Used by hundreds of successful candidates
Ace Your Next Interview!
Practice with AI feedback & get hired faster
Personalized feedback
Used by hundreds of successful candidates