Top 29 Machine Stamper Interview Questions and Answers [Updated 2025]
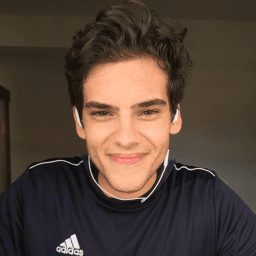
Andre Mendes
•
March 30, 2025
Preparing for a Machine Stamper interview can be daunting, but we’ve got you covered with the most common questions you’re likely to encounter. In this post, you'll find example answers and insightful tips to help you respond confidently and effectively. Whether you're a seasoned professional or new to the field, our guide is designed to equip you with the knowledge and strategies needed to succeed.
Download Machine Stamper Interview Questions in PDF
To make your preparation even more convenient, we've compiled all these top Machine Stamperinterview questions and answers into a handy PDF.
Click the button below to download the PDF and have easy access to these essential questions anytime, anywhere:
List of Machine Stamper Interview Questions
Behavioral Interview Questions
Can you describe a time when you identified a defect in the stamping process and how you addressed it?
How to Answer
- 1
Be specific about the defect you found
- 2
Explain the steps you took to investigate the issue
- 3
Describe the solution you implemented and its impact
- 4
Use metrics or outcomes if possible to quantify results
- 5
Highlight collaboration with team members if applicable
Example Answers
While working on a production line, I noticed that some stamped parts had inconsistent dimensions. I measured several samples and confirmed they were outside the tolerance range. I investigated the die alignment and found it was miscalibrated. After recalibrating the machine and performing quality checks, I was able to ensure all subsequent parts met specifications, reducing defects by 30%.
Give an example of a successful project you worked on as part of a team in a manufacturing environment.
How to Answer
- 1
Choose a specific project that had clear goals and outcomes
- 2
Describe your role and contributions to the team
- 3
Highlight the teamwork aspect and collaboration
- 4
Mention any challenges faced and how they were overcome
- 5
Discuss the positive impact or results of the project
Example Answers
In my last position, I worked on a project to improve the efficiency of our stamping process. My role was to analyze the workflow and propose changes. We collaborated with maintenance to implement a better preventive maintenance schedule, which reduced downtime by 20%. This teamwork resulted in a total output increase of 15%.
Don't Just Read Machine Stamper Questions - Practice Answering Them!
Reading helps, but actual practice is what gets you hired. Our AI feedback system helps you improve your Machine Stamper interview answers in real-time.
Personalized feedback
Unlimited practice
Used by hundreds of successful candidates
Describe a situation where you had to lead a team in resolving a production issue, what was your approach?
How to Answer
- 1
Choose a specific production issue you've faced.
- 2
Explain your role clearly in the team.
- 3
Detail the steps you took to analyze the problem.
- 4
Describe how you communicated and coordinated with the team.
- 5
Explain the outcome and lessons learned.
Example Answers
In my previous position, we faced a significant bottleneck in our assembly line due to a malfunction in the stamping machine. As the team lead, I organized a meeting to identify the issue and delegated tasks for troubleshooting. We quickly discovered the root cause was a misalignment in the equipment. I coordinated with our maintenance team to fix the issue, while keeping communication open with the production staff. We resolved the problem within two hours, minimizing downtime, and I learned the importance of swift team collaboration.
Tell me about a time when your attention to detail prevented a significant error in the stamping process.
How to Answer
- 1
Select a specific example from your experience.
- 2
Describe the situation and the potential error.
- 3
Explain the actions you took to fix or prevent the error.
- 4
Highlight the positive outcome resulting from your attention to detail.
- 5
Keep it concise and focused on your contribution.
Example Answers
In my previous role, I noticed that the measurements for stamp alignment were off before the production run. I double-checked the specifications and recalibrated the machine, preventing misaligned stamps. This saved us from a costly batch rejection and ensured product quality.
Have you ever had to adapt to a sudden change in production scheduling? How did you handle it?
How to Answer
- 1
Describe a specific situation where a change occurred.
- 2
Explain the impact of the change on production.
- 3
Detail the steps you took to adapt and mitigate any issues.
- 4
Mention any collaboration with coworkers or supervisors.
- 5
Highlight the positive outcome or lesson learned from the experience.
Example Answers
In my previous role, we received a last-minute order that conflicted with our production schedule. I quickly communicated with my team to prioritize the new order and reallocate resources. We held a brief meeting to reorganize our tasks, which allowed us to meet the customer's deadline, and we learned better flexibility in scheduling for the future.
What is a significant lesson you learned about stamping technology through your experience?
How to Answer
- 1
Reflect on a specific experience with stamping technology.
- 2
Mention a challenge you faced and how you addressed it.
- 3
Highlight the impact of the lesson on your work or team.
- 4
Be concise and focused on the lesson learned.
- 5
Relate the lesson to improving processes or outcomes in stamping.
Example Answers
I learned the importance of precision in stamping during a project where slight misalignment caused defects. By implementing a better alignment check, we reduced errors significantly.
Describe a time when you went above and beyond your duties as a machine stamper.
How to Answer
- 1
Select a specific example from your experience.
- 2
Focus on the impact of your actions on the team or production.
- 3
Use the STAR method: Situation, Task, Action, Result.
- 4
Emphasize teamwork or problem-solving skills.
- 5
Highlight any recognition received for your efforts.
Example Answers
In my previous role, we faced a tight deadline to fulfill a large order. I noticed our stamping machine was running low on calibrated dies. I took the initiative to work overtime to ensure all dies were calibrated and ready, which not only kept production on track but also helped the team meet the deadline without delays.
Technical Interview Questions
What types of stamping machines are you familiar with, and what specific experiences do you have operating them?
How to Answer
- 1
Identify specific types of stamping machines you have used, like mechanical, hydraulic, or pneumatic.
- 2
Discuss any brand names or models if relevant to the role.
- 3
Highlight your experience in settings such as factories or workshops.
- 4
Mention any relevant certifications or training you've completed.
- 5
Share a brief example of a project or task that illustrates your skills with these machines.
Example Answers
I am familiar with hydraulic stamping machines, particularly the XYZ model, which I operated for 3 years in a manufacturing plant. I was responsible for setting up the machine and ensuring quality control on the parts produced.
What different types of materials have you worked with during the stamping process?
How to Answer
- 1
List specific materials you have experience with
- 2
Mention any relevant techniques used with those materials
- 3
Highlight any specialized equipment used
- 4
Share challenges faced with different materials
- 5
Discuss any successful outcomes or projects that utilized those materials
Example Answers
I have worked primarily with aluminum and brass during the stamping process, employing both progressive and deep-draw stamping techniques. One project involved stamping aluminum for automotive components, where I fine-tuned the press settings to reduce material waste.
Don't Just Read Machine Stamper Questions - Practice Answering Them!
Reading helps, but actual practice is what gets you hired. Our AI feedback system helps you improve your Machine Stamper interview answers in real-time.
Personalized feedback
Unlimited practice
Used by hundreds of successful candidates
Explain the quality control methods you used in your previous stamping roles.
How to Answer
- 1
Start by identifying specific quality control methods you have experience with.
- 2
Mention any tools or equipment used for measuring quality.
- 3
Include how you documented quality control processes and results.
- 4
Discuss any team collaboration on quality assurance.
- 5
Provide examples of issues resolved through these methods.
Example Answers
In my previous role, I used statistical process control to monitor stamping processes and catch deviations early. I implemented regular checks using calipers and gauges to ensure dimensions were within tolerance. I documented all findings in a quality log and shared it with my team during our weekly meetings.
How do you perform routine maintenance on stamping machines to ensure their optimal performance?
How to Answer
- 1
Regularly check and replace worn parts like dies and punches.
- 2
Lubricate moving parts according to the manufacturer's specifications.
- 3
Inspect electrical connections and sensors for any signs of wear or damage.
- 4
Clean the machine regularly to remove dust and debris that can affect performance.
- 5
Keep detailed maintenance logs to track issues and repairs.
Example Answers
I perform maintenance by checking and replacing any worn dies and punches regularly, ensuring they are in optimal condition. I also lubricate the moving parts to keep them running smoothly and inspect the electrical connections for any issues.
Describe a technical improvement you've implemented in a stamping process and its impact.
How to Answer
- 1
Identify a specific stamping process that needed improvement.
- 2
Explain the technical change you made, including tools or techniques used.
- 3
Discuss the measurable impact of this change on productivity or quality.
- 4
Mention any collaboration with team members or departments.
- 5
Conclude with how this experience enhanced your technical skills or problem-solving ability.
Example Answers
In my previous role, I noticed a high defect rate due to die misalignment. I implemented a laser alignment system that ensured precise positioning of dies before stamping. This cut the defect rate by 30% and improved overall production efficiency, resulting in fewer reworks and lower material waste.
Can you detail the troubleshooting steps you follow when a stamping machine is not functioning correctly?
How to Answer
- 1
Start by identifying the specific issue the machine is exhibiting.
- 2
Check for error messages or indicators on the machine interface.
- 3
Inspect mechanical components for wear or blockage.
- 4
Examine electrical connections for loose or damaged wiring.
- 5
Test the machine's functions in a systematic way to isolate the problem.
Example Answers
When the stamping machine is not functioning, I first check the display for any error codes. If there are none, I inspect the mechanical parts for any signs of wear or obstruction. Next, I review the electrical connections to ensure they are secure and not damaged. Finally, I test the machine step by step to pinpoint where it fails.
What procedures do you follow to keep accurate documentation of the stamping process?
How to Answer
- 1
Use a standardized template for documenting each stamping job.
- 2
Record key parameters such as pressure, temperature, and material type.
- 3
Log any deviations from the standard process immediately.
- 4
Regularly review documentation for accuracy and completeness.
- 5
Ensure all team members are trained on proper documentation practices.
Example Answers
I use a standardized template to document each stamping job, recording details like pressure, temperature, and material. I log any deviations right away to maintain accuracy.
What experience do you have with programming CNC stamping machines?
How to Answer
- 1
Highlight specific CNC machines you have programmed
- 2
Mention relevant programming languages or software you used
- 3
Include any troubleshooting or optimization experiences
- 4
Talk about production outcomes or efficiency improvements achieved
- 5
If applicable, relate to any team collaboration or projects
Example Answers
I have programmed several CNC stamping machines, including the XYZ model. I primarily used G-code for programming and successfully optimized the settings to increase production speed by 15%.
What safety standards are important in the stamping industry, and how do you ensure compliance?
How to Answer
- 1
Identify key safety standards like OSHA and ISO 9001.
- 2
Discuss specific machine safety features and training protocols.
- 3
Mention the importance of PPE (personal protective equipment).
- 4
Explain how regular audits and inspections can ensure compliance.
- 5
Share an example of a safety procedure you've implemented.
Example Answers
In the stamping industry, key safety standards include OSHA regulations, which ensure worker safety, and ISO 9001 for quality management. I regularly conduct training sessions for staff on safe operating procedures and ensure PPE, like gloves and eye protection, is always available. We also perform weekly safety audits to maintain compliance and address any potential hazards.
How do you calibrate stamping machines to maintain product quality?
How to Answer
- 1
Regularly check the machine's alignment and leveling.
- 2
Use calibrated gauges to measure stamp depth and pressure.
- 3
Record and analyze output quality for consistency.
- 4
Adjust machine settings based on material type and specifications.
- 5
Conduct routine maintenance to prevent wear and tear.
Example Answers
I calibrate stamping machines by first ensuring they are level and aligned properly. Then, I use precise gauges to check the stamp's depth and pressure, making adjustments as necessary based on material specifications.
Don't Just Read Machine Stamper Questions - Practice Answering Them!
Reading helps, but actual practice is what gets you hired. Our AI feedback system helps you improve your Machine Stamper interview answers in real-time.
Personalized feedback
Unlimited practice
Used by hundreds of successful candidates
How do you use data analysis in your role as a machine stamper to improve processes?
How to Answer
- 1
Identify key metrics that impact stamping quality and efficiency.
- 2
Regularly collect data from machine outputs and downtime.
- 3
Analyze trends over time to pinpoint recurring issues.
- 4
Collaborate with team members to interpret data insights.
- 5
Implement small changes based on data findings and test their effects.
Example Answers
In my role, I track metrics like defect rates and machine uptime. By analyzing this data weekly, I can see patterns that indicate when the machine needs maintenance, which reduces downtime.
Situational Interview Questions
If a customer complained about the dimensions of stamped parts not meeting specifications, how would you respond?
How to Answer
- 1
Acknowledge the complaint promptly and show understanding of the issue.
- 2
Ask for specific details about the dimensions that are in question.
- 3
Review the production process to identify potential causes of the discrepancy.
- 4
Communicate openly with the customer about the steps being taken to resolve the issue.
- 5
Provide a timeline for resolution and follow up to ensure customer satisfaction.
Example Answers
I appreciate you bringing this to our attention. Can you provide the specific dimensions that are not meeting specifications? I will investigate our production process to find any issues and will keep you updated on our progress.
If you encounter a machine breakdown that halts production, what steps would you take to resolve the issue?
How to Answer
- 1
Immediately assess the situation to identify the cause of the breakdown.
- 2
Notify your supervisor and relevant team members about the issue.
- 3
Check the machine's manual for troubleshooting guidelines.
- 4
Attempt to reset or address the minor issues if safe to do so.
- 5
Document the incident and report any follow-up needs.
Example Answers
First, I would assess the machine to identify any obvious issues. Then, I would notify my supervisor and the maintenance team. I would consult the troubleshooting section of the manual. If it's safe, I might attempt a reset. Finally, I would document what happened for future reference.
Don't Just Read Machine Stamper Questions - Practice Answering Them!
Reading helps, but actual practice is what gets you hired. Our AI feedback system helps you improve your Machine Stamper interview answers in real-time.
Personalized feedback
Unlimited practice
Used by hundreds of successful candidates
If you notice a colleague violating safety protocols, how would you handle the situation?
How to Answer
- 1
Stay calm and assess the situation carefully.
- 2
Consider the severity of the violation and its impact on safety.
- 3
Approach your colleague diplomatically and express your concern.
- 4
If necessary, escalate the issue to a supervisor or safety officer.
- 5
Document the incident in case further action is required.
Example Answers
I would first assess the situation to understand the gravity of the safety violation. If it is serious, I would immediately speak to my colleague and explain why it's important to follow safety protocols. If they don't respond favorably, I would report it to my supervisor so that it can be addressed.
How would you prioritize your tasks if faced with a tight deadline for delivery of stamped parts?
How to Answer
- 1
Identify the most critical parts needed for delivery and assess their completeness.
- 2
Communicate with your team to understand their timelines and dependencies.
- 3
Break tasks into smaller, manageable steps to track progress effectively.
- 4
Use a priority matrix to categorize tasks by urgency and importance.
- 5
Stay flexible and adjust priorities as necessary based on real-time feedback.
Example Answers
I would first identify which stamped parts are most critical for the delivery and ensure those are completed first. I would communicate with my team and find out if any tasks depend on others and then break down my tasks into smaller steps, focusing on the most urgent ones.
If a new type of material causes unexpected issues in stamping, how would you address the situation?
How to Answer
- 1
Identify the specific issues caused by the material
- 2
Assess the stamping process parameters and adjust as necessary
- 3
Consider collaborating with the materials team for insights
- 4
Test different adjustments on a small scale before full implementation
- 5
Document findings and solutions for future reference
Example Answers
First, I would analyze the issues the new material is causing, such as misalignment or poor quality. Then, I would adjust the stamping parameters, like pressure and speed, and experiment with these changes on small batches. I would also engage with the materials team to understand better the properties of the new material.
How would you manage multiple stamping machines running simultaneously?
How to Answer
- 1
Prioritize tasks based on production schedule
- 2
Monitor each machine for performance and quality
- 3
Implement regular communication with operators
- 4
Use automation tools for tracking progress
- 5
Conduct periodic maintenance to prevent downtime
Example Answers
I would prioritize tasks based on the production schedule, monitoring each machine closely to ensure they meet quality standards. Regular communication with operators allows for quick adjustments and addressing any issues.
If you were in a disagreement with a coworker about a technical approach to stamping, how would you resolve it?
How to Answer
- 1
Listen actively to your coworker's perspective.
- 2
Present your own approach clearly and logically.
- 3
Find common ground and shared goals.
- 4
Suggest a trial period to test both methods.
- 5
Involve a supervisor if necessary to mediate.
Example Answers
I would start by listening to my coworker’s perspective to understand their reasoning. Then, I would clearly explain my approach, focusing on the benefits. We could agree on common goals for the stamping process and consider running a trial to evaluate both methods before making a final decision.
In the event of a hazardous material spill during the stamping process, what actions would you take?
How to Answer
- 1
Immediately alert your supervisor and the safety team.
- 2
Evacuate the area following the emergency protocols.
- 3
Identify the type of spill and refer to the Material Safety Data Sheet (MSDS).
- 4
Use personal protective equipment (PPE) to contain the spill if trained.
- 5
Follow the company’s spill response procedure to clean up safely.
Example Answers
I would first alert my supervisor and the safety team to ensure everyone is informed. Then, I would evacuate the area according to the emergency protocols to keep everyone safe. After that, I would try to identify the spill type and refer to the MSDS for guidance before proceeding.
How would you prepare for the introduction of advanced stamping technologies in your workplace?
How to Answer
- 1
Research the new stamping technologies thoroughly to understand their benefits and challenges
- 2
Assess the current skill levels of the team and identify training needs for new technologies
- 3
Develop a phased implementation plan that includes pilot testing and feedback loops
- 4
Collaborate with the technology providers for support and training materials
- 5
Establish metrics to evaluate the success of the integration of new technologies
Example Answers
To prepare for new stamping technologies, I would start by researching the specific technologies to grasp how they improve efficiency and product quality. I would then assess our team's current skill levels to identify any gaps and arrange necessary training sessions. Next, I would draft a phased implementation plan beginning with a pilot project to gather feedback before a full rollout. Collaboration with technology providers is key for support, and I would ensure we have metrics in place to measure the success of the new systems.
Machine Stamper Position Details
Recommended Job Boards
CareerBuilder
www.careerbuilder.com/jobs?keywords=Machine+StamperZipRecruiter
www.ziprecruiter.com/Jobs/-Machine-Stamper/These job boards are ranked by relevance for this position.
Related Positions
- Hand Stamper
- Machine Stapler
- Stamping Machine Operator
- Machine Printer
- Gold Stamper
- Stamp Pad Maker
- Machine Presser
- Punch Machine Operator
- Carbon Printer
- Bag Machine Operator
Similar positions you might be interested in.
Ace Your Next Interview!
Practice with AI feedback & get hired faster
Personalized feedback
Used by hundreds of successful candidates
Ace Your Next Interview!
Practice with AI feedback & get hired faster
Personalized feedback
Used by hundreds of successful candidates