Top 29 Machine Stapler Interview Questions and Answers [Updated 2025]
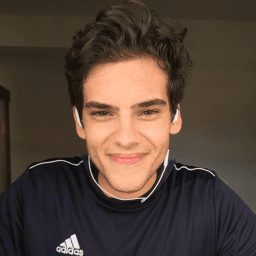
Andre Mendes
•
March 30, 2025
Navigating the interview process for a Machine Stapler role can be daunting, but preparation makes all the difference. In this blog post, we delve into the most common interview questions you might encounter, offering insightful example answers and practical tips to help you respond with confidence and clarity. Equip yourself with the knowledge to impress your interviewers and secure your next career opportunity.
Download Machine Stapler Interview Questions in PDF
To make your preparation even more convenient, we've compiled all these top Machine Staplerinterview questions and answers into a handy PDF.
Click the button below to download the PDF and have easy access to these essential questions anytime, anywhere:
List of Machine Stapler Interview Questions
Behavioral Interview Questions
Can you describe a time when you had to meet a tight deadline with your machine stapler?
How to Answer
- 1
Think of a specific instance where a deadline was critical.
- 2
Explain the task and what made the deadline tight.
- 3
Detail the steps you took to ensure timely completion.
- 4
Mention any challenges faced and how you overcame them.
- 5
Conclude with the outcome and what you learned from the experience.
Example Answers
At my previous job, we had a last-minute request to prepare 500 booklets for an event. I organized my time effectively, set up the machine stapler, and started working ahead of the delivery deadline. There were some paper jams, but I quickly fixed them and learned to clean the machine regularly. We met the deadline, and the event was a success.
Tell me about a time you collaborated with a team to improve stapling efficiency.
How to Answer
- 1
Choose a specific project where teamwork was key.
- 2
Explain the roles of team members and your contribution.
- 3
Describe a specific problem with stapling efficiency you identified.
- 4
Detail the solution your team implemented and your role in it.
- 5
Share the results and how they improved efficiency.
Example Answers
In my previous position, our team noticed that stapling efficiency dropped during peak hours. I suggested a scheduling rotation to ensure we had dedicated stapling specialists. We implemented a workflow adjustment, which reduced bottlenecks by 30%. Our team’s collaboration resulted in a smoother process throughout busy times.
Don't Just Read Machine Stapler Questions - Practice Answering Them!
Reading helps, but actual practice is what gets you hired. Our AI feedback system helps you improve your Machine Stapler interview answers in real-time.
Personalized feedback
Unlimited practice
Used by hundreds of successful candidates
Describe a situation where you encountered a mechanical issue with the stapler and how you resolved it.
How to Answer
- 1
Identify a specific mechanical issue you faced with the stapler.
- 2
Explain the steps you took to diagnose the problem.
- 3
Detail the solution you applied to fix the issue.
- 4
Mention any tools or resources you used during the process.
- 5
Conclude with the outcome and what you learned from the experience.
Example Answers
In my previous role, the stapler frequently jammed. I examined the mechanism and found that a small piece of paper was caught in it. I carefully removed the jam and lubricated the moving parts. After that, the stapler worked perfectly, improving the team's efficiency.
Give an example of a time when your attention to detail prevented a major error in production.
How to Answer
- 1
Think of a specific incident in your past roles.
- 2
Describe the context and your role in the situation.
- 3
Explain the mistake that was avoided due to your attention to detail.
- 4
Mention the outcome and its importance to production.
- 5
Keep it concise and focused on your contributions.
Example Answers
In my previous role as a machine operator, I noticed that the measurements on a batch of materials were off by a small margin. I double-checked the specifications and brought it to my supervisor's attention. This prevented a potentially costly production error and ensured the quality of the final product.
How did you handle a situation where you were under significant stress and still needed to operate the machine stapler effectively?
How to Answer
- 1
Stay calm and focused on the task at hand
- 2
Prioritize safety first to avoid accidents
- 3
Break down the job into manageable steps
- 4
Communicate with teammates, if applicable
- 5
Reflect on past experiences to boost confidence
Example Answers
In a busy production day, a machine malfunctioned and orders were piling up. I took a deep breath, ensured the equipment was safe to operate, and focused on completing one order at a time. By breaking it down, I managed to stay efficient and meet the deadline.
Can you tell me about a time you took the initiative to improve the stapling process?
How to Answer
- 1
Identify a specific challenge in the stapling process you observed.
- 2
Explain the initiative you took to address this challenge.
- 3
Describe the outcome of your initiative and how it benefited the process.
- 4
Use metrics if possible to show improvement.
- 5
Keep your answer focused and concise, ideally within a minute.
Example Answers
In my previous role, I noticed that stapling papers was taking too long because we were using an outdated stapler that often jammed. I researched and proposed the purchase of a high-capacity electric stapler. After implementing this, our stapling efficiency improved by 40%, allowing the team to focus more on other tasks.
Describe a time when you had to learn a new machine stapler or technology quickly. How did you ensure you understood it well?
How to Answer
- 1
Identify a specific instance where you learned quickly.
- 2
Explain the steps you took to familiarize yourself with the stapler.
- 3
Mention any resources you used, like manuals or training sessions.
- 4
Discuss how you practiced using the machine to gain confidence.
- 5
Conclude with the outcome or how your learning benefited your work.
Example Answers
At my last job, we received a new high-capacity stapler. I reviewed the manual thoroughly and watched a training video provided by the manufacturer. I practiced with scrap paper to get a feel for the settings. My ability to quickly adapt allowed my team to meet our production deadlines without delays.
Can you provide an example of feedback you received about your stapling work and how you acted on it?
How to Answer
- 1
Choose a specific instance of feedback you received.
- 2
Explain the context in which the feedback was given.
- 3
Describe the action you took in response to the feedback.
- 4
Highlight any positive outcomes from your actions.
- 5
Reflect on what you learned from the experience.
Example Answers
In my last role, my supervisor mentioned that my stapling was not consistently aligned. I took this feedback seriously and started measuring the margins before stapling. As a result, my stapling improved, and my team appreciated the better organization of documents.
Describe a personal goal you set in your role as a machine stapler operator and how you achieved it.
How to Answer
- 1
Choose a specific and measurable goal related to your work.
- 2
Explain the steps you took to achieve that goal.
- 3
Share any obstacles you faced and how you overcame them.
- 4
Emphasize the results and benefits of achieving this goal.
- 5
Connect the goal to your overall growth as an operator.
Example Answers
I aimed to increase my production rate by 20%. I tracked my output daily, identified slow points, and adjusted my technique. By refining my stapling method and organizing my workspace, I achieved this goal in three months, significantly boosting our team's efficiency.
Tell me about a time when you had to adapt to a significant change in your work environment related to stapling.
How to Answer
- 1
Think of a specific instance where a change occurred.
- 2
Describe what the change was and how it affected your work.
- 3
Explain the steps you took to adapt to the new situation.
- 4
Highlight any positive outcomes that resulted from your adaptability.
- 5
Keep it concise and relevant to stapling.
Example Answers
In my previous job, we switched to a new high-speed stapling machine that required different handling. I took the initiative to read the manual, attend training sessions, and practiced using it to become proficient. As a result, our team was able to increase our productivity by 20%.
Don't Just Read Machine Stapler Questions - Practice Answering Them!
Reading helps, but actual practice is what gets you hired. Our AI feedback system helps you improve your Machine Stapler interview answers in real-time.
Personalized feedback
Unlimited practice
Used by hundreds of successful candidates
Technical Interview Questions
What are the key components of a machine stapler, and how do they function together?
How to Answer
- 1
Identify the main components like the stapling mechanism, feed tray, and power source.
- 2
Explain how these components work together to staple effectively.
- 3
Use simple terminology to describe mechanical actions.
- 4
Consider mentioning safety features or user-friendly aspects.
- 5
Be ready to provide examples or scenarios where these components are crucial.
Example Answers
A machine stapler has several key components: the stapling head that drives the staple through the paper, a feed tray that holds the papers, and a power source that can be electric or manual. Together, they allow the stapler to securely bind multiple sheets efficiently.
How do you troubleshoot common problems that arise with a machine stapler?
How to Answer
- 1
Check for jammed staples and remove them carefully
- 2
Ensure the stapler is loaded with the correct staple size
- 3
Inspect the stapler for any misalignment or wear
- 4
Clean the machine, especially around the feeding mechanism
- 5
Test the stapler with different paper thicknesses to see if it functions properly
Example Answers
First, I would check for any jammed staples and clear them out. Then I would confirm that the stapler has the right staples loaded. If there's a misalignment, I'd inspect and adjust it as needed. Cleaning the parts that feed paper can also help solve issues. Finally, I would try stapling different paper thicknesses to ensure it works well.
Don't Just Read Machine Stapler Questions - Practice Answering Them!
Reading helps, but actual practice is what gets you hired. Our AI feedback system helps you improve your Machine Stapler interview answers in real-time.
Personalized feedback
Unlimited practice
Used by hundreds of successful candidates
What safety protocols do you follow when operating a machine stapler?
How to Answer
- 1
Always wear appropriate personal protective equipment like gloves and safety glasses.
- 2
Ensure the area around the machine is clear of any obstructions or unnecessary personnel.
- 3
Check that the machine is properly maintained and that safety guards are in place before use.
- 4
Never place hands near the stapling mechanism while the machine is in operation.
- 5
Follow the manufacturer's guidelines for operation and emergency procedures.
Example Answers
I always wear gloves and safety glasses when using the machine stapler. I also make sure the area is clear before starting, check the machine for safety guards, and follow the operational guidelines to ensure safety.
How do you configure a machine stapler for different types of paper or stapling jobs?
How to Answer
- 1
Identify the type of paper you are using and its thickness.
- 2
Adjust the stapler's depth and position settings according to the paper type.
- 3
Select the appropriate staple size for the thickness and number of sheets.
- 4
Test the setup with sample sheets to ensure proper stapling.
- 5
Make any additional adjustments for specific stapling jobs like corner or saddle stapling.
Example Answers
To configure a machine stapler, I first check the paper type and thickness. For instance, if I'm using a heavier cardstock, I adjust the depth settings to ensure the staple penetrates properly. I also select larger staples if I'm stapling more than a few sheets together and perform a test with a sample to confirm everything works smoothly.
What metrics do you use to measure the performance of the machine stapler?
How to Answer
- 1
Identify specific metrics like stapling speed and accuracy.
- 2
Consider the number of misfeeds or jams per hour.
- 3
Evaluate the quality of staples used and finished products.
- 4
Monitor the time taken for maintenance and downtimes.
- 5
Assess operator feedback on ease of use and reliability.
Example Answers
I measure performance using metrics such as the stapling speed, aiming for an average of 30 staples per minute, and tracking any jams or misfeeds that occur during that time.
What types of materials can be used in conjunction with a machine stapler, and what should be avoided?
How to Answer
- 1
Identify common materials like paper, cardboard, and thin plastic sheets that can be stapled.
- 2
Mention specific materials to avoid, such as thick materials over 30 sheets, and metal.
- 3
Discuss the importance of using the correct staple size for different materials.
- 4
Highlight the need to consider the stapler type, whether it's electric or manual.
- 5
Emphasize checking manufacturer guidelines for compatibility.
Example Answers
Machine staplers work well with standard paper, cardboard, and thin plastic folders. However, one should avoid using them on thick materials like a stack of more than 30 sheets or metal, as these can jam the stapler.
What strategies do you implement to maximize the speed of machine stapling without sacrificing quality?
How to Answer
- 1
Ensure the machine is properly maintained for optimal performance
- 2
Use high-quality staples that are designed for speed and reliability
- 3
Optimize the workflow by organizing materials for efficient access
- 4
Train operators to use the machine effectively and minimize downtime
- 5
Monitor stapling speed and quality regularly to identify areas for improvement
Example Answers
I focus on regular maintenance of the stapling machine to avoid jams, and I always use the best quality staples which enhance performance. I also make sure that the work area is organized to reduce delays.
How do you adjust the settings on a machine stapler for specialized stapling tasks?
How to Answer
- 1
Identify the type of materials you are stapling.
- 2
Check the thickness of the materials and adjust the stapler's depth settings accordingly.
- 3
Select the correct staple size for the task.
- 4
Adjust the pressure settings if your stapler has an automatic feature.
- 5
Consult the stapler's manual for specific adjustments for different applications.
Example Answers
I start by determining the type of materials I will be stapling, then I check their thickness to adjust the depth settings. I select the appropriate staple size and adjust the pressure settings if needed, following the guidelines in the manual.
What spare parts do you keep on hand for the machine stapler, and how do you decide which ones are necessary?
How to Answer
- 1
Identify commonly used parts such as stapler heads and pins
- 2
Consider factors like usage frequency and machine model
- 3
Keep a log of repairs and replacements to track needs
- 4
Consult the manufacturer's recommendations
- 5
Store parts in an organized manner for easy access
Example Answers
I keep staple heads, pins, and the drive blade on hand since these are the parts that wear out most due to regular use. I decide based on the frequency of breakdowns and the manufacturer's guidelines.
What routine maintenance tasks do you perform on a machine stapler to ensure it operates efficiently?
How to Answer
- 1
Check the staples regularly to ensure they're the correct size and type
- 2
Clean the stapler's feeding mechanism to prevent jams
- 3
Lubricate moving parts as per the manufacturer's recommendations
- 4
Inspect the power supply and electrical connections for wear or damage
- 5
Perform periodic calibration to maintain stapling accuracy
Example Answers
I regularly check the staples for compatibility and clean any debris from the feeding mechanism to avoid jams.
Don't Just Read Machine Stapler Questions - Practice Answering Them!
Reading helps, but actual practice is what gets you hired. Our AI feedback system helps you improve your Machine Stapler interview answers in real-time.
Personalized feedback
Unlimited practice
Used by hundreds of successful candidates
Situational Interview Questions
What would you do if the machine stapler suddenly broke down during a busy production run?
How to Answer
- 1
Stay calm and assess the situation quickly
- 2
Inform your supervisor about the breakdown immediately
- 3
Isolate the machine to ensure safety before troubleshooting
- 4
Identify the issue or error code displayed on the machine
- 5
Communicate with the team to manage production expectations
Example Answers
If the machine stapler breaks down, I would first stay calm and assess what has happened. I'd inform my supervisor right away to keep them in the loop. Then, I’d isolate the machine for safety and check for any error codes to diagnose the problem, all while keeping the team updated on our production status.
If you find that the machine stapler is not meeting production quotas, how would you approach the problem?
How to Answer
- 1
Identify any mechanical issues by inspecting the machine for wear and tear.
- 2
Check if the settings and calibrations are correct for the material being used.
- 3
Review the workflow and processes to find any inefficiencies or bottlenecks.
- 4
Gather feedback from operators to understand their challenges with the stapler.
- 5
Implement trial runs after adjustments to monitor if production improves.
Example Answers
I would first inspect the machine to check for any mechanical issues or wear that could affect performance. Then, I would evaluate the settings to ensure they match the requirements of the stapling job.
Don't Just Read Machine Stapler Questions - Practice Answering Them!
Reading helps, but actual practice is what gets you hired. Our AI feedback system helps you improve your Machine Stapler interview answers in real-time.
Personalized feedback
Unlimited practice
Used by hundreds of successful candidates
Imagine you are having a miscommunication with a team member regarding stapling specifications. How would you handle it?
How to Answer
- 1
Stay calm and listen to your team member's perspective
- 2
Ask clarifying questions to pinpoint the specific miscommunication
- 3
Clearly explain your understanding of the stapling specifications
- 4
Use visuals or examples if necessary to clarify your point
- 5
Follow up to ensure everyone is on the same page after the conversation
Example Answers
I would first listen to my team member to understand their viewpoint. Then, I would ask specific questions to figure out where the miscommunication happened. After that, I would explain my understanding of the stapling specifications clearly, maybe even share a diagram if needed. Finally, I would check with them later to confirm we both have the same understanding.
How would you manage a scenario where multiple team members need to use the stapler at the same time?
How to Answer
- 1
Assess the urgency of each request for the stapler
- 2
Implement a first-come, first-served system if possible
- 3
Suggest staggered usage times to avoid conflicts
- 4
Encourage teamwork by offering to help those in need
- 5
Ensure the stapler is accessible to everyone and check if additional staplers are needed
Example Answers
I would first gauge the urgency of each team member’s need for the stapler. Then, I would set up a first-come, first-served system so that everyone knows when they can use it.
If you notice that finished products stapled with the machine are not meeting quality standards, what steps would you take?
How to Answer
- 1
Identify the specific quality issues with the stapled products
- 2
Check the stapling machine settings for accuracy
- 3
Inspect the materials used for any defects or inconsistencies
- 4
Consult with team members or supervisors for additional insights
- 5
Document the findings and suggest improvements or adjustments
Example Answers
First, I would pinpoint the quality issues, such as loose staples or uneven stapling. Then, I would verify the machine settings and ensure they are correctly calibrated. Next, I would inspect the materials for any flaws that might be contributing to the problem. I would also discuss these findings with my team to gather additional input. Finally, I'd document everything and propose necessary adjustments based on the team's input.
How would you respond if a customer complained about improperly stapled documents that were sent out?
How to Answer
- 1
Acknowledge the customer's concern and apologize for the inconvenience
- 2
Gather details about the issue to understand what went wrong
- 3
Explain the steps you will take to resolve the issue
- 4
Assure the customer that corrective actions will be implemented to prevent future occurrences
- 5
Follow up with the customer to ensure their satisfaction after resolving the issue
Example Answers
I would start by apologizing to the customer for the mistake and understand the specifics of the issue. Then, I would assure them that I will address it immediately by re-stapling the documents and sending replacements if necessary. I'll also let them know we're reviewing our process to prevent this in the future.
If you had the opportunity to improve the design of the machine stapler, what changes would you suggest?
How to Answer
- 1
Consider ergonomics and user comfort in your suggestions.
- 2
Think about the materials used and their environmental impact.
- 3
Propose features that enhance functionality, like staples that can bind more pages.
- 4
Suggest improvements in the loading mechanism for ease of use.
- 5
Discuss durability and maintenance aspects for long-term use.
Example Answers
I would suggest using biodegradable materials for the stapler to reduce plastic waste and also include ergonomic grips for better handling.
What steps would you take if a safety incident occurred while you were operating the stapler?
How to Answer
- 1
Immediately stop the stapler to prevent further injury or damage.
- 2
Assess the situation to determine the severity of the incident.
- 3
Call for assistance or notify a supervisor if needed.
- 4
Follow established safety protocols for reporting the incident.
- 5
Ensure that everyone involved is safe and accounted for before resuming work.
Example Answers
I would stop the stapler immediately and assess whether anyone is injured. Then, I would notify my supervisor and follow any safety protocols for reporting.
Suppose a long-time customer expresses concern about the quality of stapling. How would you address their concerns?
How to Answer
- 1
Acknowledge the customer's concerns sincerely
- 2
Ask for specific details about their experience
- 3
Reassure them of your commitment to quality
- 4
Suggest ways to troubleshoot and improve the situation
- 5
Follow up to ensure their satisfaction after addressing the issue
Example Answers
I appreciate you bringing this up and I understand how important quality is. Could you share what specific issues you've noticed? I want to ensure we address this properly. I am committed to making this right and will follow up to ensure you're satisfied with the solution.
Machine Stapler Position Details
Related Positions
- Hand Stapler
- Machine Stamper
- Machine Presser
- Siding Stapler
- Bag Machine Operator
- Punch Machine Operator
- Stamping Machine Operator
- Machine Printer
- Paper Sorter
- Hand Stamper
Similar positions you might be interested in.
Ace Your Next Interview!
Practice with AI feedback & get hired faster
Personalized feedback
Used by hundreds of successful candidates
Ace Your Next Interview!
Practice with AI feedback & get hired faster
Personalized feedback
Used by hundreds of successful candidates