Top 31 Hand Stamper Interview Questions and Answers [Updated 2025]
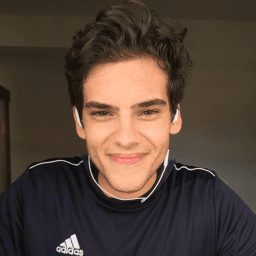
Andre Mendes
•
March 30, 2025
Preparing for a Hand Stamper interview? Our latest blog post is your go-to resource for mastering this unique role. We've compiled the most common interview questions and paired them with example answers and effective tips. Whether you're new to the field or looking to polish your skills, this guide will help you confidently tackle any question and make a lasting impression.
Download Hand Stamper Interview Questions in PDF
To make your preparation even more convenient, we've compiled all these top Hand Stamperinterview questions and answers into a handy PDF.
Click the button below to download the PDF and have easy access to these essential questions anytime, anywhere:
List of Hand Stamper Interview Questions
Behavioral Interview Questions
Can you describe a time when you worked closely with a team to achieve a goal as a Hand Stamper?
How to Answer
- 1
Identify a specific project where teamwork was essential.
- 2
Highlight your role and contributions in the team.
- 3
Mention the goal you were trying to achieve together.
- 4
Explain how you collaborated with others to overcome challenges.
- 5
Conclude with the results and what you learned from the experience.
Example Answers
In my previous position at XYZ Company, we had a target to stamp 10,000 parts in a week. As a hand stamper, I coordinated with two other team members to establish a workflow. We found that by dividing the parts based on complexity, we could meet our goal efficiently. Working together, we managed to not only meet but exceed our target by 15%. I learned the importance of clear communication and teamwork.
Tell me about a challenging stamping project you worked on and how you overcame the obstacles.
How to Answer
- 1
Identify a specific project with clear challenges and provide details.
- 2
Explain the obstacles you faced and the impact they had on the project.
- 3
Highlight the steps you took to overcome these challenges.
- 4
Conclude with the successful outcome and what you learned.
- 5
Keep your answer focused and relevant to the stamping process.
Example Answers
In a previous role, I worked on a stamping project for custom metal pieces. The challenge was aligning the dies correctly to avoid misprints. I overcame this by collaborating with the design team to create precise templates, and we conducted several test runs. As a result, we improved accuracy and met deadlines, leading to a successful product launch.
Don't Just Read Hand Stamper Questions - Practice Answering Them!
Reading helps, but actual practice is what gets you hired. Our AI feedback system helps you improve your Hand Stamper interview answers in real-time.
Personalized feedback
Unlimited practice
Used by hundreds of successful candidates
Give an example of a time when your attention to detail prevented a mistake in your stamping work.
How to Answer
- 1
Think of a specific incident related to stamping.
- 2
Describe the context where attention to detail was critical.
- 3
Explain the mistake that could have happened without your diligence.
- 4
Highlight the outcome of your attention to detail.
- 5
Keep it concise and focus on your actions.
Example Answers
During a production run, I noticed that the alignment of the stamping template was off. If I hadn't double-checked the alignment, it would have led to misprints on hundreds of units. My attention to detail ensured everything was correctly positioned, preventing a costly error.
Describe a situation where you had to communicate effectively with a client about their stamping needs.
How to Answer
- 1
Identify the client's specific stamping needs.
- 2
Explain how you clarified those needs through questions.
- 3
Discuss how you presented solutions based on their requirements.
- 4
Mention any feedback you received from the client.
- 5
Emphasize the importance of establishing a good rapport.
Example Answers
In my previous role, I had a client who needed custom stamps for their business. I scheduled a meeting to ask detailed questions about their branding and preferences. After understanding their needs, I proposed several design options. The client appreciated my attentive approach and was pleased with the final product.
How have you managed tight deadlines in a previous stamping project?
How to Answer
- 1
Identify a specific project with a deadline challenge.
- 2
Explain the steps you took to prioritize tasks.
- 3
Mention any tools or methods you used to stay organized.
- 4
Describe how you communicated with your team or clients.
- 5
Highlight any results or outcomes from your efforts.
Example Answers
In a recent stamping project with a tight deadline, I prioritized tasks by creating a timeline. I used project management software to track progress and ensured my team was aware of their responsibilities. We communicated daily to address any roadblocks. As a result, we completed the project on time and received positive feedback from our client.
What motivates you to produce high-quality stamping work?
How to Answer
- 1
Emphasize personal pride in craftsmanship
- 2
Mention the importance of precision in stamping
- 3
Discuss commitment to meeting quality standards
- 4
Share how quality work impacts the team and company
- 5
Reflect on past experiences that drive your motivation
Example Answers
I take personal pride in every stamp I create. Knowing that my work contributes to a high-quality product motivates me to always improve my craft.
Can you discuss a time when you learned a new stamping technique or skill?
How to Answer
- 1
Choose a specific stamping technique you learned.
- 2
Explain the context and why you needed to learn it.
- 3
Describe the process of learning the technique step-by-step.
- 4
Share the outcome or results of using this new skill.
- 5
Reflect on how this experience improved your stamping skills.
Example Answers
I learned a new foil stamping technique when completing a project for a client who wanted a more luxurious finish. I researched online tutorials, practiced on scrap materials, and eventually achieved a great look on their final products. The client loved it, which boosted my confidence in using this technique.
Have you ever taken the lead on a stamping project? What was the outcome?
How to Answer
- 1
Think of a specific project where you led stamping operations.
- 2
Outline your responsibilities and the steps you took to lead the project.
- 3
Mention the outcomes and any measurable successes.
- 4
Highlight teamwork and collaboration aspects if applicable.
- 5
Be honest about challenges faced and how you overcame them.
Example Answers
In my previous role, I led a project to implement a new stamping line for a product launch. I coordinated with the engineering team to ensure the machinery was calibrated correctly, and we met our production goals, resulting in a successful launch that exceeded sales projections by 20%.
Describe how you have responded to constructive feedback on your stamping work.
How to Answer
- 1
Acknowledge the feedback positively
- 2
Provide a specific example of feedback you received
- 3
Explain the steps you took to improve based on the feedback
- 4
Share the results or improvements after applying the feedback
- 5
Express appreciation for the opportunity to learn
Example Answers
In my previous position, I received feedback about my stamping alignment being slightly off. I took the feedback positively and focused on better positioning. After adjusting my technique, my alignment was consistently within the required specifications, leading to a decrease in rework.
Don't Just Read Hand Stamper Questions - Practice Answering Them!
Reading helps, but actual practice is what gets you hired. Our AI feedback system helps you improve your Hand Stamper interview answers in real-time.
Personalized feedback
Unlimited practice
Used by hundreds of successful candidates
Can you recall a time when you had to stand by your decision regarding a stamping design?
How to Answer
- 1
Choose a specific experience where your design choice faced challenge.
- 2
Explain the reasoning behind your design and its importance.
- 3
Describe how you communicated your decision to the team or clients.
- 4
Highlight the positive outcome or learning from the situation.
- 5
Keep the focus on your commitment and professionalism.
Example Answers
In a recent project, I designed a custom stamp for a client. After presenting the design, the client suggested changes that I felt compromised the original concept. I stood by my decision, explaining how the design aligned with their brand values. Ultimately, they appreciated my expertise and went with my design, which received positive feedback.
Technical Interview Questions
What techniques do you use to ensure that each stamp impression is consistent and of high quality?
How to Answer
- 1
Regularly clean the stamp to avoid ink build-up.
- 2
Use consistent pressure when applying the stamp.
- 3
Align the stamp properly with the surface before pressing down.
- 4
Test the stamp on scrap material before using it on final products.
- 5
Check the ink level and consistency before starting large batches.
Example Answers
I ensure consistency by cleaning the stamp regularly to prevent any ink build-up. I also apply the same amount of pressure every time I stamp to achieve uniformity.
What types of materials have you worked with for stamping, and how do they affect the final result?
How to Answer
- 1
Identify the specific materials you have used such as metals, plastics, or paper.
- 2
Explain how each material influences ink adhesion, texture, and overall appearance.
- 3
Mention any past experiences or projects where you learned about these effects.
- 4
Discuss any challenges you faced with certain materials and how you overcame them.
- 5
Be ready to tie your experience back to how it relates to the job you're applying for.
Example Answers
I have worked primarily with metal and plastic for stamping. For instance, metal surfaces tend to yield sharper impressions, enhancing detail, while plastic can sometimes lead to smudging due to its smooth surface. In my last project, I had to adjust the ink choice for plastic to improve adhesion.
Don't Just Read Hand Stamper Questions - Practice Answering Them!
Reading helps, but actual practice is what gets you hired. Our AI feedback system helps you improve your Hand Stamper interview answers in real-time.
Personalized feedback
Unlimited practice
Used by hundreds of successful candidates
Describe your experience with different types of stamping equipment and their maintenance.
How to Answer
- 1
Identify specific types of stamping equipment you have used
- 2
Mention any maintenance routines you followed regularly
- 3
Highlight any repairs or troubleshooting you performed
- 4
Discuss how you kept the equipment clean and operational
- 5
Relate your experience to any safety protocols you adhered to
Example Answers
I have experience using both manual and hydraulic stampers. I followed a strict maintenance routine that included daily cleaning, lubrication, and checking for wear and tear. I also handled minor repairs like replacing springs and adjustments to ensure optimal performance.
How do you approach the design process for new stamp impressions?
How to Answer
- 1
Begin with understanding the client’s requirements and brand identity.
- 2
Research current design trends and effective stamp styles.
- 3
Sketch initial ideas focusing on simplicity and clarity.
- 4
Iterate designs based on feedback and practical stamping tests.
- 5
Finalize the design ensuring scalability and compatibility with materials.
Example Answers
I start by gathering client requirements to understand their brand. Then, I research current trends to find inspiration. I create initial sketches, focusing on clean and clear designs, and I test them out to see how they stamp. After gathering feedback, I refine my designs before finalizing.
How do you troubleshoot issues that arise during the stamping process?
How to Answer
- 1
Observe the process carefully to identify where the issue occurs.
- 2
Check the materials and equipment for any obvious defects or misalignments.
- 3
Consult the operational manual for troubleshooting guidelines specific to the equipment.
- 4
Document the problem and your steps to resolve it for reference in the future.
- 5
Collaborate with team members if the issue persists, to gather different perspectives.
Example Answers
I first observe the stamping process to pinpoint where the issue occurs, such as misalignment. Then, I check the materials for defects or misalignments, and refer to the manual for troubleshooting tips. If the issue continues, I document what I've done and seek input from my coworkers.
What finishing techniques do you apply after stamping to enhance the final product?
How to Answer
- 1
Mention specific techniques like polishing or coating.
- 2
Discuss how those techniques improve appearance or durability.
- 3
Include any personal experience or success story with these techniques.
- 4
Emphasize the importance of quality control in the finishing process.
- 5
Be prepared to explain the materials or tools used.
Example Answers
I typically apply polishing after stamping to enhance the shine of the stamped surface. This not only improves the aesthetic appeal but also helps in preventing rust.
How do you ensure proper color application in your stamped products?
How to Answer
- 1
Choose high-quality ink that matches the material being stamped.
- 2
Test colors on a sample before final application to ensure accuracy.
- 3
Use the correct amount of ink on the stamp to avoid bleeding.
- 4
Adjust pressure and speed of stamping for consistent results.
- 5
Regularly clean stamps to prevent color contamination.
Example Answers
I start by selecting the right ink for the material. Before I stamp the final product, I always do a test stamp to check the color. Ensuring I use the correct amount of ink prevents any bleeding, and I adjust my pressure and speed based on the material for the best results.
What strategies do you implement to improve the efficiency of your stamping workflow?
How to Answer
- 1
Assess and map out the current stamping process to identify bottlenecks
- 2
Invest time in training and cross-training team members for optimal role flexibility
- 3
Maintain and regularly calibrate stamping equipment to ensure it runs smoothly
- 4
Implement a system for tracking and measuring workflow data to spot inefficiencies
- 5
Encourage open communication among the team to share insights and suggestions
Example Answers
I start by mapping out each step of the stamping process to find bottlenecks. Then, I focus on cross-training team members so they can step in where needed, which helps keep the workflow moving efficiently.
What design software or tools have you used to create stamp designs?
How to Answer
- 1
List specific design software you are familiar with
- 2
Mention tools you use for creating or modifying designs
- 3
Explain how you've used these tools in past projects
- 4
Highlight any relevant experience with hand stamping techniques
- 5
Emphasize your ability to learn new software quickly if needed
Example Answers
I have experience using Adobe Illustrator for creating intricate stamp designs. I also use Photoshop to modify images and prepare them for stamping. In my last project, I designed floral stamps using these tools and ensured they were production-ready.
Situational Interview Questions
If you notice a defect in a batch of stamped products, how would you handle the situation?
How to Answer
- 1
Identify the specific defect clearly and document it.
- 2
Stop the stamping process to prevent further defective products.
- 3
Notify your supervisor or quality control team immediately.
- 4
Assess the cause of the defect if possible.
- 5
Implement corrective actions or follow procedures to resolve the issue.
Example Answers
I would first document the specifics of the defect I noticed. Then, I would stop the stamping process to avoid producing more defects. After that, I would inform my supervisor about the situation and any observations I have regarding the cause.
Imagine a client is unhappy with the stamps you created for them. How would you address their concerns?
How to Answer
- 1
Listen carefully to the client's feedback without interrupting.
- 2
Acknowledge the client's feelings and validate their concerns.
- 3
Ask clarifying questions to fully understand their dissatisfaction.
- 4
Offer solutions, such as adjustments or replacements, to rectify the issue.
- 5
Follow up with the client to ensure their satisfaction after addressing their concerns.
Example Answers
I would first listen to the client and let them express their concerns fully. Then, I would acknowledge their feelings and assure them that I want to resolve the issue. I would ask questions to clarify what specifically didn't meet their expectations and then offer to make adjustments or create new stamps to fit their needs. Finally, I'd follow up after the changes to ensure they are satisfied.
Don't Just Read Hand Stamper Questions - Practice Answering Them!
Reading helps, but actual practice is what gets you hired. Our AI feedback system helps you improve your Hand Stamper interview answers in real-time.
Personalized feedback
Unlimited practice
Used by hundreds of successful candidates
If assigned multiple stamping projects with tight deadlines, how would you prioritize your work?
How to Answer
- 1
List projects by deadline to see which are most urgent
- 2
Assess the complexity of each project to understand time required
- 3
Communicate with your team to coordinate on overlapping tasks
- 4
Focus on high-impact projects that deliver the most value
- 5
Remain flexible and adjust priorities as needed based on new information
Example Answers
I would start by listing all the projects by their deadlines to identify which ones are most urgent. Then, I would evaluate the complexity of each to determine how much time I need for each task. I would communicate with my team to ensure we are not duplicating efforts and would focus on projects that are critical to our goals.
Suppose you were asked to incorporate new design techniques into your stamping process. How would you approach this task?
How to Answer
- 1
Research recent stamping design techniques relevant to your work
- 2
Consider the materials and technology available in your workplace
- 3
Collaborate with team members to gather input and ideas
- 4
Test new techniques on a small scale to evaluate effectiveness
- 5
Document the process and results for future reference
Example Answers
I would start by researching the latest design techniques that are applicable to our stamping process. After identifying promising techniques, I would collaborate with my team to discuss feasibility. Testing on a small scale would allow us to assess the effectiveness of these new methods before implementing them fully.
What actions would you take if you observed unsafe practices in the stamping workshop?
How to Answer
- 1
Identify the unsafe practice clearly and calmly.
- 2
Report the unsafe practice to a supervisor or safety officer immediately.
- 3
Encourage affected colleagues to stop any work that may be dangerous.
- 4
Follow up to ensure corrective actions are taken to improve safety.
- 5
Document the unsafe practice and the steps you took to address it.
Example Answers
If I see unsafe practices, I will first identify the specific issue. Then, I would promptly report it to my supervisor to ensure it is addressed. I would also encourage my teammates to pause any unsafe work until the problem is resolved.
How would you deal with a colleague who disagrees with your approach to a stamping project?
How to Answer
- 1
Listen carefully to their concerns about your approach
- 2
Acknowledge their viewpoint and show respect for their opinion
- 3
Explain your reasoning clearly and provide evidence for your approach
- 4
Look for common ground to find a compromise or solution
- 5
Suggest a trial period for both approaches to gather results
Example Answers
I would start by listening to my colleague's concerns and making sure I understand their viewpoint. Then, I would explain my approach and share any data or experiences that support it. If there's still disagreement, I would propose a trial of both methods to see which one yields better results.
If you run out of an essential material while working on a project, what steps would you take?
How to Answer
- 1
Assess the situation to determine the impact of running out of the material.
- 2
Identify potential alternatives or substitutes that can be used temporarily.
- 3
Communicate with your supervisor or team about the issue as soon as possible.
- 4
Check inventory or suppliers for quick restocking options if alternatives are not available.
- 5
Plan the next steps based on the urgency and importance of the project.
Example Answers
I would first assess how critical the missing material is to the project. If it's urgent, I would look for alternatives or substitutes that could work. Then, I would inform my supervisor of the situation and request additional materials from our supplier, ensuring minimal disruption to the project timeline.
What would you do if a customer requested a design modification after you completed the stamping?
How to Answer
- 1
Listen carefully to the customer's request and understand their needs.
- 2
Apologize for any inconvenience and show willingness to help.
- 3
Assess if the modification can be done and explain the process clearly.
- 4
Provide the customer with options and timelines for the modification.
- 5
Confirm the final design with the customer before making changes.
Example Answers
I would first listen to the customer's request carefully to understand exactly what they want. I would apologize for any inconvenience and assure them I am happy to help. Then I would evaluate if the modification is feasible and explain how we can make it happen, including any timeline required.
What would be your immediate response if your stamping equipment fails during a critical job?
How to Answer
- 1
Stay calm and assess the situation quickly.
- 2
Communicate immediately with your supervisor or team about the issue.
- 3
Check for any quick fixes or reset options on the equipment.
- 4
Prepare an alternative plan to minimize downtime.
- 5
Document the issue and report it for future reference.
Example Answers
If my stamping equipment fails, I would first remain calm and quickly assess the problem. I would inform my supervisor right away, check if I can resolve it with any quick fixes, and if not, I would shift to an alternative stamping method to ensure we meet our deadlines.
If a project deadline is moved up unexpectedly, how would you adjust your schedule?
How to Answer
- 1
Identify critical tasks that must be completed first.
- 2
Assess available resources and seek help if necessary.
- 3
Break down larger tasks into smaller, manageable parts.
- 4
Communicate with your team about the changes and plan together.
- 5
Stay flexible and adjust priorities as needed.
Example Answers
I would first identify the critical tasks due by the updated deadline and prioritize them. Then, I would assess my workload and, if needed, request assistance from colleagues to ensure we meet the deadline.
Don't Just Read Hand Stamper Questions - Practice Answering Them!
Reading helps, but actual practice is what gets you hired. Our AI feedback system helps you improve your Hand Stamper interview answers in real-time.
Personalized feedback
Unlimited practice
Used by hundreds of successful candidates
Hand Stamper Position Details
Related Positions
- Machine Stamper
- Hand Stapler
- Gold Stamper
- Hand Paster
- Hand Tapper
- Punch Hand
- Hand Marker
- Stamping Machine Operator
- Stamp Pad Maker
- Hand Riveter
Similar positions you might be interested in.
Ace Your Next Interview!
Practice with AI feedback & get hired faster
Personalized feedback
Used by hundreds of successful candidates
Ace Your Next Interview!
Practice with AI feedback & get hired faster
Personalized feedback
Used by hundreds of successful candidates