Top 31 Stamp Pad Maker Interview Questions and Answers [Updated 2025]
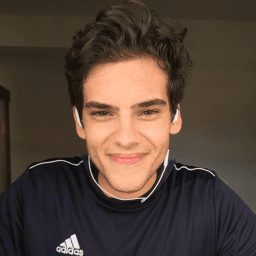
Andre Mendes
•
March 30, 2025
Preparing for a Stamp Pad Maker interview? Our latest blog post has you covered with the most common questions interviewers ask in this role. Dive into expertly crafted example answers and gain valuable tips on how to respond effectively, setting yourself up for success. Whether you're a seasoned professional or new to the field, this guide will help you confidently navigate your interview.
Download Stamp Pad Maker Interview Questions in PDF
To make your preparation even more convenient, we've compiled all these top Stamp Pad Makerinterview questions and answers into a handy PDF.
Click the button below to download the PDF and have easy access to these essential questions anytime, anywhere:
List of Stamp Pad Maker Interview Questions
Behavioral Interview Questions
Can you describe a challenging project you worked on as a Stamp Pad Maker and how you overcame the difficulties?
How to Answer
- 1
Identify a specific project that posed significant challenges.
- 2
Describe the difficulties clearly, focusing on technical or teamwork issues.
- 3
Explain the steps you took to address these challenges.
- 4
Highlight the skills you used and what you learned from the experience.
- 5
Conclude with a positive outcome resulting from your efforts.
Example Answers
In a recent project, we had an unexpected shortage of a specific ink color for our stamp pads. I coordinated with suppliers to expedite the delivery, meanwhile, we experimented with alternative colors that could still meet the client's needs. This kept the project on track and ultimately led to a satisfied customer.
Give an example of a time when you had to collaborate with others to achieve a deadline in production.
How to Answer
- 1
Identify a specific project where teamwork was essential.
- 2
Explain your role and the contributions of your team.
- 3
Focus on the challenges you faced and how collaboration helped overcome them.
- 4
Mention any tools or methods you used to facilitate communication.
- 5
Conclude with the outcome and what you learned from the experience.
Example Answers
During a recent project, our team was tasked with producing a large order of custom stamp pads within a tight deadline. I coordinated with the design and production teams to ensure everyone had clear specifications. We held daily check-ins to track progress and address any issues. As a result, we delivered the order a day early, and our customer was very pleased with the quality.
Don't Just Read Stamp Pad Maker Questions - Practice Answering Them!
Reading helps, but actual practice is what gets you hired. Our AI feedback system helps you improve your Stamp Pad Maker interview answers in real-time.
Personalized feedback
Unlimited practice
Used by hundreds of successful candidates
Tell me about a time when you noticed quality issues in your work. What steps did you take to address them?
How to Answer
- 1
Describe the specific quality issue you identified
- 2
Explain the impact of the issue on the product or team
- 3
Detail the steps you took to investigate and resolve the issue
- 4
Discuss any changes implemented to prevent future issues
- 5
Highlight the positive outcome from your actions
Example Answers
In my previous role, I noticed that some stamp pads were leaking ink. This could impact customer satisfaction. I immediately reported the issue to my supervisor and we conducted a review of the production process. We discovered that a specific machine was malfunctioning. I recommended regular maintenance checks and we implemented a new quality control step which reduced defects by 30%. Customers praised the improved quality.
Describe a situation where you had to learn a new technique or technology quickly. How did you manage?
How to Answer
- 1
Identify a specific situation that showcases your ability to learn quickly
- 2
Explain the context and what you needed to learn
- 3
Detail the steps you took to learn the new technique or technology
- 4
Highlight any resources or methods you used for learning
- 5
Conclude with the result or outcome of your learning process
Example Answers
In my previous job as a graphic designer, I was tasked with using a new design software on short notice. I dedicated a weekend to online tutorials and practiced using the software. I also reached out to a colleague who was experienced with the tool. By Monday, I felt confident enough to complete a project using it, and I received positive feedback on my work.
Have you ever dealt with a difficult client regarding a custom stamp pad order? How did you handle the situation?
How to Answer
- 1
Listen carefully to the client's concerns.
- 2
Acknowledge their feelings and frustrations.
- 3
Offer solutions or alternatives to resolve their issue.
- 4
Follow up after the resolution to ensure satisfaction.
- 5
Remain professional and patient throughout the interaction.
Example Answers
Yes, I once had a client who was unhappy with the color of their custom stamp pad. I listened to their concerns and acknowledged their frustration. I offered to create a new pad in a different color that matched their expectations, and they appreciated the prompt response.
Describe how you manage your time while juggling multiple stamp pad orders with varying deadlines.
How to Answer
- 1
Prioritize tasks based on deadlines and complexity.
- 2
Create a detailed schedule or timeline for each order.
- 3
Break down larger tasks into smaller, manageable steps.
- 4
Use a checklist to track progress and ensure quality.
- 5
Communicate regularly with customers about their order status.
Example Answers
I prioritize my stamp pad orders by their deadlines and complexity. For instance, if I have a large order due soon, I focus on that first while scheduling less urgent orders around it. I keep a checklist and update it daily to stay on track.
Can you think of a time when you received constructive criticism on your work? How did you respond?
How to Answer
- 1
Choose a specific example of constructive criticism you received.
- 2
Explain the context of the feedback clearly and concisely.
- 3
Describe how you accepted the feedback professionally.
- 4
Detail the steps you took to improve based on the criticism.
- 5
Mention the positive outcome or what you learned from the experience.
Example Answers
In my previous role as a production assistant, my supervisor pointed out that my color mixing for stamp pads was inconsistent. I listened carefully to her feedback and asked for clarification on best practices. I then practiced color mixing on my own time and sought feedback again. As a result, my mixes became much more consistent, and I was able to assist in producing a new line of stamp pads that received positive feedback from customers.
Describe a project where you had to track progress and manage resources efficiently.
How to Answer
- 1
Focus on a specific project related to manufacturing or production management.
- 2
Mention the tools or methods you used for tracking progress, such as Gantt charts or project management software.
- 3
Highlight how you managed resources, including budgeting and personnel allocation.
- 4
Include measurable outcomes to demonstrate efficiency and success.
- 5
Explain any challenges faced and how you overcame them.
Example Answers
In a recent project to develop a new line of stamp pads, I used a Gantt chart to track milestones and deadlines. I allocated resources effectively by assigning team members based on their strengths and ensured we stayed under budget by regularly reviewing our expenditures.
What motivated you to become a Stamp Pad Maker and what do you enjoy most about it?
How to Answer
- 1
Think about your passion for crafting and design in your answer
- 2
Mention specific skills you use as a Stamp Pad Maker
- 3
Share a personal story or experience that inspired you
- 4
Highlight the satisfaction of seeing your products used by customers
- 5
Emphasize the creative aspects of making unique stamp pads
Example Answers
I’ve always loved arts and crafts, which drew me to become a Stamp Pad Maker. I find joy in designing unique stamp pads that artists can use. A memorable moment was creating a custom pad for a local artist, and seeing their excitement when they received it fueled my passion further.
Don't Just Read Stamp Pad Maker Questions - Practice Answering Them!
Reading helps, but actual practice is what gets you hired. Our AI feedback system helps you improve your Stamp Pad Maker interview answers in real-time.
Personalized feedback
Unlimited practice
Used by hundreds of successful candidates
Technical Interview Questions
What machinery or tools do you regularly use in the stamp pad making process and how do you maintain them?
How to Answer
- 1
Identify the key machinery and tools involved in stamp pad making.
- 2
Explain the maintenance routines for each piece of equipment.
- 3
Mention any troubleshooting practices you follow.
- 4
Highlight the importance of cleanliness and safety in tool maintenance.
- 5
Be specific about how you ensure optimal performance of the tools.
Example Answers
I regularly use a hydraulic press for stamping and a cutting machine for sizing. I maintain these by cleaning them after each use, lubricating moving parts weekly, and checking for any wear and tear monthly.
What types of materials do you consider when creating a stamp pad and why?
How to Answer
- 1
Identify key materials such as foam, felt, and rubber.
- 2
Explain the importance of ink absorption and longevity.
- 3
Discuss surface benefits like smoothness and durability.
- 4
Mention environmental considerations or non-toxic materials.
- 5
Link material properties to the end user's experience.
Example Answers
I consider materials like foam and felt for their absorbency, which is crucial for ensuring even ink distribution. Using durable surfaces helps the stamp resist wear over time and provides a smooth stamping experience.
Don't Just Read Stamp Pad Maker Questions - Practice Answering Them!
Reading helps, but actual practice is what gets you hired. Our AI feedback system helps you improve your Stamp Pad Maker interview answers in real-time.
Personalized feedback
Unlimited practice
Used by hundreds of successful candidates
Walk us through the step-by-step process of how you create a stamp pad from start to finish.
How to Answer
- 1
Start with selecting the materials needed like felt, ink, and the casing.
- 2
Describe the preparation of the casing and layering the felt inside.
- 3
Explain how to apply the ink evenly to the felt without over-saturating.
- 4
Mention the importance of allowing the ink to absorb and settle.
- 5
Finish with sealing the stamp pad to ensure freshness and usability.
Example Answers
First, I gather my materials, including a plastic casing, felt pads, and ink. Next, I prepare the casing by ensuring it is clean and ready for assembly. I then cut the felt to fit snugly inside the casing and layer it. After that, I apply the ink evenly to the felt, making sure not to over-saturate it. Lastly, I let the ink absorb for a few minutes and seal the casing tightly.
What common issues have you encountered while making stamp pads and how did you resolve them?
How to Answer
- 1
Identify specific problems you faced during the stamp pad creation process
- 2
Explain the impact these issues had on production or quality
- 3
Describe the steps you took to diagnose and resolve each issue
- 4
Highlight any tools or techniques that were particularly effective
- 5
Emphasize the lessons learned and how they improved your future work
Example Answers
One common issue I encountered was the ink not evenly distributing across the pad. To resolve this, I adjusted the amount of ink applied and used a roller to ensure uniform coverage, which improved the quality of the stamps.
How do you ensure the design of a stamp pad meets client specifications and expectations?
How to Answer
- 1
Communicate clearly with the client to understand their needs
- 2
Review and confirm specifications before starting the design
- 3
Use prototyping to create a model of the stamp pad
- 4
Gather feedback from the client on the prototype
- 5
Make adjustments based on client feedback before final production
Example Answers
I start by having a detailed conversation with the client to clarify their requirements. Once I understand their expectations, I draft a design and send it for their approval. I then build a prototype and request their feedback to ensure it aligns with what they envisioned.
What types of ink do you most often use for stamp pads and what factors influence your choice?
How to Answer
- 1
Identify different types of ink like dye-based, pigment-based, and solvent-based.
- 2
Consider the purpose of the stamps—whether for crafting, office use, or art.
- 3
Mention factors such as drying time, durability, and surface compatibility.
- 4
Explain how environmental considerations, like non-toxicity, may influence your choice.
- 5
Be ready to discuss any personal experiences with specific brands or types.
Example Answers
I often use dye-based ink for crafting because it dries quickly and produces vibrant colors. For office stamps, I prefer pigment-based ink as it's more fade-resistant and suitable for various surfaces.
How do you approach creating a custom stamp pad for a client with unique requirements?
How to Answer
- 1
Start by understanding the client's specific needs and preferences.
- 2
Ask questions to clarify the intended use and design for the stamp pad.
- 3
Discuss material options based on durability and ink compatibility.
- 4
Show examples of previous custom designs to inspire and guide the client.
- 5
Confirm the timeline and budget before proceeding with the creation.
Example Answers
I begin by having a detailed conversation with the client to understand their specific requirements, including the design and intended use. I then discuss various materials that would work best for their custom stamp pad, showing them examples of past work to ensure we’re on the same page. Finally, I confirm the timeline and budget before starting the project.
What methods do you use to test stamp pads for durability and quality before final delivery?
How to Answer
- 1
Describe specific tests you conduct for ink absorption.
- 2
Mention any longevity tests like drying time and fade resistance.
- 3
Explain your quality assurance process and how you document findings.
- 4
Discuss any feedback mechanisms for continuously improving pad quality.
- 5
Highlight collaboration with teams for comprehensive quality checks.
Example Answers
I perform ink absorption tests by applying the ink to a sample paper and measuring the time it takes to dry and the extent of seepage. Additionally, I conduct fade resistance tests by exposing the stamp pads to light and moisture to ensure they maintain color and quality.
What techniques do you use for mixing colors in ink for custom stamp pads?
How to Answer
- 1
Understand the color wheel and complementary colors to create visually appealing mixes.
- 2
Start by mixing a small amount of ink to test the color before making large batches.
- 3
Use a consistent ratio for mixing inks to ensure reproducibility.
- 4
Experiment with additives like glycerin for improved texture and ink quality.
- 5
Keep detailed notes on the mixing process for future reference.
Example Answers
I use the color wheel to mix complementary colors, starting with small amounts of ink. This way, I can adjust as needed without wasting materials.
What software tools do you use for designing logos or patterns for stamp pads?
How to Answer
- 1
Identify key software you are proficient in for design work.
- 2
Mention any specific tools suited for creating patterns or logos.
- 3
Highlight your experience using these tools, including any relevant projects.
- 4
If applicable, discuss your familiarity with newer design technologies.
- 5
Express your willingness to learn new software if needed.
Example Answers
I primarily use Adobe Illustrator for designing logos due to its vector capabilities, which are crucial for creating scalable stamp designs. I also use CorelDRAW for pattern generation based on its user-friendly interface for detailed layout work.
Don't Just Read Stamp Pad Maker Questions - Practice Answering Them!
Reading helps, but actual practice is what gets you hired. Our AI feedback system helps you improve your Stamp Pad Maker interview answers in real-time.
Personalized feedback
Unlimited practice
Used by hundreds of successful candidates
Are you familiar with any regulatory standards applicable to the materials used in stamp pad production?
How to Answer
- 1
Research materials commonly used in stamp pads and any relevant regulations.
- 2
Mention specific standards like ASTM or REACH if applicable.
- 3
Discuss the importance of safety and environmental compliance in production.
- 4
Relate any personal experience or knowledge about regulatory compliance.
- 5
Stay updated on industry practices and materials to ensure compliance.
Example Answers
Yes, I am familiar with several regulatory standards. For example, I know that materials used in stamp pads should comply with ASTM D4236 to ensure they are safe for consumers. I also keep an eye on REACH regulations as they pertain to chemicals used in production.
Situational Interview Questions
If you received feedback that a batch of stamp pads did not perform as expected, what steps would you take to address the issue?
How to Answer
- 1
Acknowledge the feedback and express willingness to investigate.
- 2
Gather detailed information about the specific issues reported.
- 3
Analyze the production process for potential flaws.
- 4
Test samples from the batch to replicate the problem.
- 5
Implement corrective actions and communicate findings with the team.
Example Answers
I would first acknowledge the feedback and thank the team for bringing it to my attention. Then, I would collect detailed reports on what issues were experienced with the stamp pads. After that, I would review the production process to identify any discrepancies, and finally, I would conduct tests on samples to see if I can replicate the issue and take actions to fix it.
Imagine you have an extremely tight deadline for a large order. How would you prioritize your tasks to meet the deadline?
How to Answer
- 1
Assess the task requirements and breakdown the order into manageable parts
- 2
Identify critical tasks that have the highest impact on meeting the deadline
- 3
Delegate tasks to team members if possible to speed up the process
- 4
Set realistic time frames for each task and stick to them
- 5
Communicate clearly with your team about priorities and status updates
Example Answers
I would start by breaking the order down into smaller, manageable parts and prioritize the key components needed to meet the deadline. I would focus on the critical tasks first and delegate other tasks to team members to ensure we stay on track.
Don't Just Read Stamp Pad Maker Questions - Practice Answering Them!
Reading helps, but actual practice is what gets you hired. Our AI feedback system helps you improve your Stamp Pad Maker interview answers in real-time.
Personalized feedback
Unlimited practice
Used by hundreds of successful candidates
If two team members disagreed on the best method to create a stamp pad, how would you facilitate a resolution?
How to Answer
- 1
Encourage open communication between both team members
- 2
Ask each person to present their method and reasoning
- 3
Facilitate a discussion to compare the pros and cons of each method
- 4
Encourage collaboration to find a compromise or a better solution
- 5
Summarize the key points and suggest a trial of the agreed method
Example Answers
I would start by bringing both team members together and asking them to share their opinions respectfully. After careful consideration of their ideas, I would encourage them to discuss the pros and cons to find a middle ground that incorporates the best of both methods.
Suppose you are tasked with improving the efficiency of the stamp pad production process. What changes would you consider implementing?
How to Answer
- 1
Analyze the current production workflow to identify bottlenecks
- 2
Invest in automation for repetitive tasks to reduce manual labor
- 3
Implement Lean manufacturing principles to minimize waste
- 4
Train staff to enhance skills and improve productivity
- 5
Foster open communication for feedback on production challenges
Example Answers
I would start by mapping out the entire production process to spot inefficiencies. Then, I would look into automating tasks like ink filling to speed things up. Implementing Lean principles could help us cut down on waste and keep processes smooth.
If you noticed unsafe practices being followed in the workshop while making stamp pads, how would you address the situation?
How to Answer
- 1
Assess the situation to understand the risks involved
- 2
Document the unsafe practices you observed
- 3
Approach the individuals involved calmly to discuss the issue
- 4
Report the situation to a supervisor for further action
- 5
Suggest solutions or safer practices based on your experience
Example Answers
I would first assess the situation and confirm the unsafe practices. Then, I would document what I observed and calmly discuss it with the individuals involved. If the issue persists, I would report it to my supervisor to ensure proper action is taken.
If a client requested changes after you had already begun production on their stamp pads, how would you handle it?
How to Answer
- 1
Acknowledge the client's request and thank them for their feedback.
- 2
Evaluate the feasibility of the changes based on the current production stage.
- 3
Communicate openly about potential impacts on timelines and costs.
- 4
Propose a plan that accommodates the changes while addressing any challenges.
- 5
Ensure to document the revised requirements for clarity.
Example Answers
I would first acknowledge the client's request and express appreciation for their input. Then, I would evaluate how feasible the requested changes are, considering our current production state. If the changes can be made, I would inform the client about any potential delays or cost adjustments and present a clear plan to implement their requests.
If you were given the opportunity to redesign the workflow for making stamp pads, what changes would you propose?
How to Answer
- 1
Identify key inefficiencies in the current workflow
- 2
Suggest automation or technology solutions to improve speed
- 3
Consider material sourcing and inventory management
- 4
Propose ways to enhance quality control processes
- 5
Highlight potential cost savings and improved sustainability
Example Answers
I would analyze the current workflow to identify bottlenecks, such as slow drying times, and propose the introduction of a drying chamber that accelerates this process. This would enhance efficiency.
In a situation where you must scale up production for a big order, how would you organize your resources?
How to Answer
- 1
Assess current production capacity and identify gaps.
- 2
Prioritize essential tasks and allocate resources accordingly.
- 3
Communicate clearly with the team about roles and deadlines.
- 4
Consider outsourcing or temporary staffing if needed.
- 5
Monitor progress closely and adjust plans as necessary.
Example Answers
First, I would evaluate our current production capacity and identify any limitations. Then, I would prioritize the tasks needed to fulfill the order and allocate resources effectively. Communication with the team is key to ensure everyone knows their responsibilities and deadlines.
If a machine broke down mid-production, what contingency plans would you have in place?
How to Answer
- 1
Identify backup machines or manual processes to continue production.
- 2
Notify maintenance immediately and provide specific details of the breakdown.
- 3
Train team members on troubleshooting and basic repairs.
- 4
Keep an updated inventory of necessary spare parts.
- 5
Document and review downtime procedures for continuous improvement.
Example Answers
In case of a machine breakdown, we'd have a backup machine ready to take over. I'll notify maintenance right away and input the issue into our tracking system. I've trained my team on basic troubleshooting to minimize downtime.
How would you handle a situation where a team member consistently struggles with their share of the workload?
How to Answer
- 1
Identify the root cause of their struggles
- 2
Have a private and supportive conversation
- 3
Offer assistance and resources
- 4
Encourage open communication about workloads
- 5
Monitor progress and give constructive feedback
Example Answers
I would first try to understand why my colleague is struggling by having a private chat. If they are overwhelmed, I would offer to help them with their tasks or suggest resources to ease their workload.
Don't Just Read Stamp Pad Maker Questions - Practice Answering Them!
Reading helps, but actual practice is what gets you hired. Our AI feedback system helps you improve your Stamp Pad Maker interview answers in real-time.
Personalized feedback
Unlimited practice
Used by hundreds of successful candidates
Stamp Pad Maker Position Details
Related Positions
- Card Maker
- Machine Stamper
- Hand Stamper
- Stamping Machine Operator
- Cap Maker
- Screen Maker
- Carbon Printer
- Screen Printer
- Tube Maker
- Pill Maker
Similar positions you might be interested in.
Ace Your Next Interview!
Practice with AI feedback & get hired faster
Personalized feedback
Used by hundreds of successful candidates
Ace Your Next Interview!
Practice with AI feedback & get hired faster
Personalized feedback
Used by hundreds of successful candidates