Top 31 Cap Maker Interview Questions and Answers [Updated 2025]
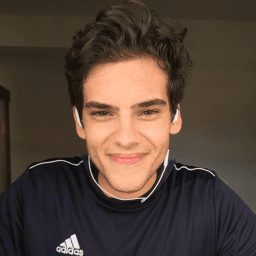
Andre Mendes
•
March 30, 2025
Navigating the competitive world of cap making requires not just skills but also the ability to articulate your expertise during interviews. In this blog post, we delve into the most common interview questions for the Cap Maker role, providing you with example answers and insightful tips on how to respond effectively. Whether you're a seasoned professional or new to the field, this guide will help you stand out and secure your next role.
Download Cap Maker Interview Questions in PDF
To make your preparation even more convenient, we've compiled all these top Cap Makerinterview questions and answers into a handy PDF.
Click the button below to download the PDF and have easy access to these essential questions anytime, anywhere:
List of Cap Maker Interview Questions
Behavioral Interview Questions
Can you describe a time when you worked as part of a team to design a new cap? What was your role?
How to Answer
- 1
Choose a specific project where you collaborated with others.
- 2
Outline your role clearly and what you contributed.
- 3
Highlight the design process and any innovative ideas you brought.
- 4
Emphasize teamwork, how you communicated, and resolved conflicts.
- 5
Mention the outcome and what you learned from the experience.
Example Answers
In my last project, I worked on a team to design a baseball cap for a local sports team. My role was as the lead designer. I initiated brainstorming sessions where I encouraged everyone to share their ideas. I designed several prototypes, focusing on unique fabric choices and aesthetics. Our final design not only won the client's approval but also boosted team spirit, and I learned the importance of inclusive communication.
Tell me about a challenging cap design project you were involved in. How did you overcome the obstacles?
How to Answer
- 1
Start by describing the specific project and its objectives.
- 2
Identify the main challenges you faced during the project.
- 3
Explain the steps you took to address those challenges.
- 4
Highlight any teamwork or collaboration that contributed to the solution.
- 5
Conclude with the positive outcome and what you learned from the experience.
Example Answers
In a recent cap design project, we faced a tight deadline while trying to incorporate a new eco-friendly material. The challenge was the material's availability and performance under production constraints. I coordinated with suppliers to secure the material ahead of schedule and collaborated with the production team to adjust the design for manufacturability. We successfully launched the cap on time, and I learned the importance of proactive communication.
Don't Just Read Cap Maker Questions - Practice Answering Them!
Reading helps, but actual practice is what gets you hired. Our AI feedback system helps you improve your Cap Maker interview answers in real-time.
Personalized feedback
Unlimited practice
Used by hundreds of successful candidates
Have you ever taken the lead on a cap-making project? How did you manage your team?
How to Answer
- 1
Describe the cap-making project in brief.
- 2
Highlight your leadership role and key responsibilities.
- 3
Explain how you communicated with your team.
- 4
Mention any challenges you faced and how you overcame them.
- 5
Conclude with the project's outcome and any lessons learned.
Example Answers
I led a project to design a new line of caps for a local sports team. I organized weekly team meetings to track progress and gather input. We faced challenges with sourcing materials, but I coordinated with suppliers to ensure we stayed on schedule. The project was a success, and the caps were well-received by the team, teaching me the value of proactive communication.
Describe a situation where a cap you made did not meet quality standards. How did you handle it?
How to Answer
- 1
Be specific about the quality issue with the cap.
- 2
Explain your immediate response to the problem.
- 3
Describe the steps you took to resolve the issue.
- 4
Highlight what you learned from the situation.
- 5
Mention how you applied that learning to future projects.
Example Answers
I once made a batch of caps where the stitching was uneven, which did not meet our quality standards. I immediately identified the problem and conducted a thorough inspection of all caps in that batch. After discarding the poor-quality caps, I worked overtime to redo them correctly. I learned the importance of double-checking stitching patterns before mass production and now I always implement a pre-check process.
Can you provide an example of a unique cap design you created? What inspired you?
How to Answer
- 1
Choose a specific cap design that stands out.
- 2
Explain the inspiration clearly, linking it to personal experience or trends.
- 3
Describe the design features that make it unique.
- 4
Mention any challenges faced and how you overcame them.
- 5
Relate how this design reflects your skills or creativity.
Example Answers
I designed a cap featuring a solar system theme. My inspiration came from my love of astronomy. The unique element was the use of glow-in-the-dark paint for the planets, creating a stunning night effect. I faced challenges sourcing the right materials, but I persevered until I found them. This design showcases my creativity and attention to detail.
Have you ever trained someone in cap-making techniques? What approach did you take?
How to Answer
- 1
Start with a specific example of training someone in cap-making.
- 2
Explain the techniques you taught and the methods you used.
- 3
Discuss how you tailored your approach to the learner's skill level.
- 4
Mention any feedback you received or results from the training.
- 5
Highlight your passion for teaching and making caps.
Example Answers
Yes, I trained a new team member on how to make custom caps. I began with an overview of the techniques, then demonstrated each step in the process. I encouraged them to ask questions and practiced with them until they felt confident. They ended up creating their own design that received positive feedback.
Describe a time when you had multiple projects to complete. How did you manage your time effectively?
How to Answer
- 1
Identify the projects and their deadlines clearly
- 2
Explain your prioritization method, like urgency or importance
- 3
Discuss tools or techniques used for time management
- 4
Provide an example of a challenge faced and how you overcame it
- 5
Conclude with what you learned and how it improved your skills
Example Answers
In my last role, I had three simultaneous projects with overlapping deadlines. I prioritized them based on impact and urgency, using a simple Gantt chart to visualize timelines. I completed the most critical project first while delegating tasks for the others. In the end, I met all deadlines and learned the value of good planning.
Can you tell me about a time when you had to adapt to a sudden change in a cap project?
How to Answer
- 1
Identify a specific project and change you faced
- 2
Explain the context and what prompted the change
- 3
Describe how you assessed the situation quickly
- 4
Discuss the actions you took to adapt
- 5
Reflect on the outcomes and what you learned
Example Answers
In one project, our cap design changed due to new regulations. I quickly reviewed the new requirements, consulted with my team, and we redesigned the cap within a week. This swift adaptation kept the project on schedule and compliant with regulations.
Describe your work ethic when it comes to meeting production deadlines for caps.
How to Answer
- 1
Emphasize time management skills by giving specific methods you use.
- 2
Discuss your commitment to quality even under tight deadlines.
- 3
Mention how you handle unexpected issues and still reach deadlines.
- 4
Explain the importance of teamwork in meeting production goals.
- 5
Share a personal experience where your work ethic positively impacted production.
Example Answers
I prioritize my tasks using a daily schedule and set clear goals to manage my time effectively. I believe in maintaining quality and I communicate with my team to ensure we are all aligned, especially when we face unexpected challenges.
Don't Just Read Cap Maker Questions - Practice Answering Them!
Reading helps, but actual practice is what gets you hired. Our AI feedback system helps you improve your Cap Maker interview answers in real-time.
Personalized feedback
Unlimited practice
Used by hundreds of successful candidates
What is your approach to ensuring customer satisfaction in cap making?
How to Answer
- 1
Understand customer needs by asking detailed questions
- 2
Provide high-quality materials for durability and comfort
- 3
Ensure accurate customization to meet client specifications
- 4
Communicate regularly with customers throughout the process
- 5
Gather feedback after delivery to improve future services
Example Answers
I start by asking customers about their preferences and needs, then I select the best materials to ensure comfort. I also keep them updated throughout the process and seek their feedback to continuously improve.
Technical Interview Questions
What types of materials do you prefer for making caps and why?
How to Answer
- 1
Identify key materials for different types of caps like cotton, wool, or polyester
- 2
Explain the benefits of each material in terms of comfort, durability, and style
- 3
Mention any personal experiences working with specific materials
- 4
Consider environmental impact and sustainability when choosing materials
- 5
Be ready to explain how material choice affects cap design and functionality
Example Answers
I prefer using cotton for caps because it is breathable and comfortable for everyday wear. It allows for moisture wicking, which is great for outdoor activities. Additionally, I like to incorporate recycled cotton for a more eco-friendly approach.
Can you explain the different sewing techniques you use when constructing caps?
How to Answer
- 1
Identify key sewing techniques relevant to cap making.
- 2
Mention any specific stitching methods like straight stitch or zigzag.
- 3
Discuss how you handle curves and seams for a good fit.
- 4
Explain the importance of reinforcement in certain areas.
- 5
Highlight any finishing techniques that enhance durability.
Example Answers
I primarily use straight stitching for the main seams of the cap, ensuring a strong hold. For curves, I utilize a zigzag stitch which helps maintain flexibility. I also reinforce the brim with double stitching to prevent wear over time.
Don't Just Read Cap Maker Questions - Practice Answering Them!
Reading helps, but actual practice is what gets you hired. Our AI feedback system helps you improve your Cap Maker interview answers in real-time.
Personalized feedback
Unlimited practice
Used by hundreds of successful candidates
What design software or tools do you use when creating cap designs?
How to Answer
- 1
Identify the key design software specific to cap design.
- 2
Mention any additional tools for prototyping or sketching.
- 3
Highlight any experience with collaborative tools if applicable.
- 4
Be prepared to discuss how these tools enhance your design process.
- 5
Relate the software's features to your design needs.
Example Answers
I primarily use Adobe Illustrator for creating vector designs of caps. I also use Photoshop for visualizing textures and colors, and I frequently utilize Sketch for quick prototyping and mock-ups.
Describe the process you follow to create patterns for cap making.
How to Answer
- 1
Start with research on current cap designs and trends.
- 2
Sketch initial ideas considering different materials.
- 3
Create a detailed pattern incorporating measurements.
- 4
Test the pattern with a sample cap for fit and design.
- 5
Make adjustments based on the test results and finalize the pattern.
Example Answers
I begin by researching the latest trends in cap designs and materials. I then sketch my initial ideas and choose the right fabric. After that, I create a detailed pattern with all necessary measurements. I make a sample cap to test the fit and style, and I adjust the pattern based on the outcome before finalizing it.
What machinery do you operate for cap production, and what is your comfort level with them?
How to Answer
- 1
List specific machines you've used for cap production.
- 2
Describe your level of experience with each machine.
- 3
Mention any relevant certifications or training received.
- 4
Highlight any achievements or projects linked to machine operation.
- 5
Express your willingness to learn new machines if necessary.
Example Answers
I have operated injection molding machines, particularly the ABC 3000, for producing plastic caps. I have 5 years of experience and feel very confident in setting up and maintaining this machine. I also completed a training course in advanced machine operations last year.
What customization options do you think are important to offer for caps?
How to Answer
- 1
Consider material choices like cotton, wool, or synthetic blends for comfort and style.
- 2
Think about design elements such as embroidery, patches or printed logos for branding.
- 3
Include size options to accommodate different head sizes with adjustable straps.
- 4
Explore color variations and patterns to appeal to diverse customer preferences.
- 5
Don't forget functionality features like moisture-wicking or UV protection for sports caps.
Example Answers
I believe important customization options include a range of materials like breathable cotton and water-resistant fabrics, as these can meet different customer needs for comfort and utility.
How do you stay updated on the latest trends in cap design?
How to Answer
- 1
Follow leading cap brands on social media to see their latest designs.
- 2
Subscribe to fashion and design newsletters to receive trend updates.
- 3
Attend trade shows and industry events to network and see new products.
- 4
Join online forums and communities focused on cap design to share ideas.
- 5
Research market reports and analysis to understand design trends.
Example Answers
I follow several leading cap brands on Instagram and Twitter to keep up with their new collections and trends. I also subscribe to fashion industry newsletters, which help me spot emerging styles.
How do you apply color theory when designing caps?
How to Answer
- 1
Understand the basics of color theory like the color wheel and color harmony.
- 2
Identify the target audience to choose colors that resonate with their preferences.
- 3
Experiment with contrasting and complementary colors to create visually appealing designs.
- 4
Consider the purpose of the cap when selecting colors, like sporty vs. casual.
- 5
Use colors to convey emotions and messages associated with the brand.
Example Answers
I use the color wheel to find complementary colors that make our caps stand out while appealing to our young audience. For example, using navy and orange can give a modern yet energetic look.
What are your thoughts on sustainability in cap manufacturing, and how have you implemented eco-friendly practices?
How to Answer
- 1
Discuss the importance of sustainability in reducing environmental impact.
- 2
Mention specific materials or processes that are eco-friendly.
- 3
Share examples of practices you have personally implemented.
- 4
Highlight any measurable outcomes from these practices.
- 5
Show a forward-thinking approach by suggesting future improvements.
Example Answers
Sustainability is crucial in cap manufacturing as it helps reduce waste. I have started using recycled materials in our products and optimized our production process to minimize energy consumption. As a result, we've cut carbon emissions by 20% over the last year.
What finishing touches do you consider essential for a high-quality cap?
How to Answer
- 1
Focus on stitching quality and its evenness.
- 2
Mention the importance of labeling for brand identity.
- 3
Discuss the significance of sweatbands for comfort and durability.
- 4
Highlight the role of proper fit for user satisfaction.
- 5
Consider embellishments that enhance aesthetic value.
Example Answers
For a high-quality cap, I ensure the stitching is consistent and tight, which prevents fraying. I also prioritize the addition of a comfortable sweatband to enhance wearability.
Don't Just Read Cap Maker Questions - Practice Answering Them!
Reading helps, but actual practice is what gets you hired. Our AI feedback system helps you improve your Cap Maker interview answers in real-time.
Personalized feedback
Unlimited practice
Used by hundreds of successful candidates
Situational Interview Questions
If a client requests a custom cap design with a tight deadline, how would you prioritize tasks?
How to Answer
- 1
Assess the client's requirements clearly to understand the scope
- 2
Break down the design process into key tasks and milestones
- 3
Communicate with the client about realistic timelines and any constraints
- 4
Prioritize tasks based on urgency and importance to meet the deadline
- 5
Ensure to allocate time for revisions and feedback during the process
Example Answers
First, I would clarify the design details with the client to know exactly what they want. Then, I would list out the tasks like drafting concepts, selecting materials, and finalizing the design, prioritizing those that are critical to meet the deadline. I'll keep the client updated on progress as well.
How would you handle a situation where the material needed for cap production is unexpectedly out of stock?
How to Answer
- 1
Assess the inventory and confirm the stock outage.
- 2
Communicate with suppliers for urgent restock options.
- 3
Explore alternative materials that can be used temporarily.
- 4
Inform key team members about the situation and next steps.
- 5
Develop a contingency plan to minimize production delays.
Example Answers
I would first confirm the stock outage and check the inventory. Then, I would contact our suppliers to see if they can expedite the delivery of the needed materials. If that’s not possible, I would look for alternative materials that could work for our caps.
Don't Just Read Cap Maker Questions - Practice Answering Them!
Reading helps, but actual practice is what gets you hired. Our AI feedback system helps you improve your Cap Maker interview answers in real-time.
Personalized feedback
Unlimited practice
Used by hundreds of successful candidates
Imagine you need to reduce production costs without compromising quality. What strategies would you implement?
How to Answer
- 1
Analyze production processes for inefficiencies and waste reduction.
- 2
Invest in employee training to improve skills and efficiency.
- 3
Negotiate with suppliers for better pricing on materials.
- 4
Implement lean manufacturing principles to streamline operations.
- 5
Use technology to automate repetitive tasks and reduce labor costs.
Example Answers
I would start by analyzing the production process to identify any inefficiencies. For example, I might use lean principles to eliminate waste and streamline operations. Additionally, I would focus on negotiating better rates with suppliers to reduce raw material costs.
If a disagreement arises between team members on a cap design, how would you facilitate resolution?
How to Answer
- 1
Listen actively to all perspectives involved in the disagreement
- 2
Encourage open communication and ensure everyone feels heard
- 3
Identify common goals or objectives for the design
- 4
Suggest brainstorming sessions to generate new ideas or compromises
- 5
Reach a consensus by summarizing key points and deciding on next steps
Example Answers
I would start by listening to each team member's viewpoint to understand their concerns. Then, I would facilitate a discussion to highlight our shared goals for the cap design, encouraging everyone to collaborate on finding a solution that incorporates the best elements from each perspective.
You receive negative feedback from a customer on the fit of a cap. What steps would you take to address this?
How to Answer
- 1
Acknowledge the customer's feedback and thank them for it
- 2
Ask specific questions to understand their concerns about the fit
- 3
Review design and size specifications related to the cap
- 4
Consider adjustments in the product or processes based on feedback
- 5
Follow up with the customer to inform them of any changes made
Example Answers
I would first thank the customer for their feedback and ask for specific details about the fit issue. Then, I'd review our size specifications and consult with the design team to see if there are adjustments we can make. Finally, I would follow up with the customer to let them know we value their feedback and inform them of any changes made.
If your workplace lacks safety protocols, how would you advocate for safer practices in cap manufacturing?
How to Answer
- 1
Identify specific safety issues in cap manufacturing processes.
- 2
Gather data or examples showing the importance of safety practices.
- 3
Engage with colleagues to discuss safety concerns and potential solutions.
- 4
Propose a plan to management that outlines steps for implementing safety protocols.
- 5
Be prepared to lead safety training sessions or initiatives if necessary.
Example Answers
I would start by identifying specific safety issues, like inadequate protective gear. Then, I would gather data on incidents related to those issues and present a case to management for establishing safety protocols.
How would you approach a long-term client who seems unhappy with recent cap deliveries?
How to Answer
- 1
Initiate a conversation to address the client's concerns directly.
- 2
Listen actively to understand their specific issues with the cap deliveries.
- 3
Acknowledge their frustration and show empathy for their situation.
- 4
Offer solutions or improvements to address their grievances.
- 5
Follow up after implementing changes to ensure their satisfaction.
Example Answers
I would first reach out to the client to set up a meeting where I can hear their concerns directly. I would listen carefully to their feedback, acknowledge their frustrations, and assure them that we take their satisfaction seriously. I would then propose specific changes to our delivery process to resolve their issues and follow up to make sure they are happy with the solutions.
What would you do if you encountered a significant error in a cap batch just before delivery?
How to Answer
- 1
Stay calm and assess the situation quickly.
- 2
Identify the nature of the error and its impact.
- 3
Communicate with the team and relevant stakeholders immediately.
- 4
Determine if the error can be corrected in time.
- 5
Document the error and the actions taken for future reference.
Example Answers
First, I would calmly evaluate the error to understand its impact. Then, I would immediately inform my supervisor and the production team about the issue. If possible, I would work with the team to correct the error before delivery. Finally, I would document everything that happened for future reference.
If you were managing a project with changing requirements, how would you keep your team aligned?
How to Answer
- 1
Communicate regularly with the team about changes and updates
- 2
Hold brief daily stand-up meetings to discuss progress and challenges
- 3
Use project management tools to track changes and keep everyone informed
- 4
Encourage open feedback from the team regarding challenges with changing requirements
- 5
Revisit team goals and priorities frequently to ensure alignment
Example Answers
I would establish daily stand-up meetings to discuss any changes and ensure everyone's on the same page. Additionally, I would encourage the team to provide feedback on new requirements so we can address any concerns immediately.
How would you assess risks in your cap production process and what steps would you take to mitigate them?
How to Answer
- 1
Identify potential risks like supplier delays, equipment failures, and quality issues.
- 2
Conduct a thorough analysis of each risk by considering impact and likelihood.
- 3
Develop contingency plans for high-risk areas, such as alternative suppliers.
- 4
Implement regular monitoring to detect issues early, using quality control metrics.
- 5
Train staff on risk management practices to foster a proactive culture.
Example Answers
I assess risks by first identifying key areas such as supplier reliability and production machinery. I analyze their impact and likelihood, then create contingency plans, like having backup suppliers and performing routine maintenance. Regular quality checks help us catch problems early.
Don't Just Read Cap Maker Questions - Practice Answering Them!
Reading helps, but actual practice is what gets you hired. Our AI feedback system helps you improve your Cap Maker interview answers in real-time.
Personalized feedback
Unlimited practice
Used by hundreds of successful candidates
Cap Maker Position Details
Related Positions
- Part Maker
- Heading Maker
- Tube Maker
- Card Maker
- Stamp Pad Maker
- Basket Maker
- Screen Maker
- Box Maker
- Form Maker
- Pill Maker
Similar positions you might be interested in.
Ace Your Next Interview!
Practice with AI feedback & get hired faster
Personalized feedback
Used by hundreds of successful candidates
Ace Your Next Interview!
Practice with AI feedback & get hired faster
Personalized feedback
Used by hundreds of successful candidates