Top 32 Part Maker Interview Questions and Answers [Updated 2025]
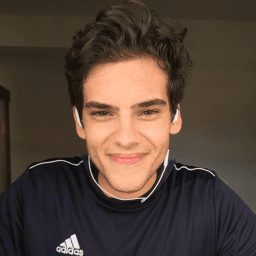
Andre Mendes
•
March 30, 2025
Are you preparing for a Part Maker interview and want to stand out? This blog post covers the most common interview questions for the Part Maker role, complete with example answers and insightful tips on how to respond effectively. Dive in to enhance your interviewing skills and boost your confidence, ensuring you're ready to impress any potential employer with well-crafted, thoughtful responses.
Download Part Maker Interview Questions in PDF
To make your preparation even more convenient, we've compiled all these top Part Makerinterview questions and answers into a handy PDF.
Click the button below to download the PDF and have easy access to these essential questions anytime, anywhere:
List of Part Maker Interview Questions
Situational Interview Questions
If you noticed unsafe working conditions in the part-making area, what steps would you take?
How to Answer
- 1
Assess the situation quickly to identify specific hazards.
- 2
Immediately report concerns to a supervisor or safety officer.
- 3
If safe to do so, warn coworkers about the danger.
- 4
Document the unsafe conditions for follow-up.
- 5
Follow up to ensure corrective actions are taken.
Example Answers
I would first assess the area to determine the exact hazards present. Then, I would report my findings to my supervisor right away. If it posed an imminent risk, I would alert my coworkers to keep them safe.
If you realize a part you've made is defective after it has completed the production run, what steps would you take?
How to Answer
- 1
Acknowledge the defect immediately and assess the situation
- 2
Document the details of the defect and affected parts
- 3
Notify your supervisor or quality control team
- 4
Analyze the root cause of the defect to prevent future issues
- 5
Communicate with the customer if the defect impacts their order
Example Answers
I would first acknowledge the defect and assess how many parts are affected. Then, I would document all relevant details about the defect and inform my supervisor right away. After that, I'd work on determining the root cause of the issue to ensure it doesn’t happen again.
Don't Just Read Part Maker Questions - Practice Answering Them!
Reading helps, but actual practice is what gets you hired. Our AI feedback system helps you improve your Part Maker interview answers in real-time.
Personalized feedback
Unlimited practice
Used by hundreds of successful candidates
Imagine you notice a bottleneck in your manufacturing process; what actions would you take to improve the situation?
How to Answer
- 1
Identify the specific bottleneck in the process.
- 2
Gather data to understand the cause and impact of the bottleneck.
- 3
Brainstorm potential solutions to alleviate the bottleneck.
- 4
Implement a solution on a small scale to test effectiveness.
- 5
Monitor the results and adjust the approach as necessary.
Example Answers
I would first identify the specific steps causing the delay. Then, I would analyze production data to find the root cause. After that, I would explore solutions like adding resources or retraining staff. Next, I would implement the chosen solution on a trial basis and monitor the results closely.
How would you handle a situation where a key material for part-making suddenly becomes unavailable?
How to Answer
- 1
Assess the impact on the production schedule and delivery timelines.
- 2
Identify alternative materials that can be used without compromising quality.
- 3
Communicate with suppliers to explore fast sourcing of the required material.
- 4
Inform team members and stakeholders about the situation and proposed solutions.
- 5
Consider implementing contingency plans for future material shortages.
Example Answers
If a key material becomes unavailable, I would first evaluate how it affects our timelines. Then, I would look for alternative materials that meet our specifications. I would work with our suppliers to see if we can quickly source the needed material or the alternatives. Keeping the team and stakeholders updated is also vital during this process.
If you and a colleague disagree on the best approach to produce a part, how would you resolve it?
How to Answer
- 1
Listen actively to your colleague's perspective without interrupting.
- 2
Ask clarifying questions to understand their reasoning better.
- 3
Present your own approach with clear justification and data.
- 4
Propose a compromise or a joint evaluation of both methods.
- 5
Focus on the project goals and collaborate to find the best solution.
Example Answers
I would first listen to my colleague's approach carefully and ask questions to understand their point of view. Then I would share my own method with supporting data, and we could evaluate both options together to see which aligns better with our project goals.
How would you prioritize your tasks if you were given an urgent order with a tight deadline?
How to Answer
- 1
Assess the requirements of the urgent order quickly
- 2
Identify any tasks that can be delegated or postponed
- 3
Focus on tasks that directly impact the completion of the order
- 4
Communicate with your team about the urgency and expectations
- 5
Use a simple priority matrix to organize tasks by importance and urgency
Example Answers
I would start by reviewing the details of the urgent order to understand its requirements. Then, I’d identify if there are tasks I can delegate or put on hold. Next, I’d prioritize tasks that are essential for fulfilling the order and communicate with my team to ensure everyone is aware of the deadlines.
What approach would you use to plan a production schedule for multiple parts?
How to Answer
- 1
Identify the parts and their specifications
- 2
Assess the production capacity and resources available
- 3
Prioritize parts based on deadlines and complexity
- 4
Create a timeline that accommodates production flow and potential bottlenecks
- 5
Monitor progress and adjust the schedule as needed
Example Answers
First, I would list all the parts needed and their specifications. Then, I would assess our machine capacity to see how many parts can be produced simultaneously. After that, I would prioritize based on upcoming deadlines and complexity of each part. Next, I'd draft a timeline ensuring a smooth workflow and account for possible delays. Finally, I would regularly check in on progress and modify the schedule if necessary.
If you are assigned to work on several different parts simultaneously, how would you handle this?
How to Answer
- 1
Prioritize tasks based on deadlines and complexity
- 2
Break down each part into smaller tasks
- 3
Set a schedule to allocate specific time for each part
- 4
Communicate with team members about progress and challenges
- 5
Review and adjust priorities as needed throughout the project
Example Answers
I would start by prioritizing the parts based on their deadlines, breaking each one down into smaller tasks. I'd allocate time slots in my schedule for focused work on each part and regularly communicate my progress to ensure alignment with the team.
If production was disrupted due to equipment failure, what steps would you take to minimize downtime?
How to Answer
- 1
Quickly assess the situation and identify the cause of the failure
- 2
Communicate with the team about the issue and expected downtime
- 3
Engage maintenance staff or technical support immediately
- 4
Implement temporary workaround solutions if possible
- 5
Document the incident for future reference and prevention
Example Answers
First, I would assess the equipment to determine the cause of the failure. I would then communicate with my team to inform them of the situation and expected downtime. I'd contact maintenance immediately to get assistance and explore any possible temporary workarounds while we await repairs.
How would you approach developing a new part-making technique or tool?
How to Answer
- 1
Identify the specific needs and challenges of part-making in your context.
- 2
Research existing techniques and tools to find gaps or improvements.
- 3
Consult with team members for input and collaboration on ideas.
- 4
Create prototypes or sketches to visualize the new technique or tool.
- 5
Test the concept thoroughly and iterate based on feedback and results.
Example Answers
I would start by assessing our current part-making needs and any issues we face. Then, I would research similar techniques to see what advancements exist. Collaborating with my team for diverse input is essential. After identifying a promising idea, I'd draft a prototype and test it before refining based on feedback.
Don't Just Read Part Maker Questions - Practice Answering Them!
Reading helps, but actual practice is what gets you hired. Our AI feedback system helps you improve your Part Maker interview answers in real-time.
Personalized feedback
Unlimited practice
Used by hundreds of successful candidates
Behavioral Interview Questions
Can you describe a time when you worked on a team to complete a part fabrication project?
How to Answer
- 1
Start with the project goal and your role in the team
- 2
Mention specific techniques or tools used during fabrication
- 3
Describe how you communicated and collaborated with teammates
- 4
Highlight any challenges faced and how you overcame them
- 5
Conclude with the results of the project and your team's success
Example Answers
In my previous position, our team was tasked with fabricating custom brackets for a new product line. I was the lead machinist and coordinated our efforts using CAD software. We faced a tight deadline, so we held daily check-in meetings to track our progress. By collaborating closely, we managed to complete the project ahead of schedule, and the brackets met all client specifications, leading to a successful launch.
Tell me about a challenging part-making issue you faced and how you resolved it.
How to Answer
- 1
Choose a specific example from your experience
- 2
Describe the challenge clearly and concisely
- 3
Explain the actions you took to resolve the issue
- 4
Highlight the outcome and what you learned
- 5
Relate it back to skills relevant to a Part Maker position
Example Answers
In a previous project, I faced an issue where a tolerance on a critical part was not met during the initial machining process. I quickly assessed the situation, pinpointed the root cause as tool wear, and replaced the tooling. I then recalibrated the machine and successfully produced parts within tolerance. This experience taught me the importance of regular maintenance and quality checks.
Don't Just Read Part Maker Questions - Practice Answering Them!
Reading helps, but actual practice is what gets you hired. Our AI feedback system helps you improve your Part Maker interview answers in real-time.
Personalized feedback
Unlimited practice
Used by hundreds of successful candidates
Give an example of a time you caught a mistake before it affected the production process.
How to Answer
- 1
Think of a specific instance where you identified a mistake.
- 2
Explain what the mistake was and how you noticed it.
- 3
Describe the actions you took to prevent it from impacting production.
- 4
Mention the outcome and what you learned from the experience.
- 5
Keep it concise and focused on your role in resolving the issue.
Example Answers
In my previous role, I noticed a discrepancy in the material measurements during quality checks. By double-checking the specifications, I realized the dimensions provided were wrong. I immediately informed my supervisor and we corrected the measurements before any parts were made. This saved us from potential rework and material waste.
Describe a situation where you had to manage multiple part-making tasks under tight deadlines.
How to Answer
- 1
Identify a specific time you faced multiple tasks.
- 2
Explain the priorities you set for each task.
- 3
Discuss the tools or methods you used to manage time.
- 4
Highlight how you communicated with the team or stakeholders.
- 5
Conclude with the positive outcome or what you learned.
Example Answers
In my previous role, I had three parts due for a major deadline. I prioritized them by complexity and deadline proximity. I used a Gantt chart to map out my time effectively. I kept my team updated daily through quick check-ins, and we successfully delivered all parts on time with high quality.
How have you successfully communicated technical information to non-technical team members?
How to Answer
- 1
Use simple language and avoid jargon
- 2
Use analogies to relate technical concepts to everyday experiences
- 3
Break down complex information into smaller, manageable parts
- 4
Ask for feedback to ensure understanding
- 5
Use visual aids like diagrams or charts when possible
Example Answers
In my previous role, I often needed to explain machining processes to the marketing team. I would use analogies, comparing a CNC machine to a 3D printer, which they were familiar with, to help them understand the basics without technical jargon.
Can you provide an example of a time when you had to adapt to a significant change in a project?
How to Answer
- 1
Think of a specific project where change occurred
- 2
Describe the change clearly and its impact
- 3
Explain your role in addressing the change
- 4
Highlight the actions you took to adapt
- 5
Reflect on the outcome and what you learned
Example Answers
In my last project, we switched from manual part production to automated machining halfway through. I quickly learned the new software and trained the team on it. As a result, we improved efficiency and met our deadline with quality parts.
Have you ever taken a leadership role in a part-making project? Please describe your experience.
How to Answer
- 1
Choose a specific project where you had a leadership role
- 2
Highlight your responsibilities and how you managed the team
- 3
Discuss any challenges faced and how you overcame them
- 4
Mention the outcome of the project and any metrics of success
- 5
Keep your answer focused and relevant to part making
Example Answers
In my last position, I led a team of three engineers on a custom part-making project for a client. I coordinated our workflows, ensuring deadlines were met. We faced a major setback with our material selection, but I organized an emergency meeting to brainstorm alternatives, resulting in a successful delivery ahead of schedule.
Describe a time when you received critical feedback on your work. How did you respond?
How to Answer
- 1
Choose a specific instance where you received feedback.
- 2
Explain the context of the feedback clearly.
- 3
Describe how you reacted emotionally and practically.
- 4
Highlight the steps you took to improve or adapt based on the feedback.
- 5
Mention any positive outcomes or what you learned from the experience.
Example Answers
In my previous job as a part maker, I received critical feedback from my supervisor about my precision in measurements. I felt initially discouraged, but I recognized it as an opportunity to improve. I asked for clarification on the specific issues and then took time to practice my measuring techniques. As a result, my precision improved significantly, and I earned praise for my attention to detail in subsequent projects.
Have you ever mentored someone in part-making? What approach did you take?
How to Answer
- 1
Share a specific mentoring experience related to part-making
- 2
Describe the goals you set for the mentee
- 3
Explain the methods you used to teach and guide them
- 4
Mention any challenges faced and how you overcame them
- 5
Highlight the outcomes or improvements in the mentee's skills
Example Answers
I mentored a junior machinist on using CNC machines. We set specific goals for mastering tool changes and programming. I used hands-on demonstrations and encouraged questions. Initially, he struggled with programming, but we tackled it together through step-by-step sessions. In the end, he successfully operated the CNC alone and even helped others.
What do you consider your greatest success in part-making, and why?
How to Answer
- 1
Pick a specific project that had a significant impact.
- 2
Explain the challenges you faced during the project.
- 3
Highlight the skills or techniques you used to achieve success.
- 4
Discuss the outcome and its importance to the team or company.
- 5
Reflect on what you learned from that experience.
Example Answers
My greatest success in part-making was when I led the production of a complex turbine component. We faced tight deadlines and material shortages, but I optimized our workflow and coordinated with suppliers. The part was delivered on time, significantly improving our project's timeline, and I learned the importance of good communication under pressure.
Don't Just Read Part Maker Questions - Practice Answering Them!
Reading helps, but actual practice is what gets you hired. Our AI feedback system helps you improve your Part Maker interview answers in real-time.
Personalized feedback
Unlimited practice
Used by hundreds of successful candidates
Technical Interview Questions
What types of machinery are you proficient with in part-making?
How to Answer
- 1
Identify the specific machines you have used
- 2
Mention your experience level with each machine
- 3
Include any relevant certifications or training
- 4
Relate your experience to the type of parts you have made
- 5
Be prepared to discuss how you operated the machines safely and efficiently
Example Answers
I have extensive experience with CNC milling machines, having operated them for over 5 years. I also proficiently use lathes and drilling machines, which I learned during my apprenticeship.
How do you ensure that the parts you make meet the required specifications and tolerances?
How to Answer
- 1
Review technical drawings and specifications carefully before starting.
- 2
Use precision measuring tools like calipers and micrometers during manufacturing.
- 3
Implement a quality control process to check parts at different stages.
- 4
Document all measurements and any adjustments made during the process.
- 5
Communicate regularly with the engineering team to clarify any doubts regarding specifications.
Example Answers
I start by thoroughly reviewing the technical drawings to understand the specifications. During production, I use calipers and micrometers to measure dimensions and ensure they fall within tolerance. I also conduct quality checks at various stages and document my measurements.
Don't Just Read Part Maker Questions - Practice Answering Them!
Reading helps, but actual practice is what gets you hired. Our AI feedback system helps you improve your Part Maker interview answers in real-time.
Personalized feedback
Unlimited practice
Used by hundreds of successful candidates
What types of materials have you worked with in part manufacturing, and how do they affect your production process?
How to Answer
- 1
Identify specific materials you've used such as metals, plastics, or composites.
- 2
Explain how each material influences your choice of machining methods.
- 3
Discuss any special handling or processing required for specific materials.
- 4
Mention quality control measures you implement for different materials.
- 5
Share any experiences with material selection based on project requirements.
Example Answers
I have worked primarily with aluminum and ABS plastic. Aluminum requires precision machining and cooling during the process, while ABS is easier to mold and shape, which affects the speed of production.
Describe your experience with CAD software in designing parts.
How to Answer
- 1
Mention specific CAD software you have used
- 2
Explain your role and responsibilities in projects
- 3
Highlight any successful projects or designs
- 4
Discuss any challenges you overcame using CAD
- 5
If possible, relate your experience to the job requirements
Example Answers
I have extensive experience using SolidWorks for designing mechanical parts. In my previous job, I was responsible for creating detailed models and assemblies for automotive components, which improved our production efficiency by 15%.
What quality control measures do you implement in your part-making process?
How to Answer
- 1
Describe specific quality control tools you use.
- 2
Mention the frequency of inspections within the process.
- 3
Highlight any standards or specifications you follow.
- 4
Discuss how you document quality checks and results.
- 5
Explain how you address and resolve quality issues.
Example Answers
I use a combination of calipers and gauges for precise measurements at various stages, check dimensions every 10 parts, and document results in a quality log. If I find inconsistencies, I adjust the machine settings immediately.
Do you have experience programming CNC machines? If so, please elaborate.
How to Answer
- 1
State your programming experience clearly and mention specific CNC machines.
- 2
Discuss the software you used, such as G-code or CAD/CAM systems.
- 3
Provide examples of projects or tasks where you programmed CNC machines.
- 4
Mention any results or improvements your programming achieved.
- 5
Conclude with your enthusiasm for CNC technology and learning further.
Example Answers
Yes, I have over 3 years of experience programming CNC mills and lathes using Mastercam. I programmed parts for a project that reduced production time by 20%. I'm excited to apply this knowledge and learn more.
What experience do you have with the assembly of parts post-manufacturing?
How to Answer
- 1
Highlight specific roles involving assembly work
- 2
Mention any relevant tools or techniques used
- 3
Discuss the importance of quality control in assembly
- 4
Share experiences with teams or collaboration
- 5
Provide examples of problem-solving during assembly processes
Example Answers
In my last position at ABC Manufacturing, I was responsible for assembling components for our hydraulic systems. I used precision tools and ensured each assembly met our strict quality standards. I also coordinated with quality control to troubleshoot any issues that arose during the assembly process.
Can you talk about your experience with designing and utilizing fixtures for part-making?
How to Answer
- 1
Explain your specific role in designing fixtures
- 2
Mention tools and software you used for design
- 3
Describe a project where your fixture improved efficiency
- 4
Highlight any challenges you faced and how you solved them
- 5
Emphasize teamwork or collaboration with other departments
Example Answers
In my last role as a part maker, I designed fixtures using SolidWorks. I created a unique fixture for engine components that reduced setup time by 30%. During the project, I collaborated closely with the machining team to integrate their feedback, which led to a more efficient design.
What do you understand by tolerance in part-making, and how do you achieve it?
How to Answer
- 1
Define tolerance in the context of part-making as acceptable limits of variation in dimensions.
- 2
Explain how you interpret technical drawings to understand specified tolerances.
- 3
Discuss the tools and machines you use to achieve these tolerances accurately.
- 4
Mention the importance of regular calibrations and maintenance of equipment.
- 5
Provide examples of how you ensure quality control during production.
Example Answers
Tolerance in part-making refers to the allowable limits of variation in a part's dimensions. I achieve this by carefully interpreting technical drawings and using precision tools like calipers and micrometers during the machining process. Regularly calibrating our CNC machines is also crucial to maintain accuracy.
Describe how you perform testing on the parts you create to ensure they function as intended.
How to Answer
- 1
Explain the specific testing methods you use for different parts.
- 2
Discuss how you verify measurements and tolerances.
- 3
Include any quality control processes you follow.
- 4
Mention how you document test results.
- 5
Share examples of issues you have resolved through testing.
Example Answers
I use precision measuring tools to verify dimensions and tolerances after machining each part. For functional testing, I simulate operational conditions and check for any failures. I document all results for future reference and improvement.
Don't Just Read Part Maker Questions - Practice Answering Them!
Reading helps, but actual practice is what gets you hired. Our AI feedback system helps you improve your Part Maker interview answers in real-time.
Personalized feedback
Unlimited practice
Used by hundreds of successful candidates
What knowledge do you have about lean manufacturing principles, and how would you apply them in your work?
How to Answer
- 1
Define lean manufacturing and its goals, such as reducing waste and improving efficiency.
- 2
Mention specific lean tools you are familiar with, like 5S, Kaizen, or Value Stream Mapping.
- 3
Provide a brief example of how you have applied lean principles in previous roles or how you would apply them as a Part Maker.
- 4
Emphasize the importance of continuous improvement and team involvement in lean practices.
- 5
Relate your answer to how these principles will impact production quality and delivery times.
Example Answers
I understand that lean manufacturing focuses on minimizing waste while maximizing productivity. For example, I've used 5S in my previous job to organize the workspace and improve efficiency. In my role as a Part Maker, I would implement regular Kaizen meetings to involve the team in continuous improvement.
What is your process for troubleshooting issues that arise during the part-making process?
How to Answer
- 1
Identify and define the issue clearly before attempting a fix
- 2
Gather data from the machinery, tools, and any relevant parameters
- 3
Consult documentation or previous reports to understand common issues
- 4
Engage team members for insights and collaborative problem-solving
- 5
Test solutions methodically and document the results for future reference
Example Answers
First, I identify the specific issue by analyzing where the process is failing. Then, I gather data from the machines to see if there are any error codes or anomalies. I also check past work logs to find similar issues. I often discuss problems with my team, as collaboration can lead to quicker solutions. Finally, I implement a fix and monitor the outcome closely.
Part Maker Position Details
Recommended Job Boards
CareerBuilder
www.careerbuilder.com/jobs-part-makerZipRecruiter
www.ziprecruiter.com/Jobs/Part-MakerThese job boards are ranked by relevance for this position.
Related Positions
- Cap Maker
- Box Maker
- Tube Maker
- Form Maker
- Screen Maker
- Heading Maker
- Chemical Maker
- Magnet Maker
- Cord Maker
- Puppet Maker
Similar positions you might be interested in.
Ace Your Next Interview!
Practice with AI feedback & get hired faster
Personalized feedback
Used by hundreds of successful candidates
Ace Your Next Interview!
Practice with AI feedback & get hired faster
Personalized feedback
Used by hundreds of successful candidates