Top 30 Screen Maker Interview Questions and Answers [Updated 2025]
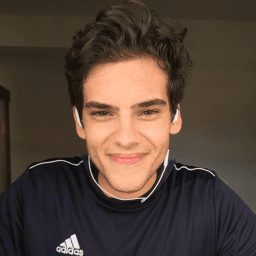
Andre Mendes
•
March 30, 2025
Navigating the interview process for a Screen Maker role can be daunting, but preparation is key to success. In this blog post, we share the most common interview questions tailored specifically for aspiring Screen Makers, complete with example answers and insightful tips on crafting your responses effectively. Whether you're a seasoned professional or just starting out, equip yourself with the knowledge to confidently tackle your next interview.
Download Screen Maker Interview Questions in PDF
To make your preparation even more convenient, we've compiled all these top Screen Makerinterview questions and answers into a handy PDF.
Click the button below to download the PDF and have easy access to these essential questions anytime, anywhere:
List of Screen Maker Interview Questions
Situational Interview Questions
If you receive multiple urgent orders for screens, how do you decide what to prioritize?
How to Answer
- 1
Assess the deadlines for each order
- 2
Determine the size and complexity of each screen
- 3
Consider the impact of each order on customer satisfaction
- 4
Look at the availability of materials and resources
- 5
Communicate with customers if needed to negotiate priorities
Example Answers
I would first check the deadlines to see which orders are the most urgent. Then I'd assess the complexity of each order, prioritizing simpler screens that can be completed quickly. Finally, I'd consider the customers’ importance and communicate with them if necessary.
Imagine you are behind on a deadline for screen production. What strategies would you employ to catch up?
How to Answer
- 1
Assess the current status of the production and identify bottlenecks
- 2
Prioritize tasks that maximize output for minimizing delays
- 3
Communicate with the team to delegate or adjust work as needed
- 4
Consider overtime or additional shifts if feasible and necessary
- 5
Review and optimize production processes to enhance efficiency
Example Answers
I would first review the production process to identify any bottlenecks and prioritize critical tasks to minimize delays. Then, I would communicate with my team to see if certain tasks could be delegated or if we could work overtime to catch up.
Don't Just Read Screen Maker Questions - Practice Answering Them!
Reading helps, but actual practice is what gets you hired. Our AI feedback system helps you improve your Screen Maker interview answers in real-time.
Personalized feedback
Unlimited practice
Used by hundreds of successful candidates
If a client provided negative feedback on a screen design you created, how would you address their concerns?
How to Answer
- 1
Listen carefully to the client’s feedback without interrupting.
- 2
Acknowledge their feelings and the validity of their concerns.
- 3
Ask clarifying questions to fully understand the issues.
- 4
Suggest adjustments or modifications based on their feedback.
- 5
Follow up with a revised design and express openness to further suggestions.
Example Answers
I would first listen to all of their feedback without cutting them off. Then, I would thank them for sharing their thoughts, and ask specific questions to clarify their concerns, such as what aspects they found unsatisfactory. After fully understanding, I would suggest ways I could adjust the design to meet their vision and send them a revised version promptly.
Suppose a new technology emerges that could improve screen quality significantly. How would you propose integrating this into your production?
How to Answer
- 1
Research the new technology to understand its benefits and challenges
- 2
Evaluate current production processes and identify integration points
- 3
Develop a pilot project to test the new technology on a smaller scale
- 4
Gather feedback from the team and adjust the integration plan as needed
- 5
Create a full roll-out strategy if the pilot is successful
Example Answers
I would start by thoroughly researching the new technology and assessing its potential impact on screen quality. Then I would analyze our existing production processes to see where we can best integrate this technology. A pilot project would allow us to test its effectiveness before a full implementation.
You have a limited budget for materials but need to produce high-quality screens. How would you prioritize your resources?
How to Answer
- 1
Identify essential materials that impact quality first.
- 2
Research affordable suppliers without compromising quality.
- 3
Invest in tools or equipment that enhance durability and reuse.
- 4
Maintain a balance between cost and quantity to optimize output.
- 5
Consider bulk purchasing for commonly used materials to save costs.
Example Answers
I would focus on sourcing high-quality base materials first, such as screens and inks, while looking for reliable local suppliers to reduce shipping costs. Then, I would invest in a good exposure unit to ensure durability for multiple uses.
If two team members disagreed on the screen design approach, how would you facilitate a resolution?
How to Answer
- 1
Listen to both perspectives fully to understand each position
- 2
Encourage a collaborative discussion to explore the pros and cons
- 3
Ask questions to clarify the design goals and requirements
- 4
Facilitate brainstorming for alternative solutions that incorporate both ideas
- 5
Aim for a consensus that aligns with project goals and user needs
Example Answers
I would start by listening to both team members' points of view to understand their reasoning. Then, I'd facilitate a discussion that allows them to explore the advantages and drawbacks of each approach. Finally, I'd help guide them toward a solution that meets our design objectives, perhaps merging elements from both ideas.
A client has very specific requirements for a screen that seem technically challenging. How would you proceed?
How to Answer
- 1
Clarify the client's requirements to ensure understanding.
- 2
Assess the technical challenges and identify key obstacles.
- 3
Propose initial ideas or alternatives that could meet the requirements.
- 4
Communicate transparently about feasibility and timelines.
- 5
Collaborate with your team for insights and solutions.
Example Answers
I would start by having a detailed discussion with the client to clarify their specific requirements and ensure I understand their vision. Then, I’d assess the technical challenges we face and identify what aspects might be difficult to achieve. Based on this, I could propose alternative approaches that still align with their goals, all while keeping the client informed about what is feasible within a reasonable timeframe.
How would you handle a situation where a new screen manufacturing technology requires your immediate adaptation?
How to Answer
- 1
Acknowledge the importance of adaptation to new technologies.
- 2
Express a willingness to learn quickly and effectively.
- 3
Mention specific resources you would utilize, such as online courses or mentorship.
- 4
Discuss your experience with previous technologies and how you adapted accordingly.
- 5
Highlight the importance of collaboration with team members during the transition.
Example Answers
I would start by researching the new technology to understand its principles and applications. I would quickly enroll in any available online courses and seek out resources from the technology provider. I have adapted to new screen technologies in the past by attending workshops and collaborating with colleagues who have experience, and I’m confident I can do it again.
If your team is underperforming, what strategies would you use to motivate them to reach production goals?
How to Answer
- 1
Conduct a one-on-one with each team member to understand their challenges.
- 2
Set clear, achievable goals and share them with the team to foster accountability.
- 3
Implement a rewards system to recognize and celebrate small wins.
- 4
Encourage open communication to allow team members to voice concerns and suggestions.
- 5
Provide training or resources that may help the team improve their skills.
Example Answers
I would start by meeting individually with team members to identify their specific challenges. Then, I'd set clear production goals together and implement a rewards program for reaching those goals, which motivates everyone.
Behavioral Interview Questions
Can you describe a project where you collaborated with designers and engineers to make a screen? What was your role in the team?
How to Answer
- 1
Identify a specific project and the product that was created.
- 2
Highlight your role clearly and the skills you utilized.
- 3
Explain how you communicated and collaborated with the team.
- 4
Mention any challenges faced and how you overcame them.
- 5
Conclude with the positive outcome of the project.
Example Answers
In my previous role, I worked on a project to develop a new touchscreen display for a smart home device. I was responsible for the technical design and worked closely with designers to ensure usability. We held regular meetings to discuss prototypes, and I provided feedback on design choices based on engineering constraints. This collaboration led to a successful launch with positive user feedback.
Tell me about a time you faced a significant challenge during the screen-making process. How did you overcome it?
How to Answer
- 1
Identify a specific challenge from your experience.
- 2
Use the STAR method: Situation, Task, Action, Result.
- 3
Focus on your thought process and decisions made.
- 4
Highlight any teamwork or collaboration involved.
- 5
Conclude with what you learned or how it improved your skills.
Example Answers
In a recent project, I had a problem where the screen prints were not aligning correctly. I realized the exposure time was too short, so I adjusted it and re-exposed the screens. After multiple tests, the alignment was perfect, resulting in a high-quality product and a satisfied client.
Don't Just Read Screen Maker Questions - Practice Answering Them!
Reading helps, but actual practice is what gets you hired. Our AI feedback system helps you improve your Screen Maker interview answers in real-time.
Personalized feedback
Unlimited practice
Used by hundreds of successful candidates
Have you ever had to lead a team of screen makers? How did you ensure all tasks were completed efficiently?
How to Answer
- 1
Describe a specific project where you led a team of screen makers.
- 2
Explain your communication strategies to ensure clarity among team members.
- 3
Discuss how you delegated tasks based on team members' strengths.
- 4
Mention any tools or systems you implemented for tracking progress.
- 5
Share the outcome of the project and lessons learned.
Example Answers
In my previous role, I led a team of screen makers for a high-volume production project. I started by holding a kickoff meeting to assign tasks based on each member's expertise. I used a shared digital project board to track progress, which helped everyone stay aligned. As a result, we completed the project ahead of schedule and received positive feedback from management.
Describe a situation where you had to adapt to a sudden change in screen specifications. What did you do?
How to Answer
- 1
Identify a specific instance where changes occurred unexpectedly
- 2
Explain how you assessed the new requirements and their impact
- 3
Describe the steps you took to modify your work plan accordingly
- 4
Highlight any collaboration with team members or stakeholders
- 5
Conclude with the outcome of the situation and what you learned
Example Answers
In my previous role, we received a last-minute change to the screen dimensions for a major project. I quickly reviewed the new specifications and assessed how they affected our existing work. I updated our design files, communicated the changes to my team, and we adjusted our production timelines. This swift response ensured we met our deadline without compromising quality.
How do you communicate with team members when there is a conflict about a design decision in screen making?
How to Answer
- 1
Listen actively to understand each person's perspective
- 2
Encourage open dialogue in a respectful manner
- 3
Focus on the project's goals and user needs to guide the discussion
- 4
Propose a brainstorming session to explore alternatives together
- 5
Aim for a collaborative resolution that satisfies all parties
Example Answers
I start by listening to everyone's viewpoints to ensure I understand the concerns. Then I encourage an open discussion where we can all share ideas. I often bring it back to what best serves our project goals, and if needed, we can brainstorm alternative designs together.
Give an example of how your attention to detail benefited a past screen-making project.
How to Answer
- 1
Think about a specific project where detail mattered.
- 2
Describe the issue you identified thanks to your attention to detail.
- 3
Explain the steps you took to resolve it and the outcome.
- 4
Highlight the positive impact on the screen-making process or final product.
- 5
Connect the experience to how you can apply it in this new role.
Example Answers
In a recent project, I noticed that the colors were mixing incorrectly due to a slight miscalibration of the printer. I took the initiative to recalibrate it and performed test prints, which ensured the final product had accurate colors and met our client's expectations perfectly.
Describe a time you managed a screen-making project from start to finish. What were the key elements of your success?
How to Answer
- 1
Choose a specific project that highlights your role as a manager.
- 2
Outline the planning process and key decisions you made.
- 3
Emphasize teamwork and communication among stakeholders.
- 4
Discuss any challenges faced and how you resolved them.
- 5
Highlight the outcomes and any metrics of success.
Example Answers
In my previous role, I led a project for a local business to design custom screens for their storefront. I created a detailed project plan, coordinated with designers and clients, and ensured the materials met quality standards. We faced a timeline challenge due to supplier delays, but I negotiated an expedited order which kept us on schedule. The project was completed successfully and resulted in a 30% increase in foot traffic for the business.
How have you used feedback from previous projects to improve your screen-making techniques?
How to Answer
- 1
Identify specific feedback you received from peers or clients.
- 2
Explain how you analyzed this feedback to understand areas of improvement.
- 3
Describe concrete changes you implemented in your screen-making process.
- 4
Provide an example of how these changes resulted in better outcomes.
- 5
Mention any ongoing methods you use for collecting feedback.
Example Answers
During my last project, I received feedback that the colors were not vibrant enough. I started experimenting with different inks and adjusted my screens to allow for better ink flow. This resulted in much brighter prints, which my clients loved.
Describe an instance where your approach to conflict resolution directly improved a work relationship with a colleague.
How to Answer
- 1
Choose a specific conflict scenario to describe
- 2
Explain your initial thoughts and feelings about the conflict
- 3
Detail the steps you took to resolve the conflict
- 4
Highlight the positive outcome and what you learned
- 5
Emphasize the improvement in the work relationship
Example Answers
In a project, I had a disagreement with a colleague over design choices. I felt strongly about my approach, but I knew I needed to listen to his perspective. I organized a meeting where we could express our views openly. By validating his ideas and combining our inputs, we created a better design. This experience not only strengthened our collaboration but also earned mutual respect.
Don't Just Read Screen Maker Questions - Practice Answering Them!
Reading helps, but actual practice is what gets you hired. Our AI feedback system helps you improve your Screen Maker interview answers in real-time.
Personalized feedback
Unlimited practice
Used by hundreds of successful candidates
What has been your most rewarding experience in screen making, and why?
How to Answer
- 1
Choose a specific project or experience you were involved in.
- 2
Describe the challenges you faced and how you overcame them.
- 3
Explain the outcome and its impact on you or others.
- 4
Reflect on what you learned and how it has shaped your skills.
- 5
Connect this experience to the role you are applying for.
Example Answers
My most rewarding experience was creating a custom design for a local band. The challenge was to translate their vision into a vibrant screen print while dealing with a tight deadline. The final product not only impressed them but also increased their merchandise sales significantly. This taught me about effective collaboration and time management, which are crucial for a screen maker.
Technical Interview Questions
What materials are commonly used in screen making, and how do they affect the final product?
How to Answer
- 1
Identify the key materials such as mesh, emulsion, and inks.
- 2
Explain how the choice of mesh affects detail and resolution.
- 3
Discuss the impact of emulsion type on durability and washability.
- 4
Mention different inks and their suitability for various surfaces.
- 5
Conclude with how these materials work together to influence the final print quality.
Example Answers
In screen making, common materials include polyester mesh, photo emulsion, and various types of inks. The mesh affects the detail and resolution of the print; for example, a finer mesh provides greater detail. The emulsion is crucial as it determines the durability of the stencil against washes. Additionally, water-based inks are great for soft fabrics, while plastisol inks are better for vibrant colors. Together, these materials dictate the final quality and durability of the printed design.
What manufacturing processes do you typically use to make screens? Can you describe one in detail?
How to Answer
- 1
Identify common screen manufacturing processes like silk screening and digital printing.
- 2
Choose one process to describe in detail.
- 3
Include specific materials and equipment used in the process.
- 4
Mention any quality control measures taken during manufacturing.
- 5
Highlight any relevant personal experience with the process.
Example Answers
I typically use silk screening for making screens. In this process, I use a fine mesh screen and a photo-emulsion to create the design. First, I coat the screen with the emulsion, then expose it to light with the design negative. After developing the screen, I use a squeegee to push ink through the screen onto the substrate. I ensure quality by inspecting each print for consistency.
Don't Just Read Screen Maker Questions - Practice Answering Them!
Reading helps, but actual practice is what gets you hired. Our AI feedback system helps you improve your Screen Maker interview answers in real-time.
Personalized feedback
Unlimited practice
Used by hundreds of successful candidates
How do you implement quality control in screen production? What steps do you take to ensure quality?
How to Answer
- 1
Define quality control checkpoints at each stage of production.
- 2
Use a standardized checklist for each screen produced.
- 3
Conduct regular training sessions for team members on quality standards.
- 4
Implement a feedback loop to address any quality issues immediately.
- 5
Document and analyze defects to prevent future occurrences.
Example Answers
In my screen production, I implement quality control by establishing checkpoints after each phase. I maintain a checklist that outlines quality expectations for each screen. Additionally, I conduct regular training to ensure my team is aware of quality standards, and we review any defects to adapt and improve our process.
Which design software do you have experience with when creating screens, and how do you use it?
How to Answer
- 1
List specific design software you are proficient in
- 2
Explain how you use each software in your design process
- 3
Mention any relevant projects you completed using the software
- 4
Highlight your ability to learn new software if needed
- 5
Be concise and confident in your response.
Example Answers
I have experience with Adobe Illustrator and CorelDRAW. I use Illustrator to create vector graphics for screen designs, as it allows for precise control over shapes and colors. I worked on a project where I designed a series of promotional screens for a local event using these tools.
What are the key technical skills that a screen maker must have?
How to Answer
- 1
Focus on skills like attention to detail and precision in work
- 2
Mention knowledge of different screen printing techniques
- 3
Highlight the importance of maintaining equipment and troubleshooting
- 4
Include familiarity with inks and substrates used in screen making
- 5
Discuss the ability to create and interpret design files accurately
Example Answers
A screen maker should have strong attention to detail to ensure high-quality prints. Knowledge of various screen printing techniques like manual and automatic printing is also essential. Moreover, being able to maintain and troubleshoot screen printing equipment is important.
Can you explain the difference between OLED and LCD screens in terms of manufacturing?
How to Answer
- 1
Start with the basic definitions of OLED and LCD screens.
- 2
Highlight the main materials used in the manufacturing of each type.
- 3
Discuss the differences in the production process for OLED vs. LCD.
- 4
Mention the implications of these differences in terms of cost and performance.
- 5
Conclude with a brief summary of the impact on consumer products.
Example Answers
OLED screens use organic compounds that emit light, while LCD screens rely on liquid crystals and a backlight. The manufacturing process for OLED involves layering organic materials on a substrate, which is generally more complex and costly than the simpler layering in LCD production, which uses glass and backlit technology. This results in OLEDs typically having better contrast and color accuracy, making them more expensive for consumers.
What safety regulations are important to consider when making screens?
How to Answer
- 1
Understand OSHA regulations related to your specific workplace.
- 2
Identify and follow proper personal protective equipment requirements.
- 3
Be aware of material safety data sheets for chemicals used.
- 4
Implement safe handling practices for sharp tools and equipment.
- 5
Ensure proper ventilation when working with solvents and chemicals.
Example Answers
When making screens, it's crucial to follow OSHA regulations to ensure a safe work environment. This includes wearing the appropriate PPE such as gloves and goggles, especially when handling chemicals.
How would you troubleshoot a production line issue that affects screen quality?
How to Answer
- 1
Identify the symptoms of the screen quality issue first.
- 2
Check the raw materials for quality and consistency.
- 3
Inspect the production equipment for any malfunctions or wear.
- 4
Review the production process for any deviations from standard operating procedures.
- 5
Engage team members to gather insights and observations on the issue.
Example Answers
First, I would analyze the screens to identify the specific quality issues, such as color inconsistencies or defects. Then, I would check the raw materials to ensure they meet our quality standards. If they are fine, I would inspect the equipment to rule out any mechanical issues. Next, I would verify if we followed all procedures correctly, and finally, I would ask my team for any additional observations that could help in pinpointing the problem.
What methods do you use to test the durability of screens after they are produced?
How to Answer
- 1
Discuss specific testing methods you use
- 2
Mention any tools or equipment that assist in testing
- 3
Explain how you ensure consistency in your tests
- 4
Include examples of common stress factors applied during tests
- 5
Highlight any industry standards you follow during testing
Example Answers
I use a combination of drop tests and pressure tests to evaluate screen durability, ensuring that each test simulates real-world conditions. For example, I drop screens from various heights onto hard surfaces to check for cracks.
How do you incorporate sustainable practices into your screen-making process?
How to Answer
- 1
Use eco-friendly inks and materials that are less harmful to the environment.
- 2
Minimize waste by reusing screens and leftover materials whenever possible.
- 3
Implement a water-saving process in cleaning screens and tools.
- 4
Choose suppliers who prioritize sustainability in their production.
- 5
Educate clients about the benefits of sustainable choices in their projects.
Example Answers
I incorporate sustainable practices by using water-based inks and reusing screens whenever I can to minimize waste.
Don't Just Read Screen Maker Questions - Practice Answering Them!
Reading helps, but actual practice is what gets you hired. Our AI feedback system helps you improve your Screen Maker interview answers in real-time.
Personalized feedback
Unlimited practice
Used by hundreds of successful candidates
Screen Maker Position Details
Recommended Job Boards
CareerBuilder
www.careerbuilder.com/jobs/screen-printingZipRecruiter
www.ziprecruiter.com/Jobs/Screen-Printing/These job boards are ranked by relevance for this position.
Related Positions
- Screen Printer
- Tube Maker
- Box Maker
- Part Maker
- Card Maker
- Heading Maker
- Form Maker
- Panel Cutter
- Cap Maker
- Stamp Pad Maker
Similar positions you might be interested in.
Ace Your Next Interview!
Practice with AI feedback & get hired faster
Personalized feedback
Used by hundreds of successful candidates
Ace Your Next Interview!
Practice with AI feedback & get hired faster
Personalized feedback
Used by hundreds of successful candidates