Top 30 Screen Printer Interview Questions and Answers [Updated 2025]
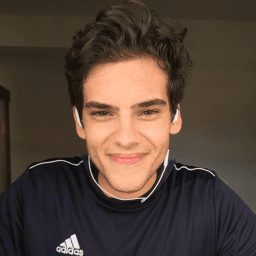
Andre Mendes
•
March 30, 2025
Preparing for a screen printer interview can be daunting, but our comprehensive guide has you covered with the most common questions employers ask. In this updated 2025 edition, you'll find example answers and insightful tips to help you respond effectively and confidently. Whether you're a seasoned professional or new to the field, this post will equip you with the knowledge to impress and succeed.
Download Screen Printer Interview Questions in PDF
To make your preparation even more convenient, we've compiled all these top Screen Printerinterview questions and answers into a handy PDF.
Click the button below to download the PDF and have easy access to these essential questions anytime, anywhere:
List of Screen Printer Interview Questions
Behavioral Interview Questions
Can you describe a time when you worked as part of a team to complete a screen printing project?
How to Answer
- 1
Think of a specific project with your team.
- 2
Explain your role and how you contributed.
- 3
Highlight teamwork and communication.
- 4
Mention any challenges faced and how they were overcome.
- 5
Conclude with the successful outcome or what you learned.
Example Answers
During a charity event, my team and I had to print 200 shirts in one day. I focused on mixing the right colors and coordinating with the team to ensure everyone had what they needed. We communicated effectively to resolve a problem with ink consistency, and by the end, we finished on time and donated the shirts successfully.
Tell me about a time when you faced a significant challenge during a printing job. How did you handle it?
How to Answer
- 1
Identify a specific printing challenge you faced.
- 2
Explain the impact of the challenge on the job or client.
- 3
Describe the steps you took to resolve the issue.
- 4
Highlight any skills or techniques you used.
- 5
Conclude with the outcome of your actions and what you learned.
Example Answers
During a large event shirt printing job, we discovered that our ink was not adhering properly to the fabric. I quickly tested alternative inks and adjusted the temperature settings on the press. I communicated with the client about the delay, and after adjusting our approach, we successfully completed the job on time without sacrificing quality. This experience taught me the importance of flexibility and thorough testing.
Don't Just Read Screen Printer Questions - Practice Answering Them!
Reading helps, but actual practice is what gets you hired. Our AI feedback system helps you improve your Screen Printer interview answers in real-time.
Personalized feedback
Unlimited practice
Used by hundreds of successful candidates
Describe a situation where you had to meet tight deadlines while ensuring quality in your work.
How to Answer
- 1
Think of a specific project that had a deadline.
- 2
Focus on how you prioritized tasks to manage your time.
- 3
Explain the quality control measures you implemented.
- 4
Discuss the outcome and how you managed stress.
- 5
Relate it back to the skills necessary for screen printing.
Example Answers
At my previous job, we had a last-minute order for custom t-shirts for an event. I created a detailed timeline to prioritize printing and quality checks. I set aside extra time for quality assurance, checking each print before moving on. We delivered on time with positive feedback from the client for the quality.
Have you ever had a disagreement with a coworker about a printing method? How did you resolve it?
How to Answer
- 1
Stay calm and professional during disagreements
- 2
Listen to your coworker’s perspective
- 3
Share your reasoning clearly and respectfully
- 4
Suggest a compromise or trial of both methods
- 5
Follow up to ensure the solution is effective
Example Answers
Yes, I had a disagreement with a coworker about the right ink for a certain fabric. I listened to their concerns about durability, and after discussing our viewpoints, we agreed to test both inks on samples to see which performed better. The tests helped us find a solution that satisfied both of us.
Can you provide an example of a time when you spotted a quality issue early in the printing process?
How to Answer
- 1
Describe a specific situation where you identified a problem.
- 2
Explain the signs that alerted you to the issue.
- 3
Detail the steps you took to address it before it escalated.
- 4
Include the outcome and how it affected the overall job.
- 5
Highlight any tools or techniques you used to monitor quality.
Example Answers
In a recent job, I noticed that the colors were not matching the sample. I realized this when the first few prints came out slightly off. I adjusted the ink mixture and communicated with the team to ensure we were on the same page. This not only saved us time but also ensured we delivered high-quality prints to the client.
Describe a time when you trained someone new in screen printing techniques. What approach did you take?
How to Answer
- 1
Choose a specific instance where you trained someone in screen printing.
- 2
Highlight the techniques you taught and why they are important.
- 3
Explain your training method, such as hands-on practice or demonstrations.
- 4
Include any challenges faced and how you overcame them.
- 5
Mention the positive outcome of the training for the new employee.
Example Answers
I trained a new hire by first demonstrating screen setup and ink mixing. I allowed them to practice while I guided them, ensuring they understood each step. After a few attempts, they successfully printed their first design, which boosted their confidence.
Have you ever introduced a new technique or tool that improved the screen printing process? What was it?
How to Answer
- 1
Identify a specific technique or tool you used.
- 2
Explain how it was implemented in the workflow.
- 3
Describe the measurable improvements achieved.
- 4
Mention any challenges faced and how you overcame them.
- 5
Highlight teamwork or collaboration, if applicable.
Example Answers
I introduced a new automatic registration system that improved our alignment accuracy. After training the team, we noticed a 30% decrease in misprints.
How do you handle feedback from clients about your printed products?
How to Answer
- 1
Listen carefully to the client's feedback without interrupting.
- 2
Acknowledge the feedback and thank the client for sharing their thoughts.
- 3
Assess the feedback to determine if it's actionable and what changes can be made.
- 4
Communicate any necessary adjustments clearly to the client and timeline for changes.
- 5
Follow up with the client after changes are made to ensure satisfaction.
Example Answers
I listen to the client's feedback carefully and thank them for their input. I then analyze the feedback to see what I can implement and I communicate with them about any changes we plan to make.
How have you collaborated with designers to achieve the desired printing outcome?
How to Answer
- 1
Discuss specific projects where you worked directly with designers
- 2
Mention tools or techniques used for communication
- 3
Highlight how you incorporated designer feedback into the printing process
- 4
Explain how you helped solve challenges together
- 5
Share a specific example that demonstrates a successful collaboration
Example Answers
In my last job, I collaborated with a designer on a t-shirt project. We used digital mockups to visualize the prints, and I provided feedback on color adjustments based on print tests. This collaboration led to a final product that both the designer and our client loved.
Technical Interview Questions
What types of screen printing equipment are you most familiar with, and what maintenance tasks do you perform?
How to Answer
- 1
List the screen printing machines you have experience with, like manual presses or automatic presses.
- 2
Mention specific brands or models if relevant to show your expertise.
- 3
Describe routine maintenance tasks such as cleaning screens, checking ink consistency, and lubricating parts.
- 4
Highlight your understanding of proper setup and adjustments for quality prints.
- 5
Emphasize safety protocols when handling equipment.
Example Answers
I have extensive experience with both manual and automatic screen printing presses, specifically with the M&R Challenger series. Routine maintenance I perform includes cleaning the screens after each job, inspecting and lubricating the squeegee blades, and checking the registration marks before printing.
Explain the process of preparing screens for printing. What steps are involved?
How to Answer
- 1
Start by cleaning the screens to remove any old emulsion or contaminants
- 2
Coat the screen evenly with photo emulsion using a scoop coater
- 3
Let the emulsion dry in a dark area to avoid exposure to light
- 4
Expose the screen with your design using a light source and follow the timing based on emulsion type
- 5
Wash out the screen to reveal the design, ensuring proper development
Example Answers
To prepare screens for printing, first, clean them thoroughly to ensure no old emulsion remains. Then, using a scoop coater, evenly apply a layer of photo emulsion. Allow the screen to dry away from light. Next, expose the screen to a light source with your design for the required time. Finally, wash the screen to develop the image and prepare it for printing.
Don't Just Read Screen Printer Questions - Practice Answering Them!
Reading helps, but actual practice is what gets you hired. Our AI feedback system helps you improve your Screen Printer interview answers in real-time.
Personalized feedback
Unlimited practice
Used by hundreds of successful candidates
What are the different types of inks used in screen printing, and how do they affect the final product?
How to Answer
- 1
Start by mentioning the main types of inks such as plastisol, water-based, and discharge.
- 2
Explain the properties of each ink type, such as opacity, feel, and environmental impact.
- 3
Discuss how ink choice can affect durability, washability, and color vibrancy.
- 4
Provide examples of specific applications for each type of ink.
- 5
Conclude with how the type of ink might influence customer preferences.
Example Answers
There are three main types of inks used in screen printing: plastisol, water-based, and discharge inks. Plastisol is the most common; it provides great opacity and durability but can feel plasticky. Water-based inks are more eco-friendly and result in a softer feel but may not be as vibrant on dark fabrics. Discharge inks remove the dye from fabric and create a soft print but require specific conditions for best results.
How do you prepare artwork for screen printing, and what software do you typically use?
How to Answer
- 1
Start by discussing how to select the right file format for printing, such as using vector files.
- 2
Mention the importance of using proper resolution and color settings to ensure quality outputs.
- 3
Talk about the software commonly used, like Adobe Illustrator or CorelDRAW, for creating and editing designs.
- 4
Explain the process of creating separations for different colors in the design.
- 5
Wrap up with how to save the final design in a format suitable for the screen printing process.
Example Answers
I prepare artwork for screen printing by ensuring I use vector graphics, typically in Adobe Illustrator. I set the resolution to 300 DPI and ensure colors are in RGB when designing. I create color separations to prepare for printing, and I save the final files in PDF or AI format.
What common issues may arise during the printing process, and how do you troubleshoot them?
How to Answer
- 1
Identify common problems such as ink smudging, misalignment, and clogged screens.
- 2
Explain how to diagnose each issue step-by-step.
- 3
Discuss preventive measures to avoid these issues in the future.
- 4
Mention the importance of equipment maintenance and calibration.
- 5
Provide specific examples to illustrate your troubleshooting process.
Example Answers
A common issue is ink smudging. To troubleshoot, I check if the ink is too thin, adjust its viscosity, and ensure the drying time is adequate.
What safety precautions do you take while operating screen printing equipment?
How to Answer
- 1
Always wear personal protective equipment such as gloves and masks.
- 2
Ensure proper ventilation in the workspace to avoid inhaling fumes.
- 3
Regularly inspect equipment for any faults or safety hazards.
- 4
Keep work area clean and free of clutter to prevent accidents.
- 5
Follow manufacturer instructions for operating and maintaining machines.
Example Answers
I always wear gloves and a mask to protect myself from chemicals and fumes while screen printing. I also make sure the area is well-ventilated.
Can you explain the difference between emulsion and direct-to-garment printing methods?
How to Answer
- 1
Start by defining both printing methods clearly.
- 2
Highlight the main difference in the process and application.
- 3
Mention the types of materials best suited for each method.
- 4
Discuss the typical uses or advantages of each printing technique.
- 5
Conclude with a brief comparison of durability or finish quality.
Example Answers
Emulsion printing involves creating a stencil on a screen with photo-emulsion, suitable for large batch prints and is often used for graphic t-shirts. Direct-to-garment printing, on the other hand, uses inkjet technology to print directly onto the fabric, best for detailed designs and small orders. Emulsion is more durable, while DTG allows for vibrant colors and complex patterns.
How do you ensure color accuracy when mixing inks for screen printing?
How to Answer
- 1
Always use a standardized color mixing system or formula for consistency
- 2
Perform test prints after mixing to check the accuracy of colors
- 3
Use a color measuring tool like a spectrophotometer if available
- 4
Maintain a clean working environment to avoid contamination of inks
- 5
Document all ink mixtures and their corresponding outcomes for future reference
Example Answers
I ensure color accuracy by following a standardized formula for mixing inks. After mixing, I perform a test print to verify the color matches the original sample.
Which printing techniques do you find most effective for bulk orders and why?
How to Answer
- 1
Identify key printing techniques like screen printing and digital printing.
- 2
Explain the advantages of each method for bulk orders.
- 3
Discuss speed, cost effectiveness, and scalability.
- 4
Mention any specific experiences or results you've achieved using these techniques.
- 5
Be concise but informative, focusing on practicality.
Example Answers
I find screen printing to be the most effective for bulk orders because it offers a high speed of production and lower costs per unit. I've completed orders of over 500 pieces in just a few hours, maintaining quality throughout.
What steps do you take to maintain your screen printing equipment?
How to Answer
- 1
Regularly clean the screens using appropriate solvents after each use.
- 2
Check and tighten all bolts and connections on the printing presses weekly.
- 3
Lubricate moving parts monthly to ensure smooth operation.
- 4
Inspect squeegees for wear and replace them as needed.
- 5
Perform a thorough maintenance check before starting new projects.
Example Answers
I clean the screens with proper solvents after every use, ensuring no ink residue affects the next print. I also check the connections on my equipment weekly and lubricate parts monthly.
Don't Just Read Screen Printer Questions - Practice Answering Them!
Reading helps, but actual practice is what gets you hired. Our AI feedback system helps you improve your Screen Printer interview answers in real-time.
Personalized feedback
Unlimited practice
Used by hundreds of successful candidates
How do you choose suppliers for inks and materials? What factors do you consider?
How to Answer
- 1
Research potential suppliers thoroughly before making a decision
- 2
Consider the quality and consistency of their products
- 3
Evaluate their pricing and payment terms
- 4
Look for suppliers with good customer service and support
- 5
Check reviews or testimonials from other customers in the industry
Example Answers
I choose suppliers by first researching their reputation and the quality of their inks. I compare prices but prioritize product quality. I also check if they have responsive customer service.
Situational Interview Questions
If a customer was unhappy with the color rendition of their printed shirts, how would you address their concerns?
How to Answer
- 1
Listen actively to the customer's feedback and concerns.
- 2
Acknowledge their feelings and apologize for the inconvenience.
- 3
Ask for specific details about the color issues they are experiencing.
- 4
Explain the process used for color matching and printing.
- 5
Offer a solution, such as reprinting the shirts or providing a discount.
Example Answers
I would listen closely to the customer's concerns and acknowledge their disappointment. I'd ask them to describe the specific color issues they faced and then explain how we approach color matching. Finally, I'd offer to reprint their shirts at no additional cost.
Imagine you're facing an unexpected machinery breakdown during a large order. What steps would you take?
How to Answer
- 1
Stay calm and assess the situation immediately
- 2
Inform the team and communicate the issue clearly
- 3
Review the troubleshooting manual or guide for quick fixes
- 4
Contact technical support or maintenance if immediate resolution is not possible
- 5
Consider backup plans, like switching to another machine or rescheduling the order if needed
Example Answers
First, I would assess the breakdown to understand the severity and gather necessary details. Then, I would inform my team about the situation, ensuring that everyone is on the same page. I would immediately check the troubleshooting manual for any potential quick solutions. If I can't solve it, I would contact technical support for help. If the delay is significant, I would discuss with my supervisor about potential backup options, like using another printer.
Don't Just Read Screen Printer Questions - Practice Answering Them!
Reading helps, but actual practice is what gets you hired. Our AI feedback system helps you improve your Screen Printer interview answers in real-time.
Personalized feedback
Unlimited practice
Used by hundreds of successful candidates
If you noticed a frequent error occurring in your printing setup, how would you approach improving the process?
How to Answer
- 1
Identify the root cause of the error through observation and analysis
- 2
Consult with team members to gather insights on the issue
- 3
Implement small changes to the setup and monitor results
- 4
Document the process improvements for future reference
- 5
Regularly review the setup to ensure consistency and effectiveness
Example Answers
I would first analyze the setup to pinpoint the error's source, then discuss it with my colleagues for different perspectives. After identifying potential fixes, I would test small adjustments to see if they resolve the issue. Finally, I would document any successful changes for future improvements.
You have multiple orders due on the same day. How would you prioritize your tasks?
How to Answer
- 1
Assess the urgency of each order based on the deadline and client importance.
- 2
Determine the complexity and time required for each order.
- 3
Prioritize orders with the nearest deadlines first.
- 4
Communicate with your team to delegate or seek help if necessary.
- 5
Keep customers informed about their order status as you progress.
Example Answers
I would first list all the orders and check which ones are due first and which clients are most critical. Then, I would tackle the quicker jobs first and ask for help on the larger orders if needed.
If after the first print run you discover misalignment issues, what steps would you take to rectify it?
How to Answer
- 1
Stop the print job immediately to prevent further issues
- 2
Inspect the printed material to determine the misalignment cause
- 3
Adjust the screen or equipment setup as needed to correct alignment
- 4
Run a test print to verify that the adjustments worked
- 5
Document the process for future reference to avoid recurrence
Example Answers
First, I would halt the printing process to prevent any further misalignment. Then, I would inspect both the printed output and the equipment to identify the exact cause. After that, I would make the necessary adjustments to the screen or machine. I would run a test print to ensure everything is aligned correctly before continuing with the production.
If you were assigned a project using a technique you're unfamiliar with, how would you prepare?
How to Answer
- 1
Identify the technique and its requirements clearly
- 2
Research the technique through online tutorials or courses
- 3
Seek advice from more experienced colleagues or mentors
- 4
Practice the technique in a low-stakes environment
- 5
Review past projects to understand similar techniques used
Example Answers
I would start by researching the technique online, looking for tutorials that break it down. Then, I'd reach out to a colleague who has experience with it to gain insights. Finally, I'd practice on some test materials to ensure I'm comfortable before starting the actual project.
What would you do if you realized a significant order would not be completed by the deadline?
How to Answer
- 1
Assess the current status of the order immediately.
- 2
Communicate proactively with your supervisor and the customer about the delay.
- 3
Work on a solution by reallocating resources or extending working hours if necessary.
- 4
Document the reasons for the delay to learn and improve future processes.
- 5
Keep the client informed throughout the resolution process to maintain trust.
Example Answers
I would first check the production status and identify how far behind we are. Then, I would inform my supervisor and reach out to the customer to discuss the delay and our plan to resolve it. If needed, I would assign more workers to the order or work overtime to complete it as soon as possible.
If you found a defect on a batch of prints, what actions would you take regarding the completed order?
How to Answer
- 1
Identify the defect type and severity quickly.
- 2
Communicate the issue to the supervisor or team lead immediately.
- 3
Review the production process to determine how the defect occurred.
- 4
Propose a solution or corrective actions to prevent future defects.
- 5
Ensure clear documentation of the incident and actions taken.
Example Answers
I would first assess the defect to understand its impact and severity. Then, I would notify my supervisor about the issue and review how it happened during production. Following that, I would suggest adjustments to our processes to prevent it from happening again and document everything for future reference.
If you were in a team dealing with a particularly challenging and intricate print job, how would you contribute?
How to Answer
- 1
Talk about assessing the situation and identifying challenges.
- 2
Mention collaborating with team members for ideas and solutions.
- 3
Describe how you would use your skills to contribute effectively.
- 4
Include a focus on communication to keep everyone on track.
- 5
Highlight your willingness to help and support others in the team.
Example Answers
I would begin by assessing the specific challenges of the print job, then collaborate closely with my teammates to brainstorm solutions. I'd share my expertise in color matching to help achieve the desired outcome.
What steps would you take if you realize that some materials are running low unexpectedly?
How to Answer
- 1
Check the inventory immediately to confirm which materials are low.
- 2
Notify the supervisor or manager about the issue as soon as possible.
- 3
Place an order for the necessary materials if authorized to do so.
- 4
Look for backup materials that can be used in the meantime.
- 5
Adjust the printing schedule if necessary to avoid delays.
Example Answers
First, I would check the inventory to see which materials are low. Then, I would immediately inform my supervisor about the situation. If I'm authorized, I’d place an order for the materials or ask for assistance with that.
Don't Just Read Screen Printer Questions - Practice Answering Them!
Reading helps, but actual practice is what gets you hired. Our AI feedback system helps you improve your Screen Printer interview answers in real-time.
Personalized feedback
Unlimited practice
Used by hundreds of successful candidates
Screen Printer Position Details
Salary Information
Recommended Job Boards
These job boards are ranked by relevance for this position.
Related Positions
- Carbon Printer
- Screen Maker
- Machine Printer
- Print Washer
- Flexographic Press Operator
- Machine Stamper
- Sign Painter
- Wire Drawer
- Paper Stripper
- Machine Hand
Similar positions you might be interested in.
Ace Your Next Interview!
Practice with AI feedback & get hired faster
Personalized feedback
Used by hundreds of successful candidates
Ace Your Next Interview!
Practice with AI feedback & get hired faster
Personalized feedback
Used by hundreds of successful candidates