Top 30 Flexographic Press Operator Interview Questions and Answers [Updated 2025]
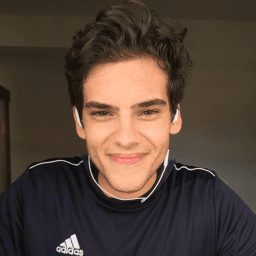
Andre Mendes
•
March 30, 2025
Preparing for a Flexographic Press Operator interview can be daunting, but we're here to help you succeed. In this post, we cover the most common interview questions for this role, providing insightful example answers and practical tips on how to respond effectively. Whether you're a seasoned professional or just starting, you'll gain valuable insights to confidently navigate your upcoming interview. Dive in to master the art of impressing potential employers!
Download Flexographic Press Operator Interview Questions in PDF
To make your preparation even more convenient, we've compiled all these top Flexographic Press Operatorinterview questions and answers into a handy PDF.
Click the button below to download the PDF and have easy access to these essential questions anytime, anywhere: