Top 28 Box Maker Interview Questions and Answers [Updated 2025]
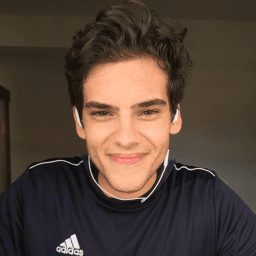
Andre Mendes
•
March 30, 2025
Are you gearing up for a Box Maker interview and want to stand out among the candidates? This blog post is your go-to resource for the most common interview questions asked in the Box Maker role. Dive in to explore example answers and practical tips that will help you respond with confidence and precision. Prepare to impress your interviewers with insights and strategies that elevate your performance.
Download Box Maker Interview Questions in PDF
To make your preparation even more convenient, we've compiled all these top Box Makerinterview questions and answers into a handy PDF.
Click the button below to download the PDF and have easy access to these essential questions anytime, anywhere:
List of Box Maker Interview Questions
Behavioral Interview Questions
Tell me about a time you faced a significant issue while making boxes. How did you resolve it?
How to Answer
- 1
Identify a specific issue related to box making.
- 2
Explain the steps you took to analyze the problem.
- 3
Describe the solution you implemented.
- 4
Highlight the outcome and any lessons learned.
- 5
Keep your story concise and focused on your contributions.
Example Answers
Once, we received a shipment of defective cardboard that affected our production. I quickly gathered the team to assess the impact and we decided to redirect our efforts towards alternative materials we had in stock. We completed the orders with minimal delay and I learned the importance of having contingency plans.
Can you describe a time when you successfully worked with a team to complete a challenging box-making project?
How to Answer
- 1
Think of a specific project where teamwork was essential.
- 2
Highlight your role and contributions to the team effort.
- 3
Mention challenges faced and how the team overcame them.
- 4
Include the positive outcomes of the project.
- 5
Use the STAR method: Situation, Task, Action, Result.
Example Answers
In a recent project, our team needed to design custom boxes for a large client. I was responsible for coordinating the materials and ensuring everyone had what they needed. We faced a tight deadline, but we worked overtime and communicated effectively. As a result, we delivered the boxes ahead of schedule, receiving praise from the client for our quality.
Don't Just Read Box Maker Questions - Practice Answering Them!
Reading helps, but actual practice is what gets you hired. Our AI feedback system helps you improve your Box Maker interview answers in real-time.
Personalized feedback
Unlimited practice
Used by hundreds of successful candidates
Give an example of how paying attention to detail impacted the quality of your box-making work.
How to Answer
- 1
Think of a specific project where details mattered.
- 2
Describe what the details were and how you noticed them.
- 3
Explain how your focus on those details improved the end product.
- 4
Use metrics or feedback to highlight the impact of your work.
- 5
Keep it concise while ensuring clarity and relevance.
Example Answers
In my last project, I noticed that slight misalignments in the box corners led to weak joints. I measured each cut with precision and double-checked the dimensions, resulting in a stronger, more durable box that received excellent customer feedback.
Describe a situation where you had to prioritize safety while working in the box-making area.
How to Answer
- 1
Identify a specific safety protocol you followed.
- 2
Explain the potential risk involved in not following safety.
- 3
Describe your actions taken to mitigate risk.
- 4
Highlight the positive outcome for you and your team.
- 5
Mention any feedback or learning from the experience.
Example Answers
In my previous job, I noticed that the blades on the cutting machine needed to be replaced. I immediately reported this to my supervisor to prioritize safety and prevent injuries. Because of this, we avoided a serious accident, and the blades were replaced promptly. My team appreciated the proactive approach.
What strategies do you use to manage your time effectively during busy periods in the box-making process?
How to Answer
- 1
Prioritize tasks based on deadlines and importance.
- 2
Break down larger tasks into smaller, manageable steps.
- 3
Use a timer or stopwatch to keep track of tasks and maintain focus.
- 4
Delegate tasks to team members when appropriate to share the workload.
- 5
Regularly review progress to adjust strategies as needed.
Example Answers
During busy periods, I prioritize tasks by their deadlines, tackling the most urgent box orders first. I also break down each order into steps to make the process smoother.
Have you ever dealt with a client who had an issue with their order? What steps did you take to address their concern?
How to Answer
- 1
Listen carefully to the client's issue to fully understand it
- 2
Acknowledge their concern and empathize with their situation
- 3
Provide a clear explanation of the steps you can take
- 4
Act quickly to resolve the issue and keep the client informed
- 5
Follow up after resolution to ensure satisfaction and build trust
Example Answers
I once had a client who received the wrong size box. I listened to their concerns, apologized for the mistake, and explained that I would resend the correct size immediately. I kept them updated throughout the process and followed up once they received the new order to ensure everything was right.
What is the most important lesson you have learned in your box-making career that has improved your skills?
How to Answer
- 1
Reflect on a specific challenge you faced in box-making.
- 2
Identify a key skill or technique that improved from that experience.
- 3
Explain how this lesson impacts your work today.
- 4
Relate it to a real-world application in box-making.
- 5
Keep your answer concise and focus on a single lesson.
Example Answers
One important lesson I learned is the value of precision in measurements. Early in my career, I made several boxes that didn't fit properly due to inaccurate cuts. I now ensure I double-check all measurements before cutting, which has greatly improved the quality of my work.
Can you give an example of a time you took the initiative to improve a process in box making?
How to Answer
- 1
Identify a specific process you improved
- 2
Explain the problem you saw and why it mattered
- 3
Describe the action you took to initiate improvement
- 4
Share the positive outcome or results of your action
- 5
Use specific metrics or feedback if possible
Example Answers
In my previous job, I noticed that we were wasting a lot of time waiting for the glue to dry on our boxes. I researched faster-drying adhesives and proposed a trial. After implementing it, we reduced drying time by 30%, which improved our overall efficiency.
Tell me about a time you received constructive criticism. How did you respond and what changes did you make?
How to Answer
- 1
Choose a specific example where the feedback had a clear impact.
- 2
Explain your initial reaction honestly but professionally.
- 3
Detail the steps you took to implement changes based on the feedback.
- 4
Highlight the positive outcomes of these changes.
- 5
Keep the tone positive, showing growth from the experience.
Example Answers
In my previous job, my supervisor pointed out that my box designs were sometimes too complex for production. Initially, I felt defensive, but I took time to review the designs with my team. I simplified my designs by focusing on essential features, which improved our production speed by 20%.
Don't Just Read Box Maker Questions - Practice Answering Them!
Reading helps, but actual practice is what gets you hired. Our AI feedback system helps you improve your Box Maker interview answers in real-time.
Personalized feedback
Unlimited practice
Used by hundreds of successful candidates
Technical Interview Questions
What types of materials are commonly used in box making, and how do their properties affect the quality of the final product?
How to Answer
- 1
Identify common materials such as cardboard, paperboard, and plastic.
- 2
Explain the strength and durability of each material and its suitability for different products.
- 3
Mention flexibility, weight, and cost-effectiveness as factors in material selection.
- 4
Discuss environmental impact and recyclability as modern considerations.
- 5
Provide examples of specific box types and their material advantages.
Example Answers
Common materials in box making include cardboard and paperboard. Cardboard is strong and lightweight, making it ideal for shipping boxes, while paperboard offers a smooth surface for printing, suitable for retail packaging.
Describe the box-making machinery you are familiar with and your experience using them.
How to Answer
- 1
List specific types of box-making machines you have operated, such as die-cutters or gluers.
- 2
Mention any relevant experience you have, including the types of materials you worked with.
- 3
Share specific tasks you performed using the machinery, like setup, operation, or maintenance.
- 4
Highlight any training or certifications you have related to box-making machinery.
- 5
Emphasize your ability to troubleshoot issues that arise during operation.
Example Answers
I am familiar with die-cutting and automatic gluing machines. I operated a BOBST die-cutter for two years, where I was responsible for setup and production runs using corrugated cardboard. I also completed a training course on troubleshooting common issues.
Don't Just Read Box Maker Questions - Practice Answering Them!
Reading helps, but actual practice is what gets you hired. Our AI feedback system helps you improve your Box Maker interview answers in real-time.
Personalized feedback
Unlimited practice
Used by hundreds of successful candidates
How do you approach the layout design for a new box order? What factors do you consider?
How to Answer
- 1
Identify the dimensions and shape of the product that will be packaged.
- 2
Consider the materials available and their properties, like rigidity and cost.
- 3
Analyze shipping constraints, such as weight limits and stacking requirements.
- 4
Think about branding elements that need to be included in the design.
- 5
Ensure that the design allows for efficient production and minimizes waste.
Example Answers
I start by measuring the product to understand its dimensions and shape. Then, I choose materials based on their strength and cost-effectiveness. I also consider how the box will be shipped, ensuring it meets any weight limits and can be stacked properly. Finally, I make sure to incorporate any branding elements the client wants.
What quality control measures do you implement in your box-making process?
How to Answer
- 1
Start by mentioning inspection of raw materials for defects.
- 2
Discuss in-process checks at various stages of box assembly.
- 3
Include final inspection steps before packaging.
- 4
Emphasize adherence to specifications and standards.
- 5
Mention any feedback loop for continuous improvement.
Example Answers
I inspect the raw materials for any defects before starting. During the assembly, I conduct in-process checks to ensure that each box meets our standards. Finally, I have a final inspection checklist to verify that the boxes are crafted correctly before they are packaged.
Can you explain the process of die-cutting in box making and its importance?
How to Answer
- 1
Start with a definition of die-cutting specific to box making.
- 2
Describe the tools and materials used in the process.
- 3
Explain the steps involved in die-cutting a box design.
- 4
Mention the benefits of die-cutting for efficiency and precision.
- 5
Conclude with how die-cutting impacts the overall quality of the box.
Example Answers
Die-cutting is a process where shapes are cut from materials using a die. We use steel rules or blades mounted on a base to create precise cuts. First, we design the box layout, then place the material on the cutting machine. This allows us to produce boxes quickly and accurately, ensuring each box is uniform, which is crucial for production efficiency.
What troubleshooting steps do you follow when a box-making machine malfunctions?
How to Answer
- 1
Identify the error: Check for error codes or indicators on the machine.
- 2
Inspect physical components: Look for jams, worn parts, or misalignments.
- 3
Test power and connections: Ensure the machine is powered and connections are secure.
- 4
Consult the manual: Reference troubleshooting guidelines specific to the machine model.
- 5
Perform a reset: If necessary, reset the machine to see if the issue resolves.
Example Answers
First, I check for any error codes displayed on the machine. Then, I inspect for jams or misalignments in the components before testing power connections. If the problem persists, I consult the manual for specific troubleshooting steps.
What industry standards do you keep in mind while creating boxes, especially for specific customers or products?
How to Answer
- 1
Discuss specific packaging regulations relevant to the product, like food safety.
- 2
Mention different materials used for different products, like corrugated for heavier items.
- 3
Include customer preferences and branding guidelines in the design process.
- 4
Address sustainability standards, such as using recyclable materials when possible.
- 5
Talk about testing and quality assurance methods to ensure durability and functionality.
Example Answers
I follow packaging regulations such as FDA guidelines for food items and ensure the materials are BPA-free. For instance, when creating boxes for organic products, I choose biodegradable materials to align with brand values.
How do you manage the costs of materials in box making without compromising on quality?
How to Answer
- 1
Evaluate the cost versus quality of every material used.
- 2
Source materials from multiple suppliers to find the best prices.
- 3
Use design principles that reduce waste and lower material use.
- 4
Invest in training for your team on efficient production techniques.
- 5
Regularly review inventory to avoid overstock and cut costs.
Example Answers
I manage costs by regularly comparing material prices from different suppliers and using the one that offers the best balance of cost and quality. I also focus on designing efficient boxes that minimize waste.
Describe how you would create a prototype box design for a new product.
How to Answer
- 1
Identify the product size and shape requirements.
- 2
Consider the materials that will be used for the box.
- 3
Sketch a few design ideas to visualize the concept.
- 4
Create a simple prototype using materials at hand.
- 5
Test the prototype for functionality and ease of use.
Example Answers
First, I would measure the dimensions of the product to ensure a perfect fit. Then, I would choose cardboard for its sturdiness, sketch a basic design, and create a prototype. After that, I would test it by placing the product inside to check if it holds securely.
Situational Interview Questions
If you have a shipment of boxes that doesn't meet quality standards, what steps would you take to address this issue?
How to Answer
- 1
Identify the specific quality issues with the boxes.
- 2
Communicate with the shipping team to check quality control procedures.
- 3
Isolate the defective boxes to prevent further distribution.
- 4
Implement corrective actions to fix the production process if needed.
- 5
Document the issue for future reference and improvements.
Example Answers
First, I would identify the specific quality issues and assess the extent of the problem. Then, I'd communicate with the shipping team to ensure everyone is aware of the situation and stop further distribution of the affected boxes. After isolating the defective items, I would look into what caused the issue and implement corrective measures to prevent it from happening again.
Imagine you have to work with a new team who has different box-making techniques. How would you approach this situation?
How to Answer
- 1
Listen actively to understand their techniques
- 2
Ask questions to clarify their methods and goals
- 3
Share your own techniques for collaboration
- 4
Find common ground to create a unified approach
- 5
Be flexible and open to learning from their experience
Example Answers
I would listen closely to my new team members to understand their box-making techniques. Asking questions would help clarify how they work, and I would be open to sharing my own methods for collaboration. Together, we could find common ground and develop a process that combines our strengths.
Don't Just Read Box Maker Questions - Practice Answering Them!
Reading helps, but actual practice is what gets you hired. Our AI feedback system helps you improve your Box Maker interview answers in real-time.
Personalized feedback
Unlimited practice
Used by hundreds of successful candidates
If you encounter a disagreement about manufacturing techniques with a colleague, how would you handle the situation?
How to Answer
- 1
Listen actively to your colleague's perspective
- 2
Stay calm and respectful throughout the discussion
- 3
Use data to support your point of view
- 4
Seek a compromise that leverages both techniques
- 5
Suggest a trial of both methods to see which works better
Example Answers
I would start by listening carefully to my colleague's perspective and understand their reasoning. Then, I would calmly present my thoughts and support them with relevant data. If we still disagree, I would propose a trial run of both techniques to objectively evaluate the results and reach a consensus.
You receive an order with unclear specifications. How do you handle this with the client?
How to Answer
- 1
Ask clarifying questions to understand the client's needs
- 2
Restate what you think the order is to confirm accuracy
- 3
Provide examples or options to help them specify their needs
- 4
Be polite and professional in all communications
- 5
Document the conversation to avoid future misunderstandings
Example Answers
I would start by asking the client specific questions about the order to clarify their needs. For example, I might say, 'Can you please elaborate on the dimensions and materials you prefer?' After gathering information, I would restate the details to ensure we're on the same page.
You are managing multiple orders with tight deadlines. How do you prioritize your tasks to ensure timely delivery?
How to Answer
- 1
Assess the due dates of each order starting with the closest deadlines.
- 2
Evaluate the complexity and time required for each order.
- 3
Communicate with team members to delegate tasks if possible.
- 4
Keep a written list or digital tracker to visualize priorities.
- 5
Be flexible and ready to adapt to any sudden changes in order requirements.
Example Answers
I first identify which orders are due soonest and focus on those. Then, I consider the complexity and allocate my time accordingly. If needed, I communicate with my team to delegate simpler tasks and keep everything on track.
You notice a team member not following safety protocols. How would you address this situation?
How to Answer
- 1
Stay calm and approach the team member privately
- 2
Clearly explain the importance of safety protocols
- 3
Ask if they need help understanding the protocols
- 4
Encourage them to adhere to the rules for everyone's safety
- 5
Report the issue to a supervisor if the behavior continues
Example Answers
I would talk to the team member privately and explain why safety protocols are crucial for everyone. I would ask if they have any questions or need assistance with the procedures.
If you were tasked with improving the efficiency of the box-making process, what innovative changes would you consider?
How to Answer
- 1
Identify bottlenecks in the current process that slow down production
- 2
Consider automation options for repetitive tasks to reduce manual labor
- 3
Explore alternative materials that may speed up production without compromising quality
- 4
Implement a Just-In-Time inventory system to minimize waste and storage costs
- 5
Gather worker feedback to understand practical challenges and potential improvements
Example Answers
I would analyze the workflow to find bottlenecks, then integrate automated cutting machines to speed up the process and reduce errors.
How would you handle a situation where you are asked to expedite a box order that was just placed?
How to Answer
- 1
Assess the current workload and identify any critical tasks that can be delayed.
- 2
Communicate with your supervisor about the urgency and resources needed.
- 3
Prioritize the expedited order without compromising quality.
- 4
Consider any additional help or machines that can speed up the process.
- 5
Keep the customer updated about the progress and estimated delivery time.
Example Answers
I would first assess my current workload and see if I could adjust any tasks. Then, I'd communicate with my supervisor to ensure we have the resources to expedite the order. I'd focus on quality while pushing to complete the order as quickly as possible.
If you have developed a new technique that improves box making, how would you share this knowledge with your team?
How to Answer
- 1
Prepare a clear presentation of your technique and its benefits.
- 2
Offer a hands-on demonstration to show the technique in action.
- 3
Create instructional materials like guides or videos for reference.
- 4
Encourage feedback from the team for continuous improvement.
- 5
Schedule regular follow-ups to discuss the technique's impact and gather insights.
Example Answers
I would prepare a clear presentation outlining the new technique and its benefits, followed by a hands-on demonstration to the team. Afterwards, I'd provide instructional materials to help everyone understand it better.
Box Maker Position Details
Salary Information
Average Salary
$15,304
Source: Talent.com
Recommended Job Boards
CareerBuilder
www.careerbuilder.com/jobs-box-makerZipRecruiter
www.ziprecruiter.com/Jobs/Box-MakerThese job boards are ranked by relevance for this position.
Related Positions
- Wood Box Maker
- Box Bender
- Basket Maker
- Tube Maker
- Screen Maker
- Part Maker
- Form Maker
- Buttoner
- Cap Maker
- Card Maker
Similar positions you might be interested in.
Ace Your Next Interview!
Practice with AI feedback & get hired faster
Personalized feedback
Used by hundreds of successful candidates
Ace Your Next Interview!
Practice with AI feedback & get hired faster
Personalized feedback
Used by hundreds of successful candidates