Top 30 Wood Box Maker Interview Questions and Answers [Updated 2025]
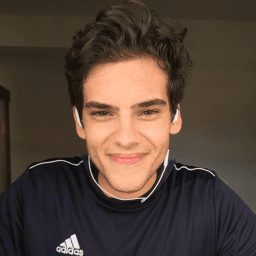
Andre Mendes
•
March 30, 2025
Embarking on a journey to become a successful Wood Box Maker? Our updated guide equips you with the most common interview questions for this creative role, complete with insightful example answers and effective tips. Dive in to enhance your preparation, boost your confidence, and stand out in your interviews. Whether you're a seasoned artisan or a budding craftsman, this post is your key to acing that interview.
Download Wood Box Maker Interview Questions in PDF
To make your preparation even more convenient, we've compiled all these top Wood Box Makerinterview questions and answers into a handy PDF.
Click the button below to download the PDF and have easy access to these essential questions anytime, anywhere: