Top 29 Box Bender Interview Questions and Answers [Updated 2025]
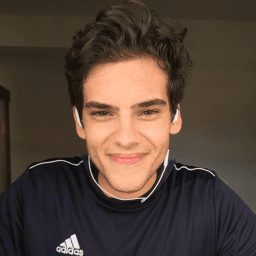
Andre Mendes
•
March 30, 2025
Preparing for a Box Bender interview? Our latest blog post is your go-to guide for acing it. Dive into the most common questions asked for this role, complete with example answers and expert tips to help you respond effectively. Whether you're a seasoned professional or new to the industry, this comprehensive resource will equip you with the insights needed to impress your interviewers.
Download Box Bender Interview Questions in PDF
To make your preparation even more convenient, we've compiled all these top Box Benderinterview questions and answers into a handy PDF.
Click the button below to download the PDF and have easy access to these essential questions anytime, anywhere:
List of Box Bender Interview Questions
Behavioral Interview Questions
Can you describe a time when you worked as part of a team to complete a box bending project? What was your role?
How to Answer
- 1
Select a specific project you worked on with your team.
- 2
Describe your role and contributions clearly.
- 3
Highlight teamwork aspects and collaboration.
- 4
Mention any challenges faced and how the team overcame them.
- 5
Conclude with the outcome of the project and what you learned.
Example Answers
In my last project, we were tasked with bending boxes for a new product line. I was responsible for operating the bending machine and coordinating with the material supply team. We faced delays due to equipment malfunctions, but by working together and troubleshooting as a team, we managed to resolve the issue and completed the project on time. The successful launch boosted our sales by 15%.
Tell me about a challenging project you worked on as a box bender. How did you overcome the obstacles?
How to Answer
- 1
Identify a specific project with clear challenges.
- 2
Explain the nature of the obstacles you faced.
- 3
Describe the actions you took to overcome these obstacles.
- 4
Highlight the outcomes or results of your efforts.
- 5
Focus on skills that are relevant to the box bender role.
Example Answers
In my previous job, we had a big order with tight deadlines. The challenge was that our bender machine was down. I coordinated with the maintenance team to fix it quickly and shifted some tasks to manual bending. We completed the order ahead of schedule and maintained high quality.
Don't Just Read Box Bender Questions - Practice Answering Them!
Reading helps, but actual practice is what gets you hired. Our AI feedback system helps you improve your Box Bender interview answers in real-time.
Personalized feedback
Unlimited practice
Used by hundreds of successful candidates
Describe an instance where you had to meet a tight deadline in your box bending work. How did you manage your time?
How to Answer
- 1
Identify a specific deadline scenario in your past experience.
- 2
Explain the steps you took to prioritize tasks effectively.
- 3
Mention any tools or methods you used to stay organized.
- 4
Describe any teamwork involved in meeting the deadline.
- 5
Reflect on the outcome and what you learned from the experience.
Example Answers
In a previous role, we had a last-minute order that needed 100 custom boxes within 24 hours. I prioritized the design, immediately set up a production schedule, and communicated with my team to divide tasks. We used a checklist to ensure each box was completed on time. We delivered the order successfully, gaining positive feedback from the client.
Give an example of a time you identified a safety hazard in the workplace while bending boxes. How did you address it?
How to Answer
- 1
Think of a specific situation where you noticed a safety issue.
- 2
Describe the hazard clearly and how it could impact safety.
- 3
Explain the steps you took to address the hazard.
- 4
Highlight any collaboration with your team or management.
- 5
Mention the positive outcome or lesson learned from the situation.
Example Answers
While bending boxes, I noticed that a metal edge on a box cutter was exposed. I immediately reported it to my supervisor and we secured the tool to prevent accidents. We also organized a safety training session to remind everyone about proper tool maintenance.
Can you talk about a time when you had to communicate a complex bending process to a co-worker? How did you ensure they understood?
How to Answer
- 1
Use a specific example from your experience.
- 2
Describe the complexity of the bending process clearly.
- 3
Explain the methods you used to communicate, like visuals or demonstrations.
- 4
Mention how you checked for understanding afterward.
- 5
Highlight any feedback received that indicated success.
Example Answers
In a previous role, I had to teach a new co-worker how to set up the bending machine for a custom product. I created a step-by-step visual guide and demonstrated the process while explaining each part. Afterward, I asked them to repeat the setup while I observed, which confirmed their understanding.
Can you describe a situation where you had to lead a small team in a box bending project? What challenges did you face?
How to Answer
- 1
Identify a specific project where you had a leadership role
- 2
Outline the team size and your specific responsibilities
- 3
Discuss key challenges faced during the project
- 4
Explain how you overcame those challenges
- 5
Reflect on the outcome and what you learned from the experience
Example Answers
In my previous role, I led a team of 4 during a box bending project for a new product. One challenge we faced was a tight deadline due to late material delivery. I organized daily check-ins to keep the team focused and adjusted our workflow to prioritize critical tasks. As a result, we completed the project on time and improved our bending precision by 10%.
Tell me about a time when your attention to detail as a box bender made a significant difference in the final product.
How to Answer
- 1
Select a specific example from your experience.
- 2
Describe the challenge or task you faced.
- 3
Explain the details you focused on and how they impacted the outcome.
- 4
Highlight the positive result of your attention to detail.
- 5
Conclude with what you learned from the experience.
Example Answers
In my previous job as a box bender, I noticed that a few boxes had inconsistent dimensions due to misaligned templates. I took the initiative to check and calibrate the templates before production. This attention to detail ensured that all the boxes fit perfectly during assembly, reducing waste and improving customer satisfaction.
Describe a time when you took the initiative to improve a box bending process. What was the outcome?
How to Answer
- 1
Think of a specific example where you identified a problem in the box bending process.
- 2
Explain the steps you took to address the issue, including any creative solutions.
- 3
Mention any collaboration with colleagues or supervisors during the process.
- 4
Quantify the outcome if possible, like improvements in efficiency or reduction in waste.
- 5
Reflect on what you learned from the experience and how it benefited the team.
Example Answers
In my previous role, I noticed that we were wasting a lot of material due to inconsistent measurements in the box bending process. I proposed a new measuring technique and created a template for the team to use. After implementation, we reduced our material waste by 20%, which saved the company costs and improved our production speed. This experience taught me the value of precise planning.
Technical Interview Questions
What types of box bending machinery have you worked with, and what are their key functions?
How to Answer
- 1
Identify specific types of box benders you have experience with.
- 2
Explain the key functions of each type clearly.
- 3
Include any specific brands or models to add credibility.
- 4
Mention your level of proficiency with each machine.
- 5
Relate your experience to the job requirements if possible.
Example Answers
I have worked with hydraulic box benders like the ABC Model 400, which is used for creating precise bends in metal sheets. I am proficient in setting up the machine and adjusting the settings for different thicknesses.
How do you ensure precision in measuring box dimensions before bending? What tools do you use?
How to Answer
- 1
Always use a calibrated measuring tape or ruler for accurate measurements.
- 2
Double-check measurements by taking them from multiple angles.
- 3
Utilize a square tool to ensure corners are correct and to avoid misalignment.
- 4
Mark measurement points clearly using a fine-tip marker or pencil.
- 5
Keep a log of measurements to track accuracy over time.
Example Answers
I ensure precision by using a calibrated measuring tape to measure the dimensions. I always double-check my measurements from different angles and use a square tool to confirm that my corners are right, which helps prevent any misalignment.
Don't Just Read Box Bender Questions - Practice Answering Them!
Reading helps, but actual practice is what gets you hired. Our AI feedback system helps you improve your Box Bender interview answers in real-time.
Personalized feedback
Unlimited practice
Used by hundreds of successful candidates
What types of materials are you familiar with when bending boxes, and how do their properties affect the process?
How to Answer
- 1
Identify common materials used in box bending like cardboard, paperboard, and plastics.
- 2
Discuss how thickness and flexibility impact bending techniques.
- 3
Mention the importance of moisture content in cardboard.
- 4
Explain how different coatings can affect adhesion and bending durability.
- 5
Show awareness of safety measures when handling various materials.
Example Answers
I have experience with cardboard and paperboard. The thickness of the material affects how steep of a bend I can achieve without creasing, while flexibility ensures a smooth folding process.
Explain the process you follow for quality control in box bending. What checks do you perform?
How to Answer
- 1
Start by outlining the initial inspection of materials before bending.
- 2
Describe the steps taken during the bending process to monitor alignment and dimensions.
- 3
Mention any specific tools or techniques used for measurements and checks.
- 4
Include post-bending inspections to ensure structural integrity and design specifications.
- 5
Conclude with your method for documenting quality checks and addressing issues.
Example Answers
I begin with a thorough inspection of the incoming materials to ensure they meet our specifications. During the bending, I use calipers to check the angles and dimensions at crucial stages. After bending, I verify the final dimensions and check for any deformations using a straight edge. I document each step in our quality control log for accountability and review.
What safety standards must be followed when operating box bending machinery?
How to Answer
- 1
Always wear appropriate personal protective equipment such as gloves and safety goggles.
- 2
Ensure the machinery is properly maintained and checked for any faults before operation.
- 3
Follow lockout/tagout procedures to prevent accidental machine start-up.
- 4
Be aware of emergency shut-off mechanisms and their locations.
- 5
Keep work areas clear of debris and ensure all safety barriers are in place.
Example Answers
To ensure safety while operating box bending machinery, I always wear PPE like gloves and goggles. I also check that the machine is maintained and follow the lockout/tagout procedures.
When a box bending machine malfunctions, what steps do you take to troubleshoot the issue?
How to Answer
- 1
Start by checking the power supply and ensuring the machine is plugged in.
- 2
Inspect the machine for any visible signs of damage or misalignment.
- 3
Refer to the machine manual for troubleshooting tips specific to the error.
- 4
Run a test diagnostic if available to identify error codes.
- 5
Document all findings and steps taken for future reference.
Example Answers
First, I check the power supply to make sure everything is connected properly. Then I look for any visible issues like misalignments or damage. After that, I consult the machine's manual for troubleshooting steps that match the symptoms seen.
What routine maintenance do you typically perform on box bending machines to ensure they operate smoothly?
How to Answer
- 1
Check and clean the rollers and bending arms regularly to prevent debris buildup.
- 2
Lubricate moving parts as specified in the machine's manual to reduce friction.
- 3
Inspect electrical connections and safety devices to ensure proper functionality.
- 4
Tighten any loose bolts or fasteners to maintain structural integrity.
- 5
Perform regular calibration checks to ensure precise bending accuracy.
Example Answers
I routinely clean the rollers and lubricate all moving parts to ensure smooth operation. I also check the electrical connections weekly to avoid any downtime.
How do you create or follow patterns for box bending, and what tools do you use?
How to Answer
- 1
Explain your understanding of box bending patterns and their importance.
- 2
List specific tools you use in the box bending process.
- 3
Describe your method for following patterns accurately during bending.
- 4
Mention any software or templates you use to create bending patterns.
- 5
Share experiences where your method improved efficiency or quality.
Example Answers
I understand that creating accurate patterns is crucial for precise box bending, and I use tools like a ruler, protractor, and bending machine. I usually draw patterns on paper and then transfer them to materials while ensuring they match my templates.
How do you interpret engineering drawings or designs when preparing to bend boxes?
How to Answer
- 1
Review the drawings to understand dimensions and angles clearly
- 2
Pay attention to any specific notes or annotations related to bending
- 3
Identify material specifications and their properties from the drawings
- 4
Visualize the bending process step-by-step to anticipate challenges
- 5
Confirm any unclear details with the project engineer before proceeding
Example Answers
I start by carefully reviewing the engineering drawings, focusing on the key dimensions and angles. I also look for any annotations that might indicate special bending techniques or material properties needed for the boxes.
Are you familiar with any CAD software for designing boxes? If so, which ones and how have you used them?
How to Answer
- 1
Identify specific CAD software you have used.
- 2
Mention the types of boxes you have designed.
- 3
Explain particular features of the software that helped in your design work.
- 4
Give a brief example of a project where you used CAD.
- 5
Be prepared to discuss your learning process and improvements.
Example Answers
I am familiar with AutoCAD and SolidWorks. I used AutoCAD to design cardboard boxes for a packaging project, focusing on dimensions and structural integrity. The software helped me visualize the final product before production.
Don't Just Read Box Bender Questions - Practice Answering Them!
Reading helps, but actual practice is what gets you hired. Our AI feedback system helps you improve your Box Bender interview answers in real-time.
Personalized feedback
Unlimited practice
Used by hundreds of successful candidates
Situational Interview Questions
If a co-worker disagrees with your approach to bending a box design, how would you handle the situation?
How to Answer
- 1
Listen to your co-worker's perspective without interrupting.
- 2
Ask clarifying questions to understand their viewpoint better.
- 3
Discuss the merits of both approaches openly and constructively.
- 4
Focus on finding a solution that works for both designs if possible.
- 5
Remain respectful and professional throughout the conversation.
Example Answers
I would first listen carefully to my co-worker's concerns and try to understand their perspective. Then, I would initiate a discussion about our approaches and see if we can combine the best elements of both.
Imagine you have two different methods for bending a certain box shape. How would you decide which method to use?
How to Answer
- 1
Evaluate the material used for each method and its compatibility.
- 2
Consider the production speed and efficiency of each method.
- 3
Assess the final quality and precision of the bending results.
- 4
Analyze the cost implications, including time and resources.
- 5
Think about any regulatory or safety standards that must be met.
Example Answers
I would first look at the compatibility of the material with each bending method. If one method is known to produce better quality bends with the material at hand, that would influence my decision. I would also consider production speed; if one method is considerably faster without compromising quality, it would be preferable.
Don't Just Read Box Bender Questions - Practice Answering Them!
Reading helps, but actual practice is what gets you hired. Our AI feedback system helps you improve your Box Bender interview answers in real-time.
Personalized feedback
Unlimited practice
Used by hundreds of successful candidates
If you're faced with multiple box bending orders with overlapping deadlines, how would you prioritize your tasks?
How to Answer
- 1
Assess the deadlines of each order and identify the most urgent ones.
- 2
Evaluate the size and complexity of each order to estimate the required time.
- 3
Communicate with team members about their workloads to delegate if necessary.
- 4
Consider customer importance and any contractual obligations.
- 5
Create a clear list or timeline to visualize priorities and track progress.
Example Answers
I would first look at the deadlines of all my box bending orders and prioritize those that are due soonest. Then, I would assess which orders are more complex and might take longer to complete. If I see any that I can delegate to teammates, I'd discuss it with them. Finally, I would make a list to manage my time effectively.
If a client is unhappy with the quality of boxes you produced, how would you address their concerns?
How to Answer
- 1
Listen carefully to the client's feedback
- 2
Acknowledge their concerns and empathize with their situation
- 3
Ask clarifying questions to understand specific issues
- 4
Offer solutions or alternatives to rectify the problem
- 5
Follow up after implementing changes to ensure client satisfaction
Example Answers
I would first listen to the client's specific concerns without interruption. Then, I would empathize with them, acknowledging that their satisfaction is important to us. I would ask questions to gather more details about the quality issues and work on a solution, such as redoing the boxes if needed. Finally, I would follow up to ensure the new boxes meet their expectations.
If you notice that box bending times are slower than usual, what steps would you take to improve efficiency?
How to Answer
- 1
Analyze the current workflow to identify bottlenecks.
- 2
Engage with team members to gather feedback on issues.
- 3
Implement time tracking to assess bending times accurately.
- 4
Provide training or refreshers on best practices for operating equipment.
- 5
Consider adjusting the layout or workflow for better ergonomics.
Example Answers
I would start by analyzing the workflow to pinpoint any specific delays, then I would talk to the team to understand their challenges. If necessary, I would introduce a time tracking system to measure bending times and identify specific areas for improvement.
If you made an error in bending a box that caused a production delay, how would you handle it with your supervisor?
How to Answer
- 1
Acknowledge your mistake immediately and take responsibility.
- 2
Explain the impact of the error on production clearly.
- 3
Offer a solution or mitigation plan to rectify the situation.
- 4
Communicate proactively and keep your supervisor informed.
- 5
Learn from the mistake and suggest ways to prevent it in the future.
Example Answers
I would first admit to my mistake to my supervisor and explain how it caused the delay. Then, I'd outline a plan to fix the issue, such as adjusting the bending process or working overtime to catch up on production. I would also assure them that I would take steps to prevent similar mistakes in the future.
If you were given the opportunity to implement a new technology in the box bending process, what would you choose and why?
How to Answer
- 1
Identify a technology that improves efficiency or quality.
- 2
Explain how it enhances the current box bending process.
- 3
Consider cost-effectiveness and potential ROI.
- 4
Mention any relevant industry trends or innovations.
- 5
Be ready to discuss potential challenges and solutions.
Example Answers
I would implement an automated laser cutting system. It would increase precision in cutting, reduce material waste, and speed up the overall production process, ultimately leading to cost savings and higher quality boxes.
If a customer requests a custom box type that you haven’t worked with before, how would you proceed?
How to Answer
- 1
Ask clarifying questions to understand the customer's requirements clearly
- 2
Research the materials and techniques that may be needed for this custom box
- 3
Consult with team members or supervisors who might have experience with similar requests
- 4
Outline a basic plan for creating the custom box, including design and production steps
- 5
Keep the customer updated on your progress and any challenges you encounter
Example Answers
I would start by asking the customer specific questions to fully understand their needs for the custom box. Then, I would do some research on the materials needed and consult with my team for any best practices. Finally, I would keep the customer informed throughout the process.
If you were to work with someone who has a very different working style from yours, how would you ensure effective collaboration?
How to Answer
- 1
Identify key differences in work styles and acknowledge them.
- 2
Communicate openly about preferences and methods.
- 3
Find common goals to align your efforts.
- 4
Be flexible and willing to adapt your approach.
- 5
Regularly check in to ensure both are on the same page.
Example Answers
I believe that understanding our differences is crucial. I would first identify how our working styles differ and openly communicate those preferences. By focusing on our common goals, we can both adapt our methods while keeping our objectives aligned. I would also ensure we have regular check-ins to discuss our progress and make adjustments if needed.
Don't Just Read Box Bender Questions - Practice Answering Them!
Reading helps, but actual practice is what gets you hired. Our AI feedback system helps you improve your Box Bender interview answers in real-time.
Personalized feedback
Unlimited practice
Used by hundreds of successful candidates
Box Bender Position Details
Related Positions
- Box Maker
- Hand Bender
- Wood Box Maker
- Panel Cutter
- Hand Tube Bender
- Buttoner
- Board Runner
- Wood Hacker
- Tube Maker
- Board Worker
Similar positions you might be interested in.
Ace Your Next Interview!
Practice with AI feedback & get hired faster
Personalized feedback
Used by hundreds of successful candidates
Ace Your Next Interview!
Practice with AI feedback & get hired faster
Personalized feedback
Used by hundreds of successful candidates